By T.R. Witcher
Like many American cities in the years before World War I, Pittsburgh had developed its own fledgling automobile industry. The city boasted the first 24-hour drive-in gas station in the nation, a development that helped kick-start the city’s Automobile Row, as the stretch of town around the city’s Baum Boulevard and Centre Avenue came to be known.
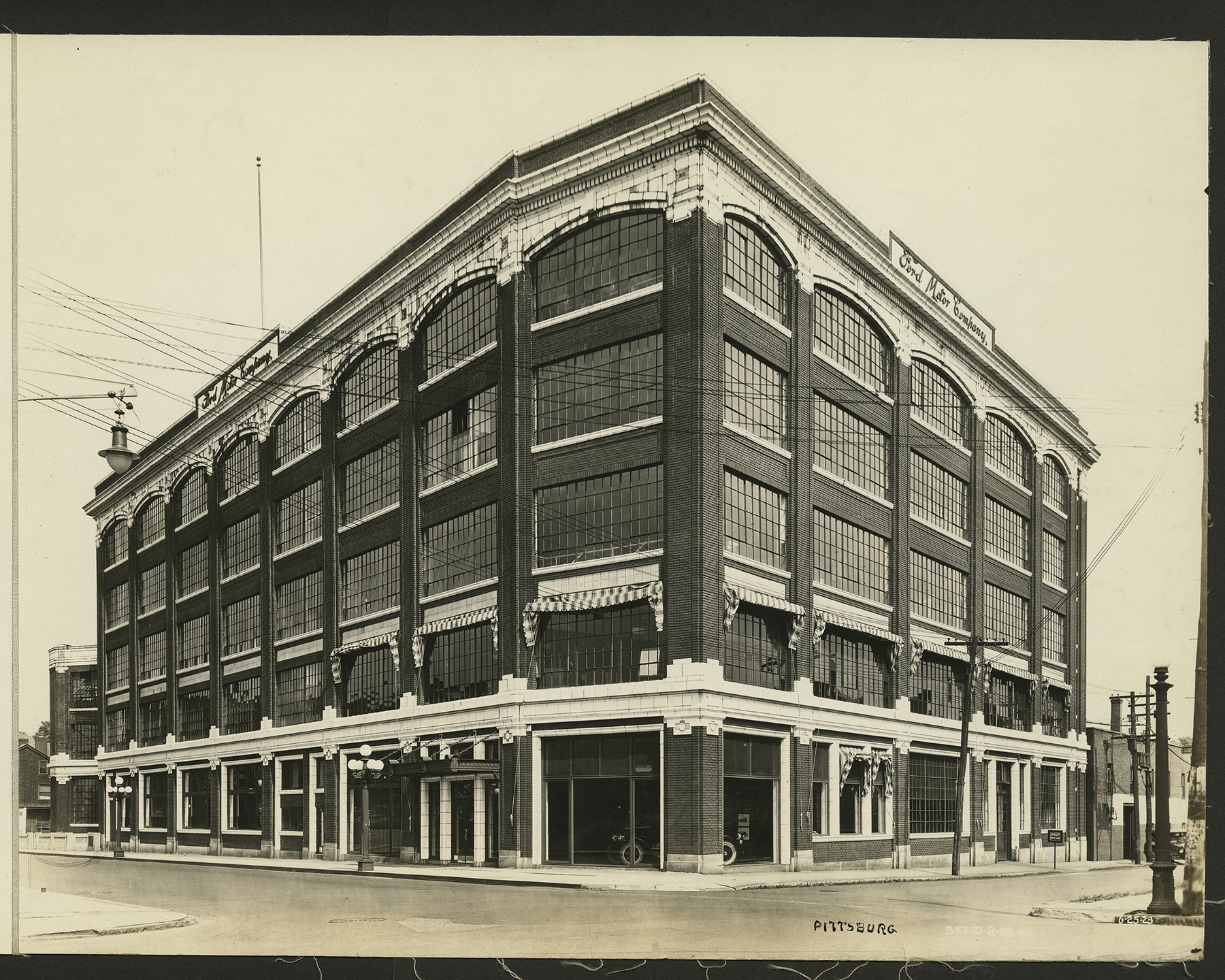
Detroit, led by the Ford Motor Co., quickly established itself as the center of car production. But Ford was also quickly building out its plant capacity across the United States. In Pittsburgh, the company opened an innovative assembly plant that served for years as a car factory and a point-of-sale showroom.
Now, 70 years after Ford finally sold the plant, it has been brought back to life. The new iteration of the Ford Motor Co. Assembly Plant is a biomedical research facility for academic research and industry partners that is known as The Assembly, a joint venture between the developer, Baltimore-based Wexford Science+Technology, and the University of Pittsburgh.
Dual-purpose powerhouse
The plant was originally designed by architect John H. Graham, Ford’s corporate architect between 1913 and 1918 and a specialist in the use of reinforced concrete, according to the nomination for the building’s inclusion on the National Register of Historic Places, prepared by JulieAnn Murphy and Jennifer Hembree, of MacRostie Historic Advisors LLC. The building was listed on the register on Nov. 20, 2018.
Built in 1915, the eight-story, 180,000 sq ft structure, along with a connected six-story volume height crane shed, cost half a million dollars to build. About 300 people worked the line, the register report noted, “assembling a car every one-and-a-half minutes.”
