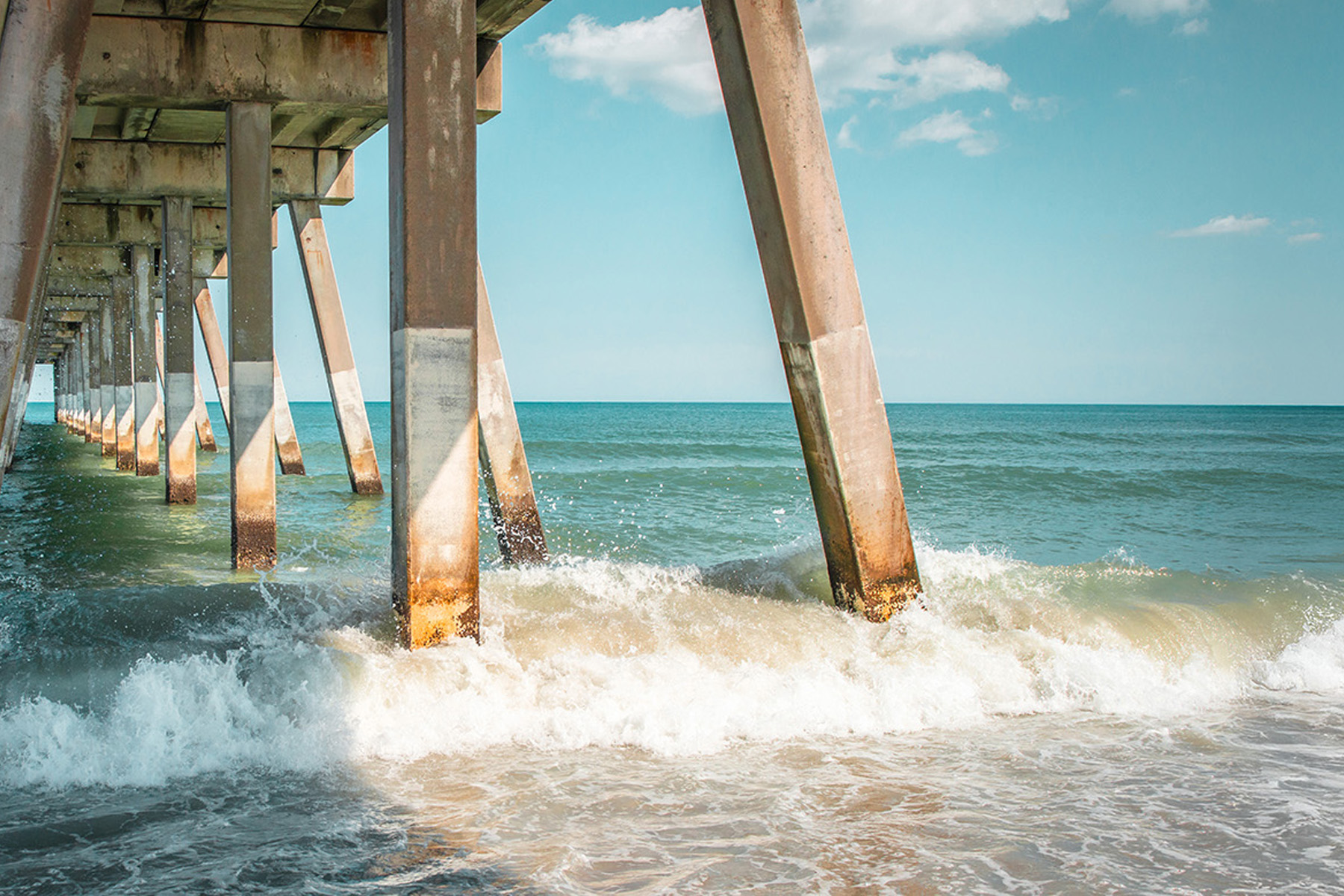
By Thomas Spencer, P.E., S.E., P.Eng, BC.PE, M.ASCE, Sean Chapman, P.E., M.ASCE, and Noah Elwood, P.E., BC.OE, BC.PE, M.ASCE
Waterfront infrastructure is vital to national security, economic growth, and recreation. A specialized discipline within civil engineering has evolved to support the inspection, assessment, and design of waterfront facilities.
