By Robert L. Reid
It’s not exactly rocket science to realize that if you need to roll an extremely heavy object over a roadway made from various layers of rocks, sands, and soils, it’s a good idea to test that roadway first — by rolling a really heavy object over it again and again.
But sometimes it is the epitome of rocket science — especially when the rocky road in question is located at the Kennedy Space Center in Florida, the people testing the bearing capacity of that roadway work for NASA, and the object that will eventually be rolled over the roadway includes the heaviest and most powerful rocket that NASA has ever launched.
That sums up the work that has been underway at the space center since late last year as NASA prepares for the first launch of its massive Space Launch System rocket.
The SLS is part of the agency’s Artemis program, which will take astronauts back to the moon as a step toward an eventual trip to Mars.
Short trip, heavy load
To start the SLS and its Orion space capsule on this interplanetary journey, NASA first needs to move the rocket and capsule 4.2 mi from the enormous Vehicle Assembly Building to Launch Complex 39B, otherwise known as Pad B. That roadway must accommodate a total weight of at least 25.5 million lb, even though it was originally designed for loads of 18 million lb, says Robert Schroeder, P.E., a NASA design manager and engineer.
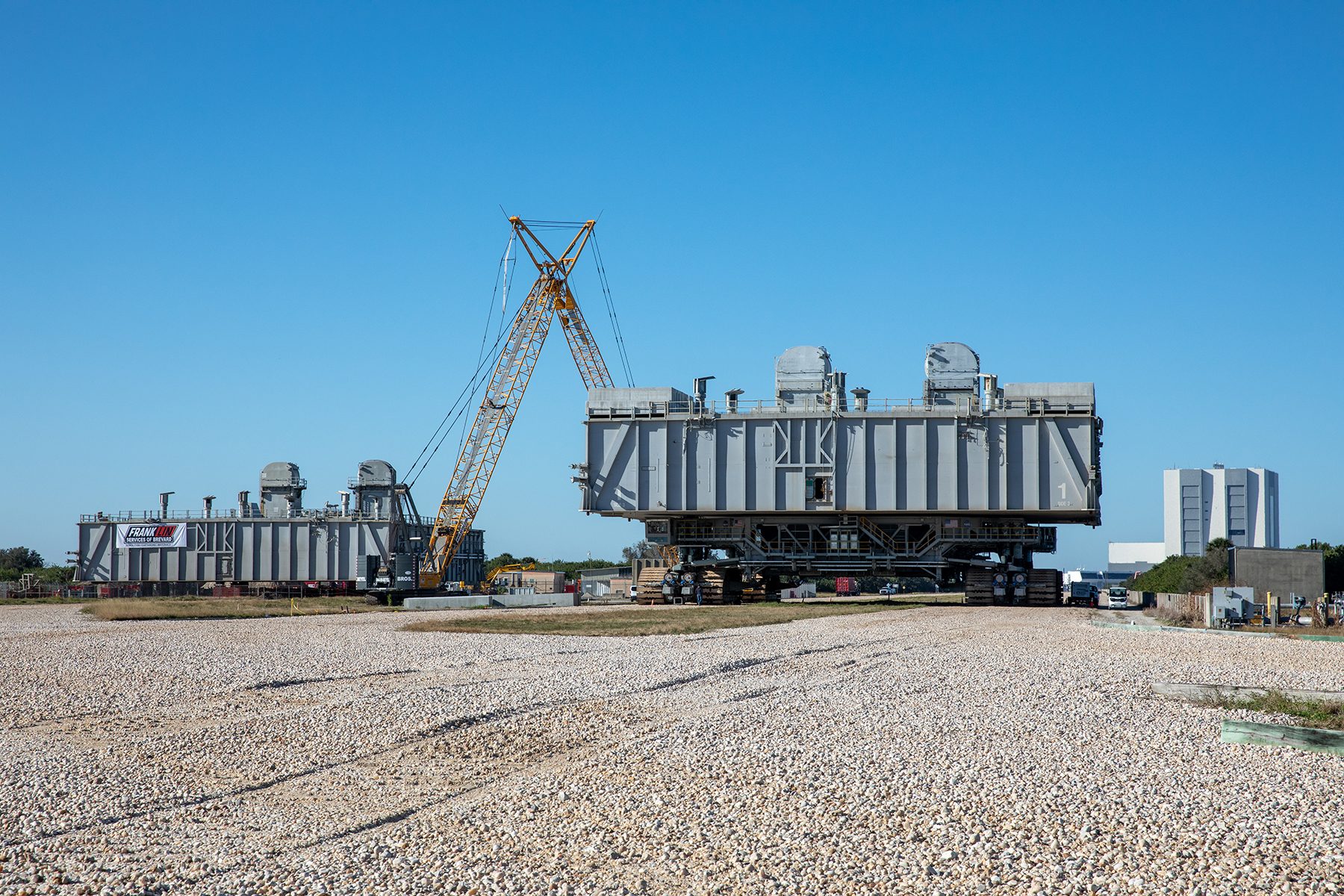
The 25.5 million lb that will travel the roadway includes the SLS rocket and capsule, the launch tower that supports the rocket, and the enormous vehicle — the crawler-transporter — that will carry the rocket and tower slowly and carefully along the rock-covered roadway known as the crawlerway.
