By John Jucha, P.E., and Shaun Franklin, P.E.
At first glance, The River Mile area of Denver appears full of constraints and barriers that typically would preclude development. Adjacent to a nearly mile-long stretch of the South Platte River in downtown Denver, the area in its current form is an industrial landscape with underused and underdeveloped pockets of land interspersed among such Denver landmarks as Elitch Gardens Theme and Water Park; Ball Arena, an event center; and Empower Field at Mile High, home of the NFL’s Denver Broncos.
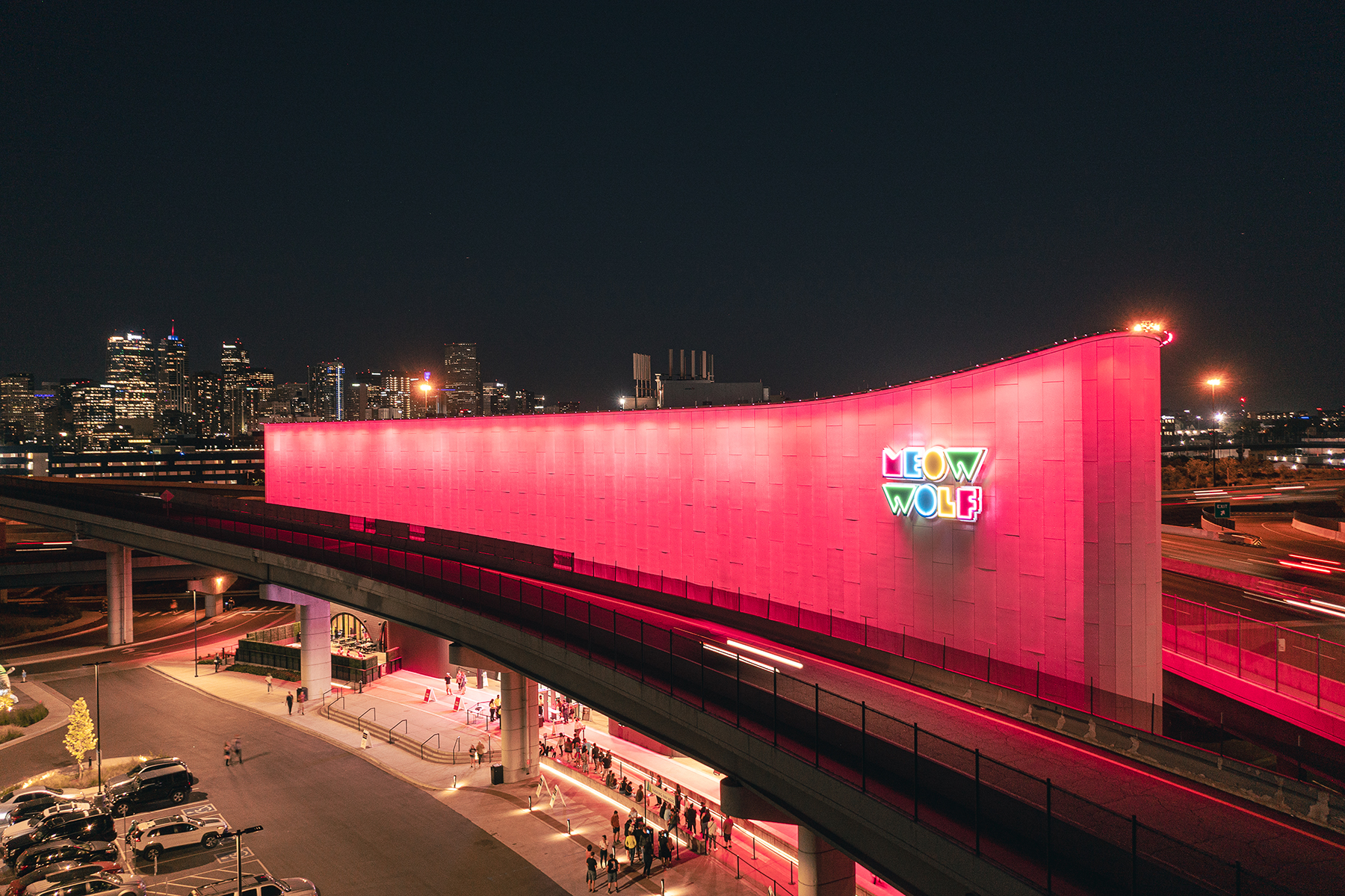
In addition, three major thoroughfares — Interstate 25, Auraria Parkway, and Colfax Avenue — delineate the area, with the three elevated roadways merging into a triangular form at the southwestern tip of The River Mile. This small, triangular site — hemmed in by the elevated roadways — is the new home of the Meow Wolf Denver Convergence Station, a five-story, 90,000 sq ft, immersive art experience and the first major commercial destination of the planned neighborhood known as The River Mile.
Despite the site’s obvious physical constraints and not-so-obvious obstacles that presented themselves during the design and construction phases, the project team for Meow Wolf Denver converged to create an open, collaborative environment, facilitating the free-thinking and pressure-testing of ideas needed to build this intricate space.