Historically, the waterfront practitioner has relied on experience and knowledge to inspect and assess waterfront structures. The waterfront segment of the industry generally lacks the same level of codes and references employed in other areas of structural engineering, such as buildings and bridges. In the past decade, the industry has made strides to close that knowledge gap. For example, the ASCE Ports and Harbors Committee has developed standards on waterfront seismic requirements and manuals of practice dedicated to waterfront facility inspections and assessments, such as ASCE’s Manual of Practice 130, Waterfront Facilities Inspection and Assessment. Other manuals are under development for the analysis, rehabilitation, and design of waterfront structures.
Waterfront structures are uniquely constructed, differing significantly from buildings, bridges, and other civil infrastructure. Common types of waterfront structures include open-piled platforms, floating platforms, relieving platforms, bulkheads, seawalls, revetments, moorings, security barriers, gangways, ramps, and railways. Understanding the construction, components, functions, and load paths of these structures is essential. Each type has unique attributes and common problem areas that require the expertise to know where to look as well as what to look for.
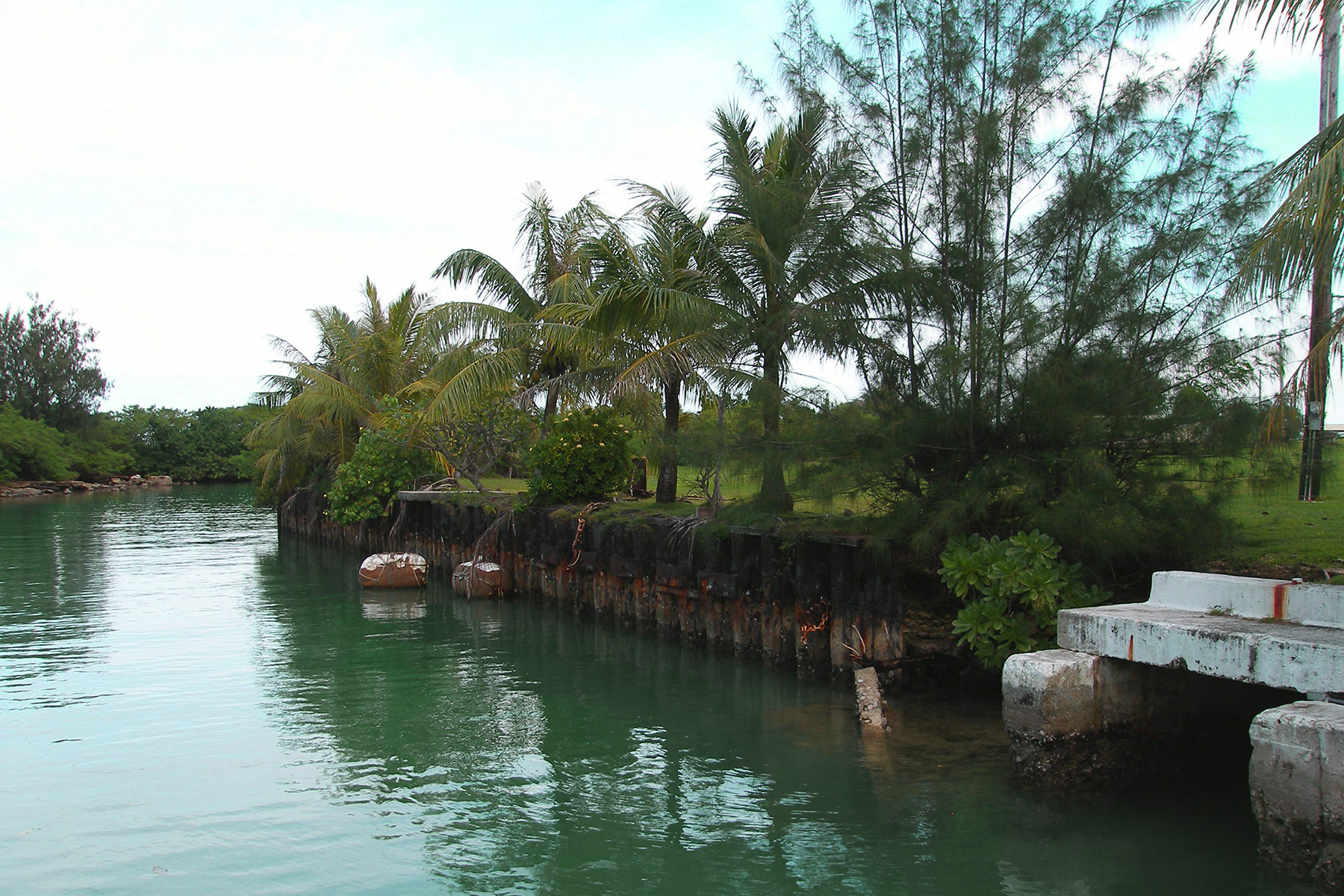
Inspections of waterfront structures are a necessary part of effective waterfront facility asset management programs. They play an important role in protecting the public and the environment, enabling reliable operational facilities, and reducing maintenance and repair costs. Structural conditions at the deck level that could lead to failure, loss of life, or property damage are often observed by engineers, maintenance workers, operation personnel, and the public.
