To help New York City workers avoid the daily headaches of long commute times on crowded buses and subways, the New York City Economic Development Corp. launched a new ferry service in 2017 to get people off the streets, out of the tunnels, and onto the waters that surround Manhattan and the city’s four other boroughs. The project was also aimed at connecting underserved waterfront communities — sites historically considered “transit deserts” that had some waterfront amenities but lacked the infrastructure to load or unload ferry passengers, notes Stephen Famularo, P.E., D.PE, M.ASCE, a vice president of marine engineering at McLaren Engineering Group, based in Woodcliff Lake, New Jersey. McLaren served as the project’s primary engineering consultant.
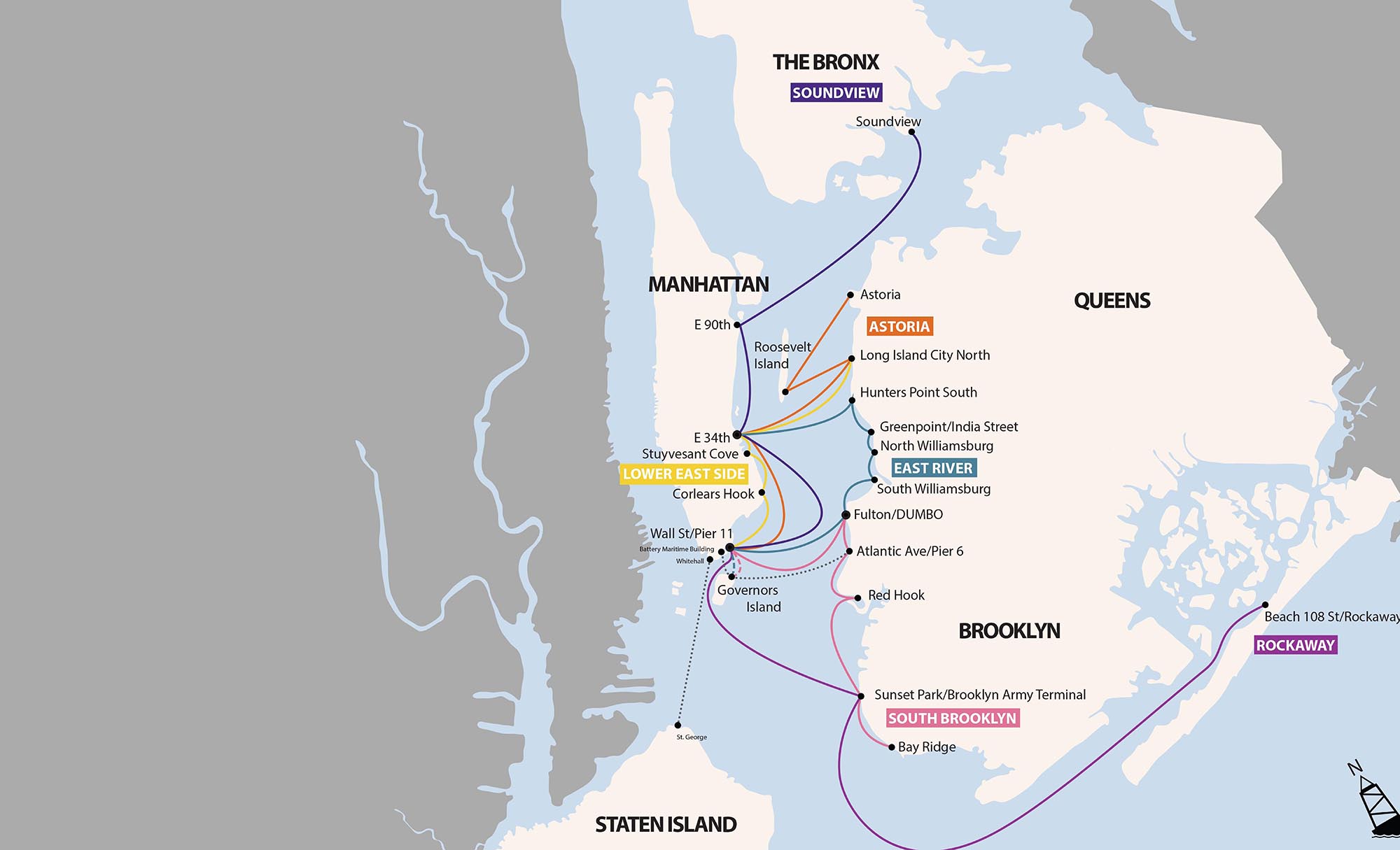
Because the project is also intended to “address some of the inequities that were inherent in (New York City’s) existing transportation system,” the price of the ferry tickets is being subsidized by the city so that riders pay the same amount to use the ferries as they do to use the subway system, Famularo says. This makes the system much more accessible to everyone in the community, especially lower-income users, he stresses.