Immersive identity shapes the project and team
As a build-to-suit development, the structure was designed to meet the needs of the tenant, Meow Wolf, a Santa Fe, New Mexico-based arts and entertainment company. Meow Wolf creates immersive, interactive experiences to “transport audiences into fantastic realms of story and exploration,” according to the company’s website. As Meow Wolf’s largest installation to date, the Denver location adds to the city’s booming arts scene, with hundreds of local artists participating in the interior finishes of the project.
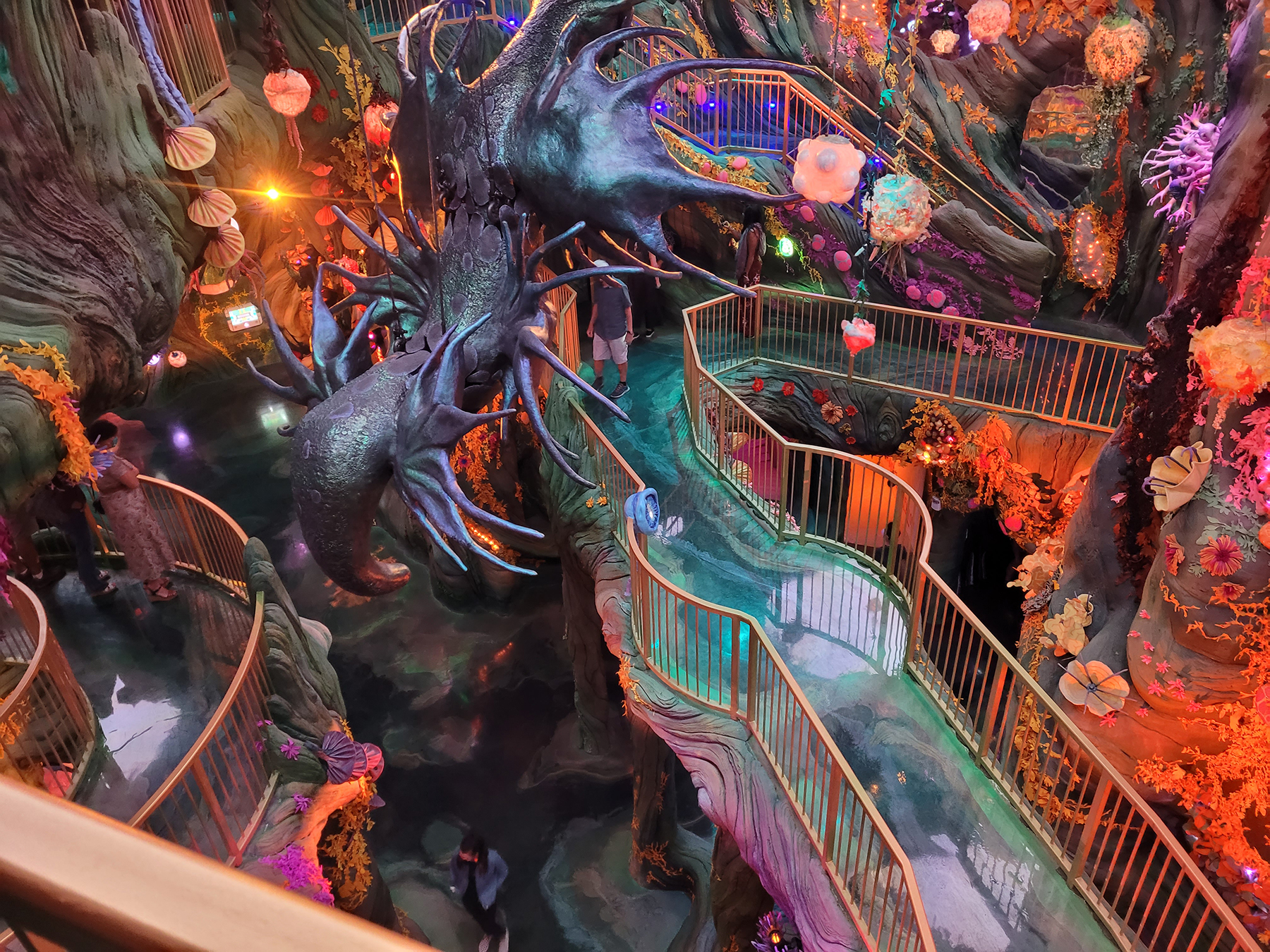
Meow Wolf’s character influenced the formation and behavior of the team that brought this unique project to life. Spearheaded by Revesco Properties and Shears Adkins Rockmore Architects, known also as SAR+, the project team operated in an open, trusting manner that fostered the ideas needed to achieve the best solutions.
In addition to the external collaborative environment of the project team members, an internal collaborative environment held sway within KL&A Engineers and Builders, which served as the structural engineer on the project. Unlike the archetypal role of a consulting engineering firm, KL&A’s scope for Meow Wolf Denver extended beyond just the engineering portion and included construction contracts as well.
