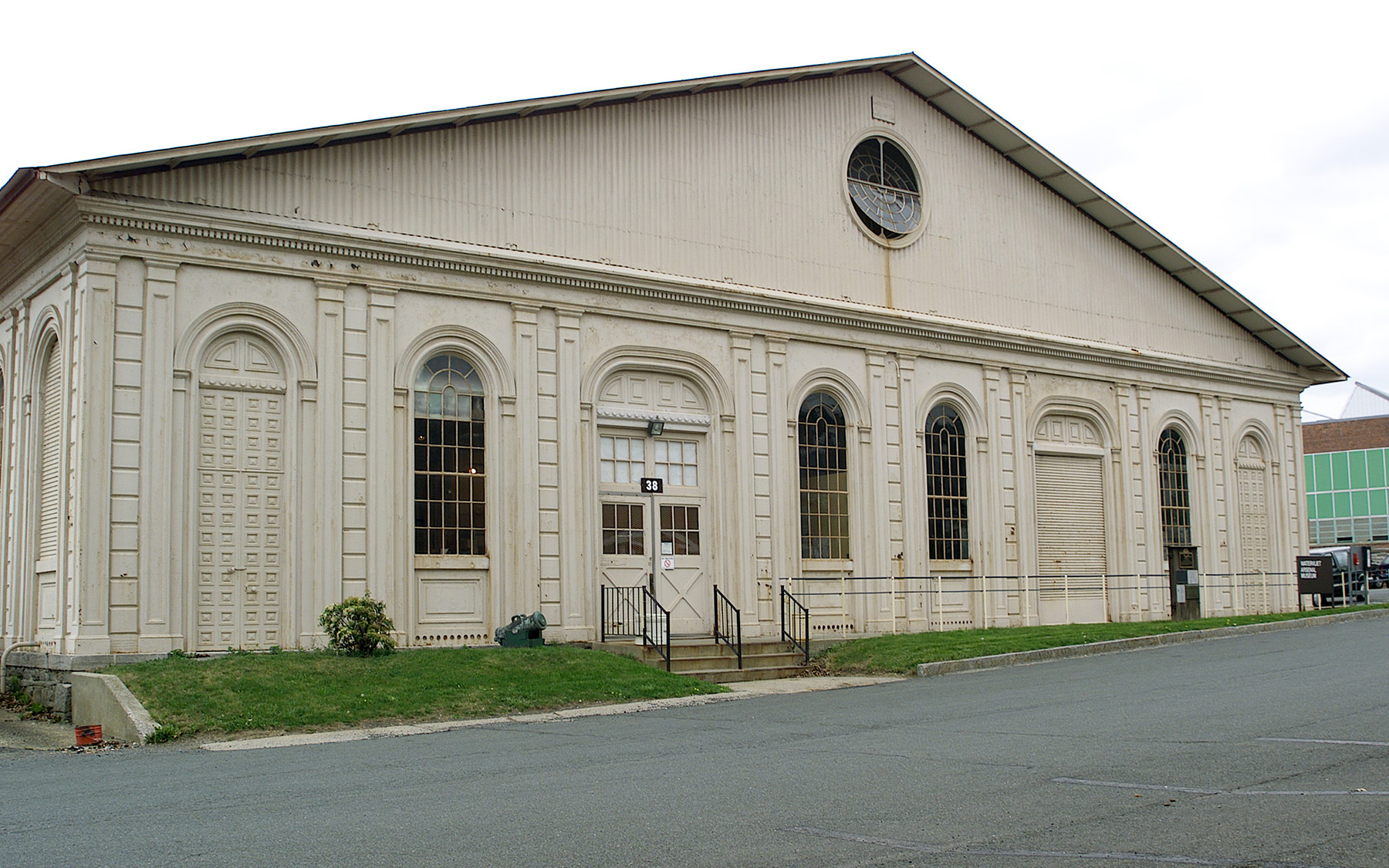
By T.R. Witcher
Upstate New York’s Watervliet Arsenal, the oldest active armory in the United States, brings together an unusual mix of history and engineering. As "America’s gun factory,” it has helped arm American military forces for conflicts, stretching from the War of 1812 through the Gulf War in 1991. And it also demonstrated the creativity and ingenuity of 19th-century American engineers, particularly in the use of cast iron as a building material: The arsenal’s 1859 ammunition storehouse represents the country’s oldest fully metal building and is an early example of prefabricated construction.
