Brightline, the Florida-based builder and operator of the nation’s first privately funded passenger rail system in more than a century, had a problem. The company opened its first route between West Palm Beach and Fort Lauderdale in January 2018, expanding to Miami by May of that year. But as the company worked on another extension — from West Palm Beach to the Orlando International Airport — it ran into a series of challenges for the planned underpass to carry its high-speed trains beneath State Road 528 in Cocoa, which is in Brevard County.
SR 528, also known as the Beachline Expressway, runs east to west from Brevard County to Orlando and is an extremely busy highway that could not be shut down for construction of the underpass, explains Matt Carroll, P.E., , a Brightline assistant project manager. The road carries beachgoers to and from Cocoa Beach, cruise ship passengers heading to or leaving from Port Canaveral, and space industry employees and visitors trying to access the nearby Kennedy Space Center. It is also designated by the Florida Department of Transportation as a key hurricane evacuation route, which means that the volume of traffic on the road cannot be severely limited during the region’s hurricane season, June 1-Nov. 30.
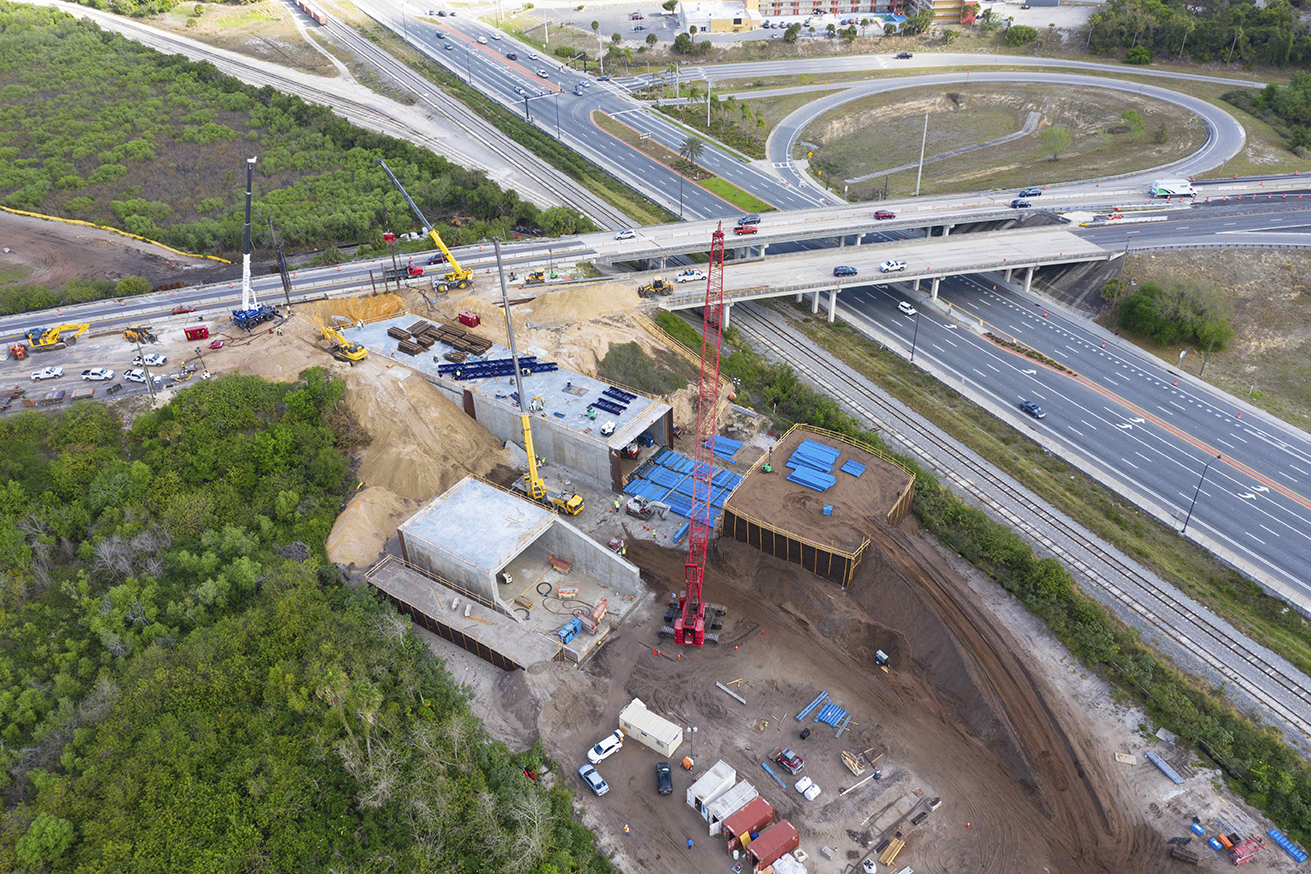
Two options
Those constraints left Brightline with two options, an expensive, yearlong major modification to the surrounding roadways utilizing a multiphase cast-in-place approach or a method to construct an underpass within the allotted six-month window, Carroll notes.
