By Jay Landers
To meet the sanitation requirements of its rapidly expanding population, the fast-growing city of Redmond, Oregon, must increase its wastewater treatment capacity. However, the city’s existing wastewater treatment facility has been hemmed in by development, precluding any chance of enlarging the facility’s footprint. Fortunately for the city, Redmond owns a large property outside of town. With plenty of land at its disposal, the city is planning to replace its existing mechanical-electrical treatment facility with lagoons and treatment wetlands.
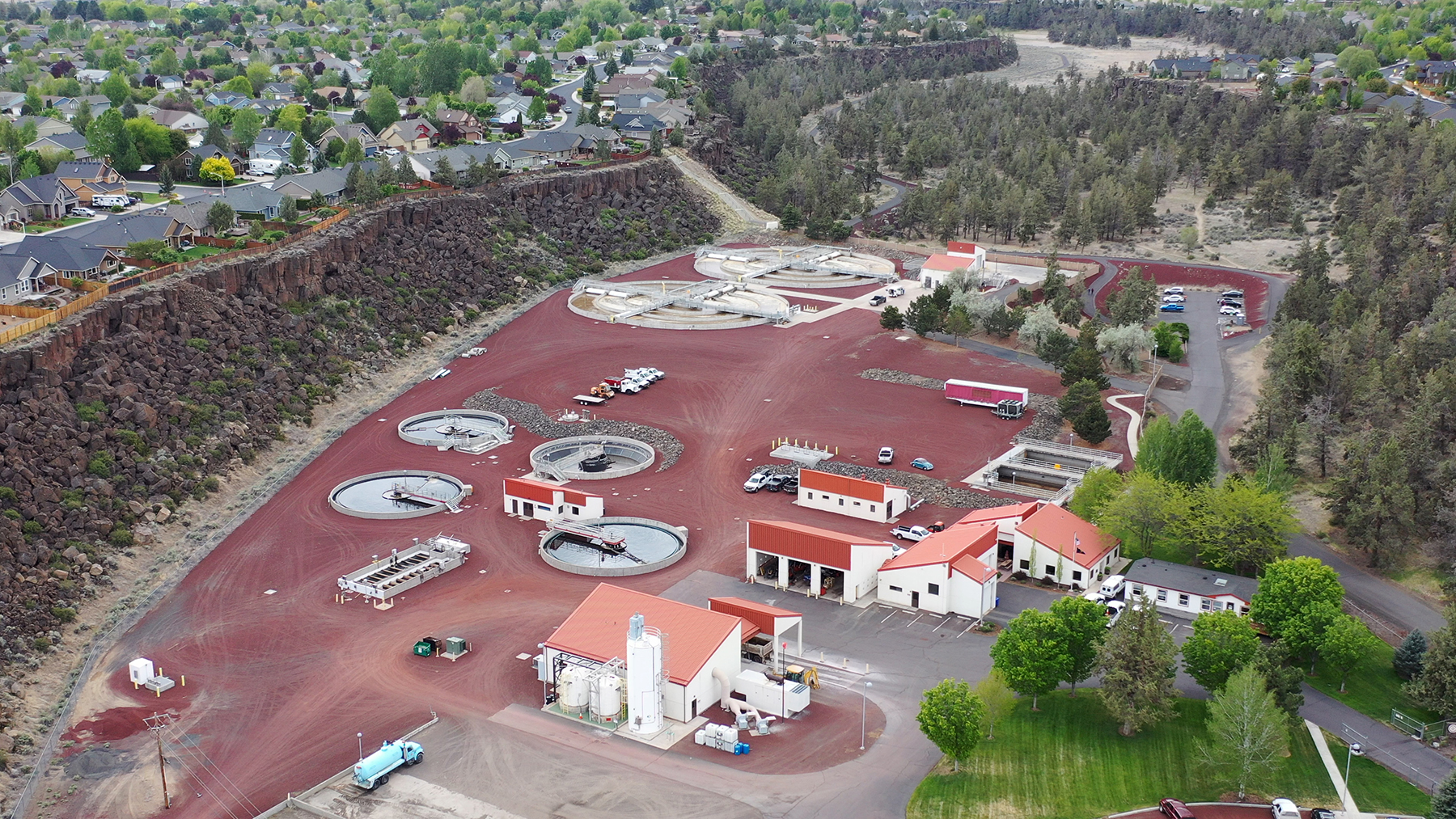
Known as the Redmond Wetlands Complex, the constructed wetlands system offers the promise of a treatment approach that is more cost-effective and sustainable than a traditional mechanical treatment plant. Along with creating wetlands habitat for birds and other wildlife, the project will provide recreational and educational opportunities for the local community.