The emergence of cast-iron architecture in the United States in the mid-to-late 19th century “opened up new structural and decorative possibilities and pointed toward modern urban architecture,” wrote Margot Gayle and Carol Gayle in their 1998 book Cast-Iron Architecture in America: The Significance of James Bogardus (New York City: W.W. Norton & Co.).
The roots of Watervliet go back to the War of 1812, fought between the United States and Great Britain over American expansion in North America, among other causes. American commanders feared the British might attack upstate New York, near present-day Troy, from either Lake Champlain (to the north) or Niagara Falls (to the west), according to a Historic American Engineering Record report on the storehouse (Watervliet Arsenal Cast-Iron Storehouse, HAER No. NY-1), written in 1969 by architect David Bouse, architecture student Charles A. Parrott III, and architecture professor Richard J. Pollak. (The historical research was overseen by Robert M. Vogel, curator of mechanical and civil engineering at the Smithsonian Institution.)
The U.S. Army Ordnance Department (now called the Ordnance Corps) planned the arsenal to manufacture fixed ammunition and other small items to outfit infantry and artillery, including powder horns, pouches, flints, and cartridge boxes, according to the 1986 successful nomination for the storehouse’s inclusion on the National Register of Historic Places. (The cast-iron storehouse was named a Historic Civil Engineering Landmark by ASCE in 1983.)
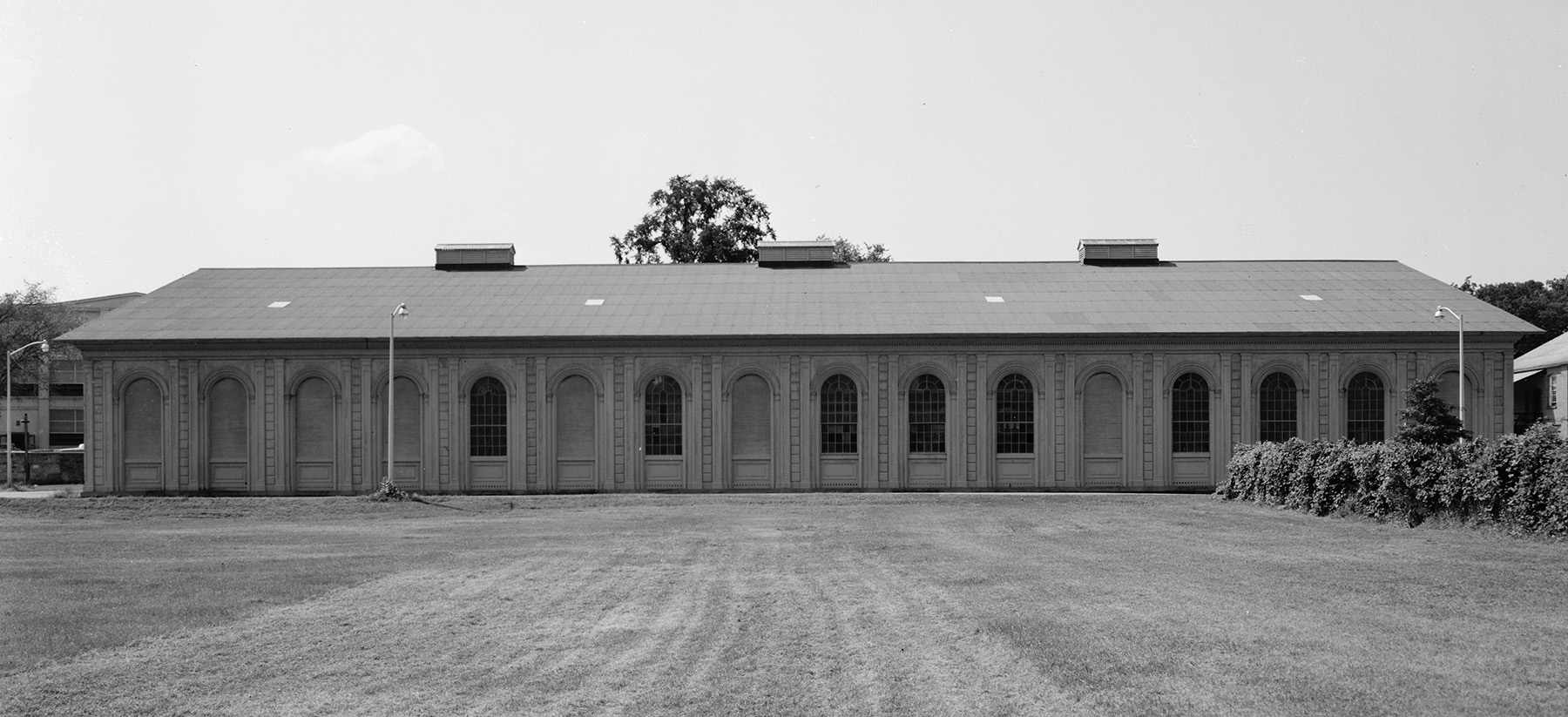
Army planners selected a 12-acre site near Albany named Gibbonsville — and later renamed Watervliet, the Dutch word for flowing waters. The location was “strategically important,” according to another HAER report, from 1986, on the entire Watervliet Arsenal, written by historian Barbara E. Hightower (Watervliet Arsenal, HAER No. NY-1A). “Supplies could be transported along the Hudson and Mohawk Rivers to American defenses on the Canadian border and in New York City,” Hightower wrote. “Its proximity to the river was also advantageous since lengthy portages of equipment over land were eliminated.”
