By T.R. Witcher
When Brown University hired New York City-based design firm REX to design a performing arts center, architects were eager to tackle the challenges. “There were many needs for the performing arts on campus,” says project leader Adam Chizmar, AIA, a REX associate principal. “It was made clear that there was a lack of contemporary performance spaces for all these different groups.”
After meeting with university officials, facilities managers, student groups, and representatives of each arts department, REX and its collaborators concluded that Brown needed a space that could serve many different groups – but it needed to be combined into one place.
Further reading:
- Australia’s Sydney Opera House hits all the right notes
- Dynamic structure pays homage to rock and roll pioneer
- How a new performing arts center in NYC redefines modern design
Traditional black box spaces – which leave the reconfiguration of the space up to the tenants – tend not to get reconfigured because it’s too expensive and cumbersome. But what if Brown’s single-space, multiuse venue could – with a combination of automated controls and some manual labor – be easily reconfigured?
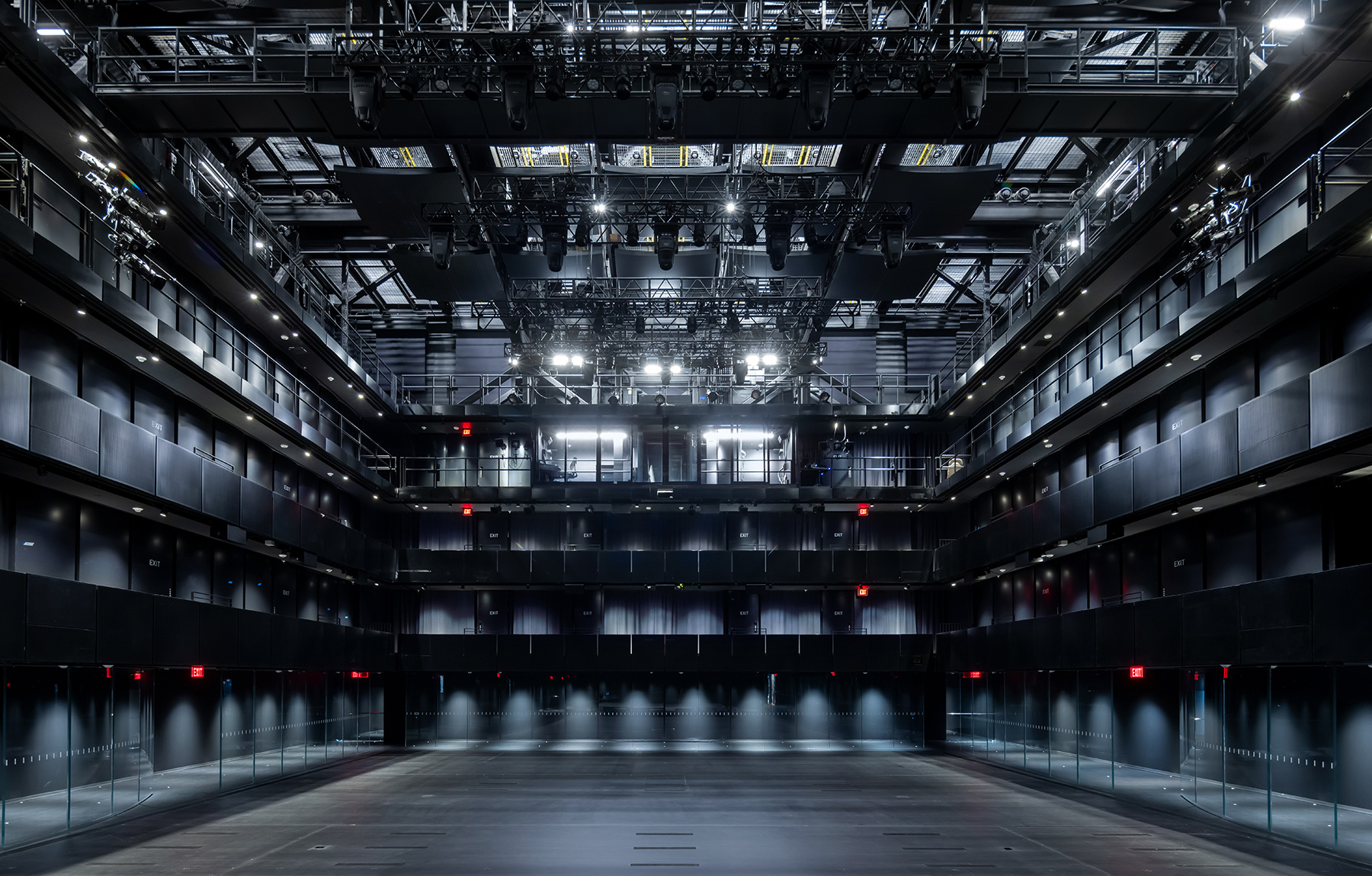
“That was the genesis of the highly flexible main hall,” says Chizmar. “We needed to create a performance space that could serve the symphony orchestra, that could serve theatrical groups, that could work for dance groups, and that would be for more contemporary media.”
Flexibility meets transparency