Brought on to the team at site selection, KL&A provided design engineering services for the core and shell for the building owner and developer, engineering design for the tenant improvements, and engineering services for many of the art exhibits and installations.
Given the complexity of the building and the inseparable nature of the final exhibits, KL&A was also selected to construct the structural steel elements of the core and shell, tenant improvements, and a few of the large steel exhibit structures. This continuity within KL&A’s team as it worked on the overlapping phases of the project enabled numerous efficiencies and a more collaborative design and construction process.
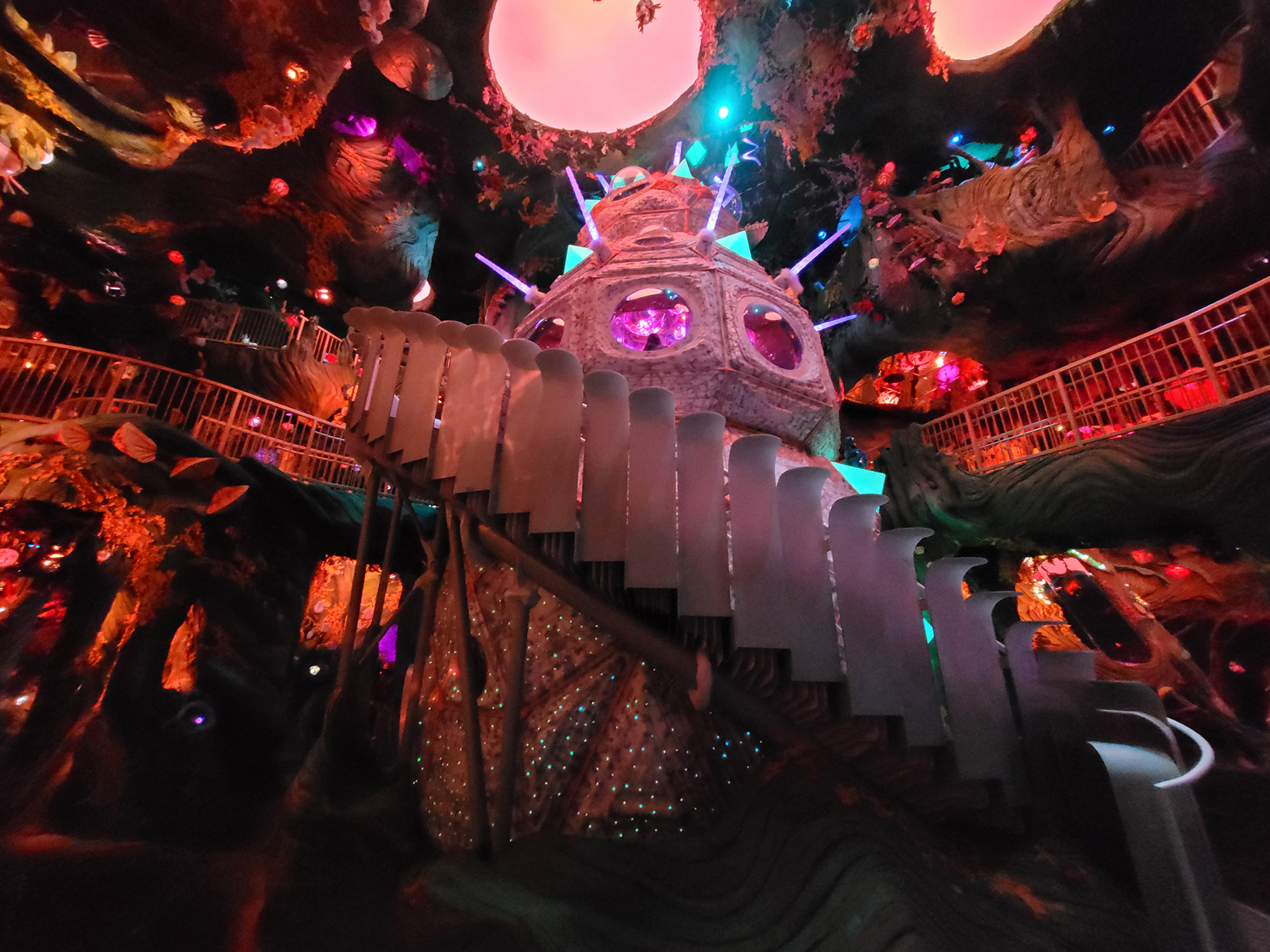
Site selection
Meow Wolf’s overall immersive identity also influenced the site selection. To reduce urban sprawl and support smart growth development in Denver, the project team selected this unique plot, which was characterized as an infill site located near the underserved neighborhood of Sun Valley.
Creating a cultural destination out of previously undesirable land — which had been occupied by Midwest Steel, a cell tower, and a parking lot for Broncos’ season ticket holders — speaks to Meow Wolf’s spirit of integrating art into underserved communities.