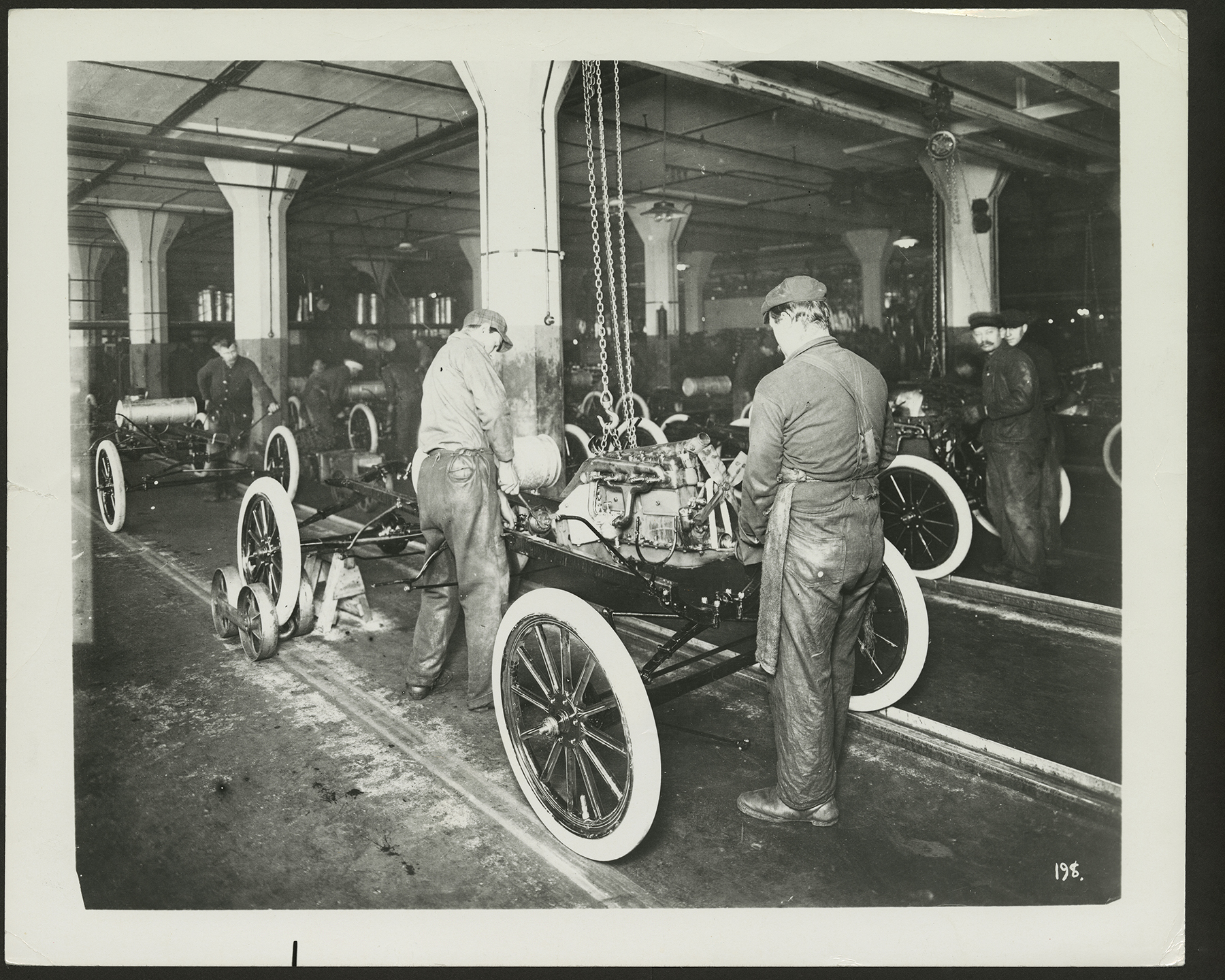
The Pittsburgh plant used an innovative concrete construction technique, first developed in Ford’s assembly plant in Chicago. Concrete slabs in this type of construction were generally 11 in. thick and designed for live loads of 150 lb/sq ft, according to Murphy and Hembree’s report. Slabs were carried on reinforced concrete octagonal mushroom-capped columns topped with a 7 ft sq, 9 in. thick concrete plate.
In addition, these slabs utilized parallel bars that extended transversally and longitudinally. “Parallel bars ran across the entire system of bays, with some bars bent up at their supports — either the columns or the band of reinforcing connecting the column — to account for negative-movement tension at the top of the slab,” according to the report.
Different stages of the assembly process took place on different floors of the building, the report notes. Body assembly, frame painting, and storage were handled in the basement. Carpentry and office space occupied part of the first floor, which also hosted the building’s car showroom, while repair areas were on the second floor. The assembly line was on the third floor, and enameling, painting, and upholstery took place on the top two floors.