The resulting building, the 101,000-square-foot Lindemann Performing Arts Center, which opened in fall 2023, encompasses five performance venues in one:
- A 625-seat concert hall that has room for a 100-piece orchestra and includes an 80-person choir loft
- A 350-seat recital hall for smaller, chamber music or solo performers
- A 250-seat end stage theater with a traditional proscenium
- A smaller, cubelike experimental media configuration for nontraditional performances as well as standing concerts, seminars, and cabarets
- A flat-floor configuration with, Chizmar says, “all the tiered seating for audience removed so that they could do anything they want in there”
These preset performance spaces can be reconfigured by moving the ceilings, floors, and walls of the main performance space. The balcony seats, comprising two levels of audience seating and two technical levels, are hung by moving gantries – a large one at the rear and two on each side – which are not supported from the ground but from the main building’s truss system. Further, the main seating on the floor can be raised or lowered in different sections and at different heights to create a variety of seating arrangements. The building can be reconfigured among these presets in about four hours.
“The goal is that each preset would have exceptional acoustics, sightlines, and intimacy for the audience and the performers,” says Chizmar.
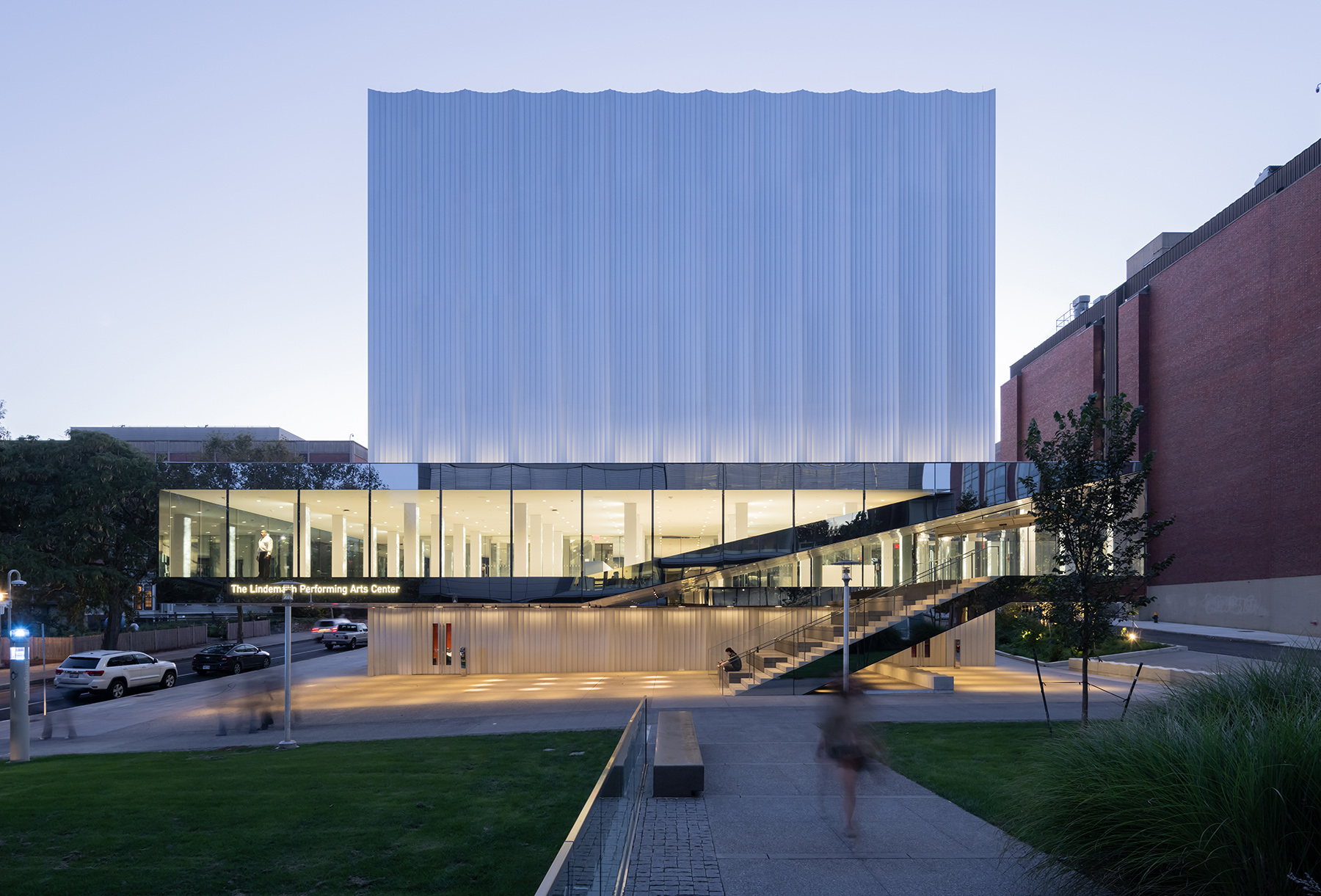
