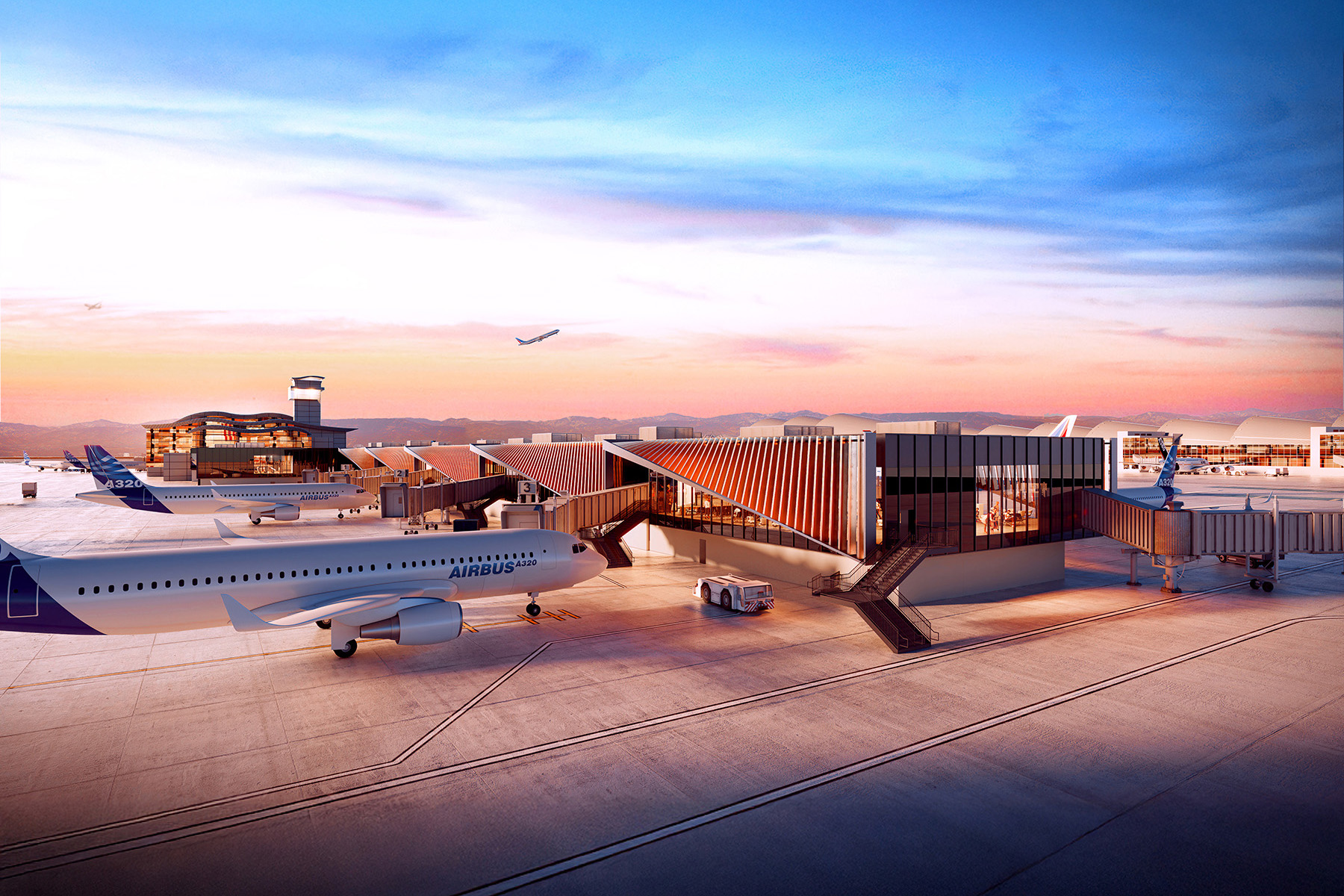
By Derrick Roorda, P.E., S.E., Louisa Phillips, P.E., and Stuart Brumpton
Los Angeles International Airport is building a new concourse — via an innovative off-site construction and relocation method — that celebrates the city’s modernist appeal and prioritizes sustainable design.
The new Midfield Satellite Concourse South at Los Angeles International Airport expands the facility’s international terminal by adding eight gates for narrowbody aircraft. Designed by Woods Bagot with associate architect Raw International, the concourse totals approximately 150,000 gross sq ft of new construction.