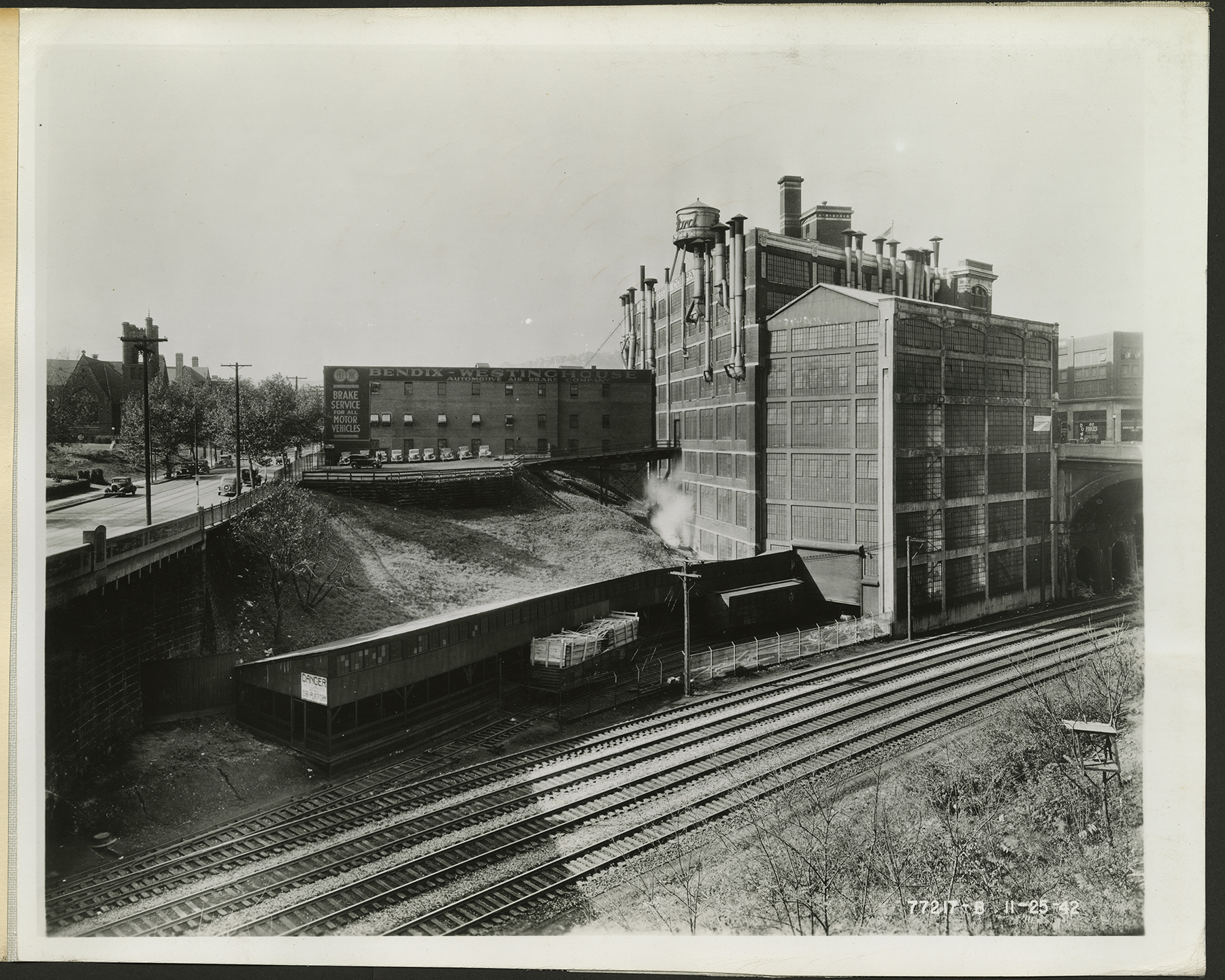
The assembly plant was along rail tracks. One problem the automaker had, according to the report, was “unloading automobile parts, distributing them within the plant, and then loading finished materials from the plant into railcars.” To solve this issue, the main assembly building was joined to the crane shed, where a roof-mounted crane could lift car parts from the Pennsylvania Railroad line that ran past the building and raise or lower them to any floor on the assembly side.
On the first floor, a garage door and sloped concrete ramp allowed cars to be moved in and out of the showroom, which itself was notable for its “historic wood frame vestibule with a denticulated cornice … (including) glazing on each side and paired full glaze doors.”
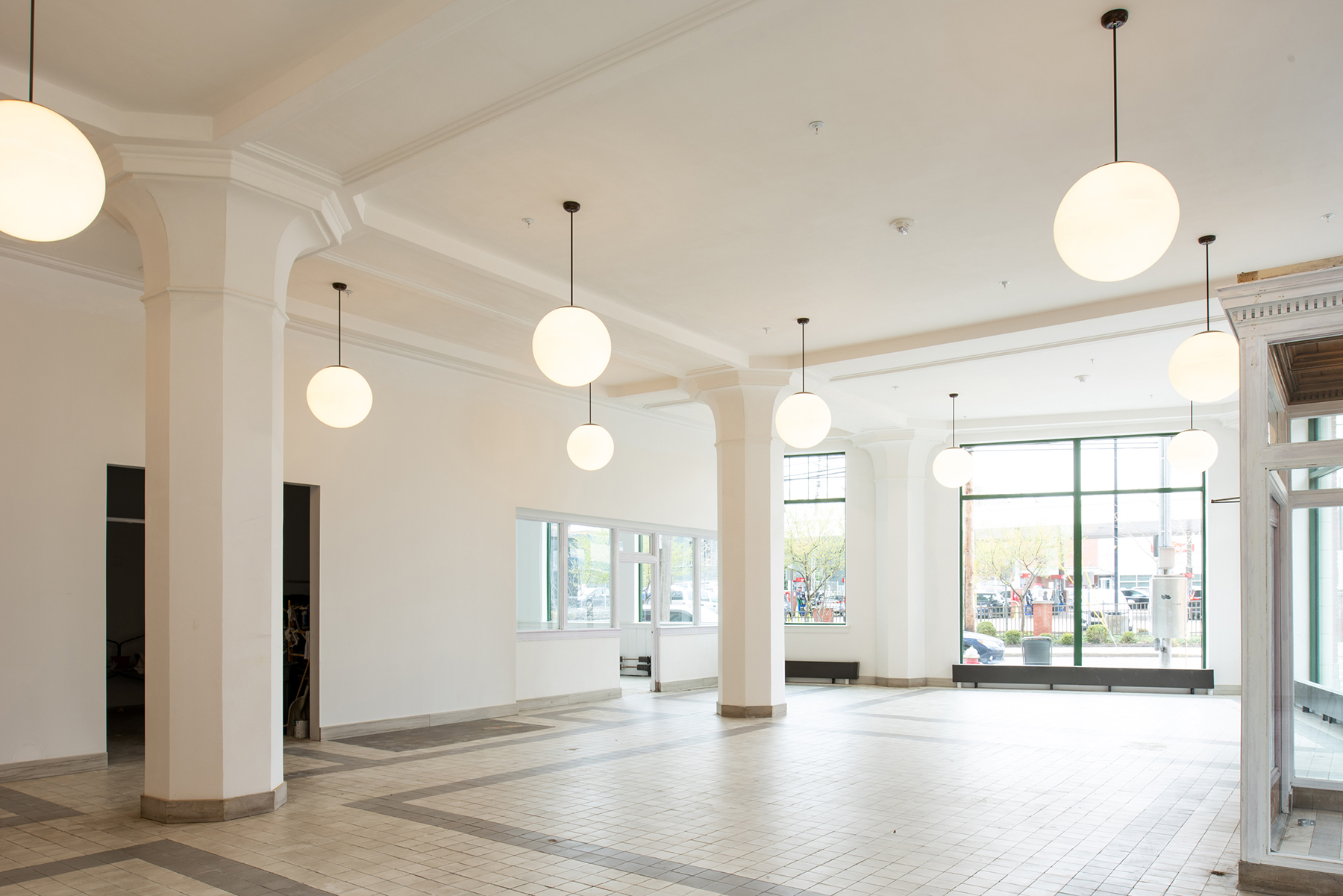
Ford built 31 regional assembly plants throughout the nation during the 1910s, and by the 1920s, Murphy and Hembree wrote, “more than 2,700 authorized Ford and Lincoln dealers made the Pittsburgh branch their base of operation, as did service stations in 37 counties in four states.” The Pittsburgh building served as an assembly plant from 1915 to 1932 — but ultimately assembly changes at Ford and the Great Depression reduced the need for the building. After that, it was used as a sales and parts facility until the automaker sold the building in 1952.
Reinvention
In the decades that followed, according to the report, the assembly building saw use as a motor supply store, a party supply store, a clothing manufacturer, and a printing business.
In 2006 the University of Pittsburgh Medical Center acquired the site. As early as 2012, architecture firm ZGF was invited to look at the project, which was eventually mothballed because of lack of funding. Wexford came on board and revived the project several years later.
For ZGF, the renovation was an opportunity to continue the assembly building’s “legacy of innovative technology,” says Deanna Keil, Associate AIA, a project manager for the project and a principal in ZGF’s Washington, D.C., office. “Because it had been used for mass automotive assembly from start to finish — assembly to sale — the existing building had an expansive floor plate.” This meant the building structure was robust and could withstand the “vibration and everything that an intensive lab building tends to mitigate and require intensive structural reinforcement for,” she explains.
Keil says the biggest challenge of dealing with such an old building was the lack of mechanical infrastructure needed to support modern, intensive lab research. Architects had to design new ductwork, pipes, and electrical systems, Keil says, as well as “identifying space for emergency generators (and) determining where to put air handling units within the building or outside the building.” A lot of the main ductwork now extends through a former elevator shaft.