Along with this programmatic flexibility, openness became a guiding theme for the building’s design. Brown officials didn’t want a traditional separation between back-of-house functions and the front of house. So REX created a transparent ground floor, spanning the performance space and adjacent lobby. The performance space can be blacked out for shows, of course, but can also be opened up to people in the lobby and those passing by on the street.
“So when you’re in the lobby and when you’re outside, you can see in,” Chizmar says. Even when workers are changing configurations or performers are rehearsing, “whatever’s going on in the main hall, if they choose for it to be visible, it’s visible.”
This transparency created structural and acoustical challenges. Lindemann had to be “somewhat transparent at the ground level,” says David J. Odeh, P.E., S.E., F.SEI, F.ASCE, a principal at Odeh Engineers, which operates under the WSP umbrella. “That’s very unusual for a performance space. Most are enclosed boxes; they don’t have any windows.”
The transparent, column-free band of glass ringing the base of the building encompasses its lobby and main performance hall like a ribbon or, as Chizmar puts it, a “clerestory band.” This required engineers to devise a structure that could satisfy the building’s acoustical needs while also holding up the roof while not blocking that wraparound “window” without using columns or walls. Odeh and its engineering partner firm, Seattle-based Magnusson Klemencic Associates, developed a long-span steel belt truss system supported only at the four corners of the building. This steel structure allows the main box to have a column-free area of 86 feet by 113 feet.