The innovative solution that was selected — an alternative technical concept, provided in the bidding process for the east-west corridor of the Orlando extension project by Granite Construction Inc. of Watsonville, California — involved a method popular around the world though relatively unconventional in the United States. But it would get the job done in a fraction of the allocated time.
Called box-jacking, the approach involves the use of hydraulic jacks to push precast concrete boxes into position to create an underpass beneath a roadway. An anti-drag system — composed of steel plates, a latticed steel retaining beam, tensioned anchoring cables, and a biodegradable lubricant — makes it possible to slowly slide the boxes beneath active roadways.
The underpass beneath SR 528 became the first project to use this technique in North America beneath live traffic, according to Carroll.
The box-jacking method was created by the Italian firm Petrucco Italia SRL, which served as a subcontractor to Granite on the project. Petrucco has used the method extensively, previously constructing more than 1,600 box-jack structures around the world. But there have been only a few applications that have used the method in North America. Granite and Petrucco previously used a similar approach on another portion of Brightline’s expansion to the Orlando airport. But, at that location — at Goldenrod Road, east of the airport — they were able to shut down the road entirely and slide the underpass into place by partnering with the local highway authority, Central Florida Expressway Authority, and the Orlando airport’s Greater Orlando Aviation Authority, Carroll says.
Shifting lanes
For the box-jack installation at SR 528 and U.S. Route 1, Brightline worked in close partnership with FDOT, the authority for this part of the highway. FDOT’s support of using the box-jacking method was key to moving the idea forward, explains Carroll. This was because the traffic phasing plans and timelines for the box-jacking operations were complex and had to be dynamic due to the intricacy of the work and the proximity of U.S. 1.