Once the abandoned remnant structures of Midwest Steel on the site were demolished and excavated, the remaining fill was found to be unsuitable for a slab-on-grade first floor without significant subgrade preparation and improvement. The 15 ft overexcavation requirement for a slab-on-grade would have been costly and logistically problematic because temporary shoring would have been needed to avoid undermining the adjacent highway viaduct foundations. These complications forced the project team to seek alternative solutions.
To stabilize the subgrade and permit a slab-on-grade first floor without having to overexcavate, the team implemented rammed aggregate piers provided by Hayward Baker, which has since been rebranded as Keller. Reinforced-concrete drilled piers were also used to support the superstructure, primarily because of the large building grid and substantial floor loads.
Design and construction impacts of highway viaducts
Design work began on the core and shell of the building in October 2017 and on tenant improvements in June 2018. The highway viaducts also informed, and in some ways constrained, several of the building’s design and construction components. First and foremost was the triangular shape of the building. Its exterior skin is set back a mere 10 ft from the elevated highways on all three sides, creating a uniquely shaped structure that the architect aptly likened to a soggy slice of pizza.
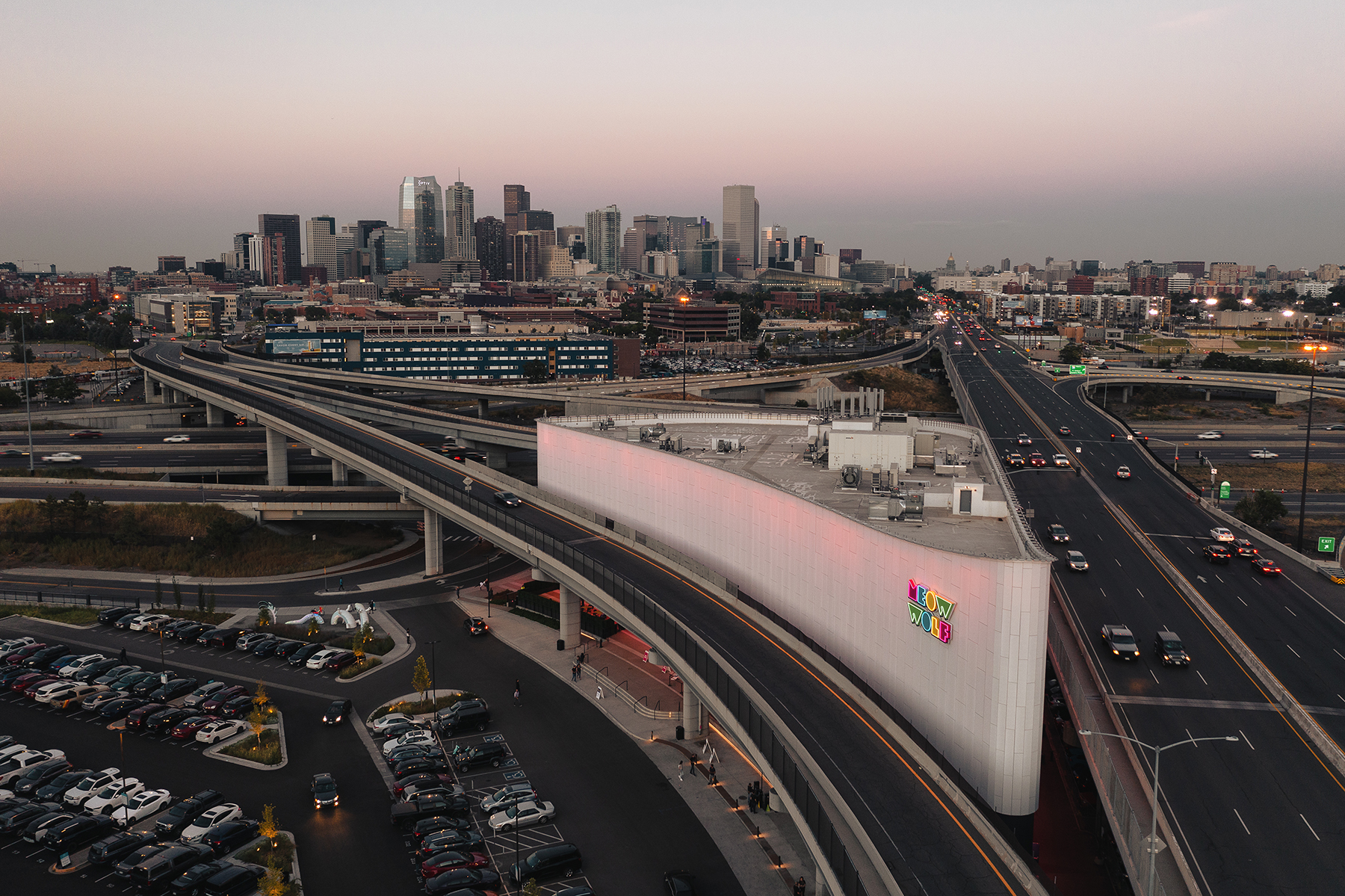
The highways surround the third floor of the building, and no windows are located above these roadways. This was partially due to the unique nature of Meow Wolf Denver’s exhibits, which have strict requirements regarding lighting control, but also because any windows at that proximity to the roadway would need to be impact-resistant.