What’s more, due to the compact site, the building could only rise about 75 feet, so the first order of business was to dig deep. “We conceived of a vertically stacked structure with a very deep basement,” Odeh says. “It’s about as deep as it is tall.” Much of the project – rehearsal spaces, mechanical equipment, storage areas, practice rooms, and the orchestra pit – is below grade. Further, engineers had to move the Sharpe House, a historic 1873 Victorian building, from the site to a new location to make way for Lindemann.
Sculpting sound
Lindemann’s transparency also created sonic challenges. “Performance spaces want to keep the sound and acoustics inside and keep whatever’s outside out,” Odeh says. “The challenge was to use glass to let people see inside, to be inspired by what’s going on inside, while still retaining world-class acoustics.”
The ceiling houses 40 80-square-foot, curved, veneered, medium-density fiberboard acoustic reflectors that can be tilted, raised, or lowered from about 48 feet above the stage down to just 4 feet. The reflectors weigh 860 pounds apiece and literally help shape the sound of the performance room.
“We can change the reflection structure to get full frequency sound into people’s ears at the right time and at the right level. And we can change the reverberation time, which is how long the sound lingers in the hall, while maintaining a sense of intimacy,” says Shane Jerome Kanter, a principal at Chicago-based Threshold Acoustics, which designed the building’s acoustic systems. “It has more bloom or more life, for instance, when it’s in the orchestra configuration, when it wants to be this big lush-sounding environment.” The theater configuration, by contrast, “wants to sound crisp and short so unamplified speech is heard clearly at every audience seat.”
Traditional concert halls employ heavy materials like masonry or wood veneered to masonry, so that low-frequency sounds are retained, leaving the room with a sense of warmth. So how could acousticians retain that sonic energy in a building with visually transparent glass walls?