‘Running out of footprint’
Home to some 35,000 residents, Redmond has seen its population triple since 2000, says Ryan Kirchner, the wastewater division manager for the city of Redmond’s Public Works Department. With central Oregon undergoing an “accelerated growth rate,” the population of Redmond is projected to reach 54,000 residents by 2045, Kirchner says. In the face of such growth, the city’s wastewater treatment infrastructure requires expansion.
Originally constructed in 1978 and last expanded in 2000, Redmond’s 2.8 mgd Water Pollution Control Facility consists of a headworks, concentric biological nutrient removal reactors, and secondary clarifiers. After undergoing dewatering by means of a belt filter press, solids are hauled by truck to a 610-acre site outside of Redmond known as the Effluent and Biosolids Complex. A pipeline conveys treated effluent from the treatment facility to the same site.
At the site, the effluent either is used to irrigate hay fields or is infiltrated to the underlying aquifer by means of four infiltration basins. The biosolids either are applied to the hay fields or are dried on-site and used as fertilizer by local farmers. In 2020, the city produced and sold 519 tons of hay that had been grown on its fields.
Initially, the city planned to upgrade, rather than replace, its existing treatment facility, Kirchner says. However, the limited space at the facility site prompted Redmond to reconsider. “We’re running out of footprint,” he says. As a result, upgrading the facility would have required optimization and not expansion. At the same time, the benefits of such an effort would have been relatively short term, Kirchner notes. “Knowing that at some point with the growth rate we’d have to keep optimizing (the existing facility), we thought it would be best to move out to the irrigation site,” he says.
Redmond was fortunate to have access to such a spacious property, says Joshua Robertson, P.E., a senior engineer for Anderson Perry & Associates Inc., the consulting firm that is developing the preliminary design for the project. “It’s pretty rare that a city would have this much land to work with, which opens up options that really aren’t normally considered,” Robertson says.
Disposal options
The Redmond Wetlands Complex will consist of a pretreatment screening step at the headworks, followed by a series of lagoons that will be designed to reduce biochemical oxygen demand and nutrients to below permitted levels. Next follows disinfection, which will be conducted by means of sodium hypochlorite. Operators of the system then will have various options for disposing of the effluent. “That’s where a lot of the flexibility comes into play,” Kirchner says.
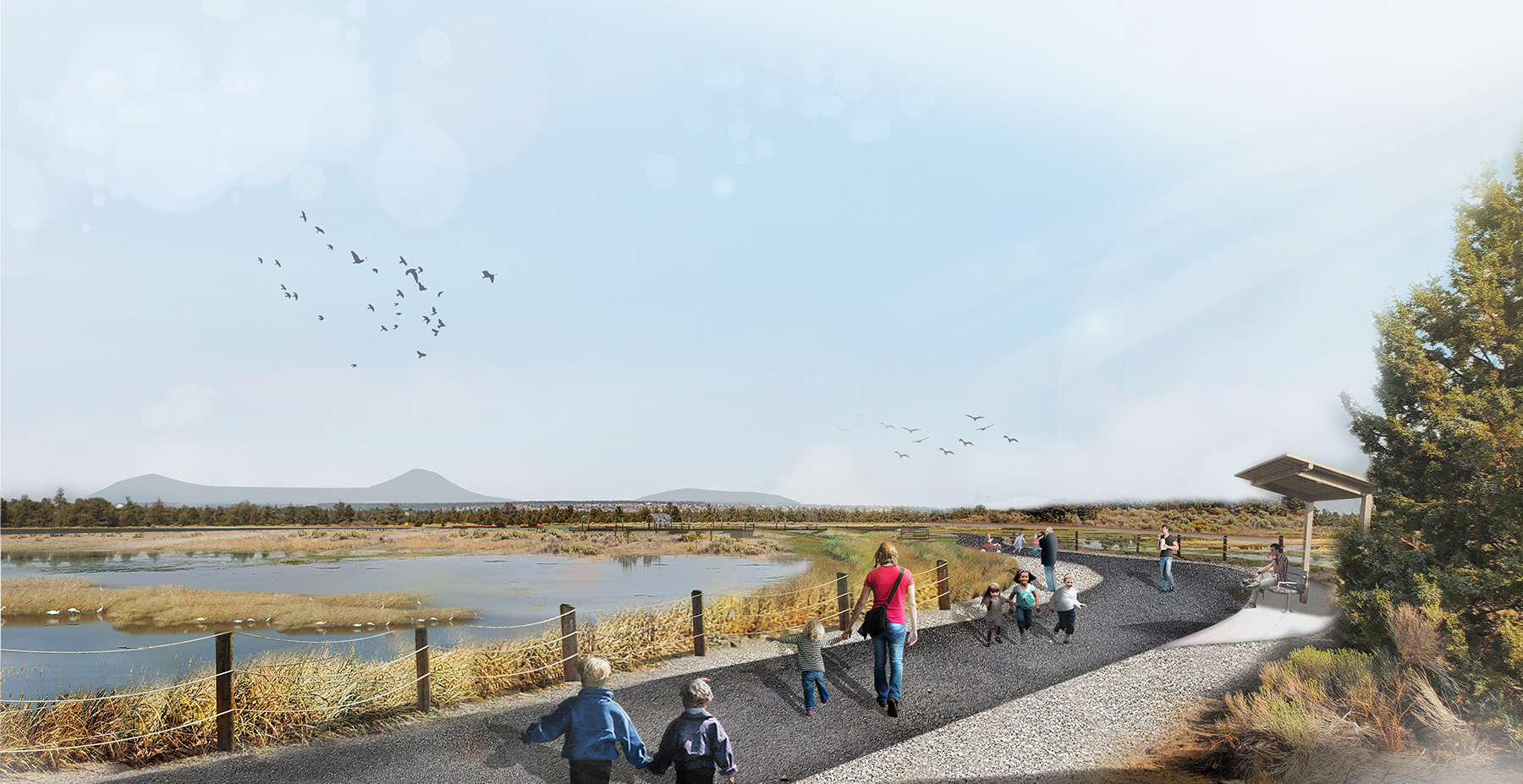
The treated water may be used for irrigation or sent to a series of so-called treatment wetlands, which will be lined to prevent percolation into the ground. After leaving the treatment wetlands, the water can be sent to the existing infiltration gallery or to a secondary system of wetlands known as the disposal wetlands. These unlined disposal wetlands will facilitate infiltration.