Although the new ferry service began primarily along the East River, it proved to be quite popular and was quickly expanded to include sites in the Upper Bay and Jamaica Bay areas of the New York City harbor, Famularo adds. More than 20 landings were ultimately planned, the last of which should be completed by the end of 2021. New York City-based Skanska USA was the project’s construction manager.
Extreme solutions
McLaren designed a series of resilient floating landings to accommodate these previously isolated locations and prepare for the potential effects of climate change and other challenges. These landings are meant to withstand extreme environmental events and remain in operation even when the city’s ground transportation services are interrupted — as they were during the September 11, 2001, terrorist attacks and 2012’s Hurricane Sandy, Famularo notes.
The system features a prefabricated steel barge, a series of tall steel piles — typically, six to eight per landing — and an aluminum gangway that is supported on a freestanding bent located just off the land. The bent is formed from a steel pipe pile topped by cast-in-place concrete. Everything is accessible from land but not structurally connected to land, explains Matthew McCarty, P.E., S.E., M.ASCE, a lead technical specialist at McLaren. A collarlike bracket in the barge deck surrounds the piles — which are generally 30 to 36 in. in diameter — to keep the barge from floating away but provides the flexibility for the barge to rise and fall on the water with the tides and even rotate as waves generated by passing vessels lift and drop different sections of the structure at different times, McCarty explains.
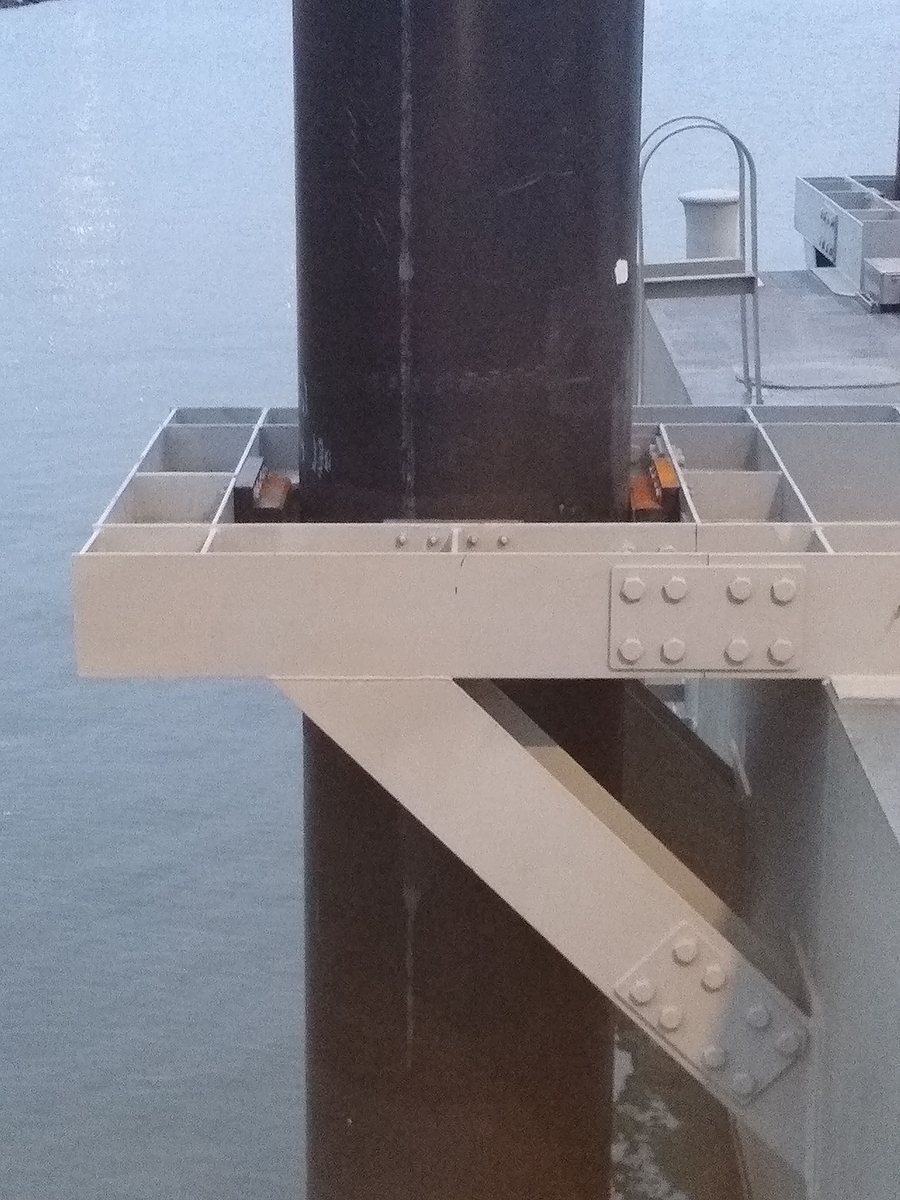
The brackets are lined with ultra-high-molecular-weight pads that “are super low friction” and thus enable the barge structure to “ride up and down the pile without causing a lot of abrasion,” says Famularo. A pinned system, similar to the connection between a truck cab and its trailer, is used at the landward end of the gangway to facilitate movement in basically any direction there, McCarty adds.