By the end of 1813, the Army had quickly erected 10 buildings, including an “arsenal, the commandant’s quarters, a barracks and hospital, a combination office, paint shop, and commissary store, two assistant officers’ quarters, and two enlisted mens’ quarters,” along with two small stables. Over the next few years, Hightower adds, more buildings were added, including a pair of timber sheds, three gun houses, and a small laboratory, but none of these latter buildings survived. By 1817, the installation had adopted the name Watervliet Arsenal.
The history of the Watervliet Arsenal is best understood as a constant cycle of expansion and atrophy — adding capacity in times of war, falling into underutilization during peace. Over the next several decades, the site was in a state of growth. The Erie Canal was built through the Watervliet site in the early 1820s, which allowed the arsenal to ship munitions efficiently. By the early 1830s, the arsenal began using hydropower from the canal to power the facility. By the end of that decade, the arsenal’s focus had shifted to manufacturing carriages for large guns, according to Hightower.
By the time of the Mexican-American War (1846-48), employment at the arsenal had doubled and the “production of cartridges for muskets, rifles, carbines, pistols, and flint and percussion arms averaged over one million every two weeks,” Hightower wrote. When the war ended, “Watervliet was inundated with supplies returned from the battlefield, making its immediate priority one of repair and storage.”
The arsenal continued innovating in munitions technology in the 1850s, including producing seacoast gun carriages out of wrought iron instead of timber and developing, Hightower noted, an “improved bullet press that enabled the arsenal to nearly triple bullet production.” Nevertheless, by the 1850s, the arsenal had entered a period of decline. The commanding officer of Watervliet, Maj. John Symington, was in poor health; the arsenal, wrote Bouse et al., was disorganized and needed a strong leader.