The proximity to the viaducts necessitated significant planning of construction logistics to avoid as much disruption and as many costly closures to the highways and ramps as possible. Crane placement, the steel erection sequence, and lateral core design were among the many decisions affected by the nearby viaducts.
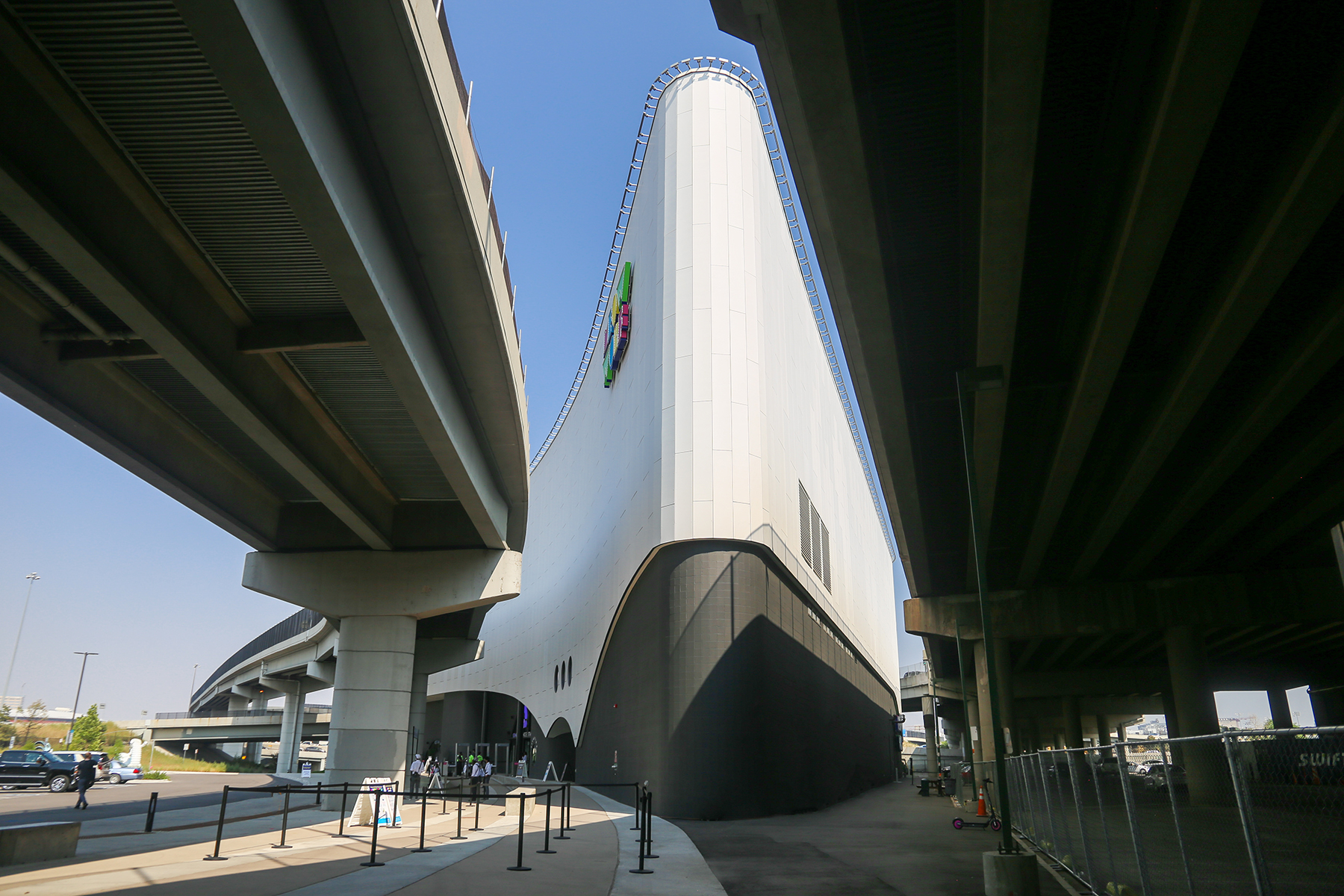
Distinguishable structural design components
Despite the site constraints and limitations imposed by the highway viaducts, the project team immersed itself in an open, collaborative design and construction environment from which several distinguishable structural design solutions emerged.
Composite steel construction was chosen to accommodate the need for a versatile structure that could support multiple types of occupancies, unique geometry, and future retrofit. Due to the large column grid and heavy building loads, the foundations consisted of 79 reinforced-concrete drilled piers. The diameters varied from 36 in. to 42 in., with socket lengths ranging from 10 ft to 25 ft into bedrock, depending on the pier loads. The perimeter foundations were reinforced-concrete grade beams spanning between piers.
Another structural design solution included the building’s gravity system, which consisted of composite steel floors supported by wide flange steel beams and wide flange steel columns. The building’s lateral system combined steel braced frames and concrete cores that were cast in place by means of modular steel forms known as RediCor and made by Vulcraft, a division of Nucor.