Led by W.E. O’Neil, construction of MSC South has garnered attention for employing a first-of-its-kind approach at LAX: off-site construction and relocation. The governing body for LAX, Los Angeles World Airports, and the project teams chose the OCR approach because it reduces construction costs and improves logistics by minimizing inflow and outflow of personnel, equipment, and materials on the tarmac. Access to the tarmac is normally limited by strict security protocols.
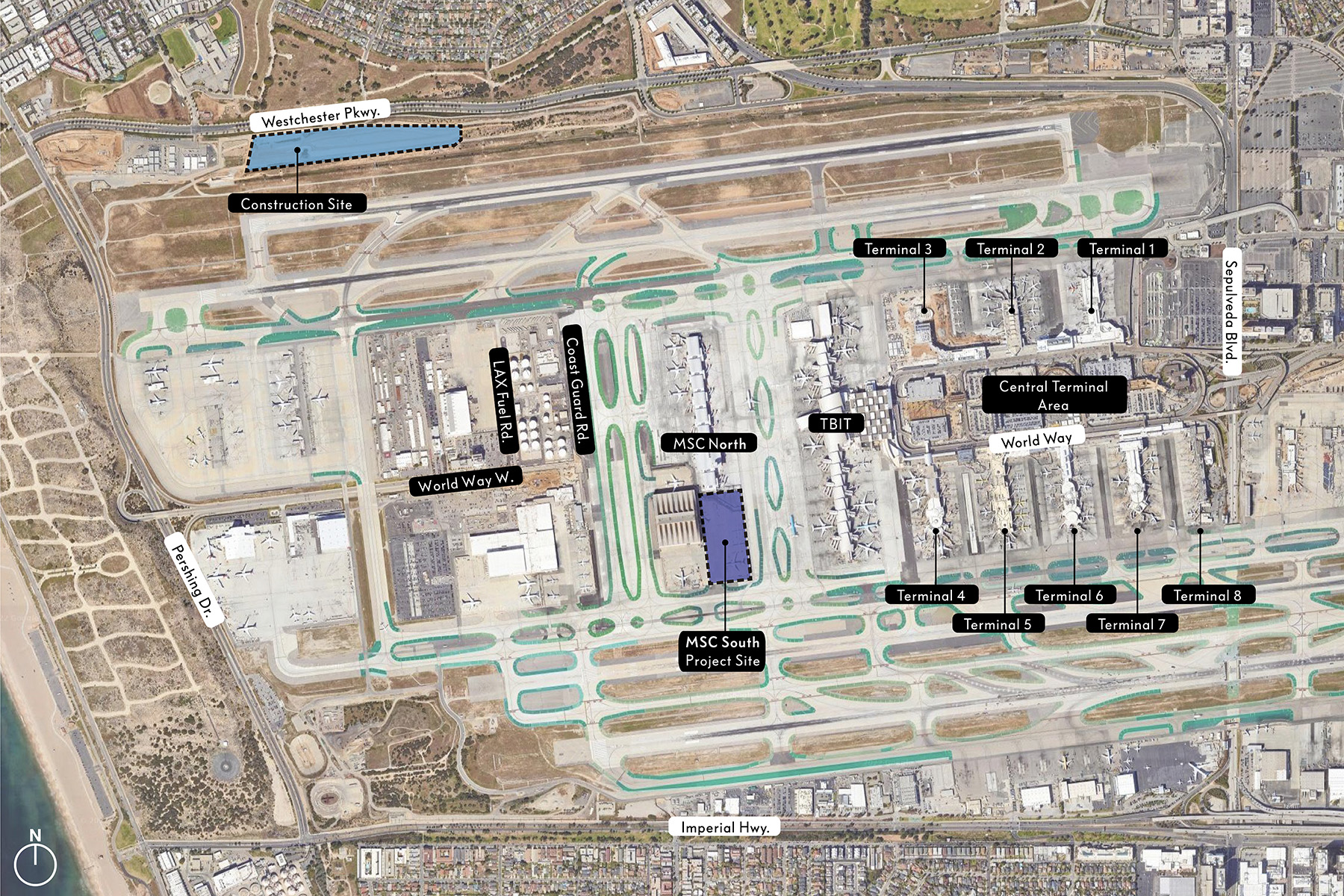
Additionally, the OCR method has provided another benefit: allowing airport operations to continue uninterrupted in more areas and for longer periods than conventional on-site construction would have permitted.