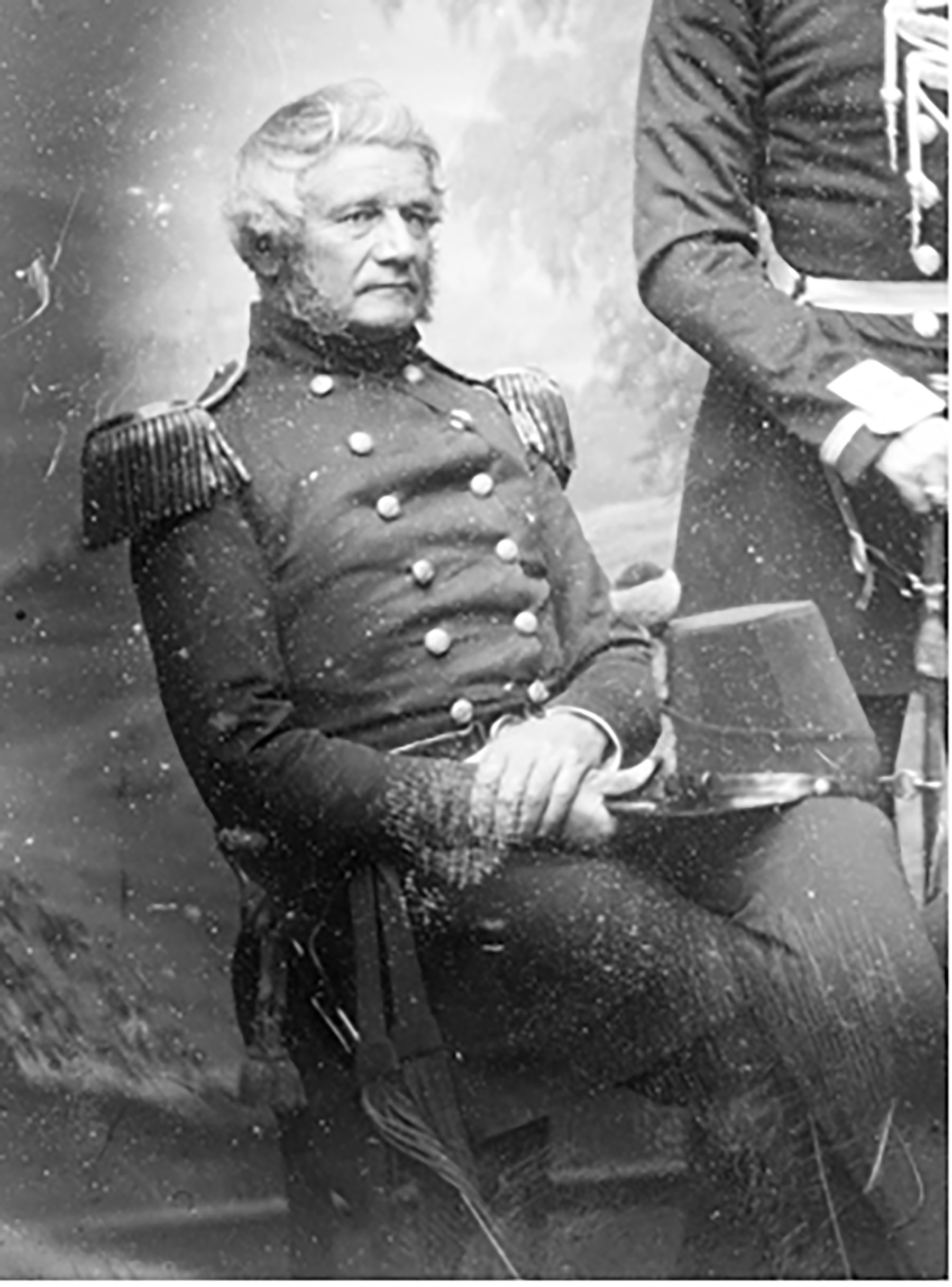
That leader was civil engineer Maj. Alfred Mordecai, an 1823 West Point graduate, who had entered the U.S. Army Corps of Engineers that same year as a commissioned second lieutenant and eventually became an ordnance officer. In 1855, he traveled to Europe to study engineering and military developments, including the structural capabilities of iron (as evidenced in railway depots).