“We made the glass just about as thick as we reasonably could while still staying under the weight limit of the hanging, movable gantries,” Kanter says. “So when you’re standing on stage, the first thing that the sound touches is an inch-and-a-half-thick laminated piece of glass that is curved in such a way that (it) pushes sound out into the audience as necessary, supporting music on its way to the audience’s ears.” He adds that strategically placed relief openings along the inner line of glass bleed off some of the excess sound energy, further develop reverberation, and allow the audience and performers to get in and out of the space.
The building features two more layers of glass: a 1 1/4-inch outer layer, which limits road noise, and a 1-inch laminated glass middle layer, which establishes the acoustic volume of the hall and limits sounds from surrounding corridors.
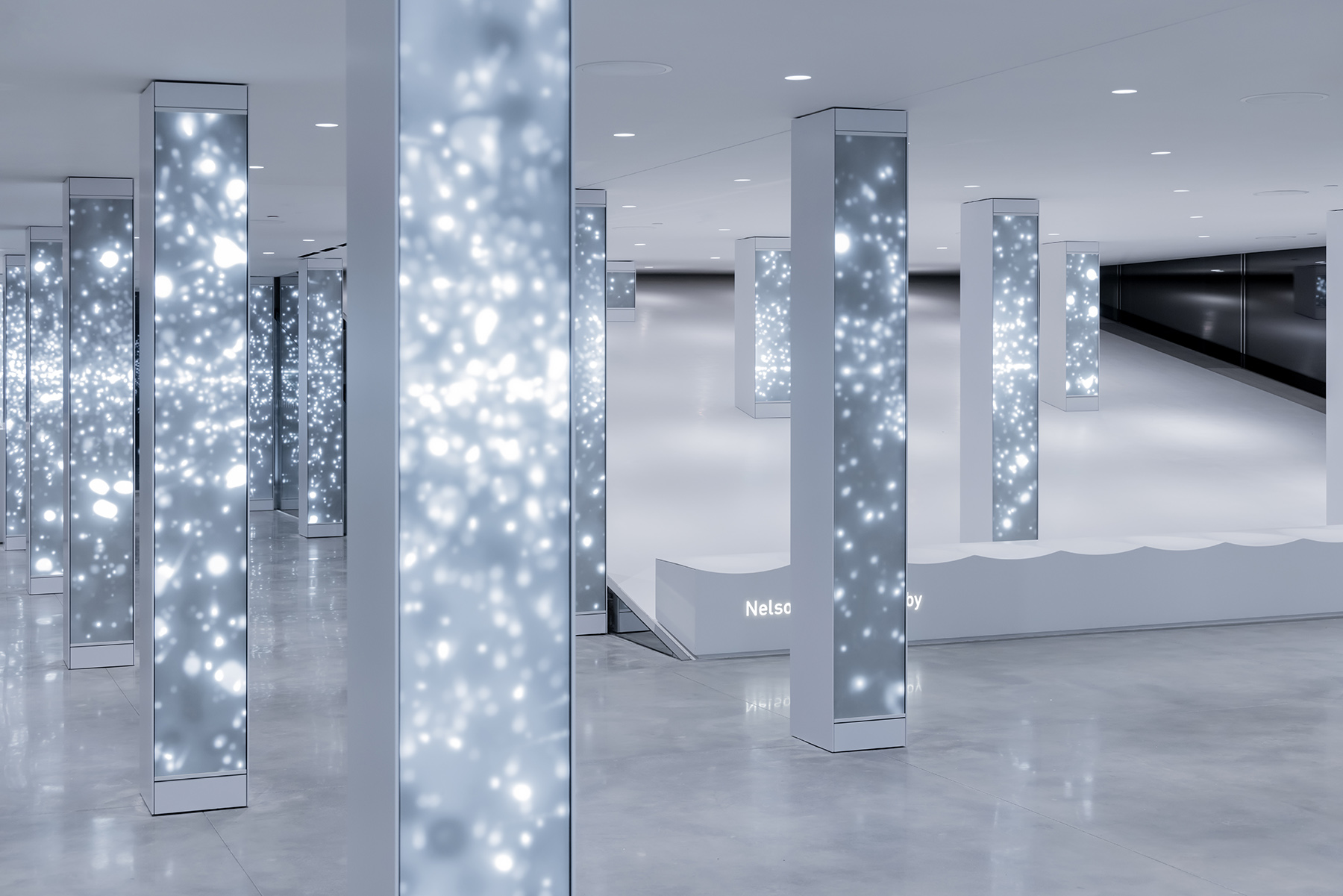
A distinctive exterior
Adjacent to the main performance hall is a lobby that cantilevers 37 feet off the east end of the building. What appear to be columns inside the lobby are actually the vertical members of a Vierendeel truss. “The lobby is basically a sandwich with those vertical members holding it together to stiffen it to be able to achieve that long cantilever that we wanted to do over that entry and create the lobby space,” Chizmar says.
The glass ribbon extends around the lobby volume, according to Odeh, “so we had to find a way to create a space with no diagonal members, as would occur in a traditional truss system, and very shallow structural depths at the floor and roof levels.” Working closely with REX, engineers devised a system of floor and roof beams interconnected with welded steel columns.
Artist Leo Villareal wrapped the columns with lights to create a 3D dynamic light sculpture, “shining a light,” as Odeh puts it, on the unique structural engineering behind Lindemann.