The third floor, which supports multistory exhibit structures, steel catwalks, and heavy shotcrete wall finishes, comprises the largest load area on the project, with the equivalent of 350 psf of uniform load. A 45 ft long girder was used in this area of the building, which spans over the music venue below. The W44x335 girder is the deepest W-shape listed in the Steel Construction Manual published by the American Institute of Steel Construction.
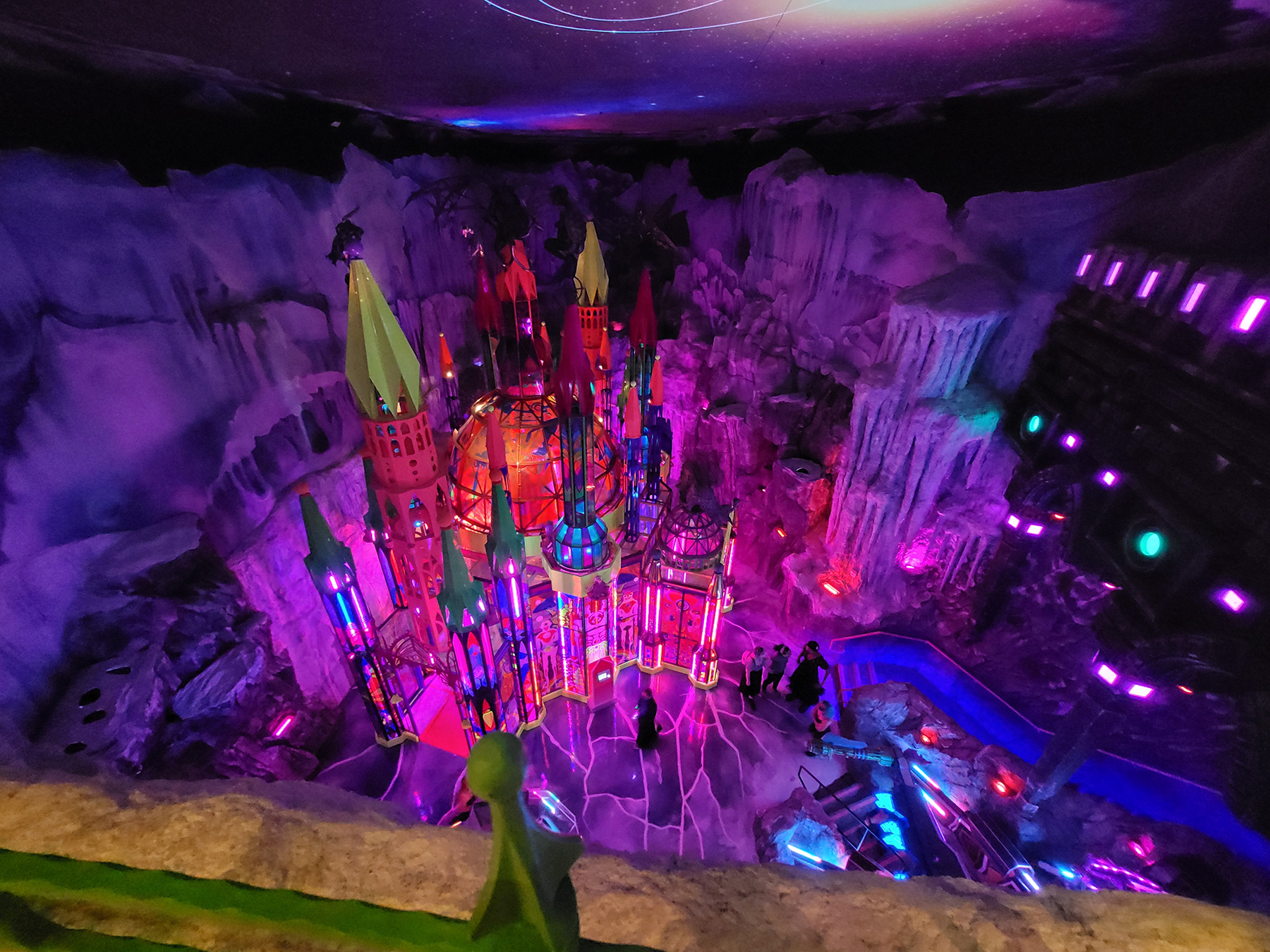
Steel fabrication began in February 2019. Steel erection started that April, followed by the topping out that June.
About halfway through the process of designing the core and shell, the project team was tasked with designing an alternative-use option for the structure. Specifically, the project was to include immersive art installations but also have the capacity to be a storage facility in the future. Live loads associated with heavy storage are given as 250 psf in ASCE’s Minimum Design Loads for Buildings and Other Structures 7-10. Although that design load governed much of the floor area, Meow Wolf’s exhibit loads controlled certain locations, such as the third floor. Due to the fact that storage live loads contribute to the effective seismic weight per Minimum Design Loads, seismic forces governed the main lateral force resisting systems.