At the SR 528 site, traffic first had to be shifted to a single lane in each direction of the westbound lanes. “That allowed Granite and Petrucco to mobilize into the eastbound roadway to excavate in front of the box-jack alignment, creating space for the first segment and phase 1 of the box-jacking system,” Carroll says.
A 1 ft thick reinforced bottom slab — called the jacking slab — was constructed for the underpass boxes to slide across and a massive thrust block supported by engineered fill was constructed for the hydraulic jacks to push against, Carroll says.
Measuring 137 ft long by 51 ft wide by 31 ft tall and weighing 4,450 tons, the first block featured a chamfered edge in front to cut through the soil and prevent voids from forming under the active roadway. Twenty-one 550-ton hydraulic jacks pushed the first block forward about 21 in. at a time, with rectangular steel spacers set between the thrust block and the jacks. As the distance increased, a series of steel pipes, each about 20 ft long, eventually supplemented the spacers. This reduced the risk of eccentricity occurring within the spacers when they were loaded with the large forces necessary to push the segments under the roadway.
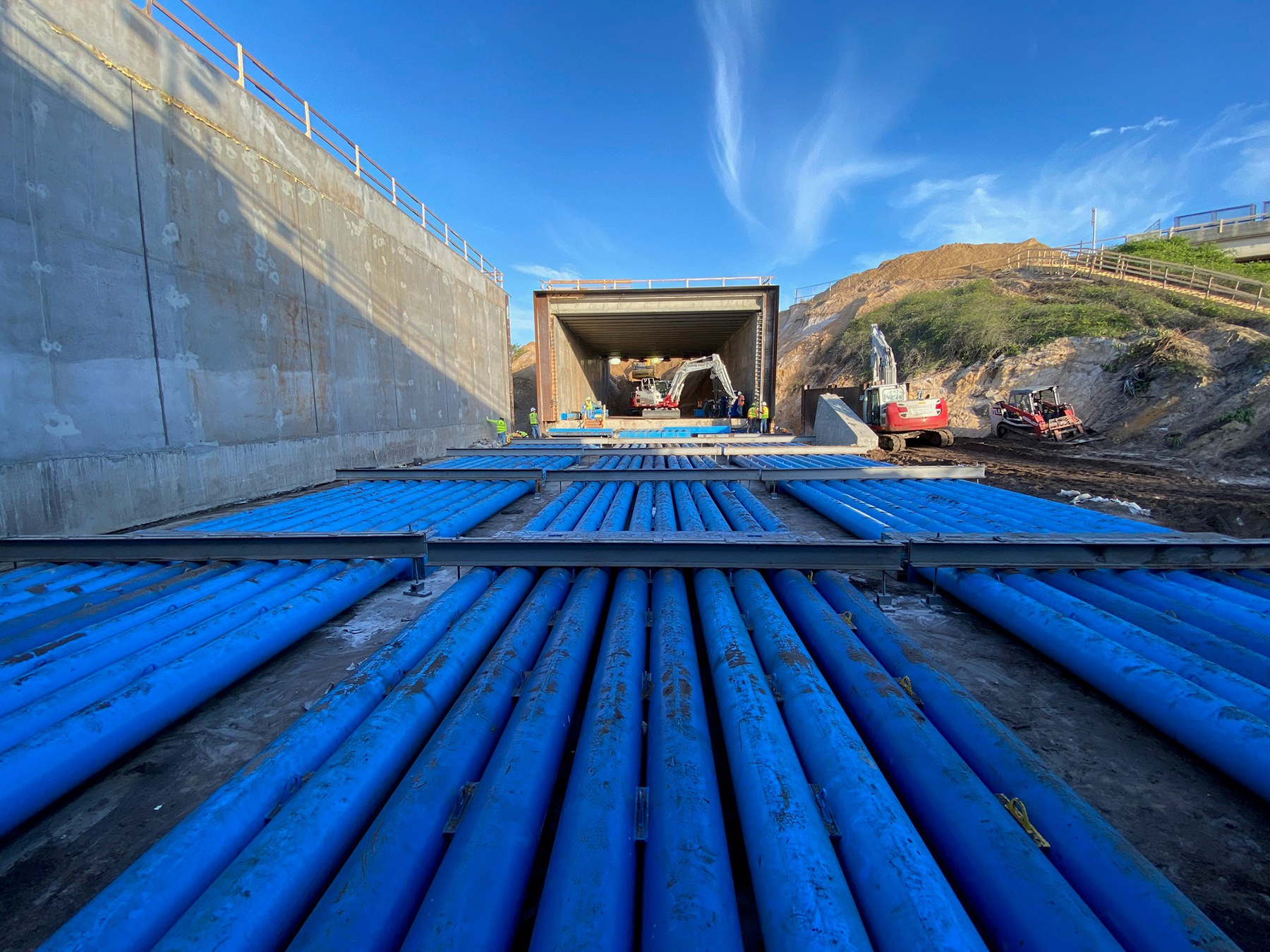
Cutting edge
The cutting edge of the lead box channeled soil into the open structure of the box as it was pushed forward, where a trio of excavators then removed the material that gathered. Once the first box had moved forward far enough, a second box — measuring 110 ft long by 51 ft wide by 31 ft tall and weighing 4,630 tons — was pushed into position behind the first box. The jacks were then repositioned to push the two boxes forward.
When the first box reached the location of the former eastbound lanes, an anti-drag system was installed on top of the structure, which featured so-called Florida I-beams — 36 in. deep concrete elements with an additional 9 in. thick reinforced top slab installed — as its roof structure. The steel plates of the anti-drag system were locked together and secured to a steel lattice retaining beam that was, in turn, anchored by tensioned steel cables to the jacking slab on which the boxes were moving. A lubricant grease was then constantly applied to the top slab to help the boxes slide beneath the steel plates. A new road surface was then constructed atop the steel plates, becoming the new eastbound lanes of SR 528.