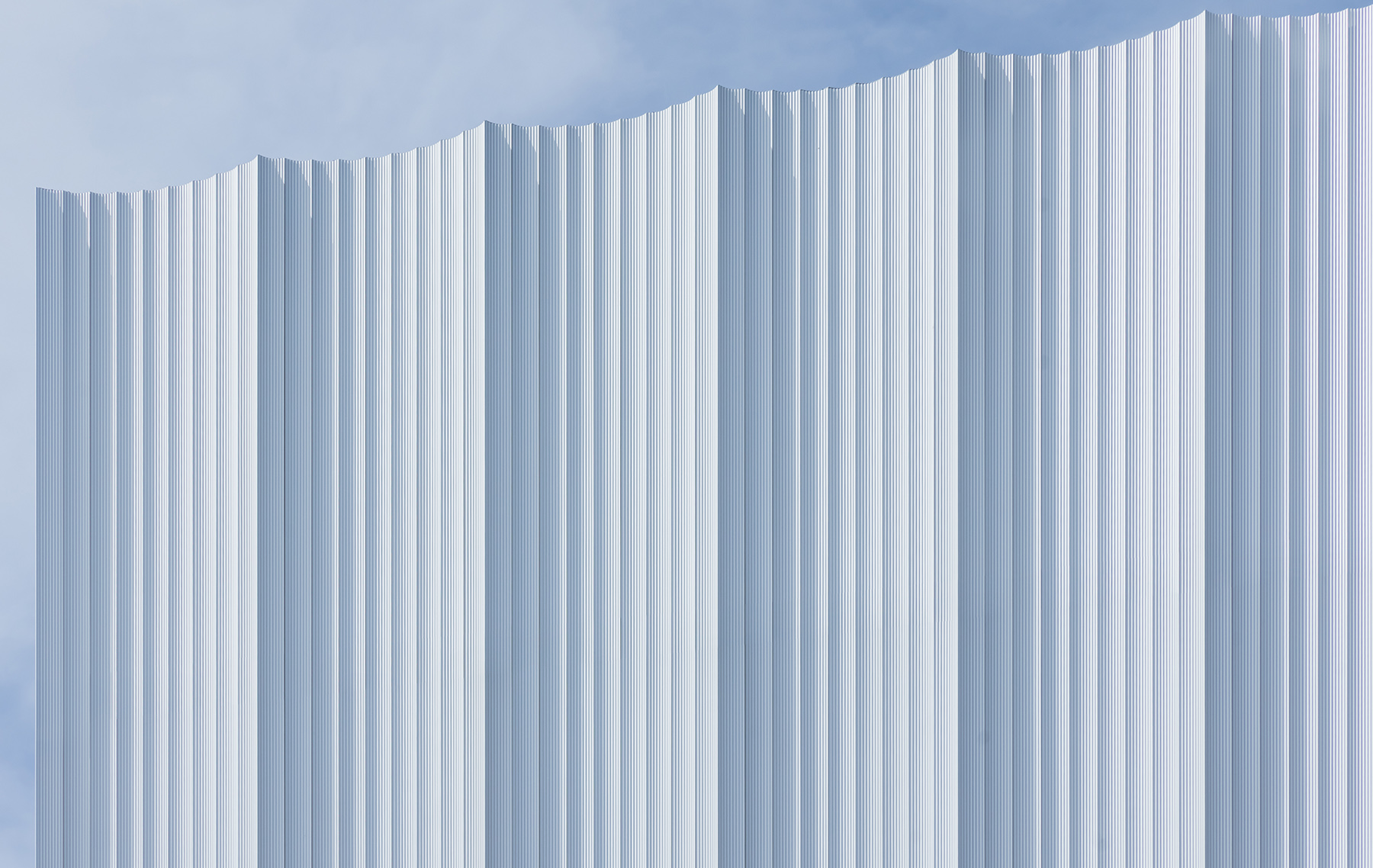
On the outside, architects sought to balance the transparent ground floor of Lindemann with a more opaque, textured facade for the rest of the building and created a series of scalloped, vertical flute shapes, each 7 feet, 1 inch in width and made of extruded aluminum. As you get closer, the fluting reveals a smaller, fractal-like second pattern – the pattern repeats within the scale of a single curved groove.
“So sometimes it’ll go there in a silver cast,” Chizmar says. “You won’t get much shadow at all. But sometimes you’ll go, and it’ll be direct light, and you’ll get a drastic, really beautiful shadow because of the fluting.”
There’s one other advantage. The fluting hides the horizontal joints between the extruded aluminum panels.
This article is published by Civil Engineering Online.