The barges measure 35 ft wide by 90 ft long and approximately 11 ft deep with a roughly 7 ft freeboard from the waterline to the top of the barge deck, Famularo says.
Tidal times
The system was designed to accommodate a wide range of tidal conditions along the ferry routes, with some locations experiencing 5 ft changes from low tide to high tide while others experience 8 or 9 ft changes, Famularo notes. Consequently, the lengths of the gangways range from 70 to 100 ft.
The soil conditions also vary considerably from sand to solid rock, says McCarty, which means that the piles vary from 100 to 120 ft long in some locations.
In addition to keeping the floating landings in place, the piles must also act as essentially giant springs to help capture and absorb the energy of the ferries as they come in and impact the barges, McCarty notes. A fender system also helps absorb the energy of the incoming ferries. The system is designed to accommodate a berthing impact of up to 4 knots.
Stormy weather
Many of the barges feature tension-structure canopies to protect riders from harsh weather, and some also have plexiglass dividers to shield people from the harbor’s salt spray. The gangway slopes and other aspects of the barge systems were designed to accommodate universal access principles under the Americans with Disabilities Act.
The gangways also provide routes for land-based electrical lines to extend to the barges to power lights, ticketing machines, and other passenger amenities as well as an electrical motor to operate a second gangway that is lowered into place to provide access between the barge and the ferry. The electrical connections plug in so that they can be easily unplugged and the gangways quickly removed and stored on land in the event of a major storm.