However, these groups rarely observe (due to the difficulty of access) similar structural conditions located below the deck or underwater until the distress has progressed to the point that damage is evident above water. A history of failures due to deterioration has led to routine inspection mandates in the United States. Many waterfront facility owners have also adopted similar routine inspection policies for their facilities, recognizing the importance of these assets.
MOP 130 offers guidelines for types and frequency of inspections, element-level damage ratings, overall system ratings, and service life estimation. The manual also sets specific qualification requirements for the personnel involved in waterfront inspection projects to ensure appropriate expertise and experience. Detailed guidelines for the different types of inspections are provided, along with special considerations for different types of structures, defects, and specialized techniques.
The significant financial investment, problems of waterfront construction, and the sensitive environment often lead owners to seek to extend the service life of their facilities.
Types and causes of defects
Many of the types of defects that occur, and their causes, are unique to waterfront facilities. This is generally due to exposure to the marine environment, elements existing below water, and applied forces from equipment and vessels. For instance, defects found in reinforced-concrete elements are commonly caused by corrosion of reinforcing steel or chemical attack from exposure to the marine environment.
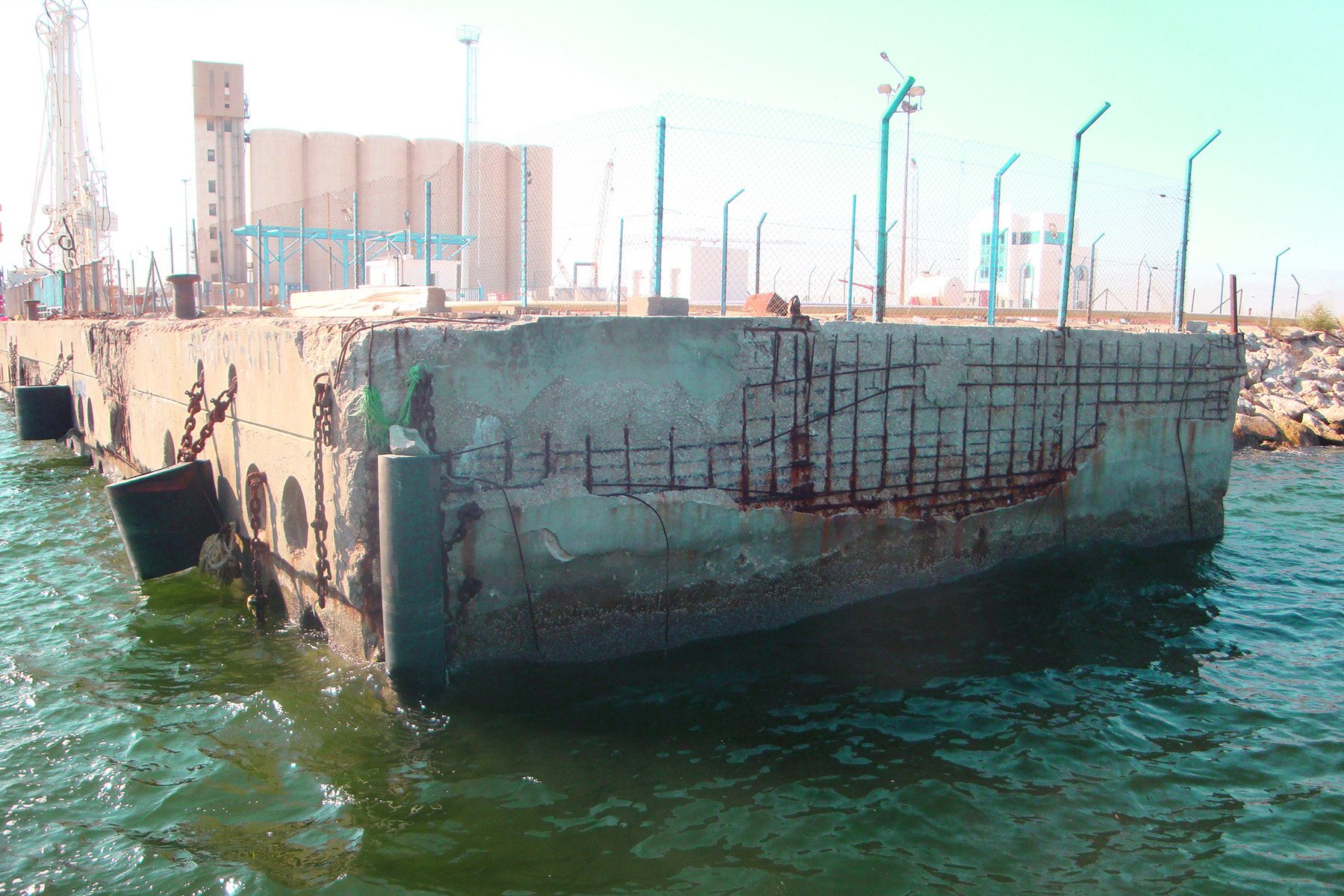
Stress-induced cracking or failure of reinforced-concrete elements is also common due to the often extreme and dynamic forces from vessels and environmental loads from waves, ice, or earthquakes. Steel elements are susceptible to highly corrosive marine environments, fatigue-prone loading, and impacts from vessels or equipment. Defects to timber elements commonly occur due to moisture collection and accumulation, wetting and drying, as well as from various types of insects and marine borers.
Waterfront facilities are subject to external physical loads, but their capacity to support these loads diminishes as they deteriorate over time. A waterfront facility inspection is a “snapshot” of the condition of a structure or element at a moment in time over the history of the asset. The validity of the assessment is limited, considering this continuum of ongoing deterioration.