The total weight of an Apollo Saturn V moon rocket, together with its launch tower and crawler-transporter, was approximately 18 million lb — and the space shuttles and their launch systems weighed about the same, notes Kim Rivera, P.E., a vice president and department manager in the civil and environmental discipline of Jones Edmunds, the Florida-based engineering firm working with NASA to prepare the crawlerway for the Artemis program.
Swampy road
The crawlerways were originally constructed in the 1960s by the U.S. Army Corps of Engineers on land that had once been a Florida swamp, notes Schroeder. It is composed of approximately 4 to 8 in. of river run gravel atop 4.5 ft of compacted lime rock plus various depths of hydraulically placed sand and natural soils, explains Rivera.
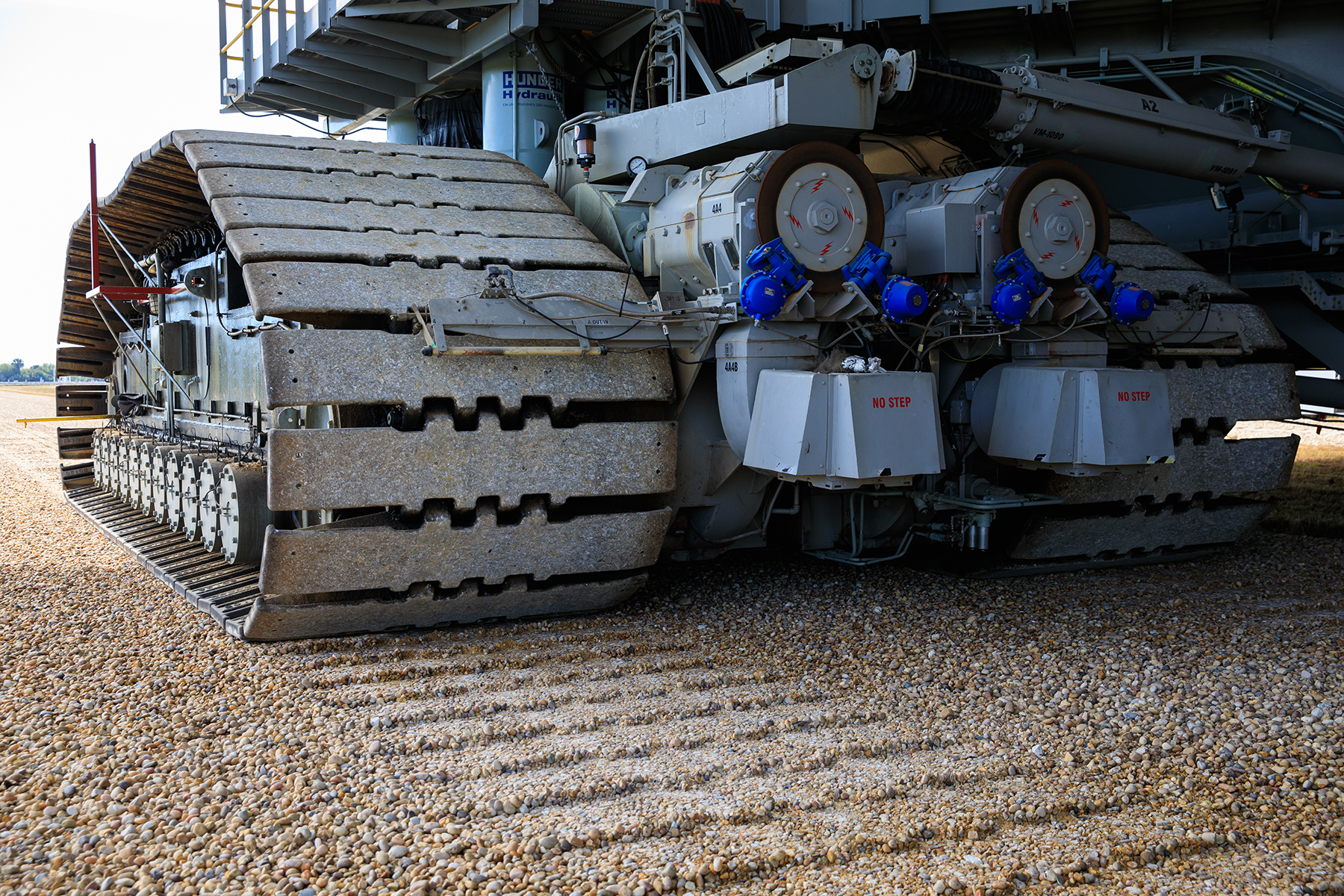
When it leaves the Vehicle Assembly Building, the Artemis crawler-transporter will first roll eastward along roughly 2 mi of Crawlerway A — which accesses Launch Complex 39A — before turning northward onto Crawlerway B for another roughly 2.25 mi to reach Pad B.
