Digging underground is critical to nearly any civil engineering project. Unfortunately, it’s also a recipe for surprise risks, price disputes, and even litigation.
Or as leading tunnel expert Randall J. Essex said, “The ground wasn’t built with a materials handbook, and we don’t have X-ray vision.”
Reducing this uncertainty is what put Essex at the forefront of the ASCE push in the 1990s to create what is now known as geotechnical baseline reports – contractually binding assumptions for pricing of subsurface risks upfront.
A second edition followed in 2007, and now, 25 years later, Essex has led a third iteration of the authoritative publication on allocating and managing risks associated with subsurface construction.
Those first two publications were committee reports. The new one is an ASCE manual of practice: Geotechnical Baseline Reports: Suggested Guidelines, MOP 154, prepared by the Task Committee on Geotechnical Baseline Reports of the Construction Institute of ASCE and peer-reviewed by a Blue-Ribbon panel.
Essex, the publication’s editor, recently spoke with Civil Engineering Source.
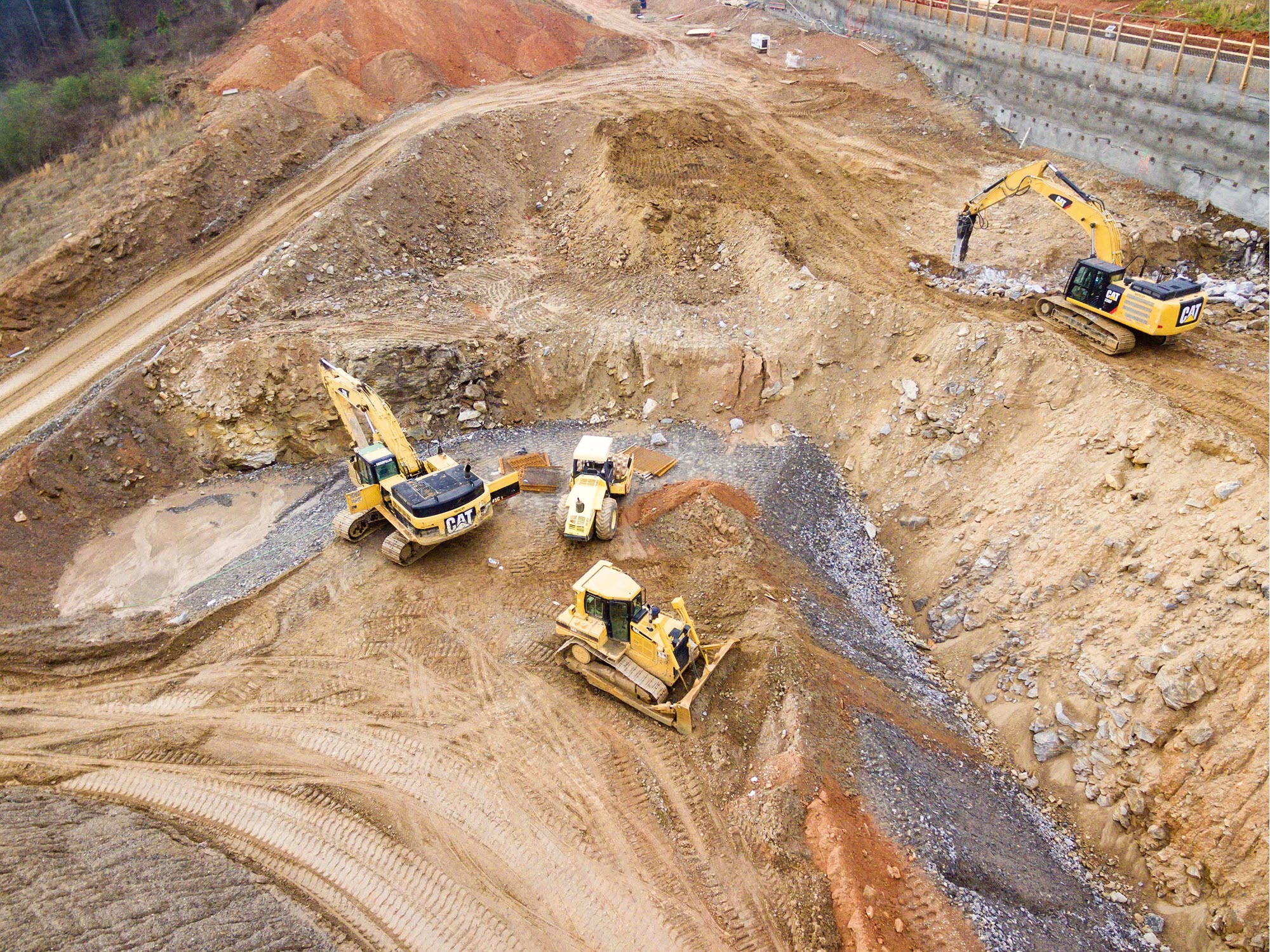
Civil Engineering Source: Where do you start with this kind of thing because this is not stuff you learn in a classroom, right?