Waterfront inspections
The inspection, testing, and rehabilitation of waterfront structures have been performed in many cases as independent operations. But there has been a migration toward comprehensive asset management programs. The initial step in the management of the structures is the selection of the appropriate inspection type.
There are eight inspection types outlined in MOP 130:
- Routine
- Structural Repair or Upgrade Design
- New Construction
- Baseline
- Due Diligence
- Special Purpose
- Repair Construction
- Post-Event
Routine Inspections, Structural Repair or Upgrade Design Inspections, Special Purpose Inspections, and Repair Construction Inspections define routine maintenance activities and help owners understand what they need to do to take care of their facilities.
The primary inspection used to provide typical condition information, and to determine if and when other inspections should be conducted, is the Routine Inspection. The Routine Inspection, when performed by knowledgeable inspectors, can identify the degradation mechanism and assess its significance in regard to the structure’s capacity. Using the data collected from multiple Routine Inspections, the variations in the observed degradation can be used to estimate the rate of deterioration, helping the various stakeholders budget and plan.
Special Purpose Inspections collect additional and necessary information to aid the engineer and owner in understanding the cause of the degradation and to help select the appropriate intervention method: Routine Inspection, preservation, repair, or rehabilitation.
Once the decision is made to preserve, repair, or rehabilitate a structure, a Structural Repair or Upgrade Design Inspection is conducted. There is a time lapse between the Routine Inspection, assessment, recommendations, and award of a design/construction contract. During this period, the degradation continues, so the Structural Repair or Upgrade Design Inspection collects data on this additional degradation. The rehabilitation method should be chosen as part of this effort, so that the information relative to the limits of the repair can be collected.