Along that route the crawler-transporter will pass over several problematic areas at which liquefaction of the soils is a concern if the local pore water pressure exceeds the bearing capacity of the crawlerway foundation, notes Rivera.
This potential is exacerbated by the end of the space shuttle program in 2011, which meant no heavy objects have been rolled over the crawlerways for several years. This lack of use has led to a condition that NASA refers to as “negative aging” on the roadway. Because the soils are not regularly compacted through use of the roadway for heavy loads, the underlying soils weaken over time, Schroeder explains.
Acid rain, the fluctuating water table, and the shell content in the bottommost layer of the crawlerways are also factors in causing the material to “relax,” which can lead to excessive settlement, Schroeder adds.
Soil tests
Jones Edmunds has worked at the Kennedy Space Center previously, analyzing the crawlerways as part of other NASA projects. Those efforts included a full-scale load test on the crawlerways’ material that earned the firm a project of the year award from ASCE’s Florida section in 2011.
The current project to prepare the crawlerways for the Artemis program began in 2017 and included multiple soil tests — using cone penetrometers, conducted every 100 ft, and staggered to accommodate both tracks of the crawler-transporter, which is about 150 ft wide, says Rivera. The cone penetrometer results were compared with earlier tests from previous projects, she adds.
Based on the data collected, Jones Edmunds developed a comprehensive conditioning program to strengthen the crawlerways’ soil structure and increase the reliability of the roadway foundation so that it could accommodate the required loads of the Artemis program.
This was accomplished by rolling an updated crawler-transporter — carrying a modified mobile launcher platform from the space shuttle program — across the surface of the crawlerways again and again at various speeds and with increasing weights. Schroeder compares the conditioning efforts to “roadway projects where a steamroller or vibratory roller presses down on the soils to compact them, which improves their load-bearing capacity.”
Concrete solution
To modify the launcher platform carried by the transporter for the roadway conditioning, NASA turned to the Jacksonville, Florida-based engineering firm RS&H, which has a long history of providing engineering, architecture, and other consulting services to the space agency.
Basically, “we told them to level the top deck” of the launcher platform, cutting off anything that protruded more than 6 in. in height, including the railing around the platform, Schroeder says. The platform was also strengthened internally by the project’s construction contractor, Pontchartrain Partners LLC, of New Orleans.
Pontchartrain Partners also constructed more than 200 concrete blocks, each measuring roughly 23 ft long, 3.5 ft wide, and 3.75 ft tall and weighing 43,000 lb. These blocks were lifted by crane onto the now-flattened deck of the launcher platform. The heavily loaded crawler-transporter was then driven slowly over crawlerways A and B as well as Crawlerway C, which loops to the north around the Vehicle Assembly Building and which NASA also wanted conditioned, Rivera says.