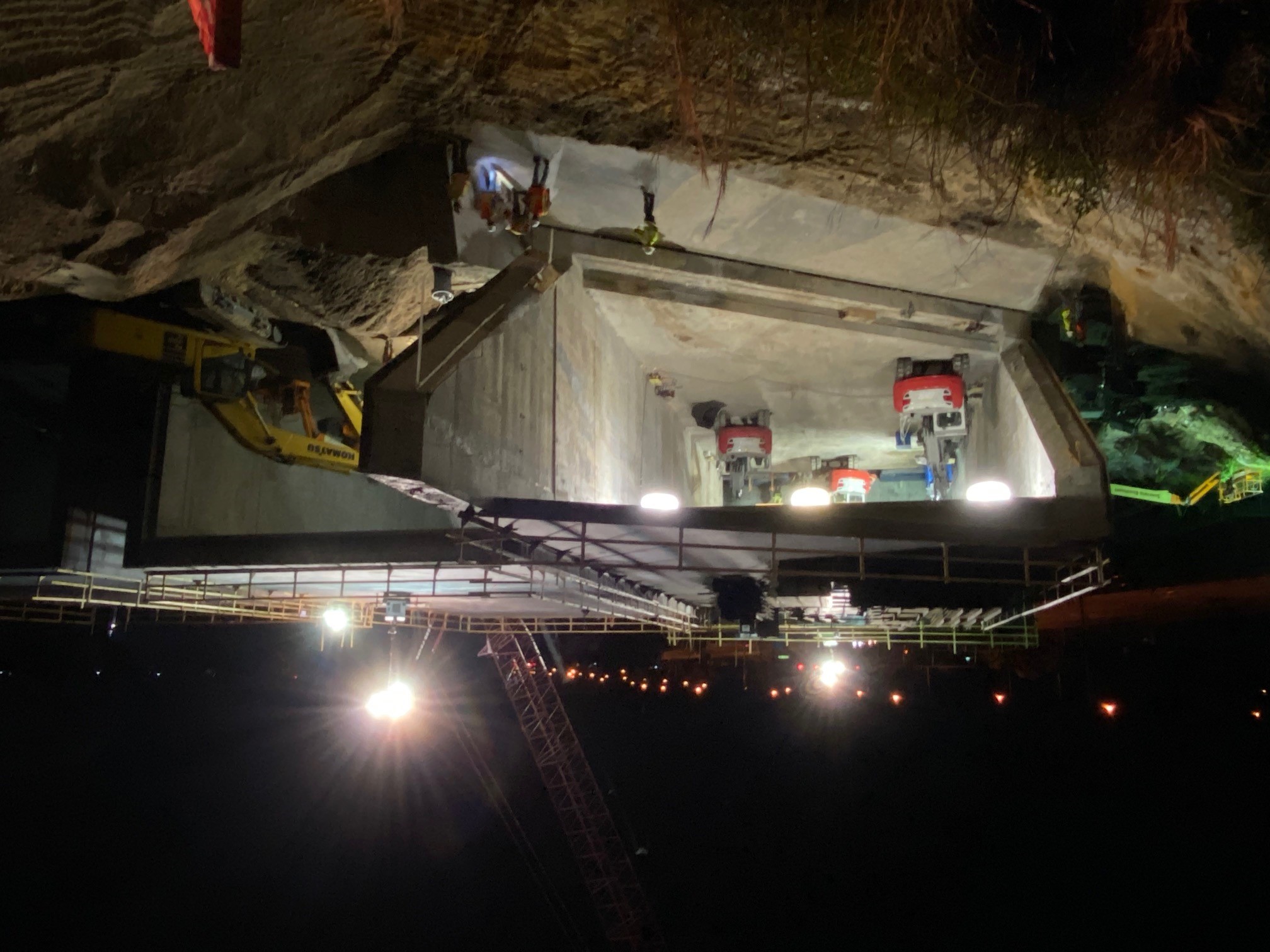
“The system essentially creates a floating roadway on top of the (underpass) segments, allowing them to freely move under active traffic without altering the travel way above,” Carroll explains.
Switching sides
At that point, traffic was shifted to single lanes in each direction on the new eastbound road atop the first and second box segments so that the original westbound lanes could be demolished.
The first two boxes were then slowly pushed forward beneath the new eastbound lanes until there was room to push a third and final box into place. The smallest of the three segments, the third box measured 110 ft long by 51 ft wide by 31 ft tall and weighed 3,260 tons.
Once the jacks had pushed all three boxes forward into their ultimate position, new westbound lanes were constructed atop the first and second boxes.
Because of the tremendous forces imposed on the boxes by the jacks — forces that threatened to misalign the tunnel both horizontally and vertically if not carefully controlled — the work proceeded more slowly than expected, Carroll says. As a result, the boxes moved forward at only about 2 ft per hour or less, rather than the 3 ft per hour originally expected. In the end, though, traffic on SR 528 returned to normal just 20 days after construction started.
The expansion gives Brightline the underpass it needs for its Orlando airport extension, which is expected to reach substantial completion by late 2022.
Although the box-jack project faced challenges, it also benefited from the sandy soil prevalent in Florida. The box-jacking method would be much more difficult in rocky conditions, according to Carroll. The technique also requires adequate space — several acres — on which to construct the jacking slab, thrust blocks, and box segments themselves as well as to stage the spacers and steel pipes for the jacks and other aspects of the work.
Support for solutions
Throughout the project, the ongoing support of partners, including FDOT was crucial, Carroll adds, because “the operation impacted a lot of people’s everyday travel routine. When developing the models and analyzing traffic flows of how we could keep traffic moving without causing backups, FDOT partnered with us on the technical aspects, execution, and public outreach of the project, making the operation successful while safely minimizing the impacts to the traveling public.”
In addition, HNTB, Brightline’s engineer of record for all construction along SR 528, was involved from start to finish in the box-jacking. HNTB reviewed the technical details and installation processes and adapted and designed the approved traffic control phases necessitated by the alternative concept.