The engineering team proposed constructing MSC South in nine separate rectangular segments at a yard adjacent to LAX’s north airfield, roughly 1.5 mi away. Each segment is a two-story building 140 ft long by 80 ft wide with a footprint of approximately 10,000 sq ft. Once complete, the segments were transported and positioned in place, then secured to the concrete foundation built on-site. This innovative and adaptive method has saved public funds and time while guaranteeing stringent building control and supervision.
Approaching the final stages of construction, MSC South pays homage to LA’s iconic modernist legacy, and it is emblematic of LAWA’s commitment to thoughtful, sustainable design.
Segmented construction
The MSC South project bears little resemblance to conventional modular construction. The key difference is that for typical modular construction, the modules or segments are on scale with a shipping container or small room; however, the segments for MSC South are essentially discrete two-story buildings.
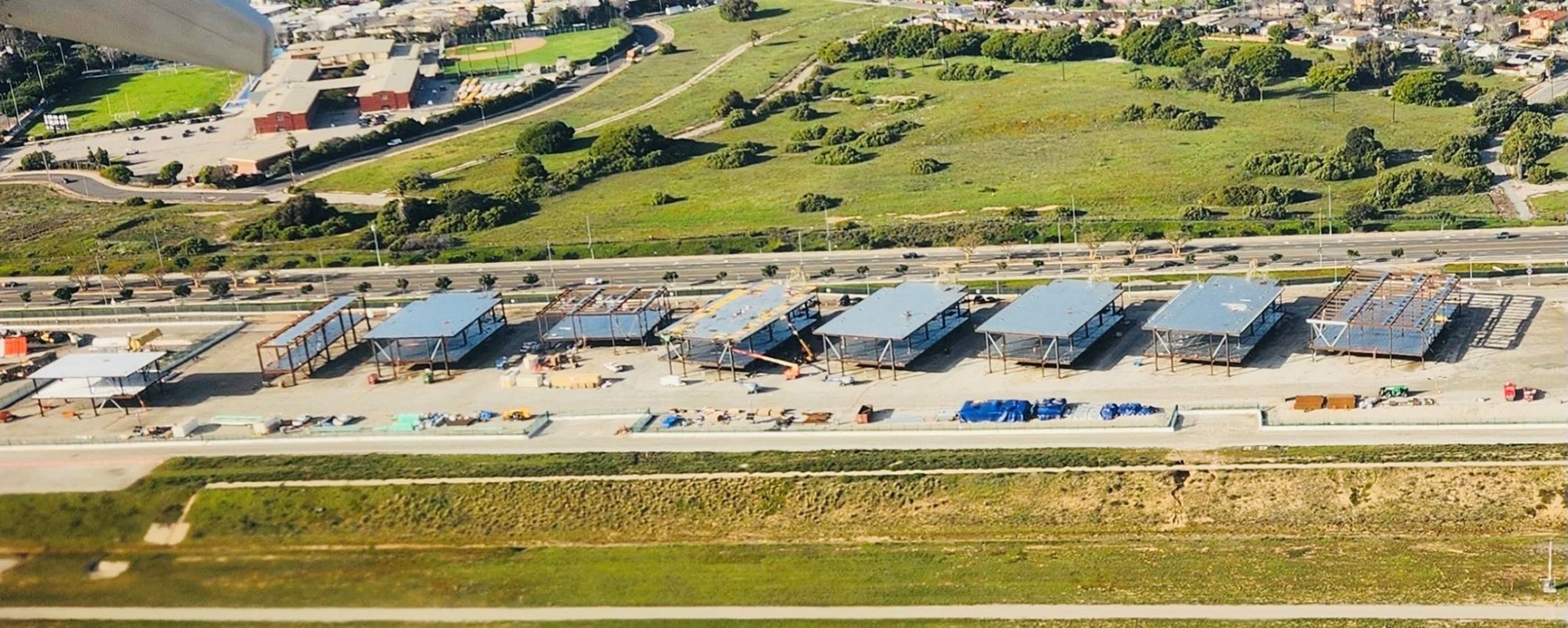
All nine segments have an upper gate level and a lower tarmac level. The segments will serve multiple functions: The first four, leading from MSC North, are for passenger pass-through and are equipped with conveniences and amenities, followed by gates for boarding flights in the other five. Restrooms are included in two of the nine segments. Lower levels are for secure, non-passenger areas for baggage transport and employees.