“One thing that is unique is that the treatment wetlands are used for polishing,” Robertson says. (This further treatment makes the water cleaner than it needs to be to meet permitting requirements.) Microbial colonies associated with vegetation in the wetlands provide an “additional way for nitrification,” he says. In fact, anoxic zones in the wetlands will conduct “some denitrification,” Robertson says.
As for key regulatory requirements, the project likely will have to reduce total dissolved solids in treated effluent to less than 500 mg/L, says Brett Moore, P.E., M.ASCE, a process designer for Anderson Perry. The limit for total nitrates is expected to be 9 mg/L. To achieve this level, BOD concentrations will need to be kept below 50 mg/L so as to promote the growth of nitrifying organisms, Moore says. Such a level should not pose a problem, he says, because the system is designed to limit BOD in effluent to 30 mg/L even in winter, when microbial activity is at its lowest level. “Our water quality most of the year is going to be much better than 30 mg/L,” Moore says.
Multiple benefits
Designed to treat 4.6 mgd, the Redmond Wetlands Complex is expected to cost on the order of $45 million to design and construct, Kirchner says, though he notes that the figure is only a preliminary estimate. Compared to a traditional mechanical-electrical treatment facility, the wetlands complex will have slightly lower capital construction costs, Robertson says.
This comparison only improves with time. Because it will have lower chemical demands and will require less upkeep, the Redmond Wetlands Complex is expected to cost significantly less than a traditional treatment system over the long term, Kirchner says. “This type of system has much lower life-cycle costs in comparison to a mechanical-electrical system,” he says.

Meanwhile, because the lagoons capture solids and break them down over time, the new facility will result in a “significant reduction in biosolids generation,” Kirchner says. “That correlates to a reduction in our carbon footprint,” he notes. “Currently, we have multiple trucks that leave the site a day hauling biosolids out to the irrigation and biosolids site,” he says. “No longer will we have that operation.”
Among its other benefits, the project will create wildlife habitat as well as publicly available open space that includes walking trails and other amenities. Public education is another key benefit, Kirchner says. “We’re taking the fence and the gate away from a treatment facility and building a site that can bring out the community to learn more about wastewater treatment and its beneficial reuse,” he says.
Looking ahead
Preliminary design is scheduled to conclude in early 2022, Robertson says. Final design then should take about nine months. Construction is expected to begin in early 2023 and conclude by 2025.
Ultimately, the project will be designed to serve a population of 54,000 people. “We’re planning this project to handle the growth for a 20-year period,” Robertson says. At the end of this time frame, Redmond will be well positioned for its next system upgrade. “The next expansion of this system is going to be pretty simple — just adding a few elements to this current footprint,” he says. “It really sets the city up for success for a long time.”