Randy Essex: No, absolutely not. You have to learn this stuff literally with the dirt under your fingernails.
I’ve lectured at universities, including the Colorado School of Mines, Virginia Tech, University of Illinois, Cornell, and the University of Arizona, on the challenges of underground engineering, and how we manage subsurface risk. While students’ eyes bug out when they learn how exciting tunnel engineering projects can be, we never get into the subject of how to avoid or resolve multimillion dollar claims specifically. That learning process is experience-based. There’s no constitutive relationship that describes what to do and how to do it. What I do discuss are the relationships among subsurface conditions, construction technologies, and the impacts of both on cost and schedule.
The basic principles on how to write and apply GBRs [geotechnical baseline reports] have not changed dramatically over these past 25 years. They’re all based on the same set of fundamental tenets.
One is to create a fair contract that pays the contractor for the work it has to perform, whether known fully at the start of construction or not.
Another is that the anticipated conditions described in the GBR are not fact. They are agreed-upon contractual assumptions created to assist bidders in developing their bids and help resolve disputes through the administration of the different site condition clause in the contract. The GBR “building blocks” are the intrinsic properties in the ground and the behavior of the ground associated with the means and methods to be employed.
The third is to quantify the occurrence of unique geologic features and manmade obstructions that will significantly impact the work. That’s it. The cleaner and more concisely these descriptions are presented, and the better connected the GBR is within the overall contract, the less likely disputes will arise.
Source: It's all about limiting surprises.
Essex: Absolutely. The goal is to develop contractual tools that allow the contractor and the owner to identify, quantify, anticipate, and manage variable ground conditions as a matter of contract administration, rather than disputes or litigation.
To write a GBR that is well-connected with the other contract documents takes experience, skill, and practice. It’s not just about writing a GBR, it’s how clearly and efficiently it connects with the other contract documents. Owners often don’t understand the importance of these subtleties, so the latest edition of the book tries to reinforce these principles.
Source: It’s been 16 years since the 2007 edition. What are some of the key points people can find in this update?
Essex: A number of key topics are either introduced or reinforced. A new chapter addresses the legal and contractual considerations of GBRs in a contract. Another is the need to have individuals involved who are suitably qualified, not just in the geotechnical aspects but in construction, means, and methods, and what the other contract documents contain. An appendix has been added that presents the results of about 20 projects where the GBR served a key role in helping to resolve a dispute.
For design-build delivery, more collaboration is needed among the owner, the contractor, and the contractor’s designer during GBR development. The document offers that the form of design-build most likely to achieve the necessary level of collaboration is progressive design-build.
In this instance, a design-build team is selected based on criteria other than lowest price. The design-build team reviews the results of preliminary site investigations and provides input on additional information required as their design and construction approaches are advanced. The physical baselines in the GBR are established after the site investigations are substantially completed. Also, the descriptions of the anticipated ground behavior in the GBR reflect a joint understanding of the means and methods the contractor actually intends to employ, not what the owner’s advisor thinks the contractor may employ.
A GBR created during progressive design-build procurement has the greatest opportunity to capture the results of a substantially completed site investigation, and to reflect a joint understanding of the what the contractor actually intends to build and how it intends to build it.
Source: You put these recommendations out into the world, how optimistic are you that they’ll have a positive impact on how things get done?
Essex: We can only try. The industry can’t compel an owner and its legal team to do what we’re suggesting. The challenge is to inform owners, so they understand what’s at stake. What we’re trying to do is to enhance price and schedule certainty, which is in the best interest of all parties.
Learn more about Geotechnical Baseline Reports: Suggested Guidelines, MOP 154.