The North Carolina native was appointed commanding officer at Watervliet in June 1857, a post he would hold for four years. Mordecai’s first order of business was constructing a new munitions storehouse. He envisioned a railway depotlike structure, “a shed about 125 feet wide and 250 feet long” that would have room for 300-350 gun carriages, according to Bouse et al. He also wanted a structure with a raised, stone floor to protect the storehouse from flooding and drainage from the Erie Canal.
He wanted an ornamental building. Most of all, he wanted cast iron.
Humans have used iron for thousands of years. Gayle and Gayle wrote that while ironworking was first developed in Asia Minor, “perhaps as early as 1500 B.C., with smelting of iron on a regular basis dating from about 1000 B.C.,” limited supply and technology constrained the use of iron in buildings in many places through the early modern period. Cast iron, wrought iron, and steel are the “three basic ferrous alloys,” the authors continued. Wrought iron has a tiny amount of carbon and can be hammered, forged, or rolled but not cast. It has considerable tensile strength, “making it perfect for tension rods and for beams.”
Unlike wrought iron, cast iron, which involves heating iron to a molten state, possesses much greater carbon content. “The carbon increases the alloy’s hardness, giving it great strength in compression and making it ideal for columns used to support heavy loads,” wrote Gayle and Gayle. “On the other hand, the carbon makes cast iron rather brittle, so that it has little elasticity and is low in tensile strength. Extensive production of cast iron became possible only with technological advances achieved between the fifteenth and eighteenth centuries, specifically furnaces able to heat the metal to a liquid state and the adoption of coal as a fuel.” By the 1790s, they continued, British foundries could produce cast iron in large quantities at an affordable price, allowing cast iron to be used in major construction projects such as bridges and framing for factories.
According to a National Park Service preservation brief, The Maintenance and Repair of Architectural Cast Iron, by Margot Gayle and John G. Waite, AIA, slender, cast-iron pillars were introduced in the 1790s in fire-prone English cotton mills. They began to turn up in the United States in the 1820s in balcony support columns in churches and theaters. By the end of the 1840s, wrote Gayle and Gayle, iron was becoming increasingly widespread in the United States.
Cast iron had many benefits. When molten, it was easy to pour into molds to make virtually any sort of ornamental form. It was stronger and proportionally lighter than masonry. And it was cheaper: “The elements can be factory-produced, (reducing) the need for skilled craftsmen on the job,” according to Bouse and his co-authors. Its weakness — its poor tensile strength — could be offset by reinforcing cast iron with wrought iron.
Moreover, the material is highly fire resistant. “Although it will warp and buckle at high temperatures,” according to the HAER report on the storehouse, “it will continue to support its load, thus making it a perfect choice of material for a warehouse whose contents are more valuable than its own walls.”
Mordecai contacted several builders and contractors and finally connected with the New York City firm Architectural Iron Works. AIW was founded by a self-trained engineer named Daniel D. Badger. Along with architect and inventor James Bogardus, Badger helped bring cast-iron construction into the mainstream on a large scale. Between 1850 and 1870, the firm built an array of cast-iron structures in New York, including in 1857 the landmark E.V. Haughwout Building in Manhattan’s SoHo neighborhood — the epicenter of cast-iron construction in the United States. (Years later, in 1871, Badger built a massive cast-iron train shed for Manhattan’s Grand Central Depot, the precursor structure to Grand Central Terminal.)
“With his team of anonymous architectural designers, modelers, pattern makers, and molders, Badger sought to reproduce ... in iron whatever could be produced in stone,” wrote Bouse et al.