One of the building’s most iconic architectural elements is the elliptical arched entryways carved from the exterior wall made of concrete masonry units. The main lobby entrance comprises a stunning 50 ft wide by 19 ft tall CMU arch with glass storefront infill. The length of the surrounding structure on each side of the arch was insufficient to carry reactions associated with masonry arching action. Therefore, the design solution needed to bear the weight of the CMUs while also bracing the wall and storefront from out-of-plane loads.
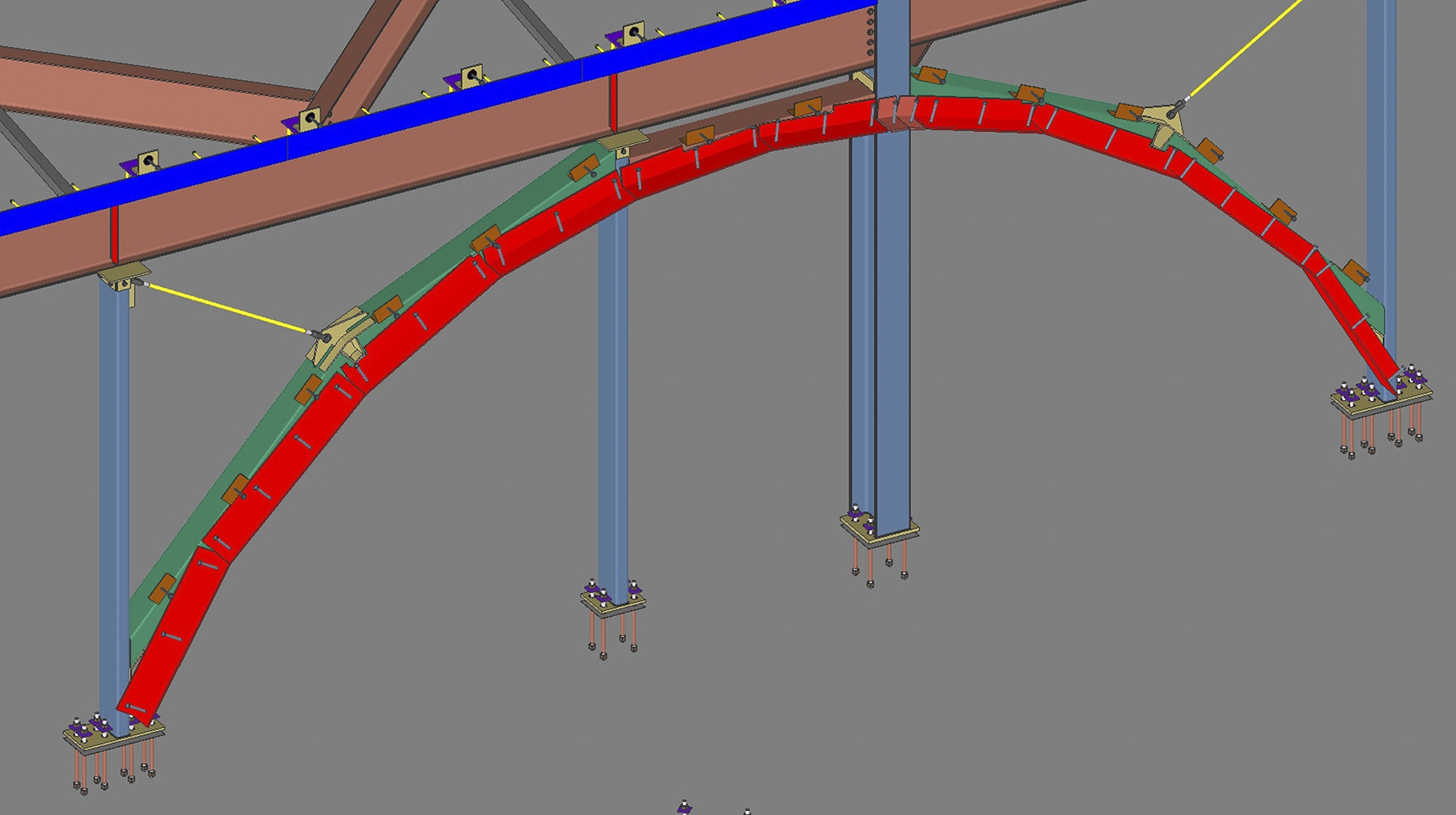
In place of expensive rolled structural members, rectangular hollow structural section wind girts were faceted around the arch, tying into rectangular HSS wind columns that aligned with the storefront mullions for concealment. A series of angles with 0.5 in. leg thickness and stiffeners were then attached to the HSS girts to reach and support the bottom of the CMUs. The facets of the steel support system were coordinated with a storefront manufacturer to ensure a tight fit. The finishing touch was a plasma-cut curved steel fascia that covered the head of the storefront to complete the curved aesthetic.