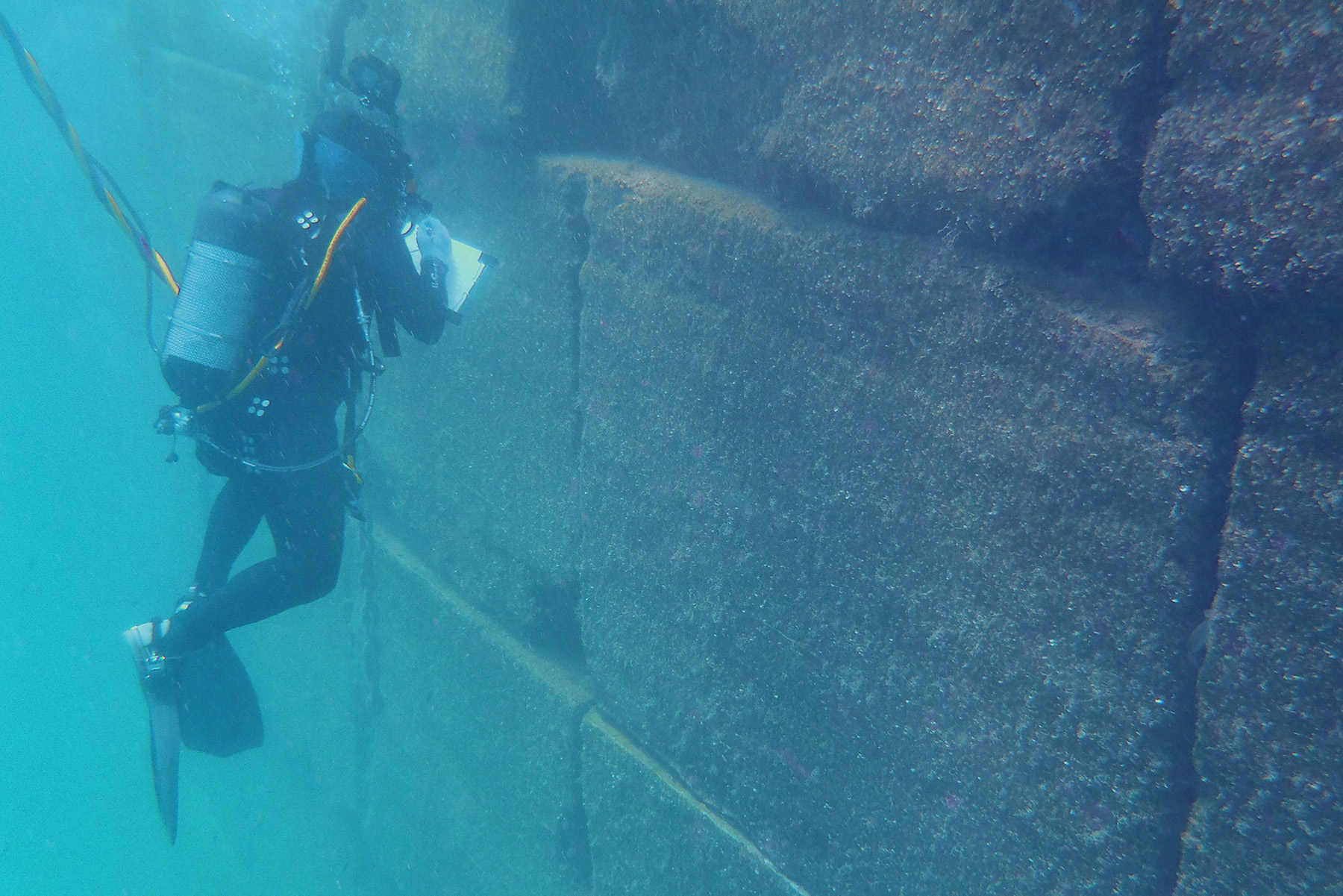
The other and probably more important purpose of the Structural Repair or Upgrade Design Inspection is to document the site conditions. Documenting the site conditions, including tidal limitations, accessibility, obstructions, etc., gives contractors the information needed to identify costs affecting their efforts.
Controlling costs is vital, which is the purpose of the Repair Construction Inspection. The key element in managing costs, provided the contractor is aware of the access limitations and obstructions, involves limiting the material quantities. Historically, the contractor decides the extent of the removal process. The cheapest elements to remove are the ones adjacent to the repair area.
Careful attention should be given to managing the repair process to prevent excessive removals exceeding the construction budget. Therefore, it is critical to conduct Repair Construction Inspections to achieve agreement among the owner, engineer, and contractor as to the areas of removal and repair.