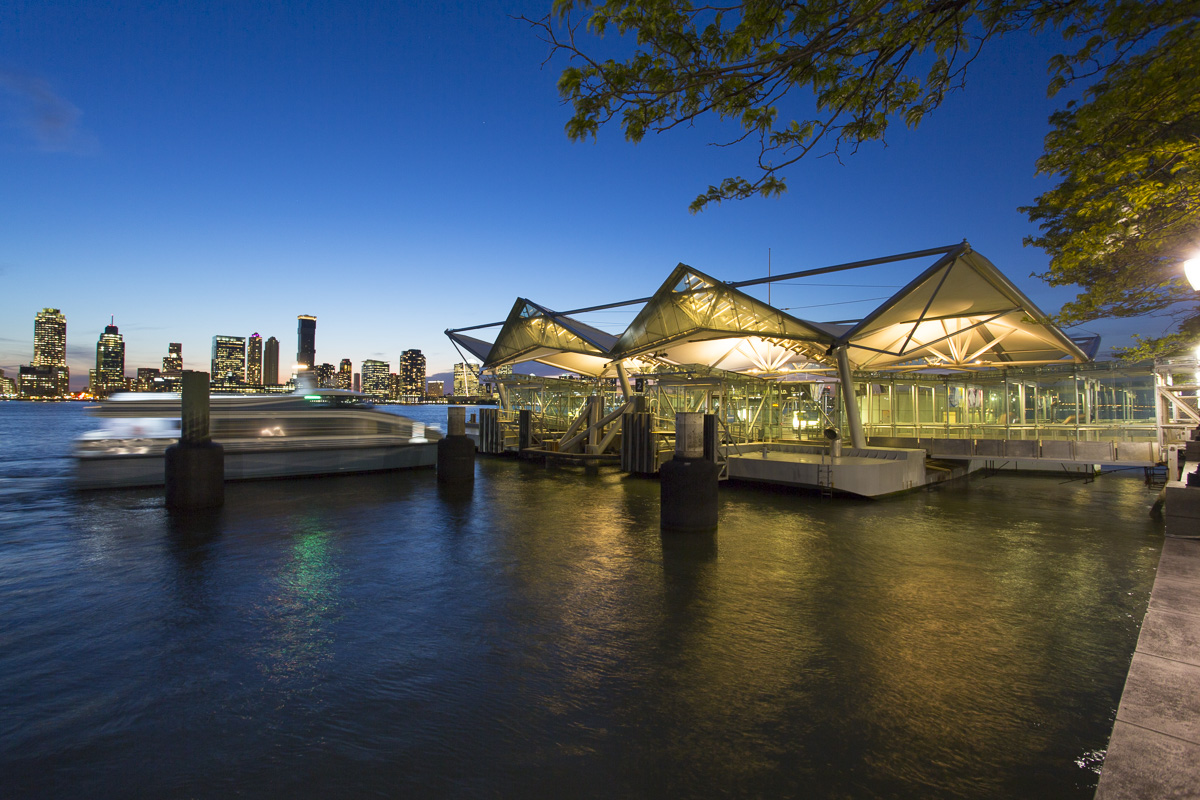
Unlike other parts of New York City’s transportation system, which flooded in many locations during Hurricane Sandy and in some cases took months to be restored, the barge system is designed to be up and running soon after a storm. Once the storm surge’s tide has gone back out, the gangways can be put back in place and the ferries would likely be running again within a day, Famularo notes.
Heading home
McLaren is also working on another project for the ferry system: a new facility where the ferries can dock at night, be refueled, get cleaned, and undergo repairs or various maintenance activities. As the second such facility for the system, the new site is dubbed Homeport II and will be located at the Atlantic Basin site in Brooklyn, off Buttermilk Channel. It is expected to be operational in about two years, Famularo notes.
The facility will provide space to berth approximately 40 vessels and include the equipment to lift ferries out of the water for maintenance. The ferry system will also take over approximately 30,000 sq ft of an existing building at the site, where McLaren is planning to elevate offices and mechanical equipment above the expected flood levels of a major storm. The lower portion of the space will be used for storage of supplies that either can be safely flooded or easily moved out in the event of a storm, Famularo says.
To help analyze the site, McLaren performed a coastal wave analysis, using an acoustic doppler current profiler to measure the waves, the velocity of the current, and the wakes caused by environmental conditions and vessels passing through the region. McLaren’s dive teams attached the profiler device to the channel bottom, where it used acoustic wave sonar signals to monitor how fast the water was moving at different elevations, notes Todd Manson, P.E., M.ASCE, a senior associate at McLaren.
“What was interesting was that a lot of the waves happening inside the basin were not caused by storm events but mainly by passing vessels,” says Manson. That information enabled the design team to provide a rough correlation between the evidence from the physical monitoring using the profiler device and the details on vessel traffic, including “what kinds of vessels were passing at what speeds,” Manson says.