This challenging and complex project has required:
- Designing the structural frame, including seismic joints.
- Planning and staging transport from the OCR yard to the final site.
- Positioning and securing each segment to its foundation.
Because the purpose of OCR was to minimize traffic in and out of LAX’s airfield, the project team completed as much segment construction as possible before transporting the segments to LAX, including the facade, interior walls, mechanical infrastructure, and roofing — everything that could withstand the transport process. The segment construction is fairly lightweight, composed of conventional steel framing with a concrete floor slab on a metal deck separating the upper and lower levels. The roof is composed of steel girders and metal decking.
Stability and delivery
Addressing the region’s seismic activity required additional attention and care. To withstand an earthquake, the nine independent segments are reinforced with stability systems that can prevent or adapt to movement, made possible with buckling-restrained braced frames along the east-west orientation and Simpson Strong-Tie Yield-Link moment-resisting frames across the north-south direction, specially detailed to react to intense seismic magnitudes. The design team chose these frames because they allow bolted connections, and the yielding-link mechanism connecting column to plate is replaceable, which is important in the event of an earthquake.
Since the guiding principle was to perform as little labor as possible after moving the segments into place, including activities like welding, installation consisted of situating each segment and securing and tightening the anchor rods and coupling nuts.
Transportation and relocation
To transport the steel-frame segments from the off-site yard to the airfield, the project team proposed an atypical method. Logistics teams lifted the segments by the midsection concrete and metal deck instead of placing most of the load on the columns. The approach created an unusual load path situation. In this temporary condition, there was greater shear force in the floor beams than what they will bear under typical circumstances.