New Construction Inspections identify construction defects — above and below water — for the owner. Providing these services as the construction progresses allows the contractor to repair or replace the damaged elements without additional mobilization and with fewer obstructions. For example, identifying a damaged pile before the pile cap is placed allows the contractor to replace the pile at minimal cost. The inspection does not replace the code-required special inspections, sampling, and testing.
If a facility has never been inspected or if there is limited information about the structure, a Baseline Inspection is conducted. This inspection lays out the basic geometry of the structure as well as the condition of the elements.
With the change in ownership of a facility, the new owner typically wants to know the condition of the facility and what the recommendations are for maintenance and rehabilitation as they relate to the new operations. A Due Diligence Inspection provides an assessment of the structural condition and recommendations for maintenance and rehabilitation so that those costs can be captured as part of the financial assessment.
An inspection that is conducted after a significant event — such as an earthquake, tsunami, hurricane, or allision — would be identified as a Post-Event Inspection. These are typically limited to inspection of the areas impacted by the event.
Testing
In some cases, after conducting a Routine Inspection, there is insufficient information to select the appropriate means of intervention. To collect this information, a testing regimen or a sampling-and-testing regimen is required. Testing can be used to measure the potential for corrosion, determine the cause of the degradation, develop chloride profiles, or determine the material properties of the construction material used on the facility, such as timber, steel, or concrete.
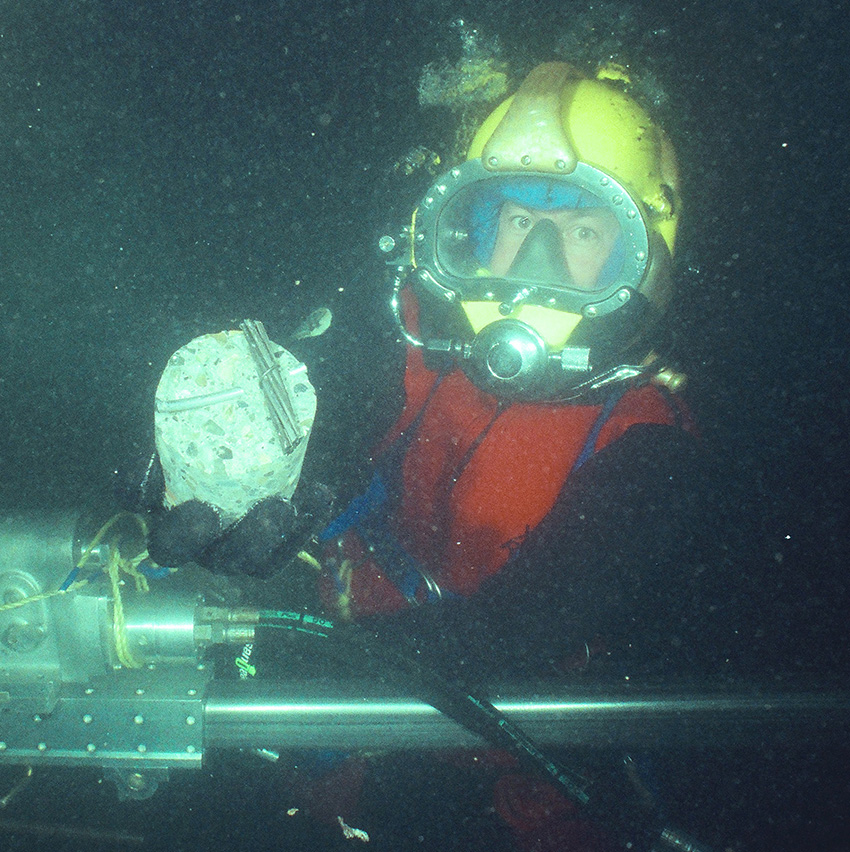
These are some of the tests that can be used as part of the process to determine if the structure should be rehabilitated or the Routine Inspections should continue. Testing can also be used to proactively monitor and assess a structure.
Various methods of testing common to buildings and bridges, including nondestructive and destructive, are used for waterfront structures, sometimes adapted to the marine environment.
For marine structures — that is, waterfront structures in a saltwater environment — sampling and testing reinforced-concrete components for chlorides (at the level of the reinforcing), sulfates, alkalinity, and chemical reactions are essential to understanding the cause of concrete deterioration and the state of steel-reinforcement corrosion.