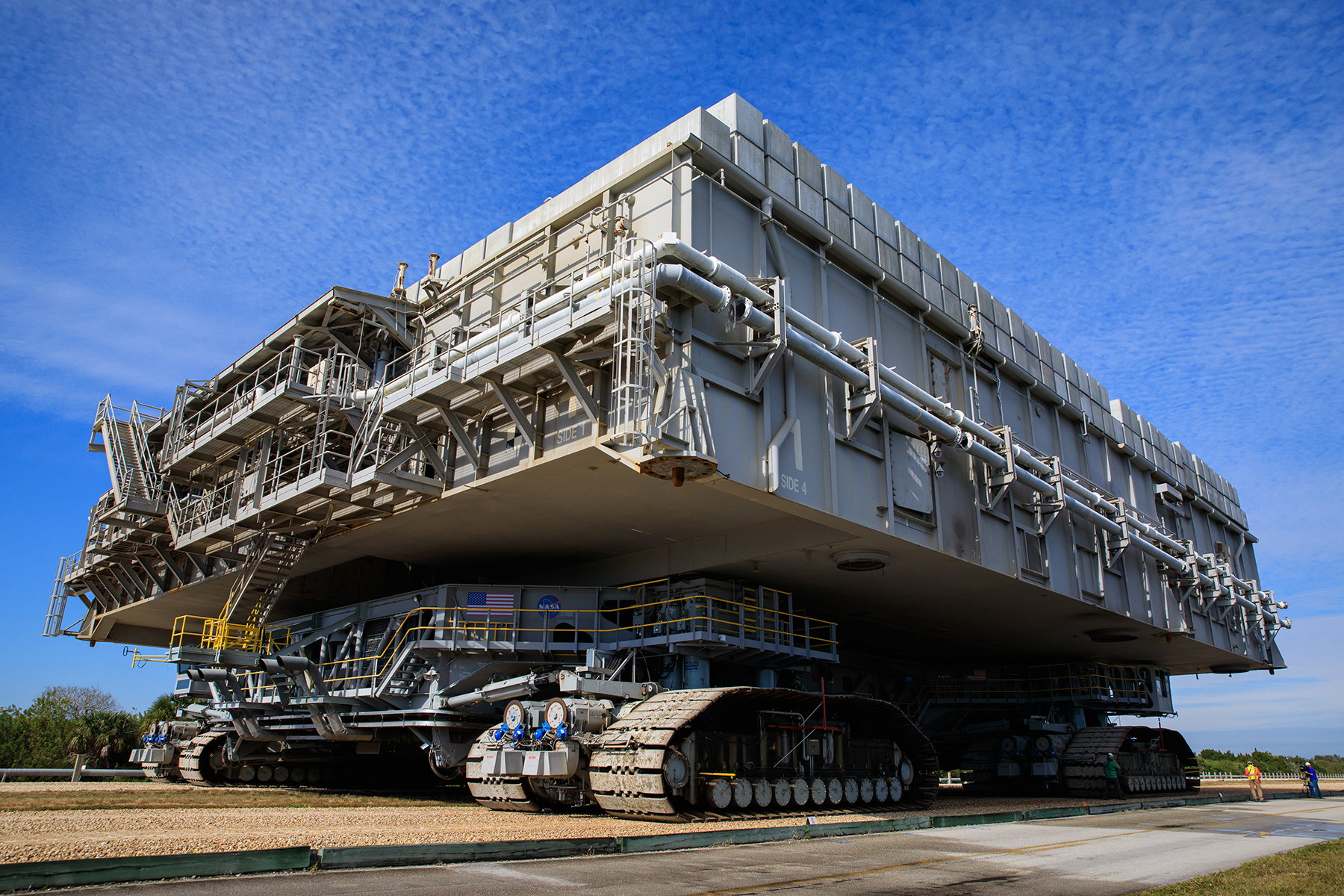
The concrete block-laden transporter made a total of eight passes, back and forth, over the crawlerways between November 2020 and April 2021. These tests began with a weight of 22 million lb at a speed of 0.3 mph, increasing both weight and speed on subsequent passes, Schroeder says. Although there were certain sensitive areas and curves along the crawlerways at which the transporter was slowed down, the tests eventually reached the required maximum weight of 25.5 million lb at 0.83 mph — the top speed that NASA expects to operate the transporter when it is carrying the SLS rocket.
Real-time monitoring
Instrumentation monitored each pass, relying on dilatometers to measure horizontal stresses, inclinometers to measure lateral displacement, settlement plates to record the deformation of the foundation, and piezometers installed at various depths to measure pore water pressures in the weaker soil stratum. If the pore water pressure results rose too high, the transporter would be directed to slow down or stop, Rivera says.
Strain gauges were installed on the ceilings of the concrete utility tunnels and so-called catacomb spaces located beneath Pad B that house the large pipes that form part of a sound-suppression system during launches. Structural analyses were then performed on both structures.
The Arlington, Virginia-based engineering firm Langan helped Jones Edmunds conduct the real-time monitoring that compared survey data taken prior to each conditioning pass with the information gathered during the pass. For example, optical levels were used with prisms attached to the transporter to monitor the mobile launcher platform’s hydraulic jacking and leveling system that kept the platform level, especially as the transporter climbed the concrete slope to access Pad B.
During these tests, the information from both surveys was compared, and if the surveying data indicated excessive settlement, the transporter would be directed within seconds to slow down or stop, Rivera explains.
Approaching launch
If the full 25.5 million lb of the Artemis rocket had simply been transported on the roadway without first conditioning it, there could have been problems, Rivera says. But by working incrementally and simultaneously analyzing and conditioning the roadway, the project “reduced risk and safely and effectively conditioned the crawlerway” to accommodate the Artemis rollout, she says.
A so-called wet rehearsal for a launch — in which the SLS rocket will be fully fueled — is expected sometime this fall. The first launch itself is expected by the end of the year.