To accommodate expected transportation-induced stress, the team prepared designs to include approximate locations of the hydraulic lifting mechanisms that were placed underneath the deck. After testing mechanism layouts and coordinating with transportation and logistics firm Mammoet, engineers finalized their designs to ensure the constructed segments would not be damaged during transport.
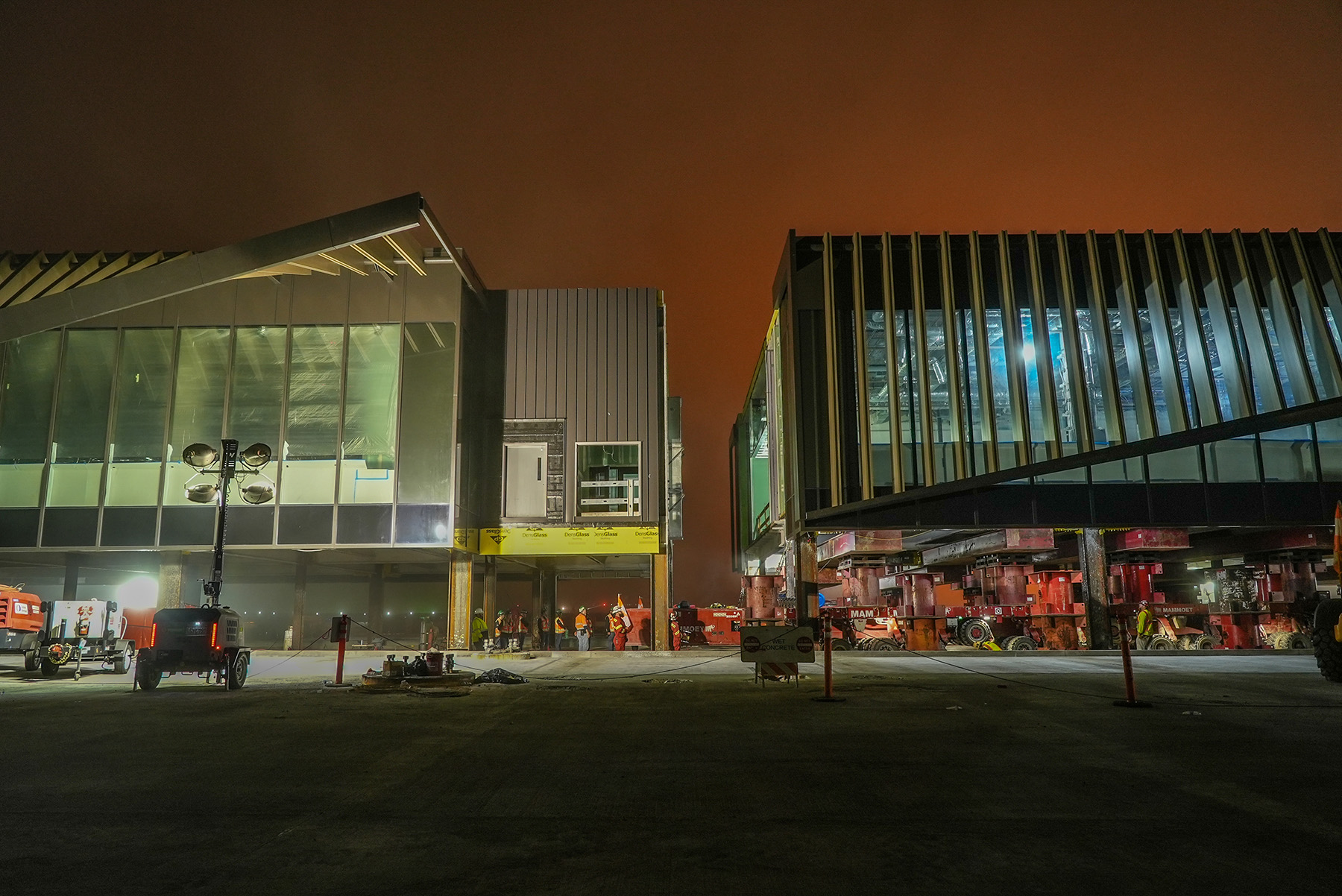
Because they were built to be flexible, Mammoet accounted for movement and adjustment as loads shifted from the columns to the floor beams. Additionally, the segments required uniform and simultaneous lifting because lifting only one corner at a time would have damaged the frame. Global consultancy Buro Happold outlined a proposed procedure for lifting and transportation and how to measure tolerated differential movements, provided to Mammoet in a tolerance report.
The transport team chose self-propelled modular transporters, each with four to eight axle lines and engineered to support up to 44 tons per axle. SPMTs can be connected in a variety of configurations to create “platforms on wheels,” able to carry enormous and unwieldy loads for short distances and execute 360-degree turns in place, as well as sideways movements. The plan required hydraulic lift mechanisms atop these mobile platforms, which arrived at the construction site and were positioned underneath the concrete deck to be lifted. The segment was then moved to its location on the airfield, positioned precisely over the foundation, and carefully lowered.
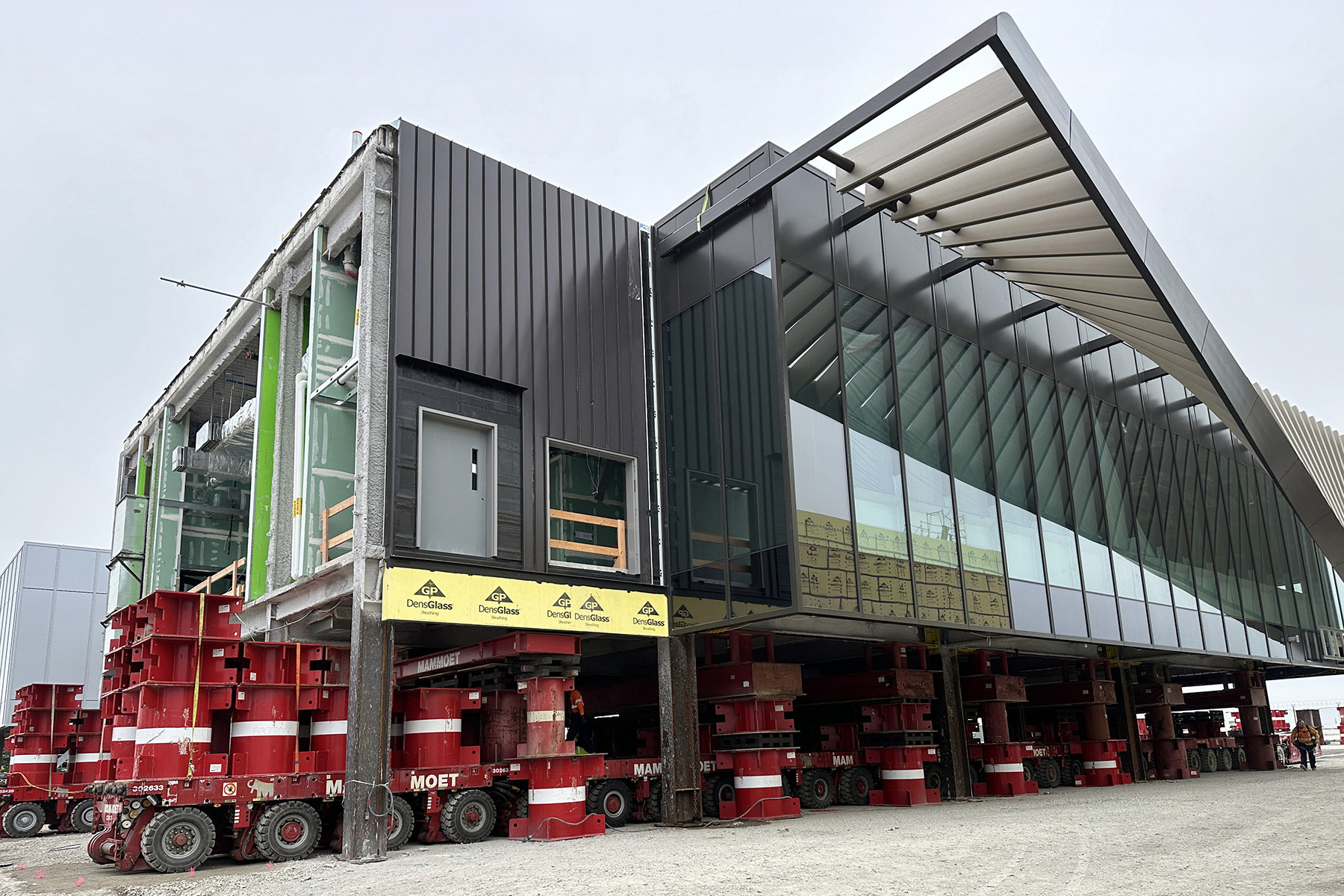
For this part of the process, the engineers diverged from conventional design practices when deciding how to connect the steel frames to the concrete foundation. Typically, when concrete is placed, steel anchor rods project upward, over which base plates are lowered and the connection secured by tightening the nuts. The mobile platforms prevented this typical procession from happening, so the engineering team devised a unique detail: a joint in which the rods were exposed within small cavities in the foundation, terminating just below the surface of the concrete.