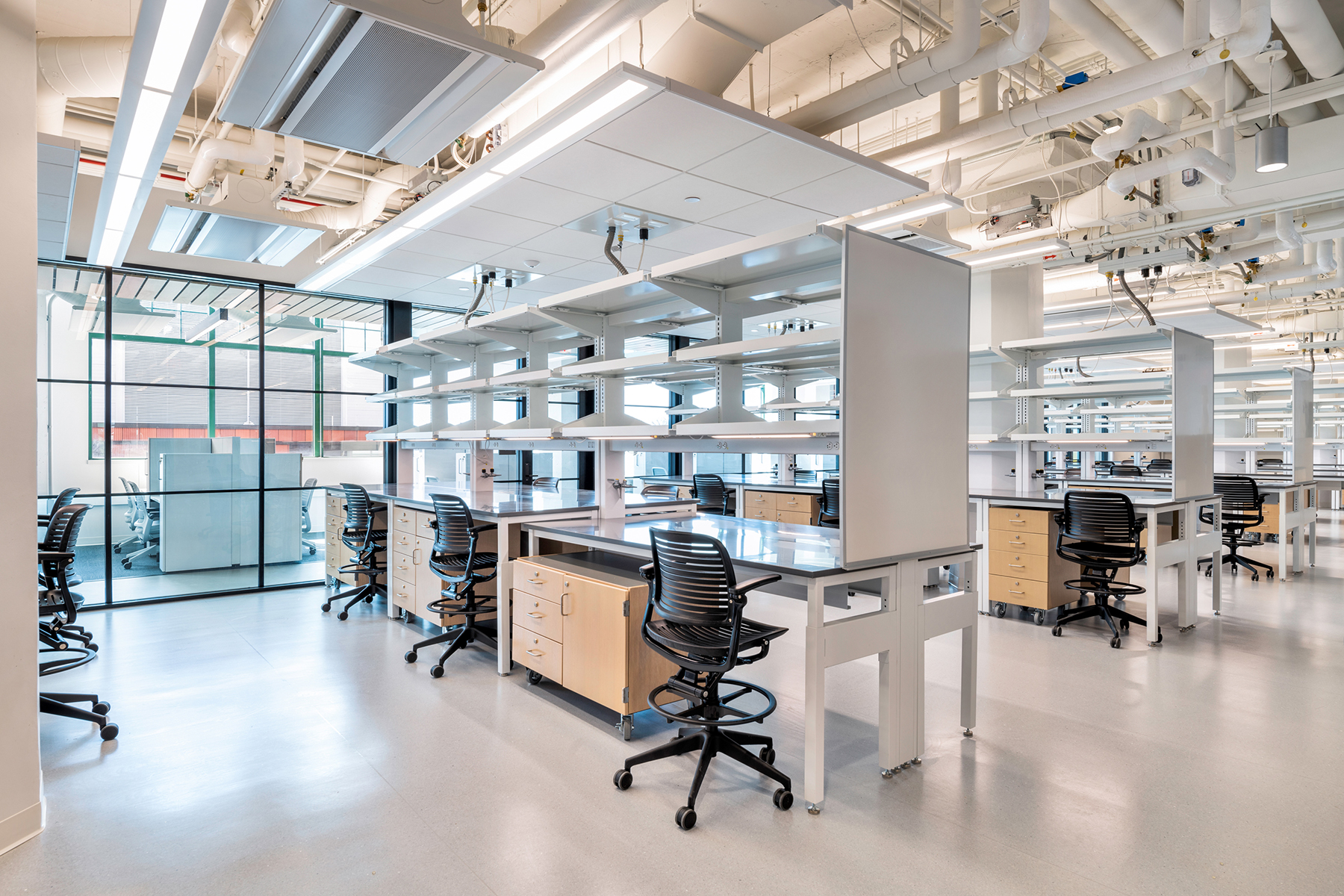
Otherwise the building’s bones were, Keil says, “really kind of a creative canvas for us.” The team was “able to keep a lot of the existing architecture exposed and have that be a feature in the building rather than an obstacle to work around,” she says.
Structural engineering firm Thornton Tomasetti also did preliminary work on the assembly building in 2012 and returned in 2018 when the current iteration of the project officially got underway. One of the challenges, says Lisa Chong, P.E., LEED AP BD+C, the structural project manager for the project and a vice president in Thornton Tomasetti’s Washington, D.C., office, was figuring out what lateral system created the big empty space. There were no surviving structural drawings of the historic building.
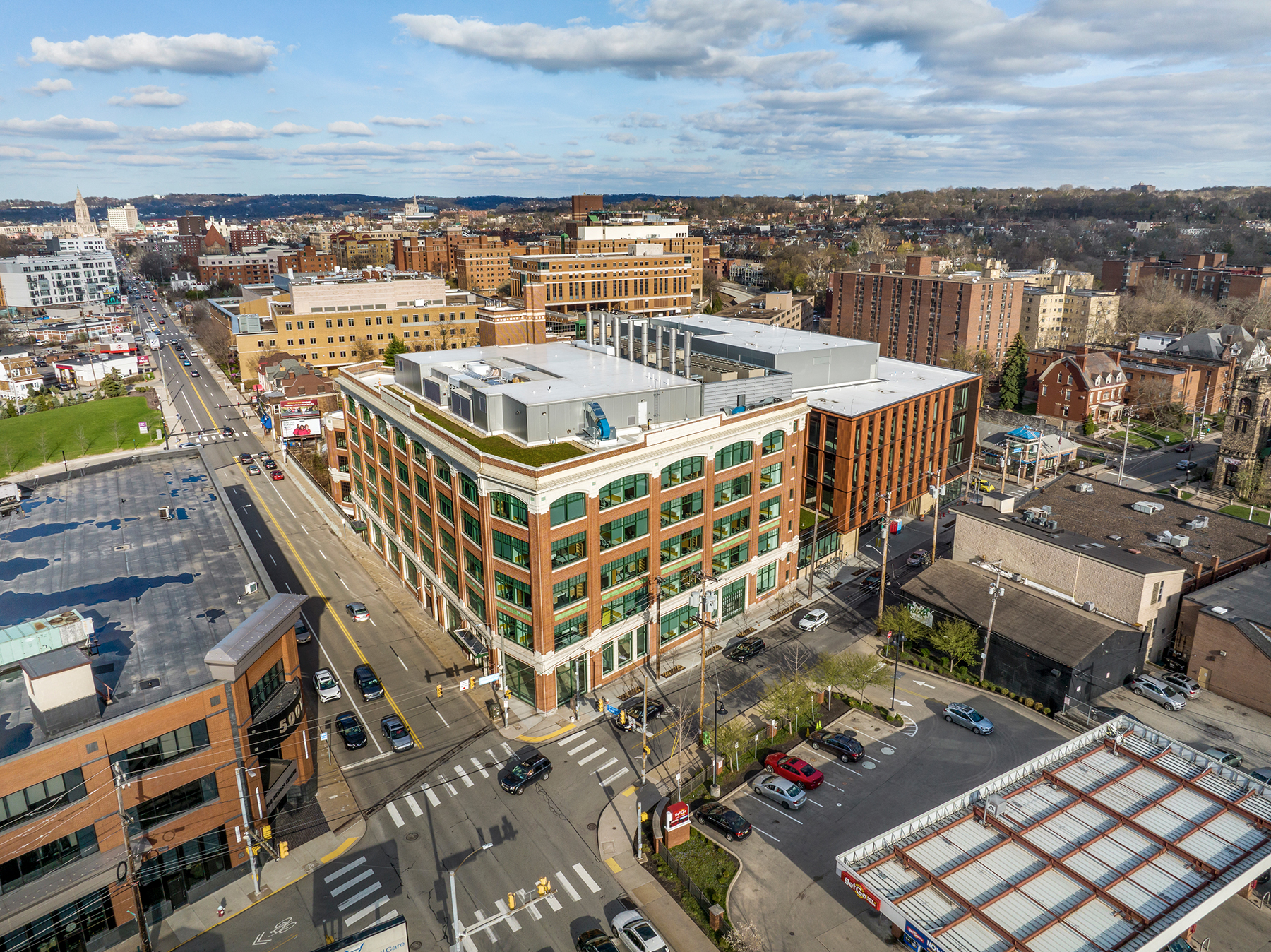
To better determine whether its existing structural system had enough load-carrying capacity for the building’s new uses, Thornton Tomasetti and the building’s contractor turned to ground-penetrating radar scanning, a nondestructive technique that could see into the concrete to identify the presence of steel reinforcing and the location of conduits.
But these GPR scans, which were performed by Turner Construction, the building’s contractor, had their limitations. “You can figure out the spacing of the bars and how far down they are in the slab,” says Chong. “You can sort of tell the difference between the top and the bottom bars, but you can't really get a good sense of the size of (the bars) without opening up pockets of the floor.”