Corrosion (electrochemical) potential testing is often performed on steel and concrete members to evaluate if corrosion is occurring or if the members are adequately protected. Ultrasonic testing, which relies on high-frequency sound waves, is commonly used to assess the remaining thickness of steel members.
Sampling and in situ testing of timber members is also performed to detect internal decay from the high moisture, the submerged environment, or damage from organisms.
Damage and overall system ratings
A damage rating is assigned to each element inspected during an investigation. The rating — no defects, minor, moderate, major, or severe — reflects the condition of the individual element only, and it is independent of the element’s structural importance and the type of inspection being conducted. Element-level damage ratings are standardized to provide a qualitative description of an element’s condition based on a quantified level of damage. By using a quantified scale, objectivity is maintained throughout the inspection. There are damage rating criteria for timber, steel, reinforced concrete, prestressed concrete, moorings, fenders, and utility elements.
This element rating system is based on the degradation/rehabilitation of the element and not its residual capacity.
At a higher level, each of the various portions of the structure gets its own rating using condition assessment rating criteria. These ratings, known as overall system ratings, rely on professional judgment to roll up the element-level damage ratings to understand the impact on the overall structure.
There are six numerical categories for Routine Inspections: good, satisfactory, fair, poor, serious, and critical (6-1, respectively). The rating system used for Post-Event Inspections differs from that used for Routine Inspections because Post-Event Inspection ratings must focus on event-induced damage only. There are four alphabetical categories for Post-Event Inspections: no significant damage, minor to moderate damage, moderate to major damage, or major event-induced damage (A-D, respectively).
Rehabilitation
Rehabilitation encompasses the acts of preservation and repair, and there are subtle differences between the two. The process of deciding which act is appropriate requires a thorough understanding of the degradation, the rate of degradation, and the desired service life of the structure. Some of the degradation mechanisms are such that the structure cannot be repaired or preserved; in some cases it needs to be replaced.
The cheapest way to achieve long-term durability of a structure is through early intervention. If this is not accomplished as part of the construction process, then preservation techniques should be used to extend the service life. The earlier the intervention, the more economical the service life extension is.
The key to preservation is that the structure must still have structural capacity, and the degradation mechanism must be understood. The next step is to select a preservation method that removes the element causing the degradation.
Some of the key preservation methods are sealers, coatings, wraps, nonstructural encasements, and cathodic protection. For concrete, the typical sealers are silanes, siloxanes, siliconates, silicates, epoxies, high molecular weight methacrylates, methyl methacrylates, and polyurethane. With most of these products, the crack size is the key metric in selecting the sealer.
Wraps are used as barriers to minimize the ingress of elements (such as chlorides and oxygen). Cathodes can be used to protect steel reinforcing from further corrosion. Initially, the concrete and the concrete cover protect the steel. Over time, the protection erodes and corrosion begins.
For steel, the initial means of protection is a coating. But over time, coatings break down, allowing corrosion to occur. Maintenance of the coating is the easiest way to extend the service life of steel. However, surface preparation is a critical factor in the performance of coatings, and in many instances, surface preparation cannot be satisfactorily achieved in the marine environment. If the coating cannot be restored, then the application of wraps or nonstructural encasements is selected.
For these methods to be effective, removing the oxygen from the corrosion process is essential. As stated above, cathodic protection is used to safeguard steel from corrosion. This method is effective in wet or underwater environments but not in the splash zone or above water. To extend the protection into this zone, cementitious material is typically used.