Below the surface level, a coupling nut was attached to each rod end within the cavity, resulting in a completely flat plane for the SPMTs to drive over and position the segments. Once in place, the segments were lowered to align all connectors — at least four and up to 12 connectors at the base of each column — with no more than 1/4 in. to spare in any direction.
It took between two and four hours to move each segment from the OCR site to the project site. A two-day gap between each move allowed the transporters to return to the OCR yard to prepare another segment for relocation.
Closures and facades
Designed as a series of independent buildings, MSC South’s only lateral connections between segments are closure assemblies for pedestrian paths. Each assembly is a flexible accordion-style fan fold composition to accommodate possible shifts or movements. The segments are structurally independent, designed not to come into contact with one another. Sufficient separation between them is required so that a seismic event will not cause the segments to damage each other.
A simple floor-over-floor overlap smooths the concourse-level pedestrian path at connection points, protecting passengers from encountering the seam between segments. The overlap is designed to accommodate up to 6 in. of movement, while the connection at roof level can handle up to a 12 in. differential.
The facades for the east and west sides of the concourse level of each segment are primarily full-height, 20 ft tall glazing that extends between the roof and the concrete deck. The glass enclosure permits natural light and unimpeded views of the airfield and landscape. A brise soleil architectural element affixed to the facade exterior is angled downward and provides shading for the concourse interior during morning and evening hours, reducing solar heat gain and enhancing overall energy efficiency. Below, the 14 ft high secure apron level used by airport and vendor employees is enclosed primarily with metal paneling.
Notably, the interior of the apron level within the segments leading out from the terminal will accommodate electric transport carts that take passengers to baggage claim in the main terminal.