Thornton Tomasetti came up with a plan to cut into the concrete columns and floor slabs to get a better look at the underlying structural system. (This was initially performed by Turner’s specialty subcontractor, ACA Engineering.) The investigation discovered that the reinforcing bars uncovered were a twisted square shape — a precursor to today’s rounded bars. It also discovered that the columns in the assembly plant and shed were actually made of steel — which significantly reduces stiffness. (The concrete was just used as fireproofing.)
Chong and her colleagues had to determine how these steel columns were connected to the concrete floor slab. “It took us a long time to determine if there were studs to transfer the load, which is how we build composite construction now,” she says. “There were not; there were reinforcing bars passed by the steel column, but they weren’t welded to it. We were able to get to a comfort level on the friction transfer between the two and determined that no retrofits were required at the column-slab connections.”
In general, the building was relatively robust. New holes were cut into the slabs, primarily for elevators and stairs (as well as new mechanical shafts for infrastructure). New steel brace frames were installed around the elevator and stair openings, and new foundations were built beneath those brace frames.
“Where we had issues was in the wind and seismic resistance of the building because that's not something that was considered in the building codes in the early 1900s,” Chong says. Thornton Tomasetti designed “pretty significant” seismic retrofits on the building, which included the addition of the new steel-braced frames and their connections back to the existing floor slab as well as associated micropile foundations.
Engineers also replaced corroded steel members in the shed and added reinforced concrete. “Typically we see this level of corrosion in exposed exterior construction when concrete begins to crack and is exposed to moisture,” Chong says.
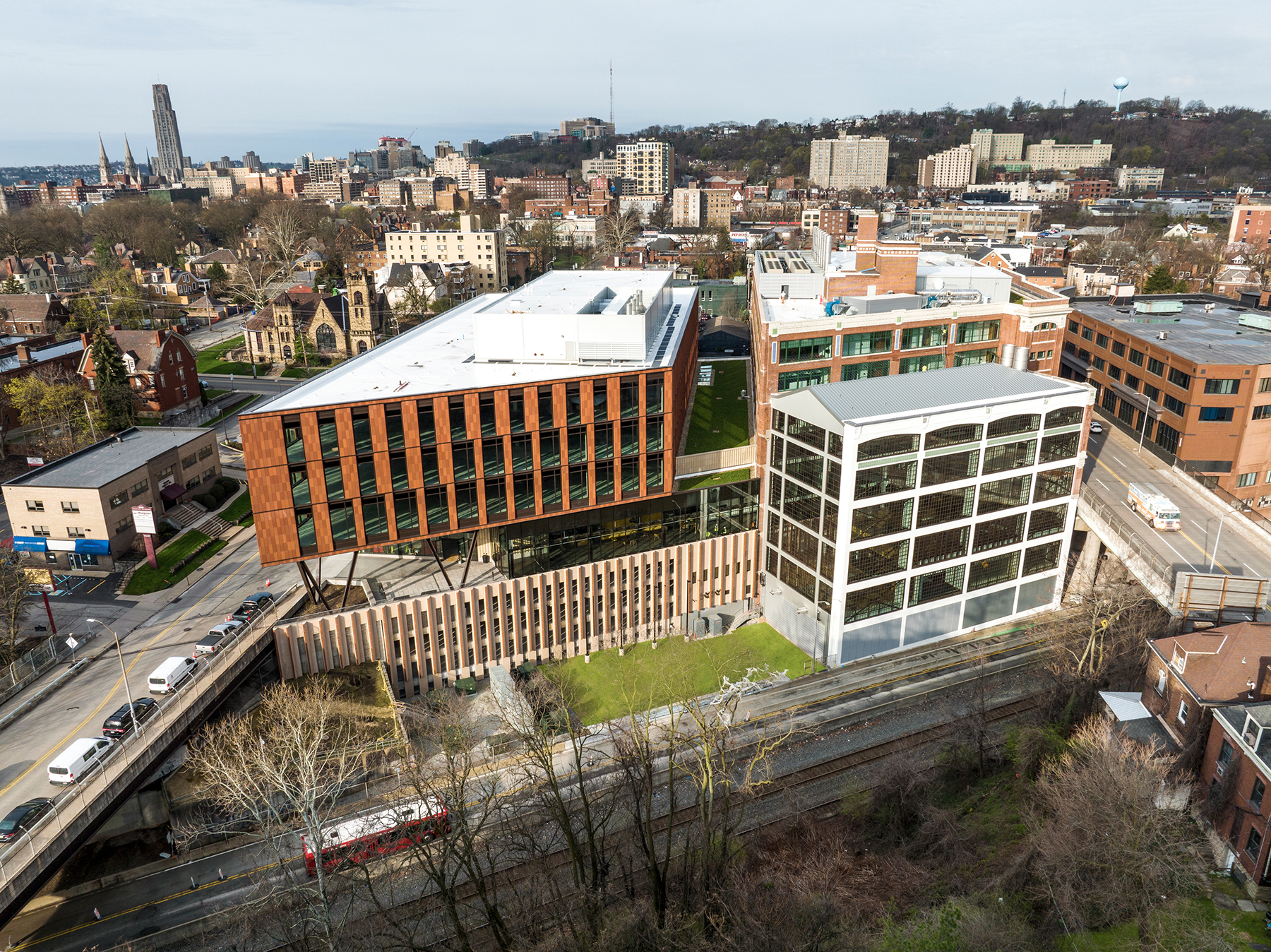
In addition to restoring the Ford building, Wexford is developing an adjacent four-story building with below-grade parking, a public entry lobby, and a loading dock. The addition, designed by ZGF to be proportionally similar to the Ford building, plays off the original building’s red brick, orange-colored terra cotta, and window proportions. The new building also features prominent diagonal bracing supporting a cantilevered section (the V-shaped supports echo the diagonal bracing of the crane shed’s curtain wall).
The courtyard-style space under the cantilevered section is meant to serve as an external public gathering and respite space off busy Centre Avenue (there’s also space for a future restaurant).
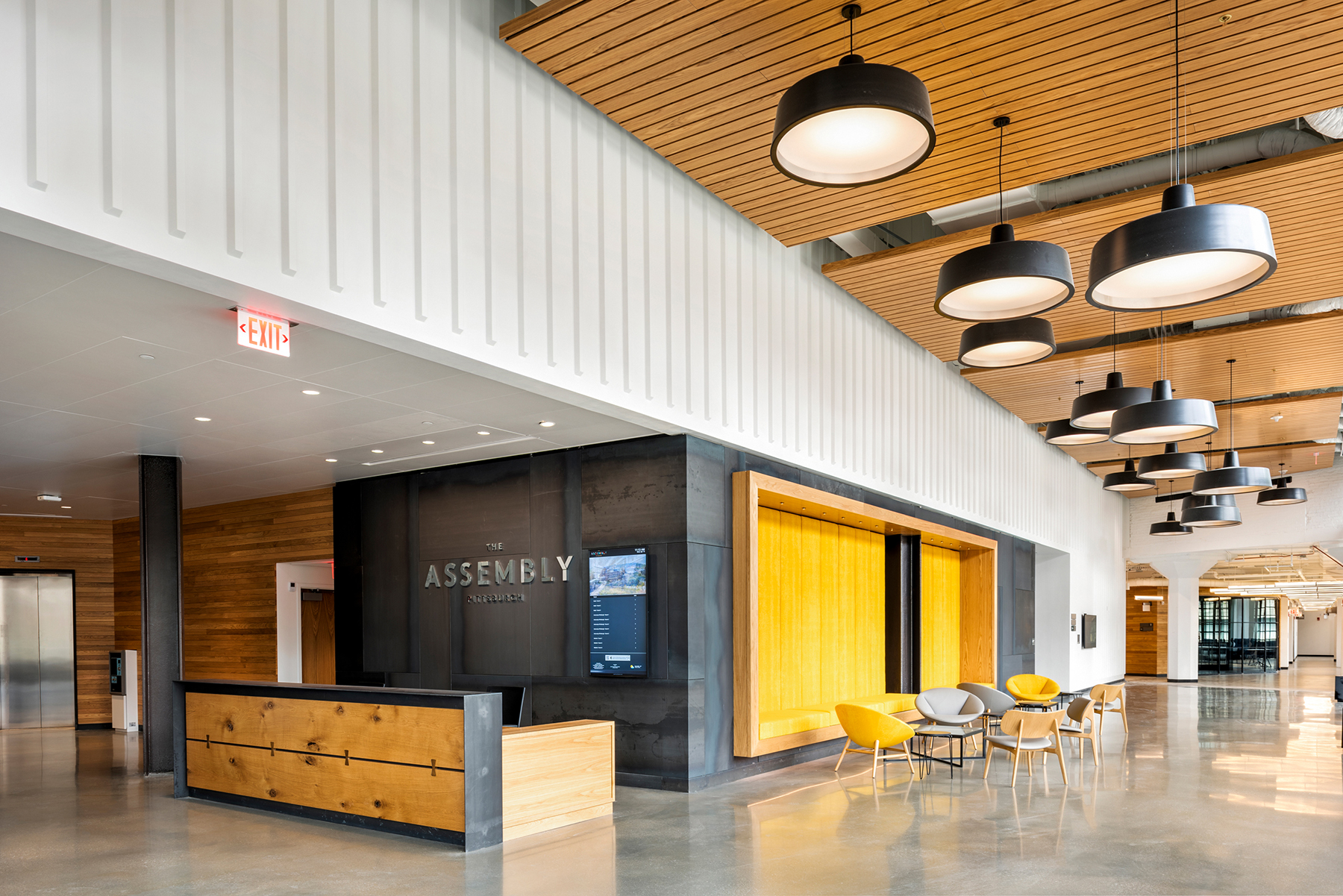
The renovated Ford building will house University of Pittsburgh researchers focused on cancer biology and immunology. Some moved into the building in late spring, while yet-to-be-identified industry partners are expected to eventually lease space in the new building.