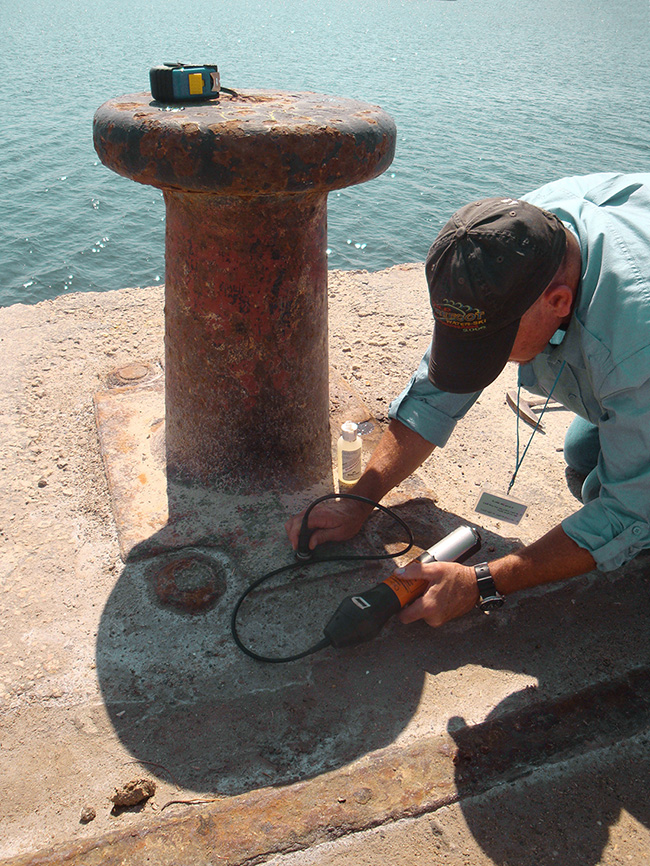
For timber elements, coatings, wraps, and nonstructural encasements are typically used to isolate them from moisture or marine borers. Historically, timber structures were dual treated, with the outer coating treatment being creosote. Current restrictions limit the use of creosote in the marine environment, thus reducing the effectiveness of the treatment in resisting marine borers.
Coatings, wraps, and sealers are used to provide a barrier against the marine borers. The effectiveness of the methods depends on the application and quality of the work.
When structural capacity needs to be restored or increased, repair and rehabilitation methods should be selected (as opposed to preservation). The typical methods to restore structural capacity are localized patching, structural encasements/jackets, or replacement. For localized patching repairs, the damaged components are removed and new components installed.
Structural encasements transfer the load from a good section, around the repair area, and back into a good section. To be effective, a development length — a length in which the repair overlaps the good section of the member — is necessary to transfer the load.
Most encasements are made up of a translucent form, a steel-reinforced cage, and a cementitious material.
Sometimes an element must be removed and replaced. It could be a pile, pile cap, beam, or deck element. With any of these methods, the load path and load transfer should be carefully considered. With any degradation or removal, the loads are transferred to the adjacent elements. If it is necessary to restore the original load path, proactive measures should be taken to restore it.
Many rehabilitation techniques inadvertently introduce degradation mechanisms. For example, for concrete repairs, a localized corrosion cell that affects the existing reinforcing can be introduced; with steel repairs, dissimilar materials can be inadvertently added among the parent or repair metal or the weld material; and with timber repairs, cutting or drilling through the coating exposes the untreated sections to fungal decay or marine borers. To truly rehabilitate a structure, we need to design a repair that addresses the degradation mechanism as part of the repair, restores the capacity, and mitigates any introduced degradation mechanism.
The process of inspection, testing, and rehabilitation is a comprehensive program necessary to manage marine assets for the long term. These marine structures are the key infrastructure pieces for global commerce. Waterfront Facilities Inspection and Assessment and other ASCE publications provide guidance to implement a comprehensive marine asset management program.
Thomas Spencer, P.E., S.E., P.Eng, BC.PE, M.ASCE, is a vice president with Moffatt & Nichol. Sean Chapman, P.E., M.ASCE, is a vice president with Marine Solutions Inc. in Nicholasville, Kentucky. Noah Elwood, P.E., BC.OE, BC.PE, M.ASCE, is the president of Appledore Marine Engineering LLC in Portsmouth, New Hampshire.
Manual of Practice 130, Waterfront Facilities Inspection and Assessment, 2nd ed., guides engineers through the specialized field of inspecting and assessing waterfront facilities. The new edition includes updates of all sections as well as content on composite materials and the latest innovations in inspection tools and technologies.
Special course at Ports ’25
The special short course Inspection, Testing, and Rehabilitation of Waterfront Structures will be offered at the Ports ’25 conference June 1-4 in Providence, Rhode Island. This course presents the current standards of practice for waterfront facility inspections and assessments in accordance with ASCE’s Manual of Practice 130, Waterfront Facilities Inspection and Assessment, as well as current practices for testing and rehabilitating waterfront infrastructure.
This article first appeared in the May/June 2025 issue of Civil Engineering as “Waterfront Watch.”