Integrated engineering
Buro Happold assisted with project delivery. The firm also provided structural engineering and integrated project services, including lighting design, acoustics, and sustainability consulting.
As with the development of the structural system, the goal is to support an environment that optimizes the passenger experience, meets sustainable design and operation benchmarks, and minimizes construction time and costs.
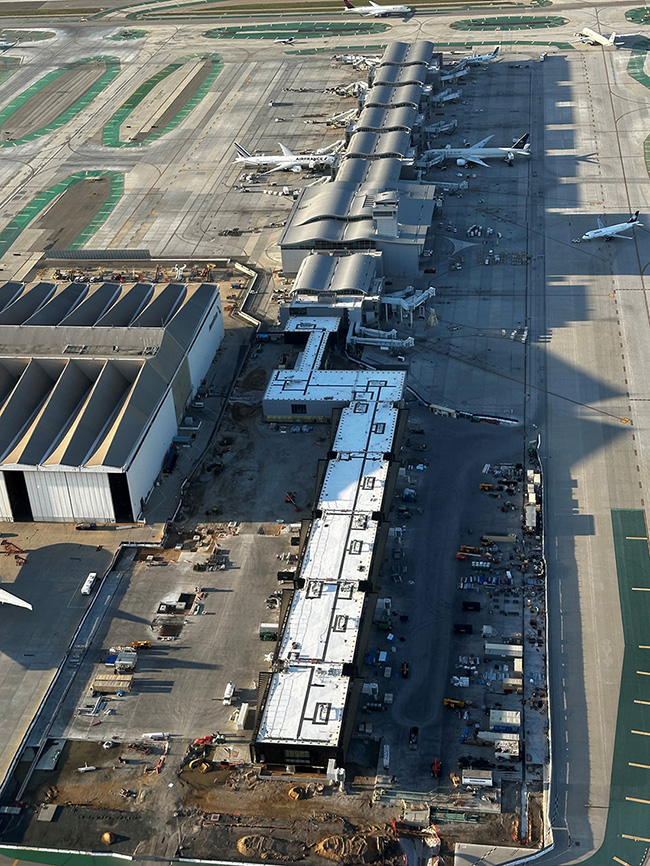
The floor-to-ceiling space was designed to dampen the sounds of airplane engines, with the minimum acoustic performance of the facade ultimately determined by the 2022 California Green Building Standards Code, Title 24, Part 11.
The acoustics team’s design ensures that the enclosure attenuates noise produced by generators, rooftop heating, ventilation, and air conditioning equipment; employee activity on the lower floor; and any other sources of high-volume sound.
The design also includes neoprene bearing pads to ensure acoustic separation at joints, corners, and seams, especially at locations where the steel structure comes into contact with concrete.
Woods Bagot designed the concourse-level ceiling to include an exposed plenum. To create visual interest and define zones, architects chose linear LED fixtures instead of can downlights. The linear fixtures — each a foot deep by an inch wide and 20 ft to 30 ft in length — will commingle with suspended acoustic baffles for reduced ambient noise.
Buro Happold’s lighting and acoustics engineers worked extensively with Woods Bagot to arrive at the ideal configuration, comparing the sizes and spacing of the baffles to create an integrated ceiling with a vibrant aesthetic. The integrated ceiling design visually defines passenger circulation and seating zones through application of materials and finishes.
The result is seating areas that feel spacious and lounge-like rather than merely functional.
Designed for longevity
The project is aiming to achieve LEED Silver certification, which will encompass rigorous social, economic, and environmental standards.