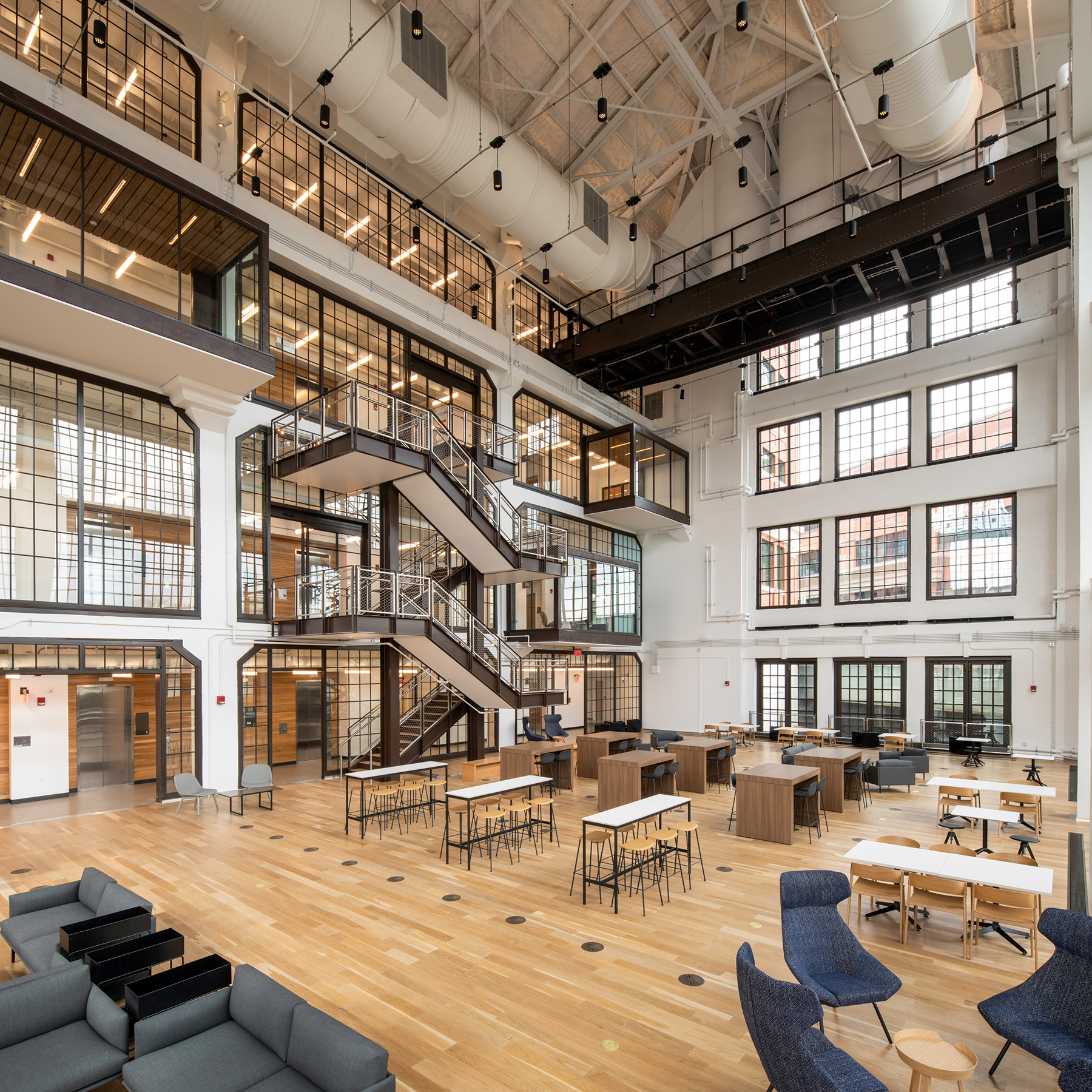
Perhaps the signature element of the new complex will be the renovated crane shed, which has been transformed into a giant gathering space. “It's really a public amenity for not only the users, the tenants in the space, but also for the city of Pittsburgh,” says Keil. The new space can accommodate both scientific and collaborative events for building tenants as well as weddings and other public events. “We’re really hopeful that it can be a melting pot for both collaboration and just engagement in the community.”