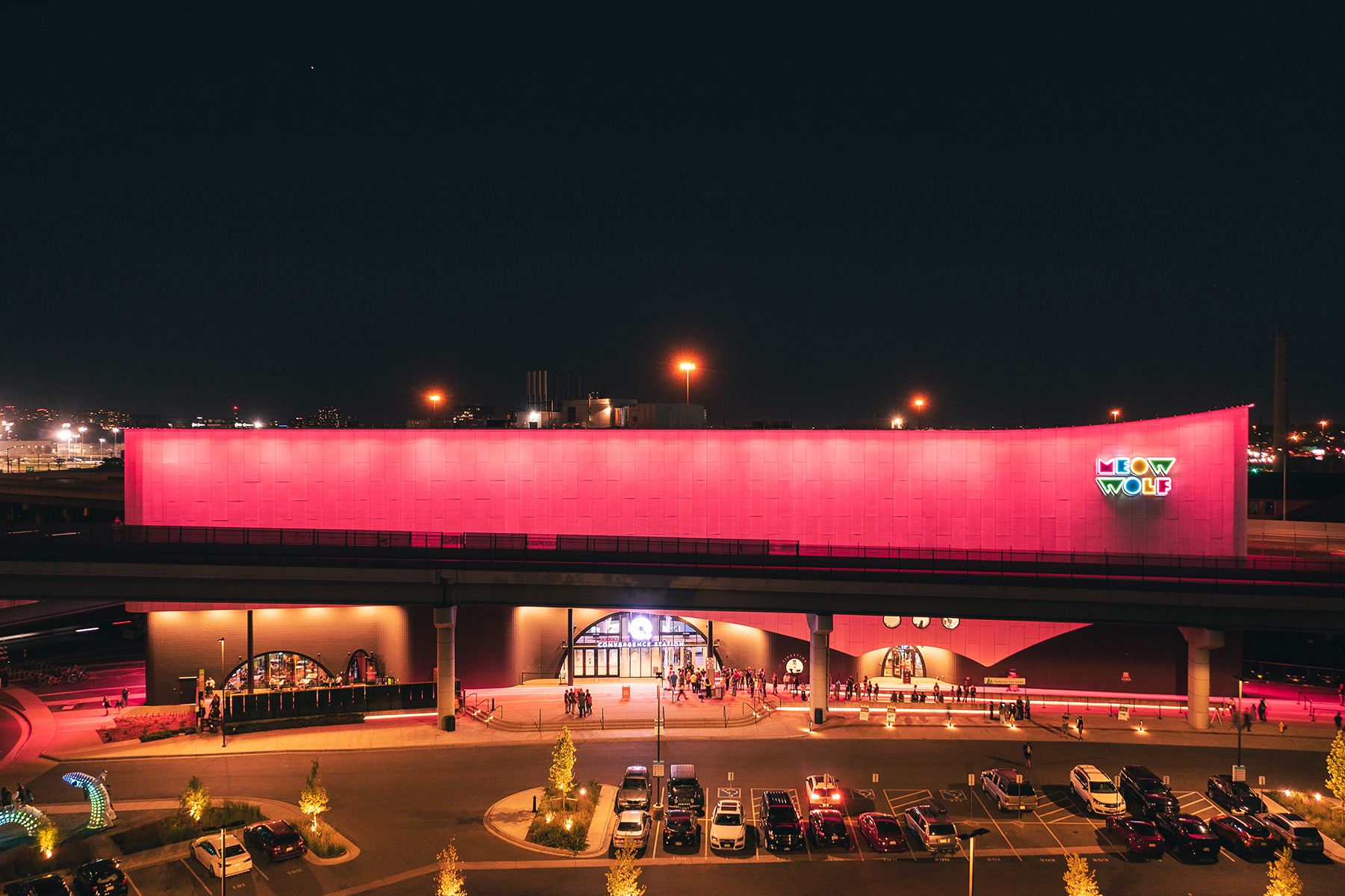
Community impact
Meow Wolf Denver held its grand opening in September 2021. Just as its project team converged to create an open, collaborative environment in which to design and build this unique structure, the resulting cultural arts center also serves as a collaborative focal point within the local community. Visitors seeking to travel to Meow Wolf Denver by means of public transportation have the option of using a bus line or the local rail system, while an adjacent parking lot is available for vehicular traffic.
Ultimately, Meow Wolf Denver exemplifies the importance of internal and external collaboration on such a unique, challenging project. It took a true team effort to interpret and manifest the vision of talented artists while also ensuring that the resulting building is structurally safe, achieves the project goals, and is constructed efficiently.
John Jucha, P.E., is the engineer of record and an associate and Shaun Franklin, P.E., is a business operations officer at KL&A Engineers and Builders.
Project credits:
Building owner: Revesco Properties
Tenant improvements: Meow Wolf
Architect of record: SAR+
Structural engineer and steel constructor: KL&A Engineers and Builders
Primary contractor: Turner Construction Co.
Civil engineer: Calibre Engineering Inc.
Geotechnical engineer: CTL | Thompson Inc.
Fabricators: HME Inc., Living Design Studios Inc., and Beatty Construction Services LLC
This article first appeared in Civil Engineering Online.