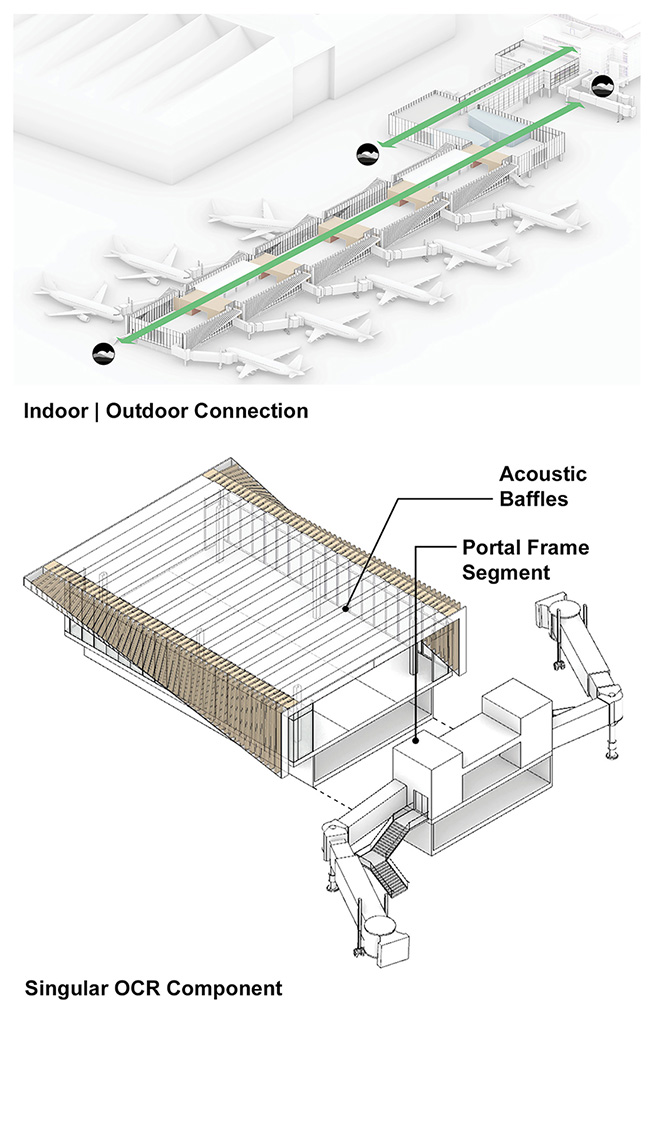
Regarding the overall sustainable design, it is notable that the segment structure embraces the cradle-to-cradle approach in regard to the building’s lifespan.
The design supports future disassembly and refurbishment for reuse. Better still, minimizing the number of welding points makes it entirely possible to detach, lift, and move each component to another area of the airport should LAWA elect to have it used elsewhere.
A top priority for LAWA has been ensuring that people and businesses in the neighborhoods surrounding LAX are part of the modernization effort, benefiting from it directly and indirectly.
The OCR method helped address social inequity by opening up a wider pool of local workers who may not have been security cleared. This included trades and subtrades and all project logistics from delivery drivers to concrete pourers.
More than a third of the 451 workers on the MSC South project were hired from the local community, some through the airport’s HireLAX Apprenticeship Readiness Program.
LAWA and the project team will meet the project’s rapid seven-month timeline without sacrificing design excellence or precision. The project will be completed by September 2025 and achieve LAWA’s goals of an enhanced passenger experience in a state-of-the-art concourse, sustainably built and high performing, setting a new bar for world-class design in the aviation sector.
The entire project team is proud that — in addition to being innovative, cost effective, time saving, and highly sustainable — the OCR approach has generated an economic boon for the surrounding communities.
Derrick Roorda, P.E., S.E., is a principal in Buro Happold’s San Francisco office. Louisa Phillips, P.E., is a senior structural engineer in Buro Happold’s New York City office. Stuart Brumpton is a principal in Buro Happold’s Los Angeles office.
Project credits
Design architect
Woods Bagot, Los Angeles
Associate architect
Raw International, Los Angeles
General contractor and construction manager
W.E. O’Neil, Los Angeles
Structural engineer and sustainability, lighting, and acoustics consultant
Buro Happold, Los Angeles
Civil engineer
Mott MacDonald/MA Engineering
Los Angeles
Mechanical and plumbing engineer, vertical transportation
Syska Hennessy Group Inc., Los Angeles
Electrical engineer
PBS Engineering and Environmental LLC, Los Angeles
Geotechnical engineer
Diaz•Yourman & Associates, Santa Ana, California
Baggage handling, passenger boarding bridges, and fueling
Swanson Rink, Denver
IT, communications, and security
TLC Engineering Solutions, Los Angeles
Wayfinding
Selbert Perkins Design, Los Angeles
Site investigations and surveying
Pfeiler Psomas, Yorba Linda, California
Group code compliance
Jensen Hughes, Los Angeles
Fire protection
Schwab Engineering Inc., West Hills, California
This article first appeared in the May/June 2025 issue of Civil Engineering as “Portable Concourse.”