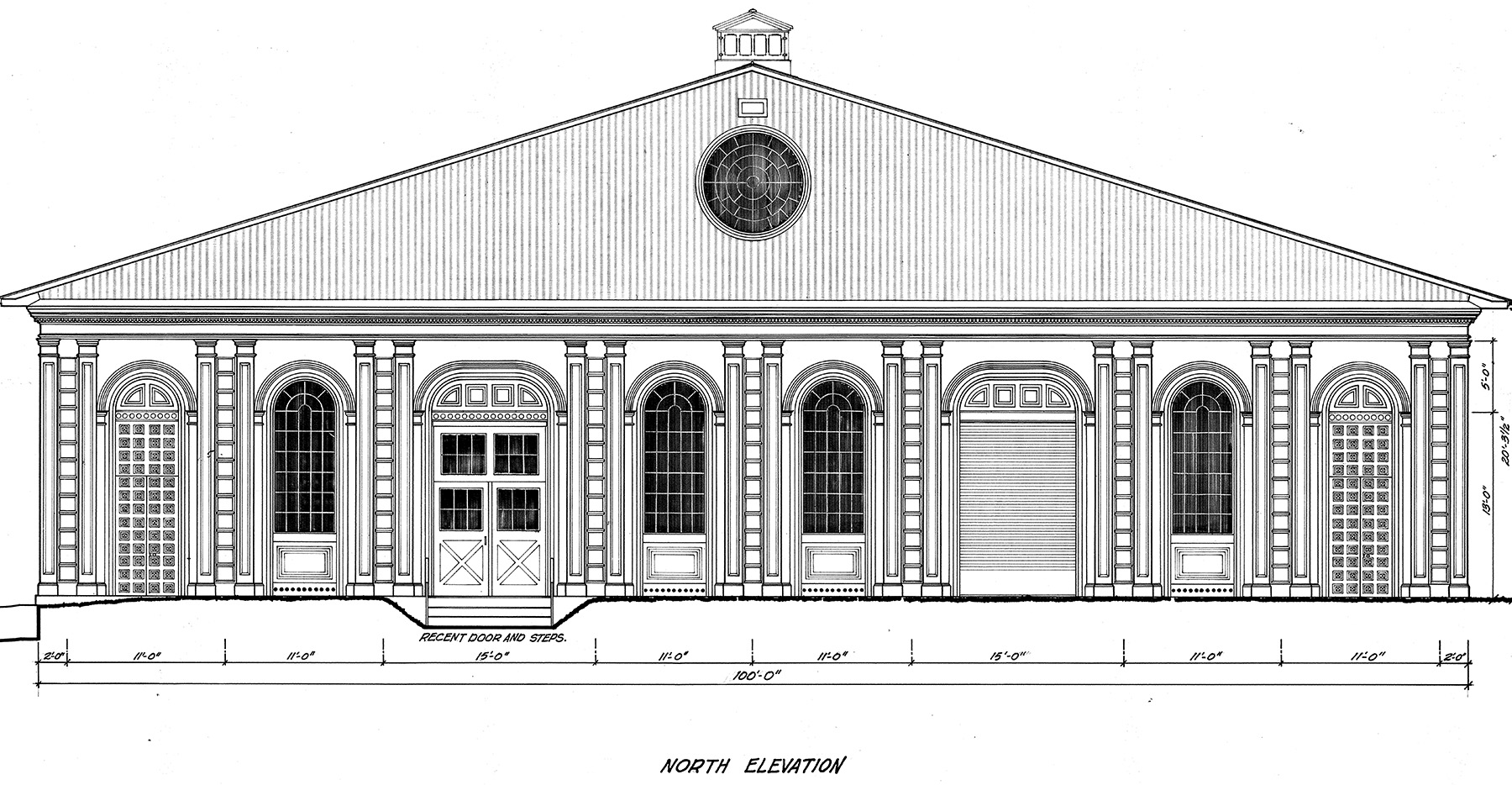
The arsenal commissioned AIW to fabricate the new storehouse, working from plans designed by Mordecai. The result was a structure with a neoclassical facade that measures 100 ft by 196 ft and encloses 16 transverse bays and three longitudinal aisles. In addition to a ground floor, the outer aisles each contain a gallery in the 14 inner bays. According to Bouse and his colleagues, the “fourteen 12-foot interior bays and two 14-foot exterior bays are delineated by transverse cast- and wrought-iron Fink trusses over the center aisle and modified Fink trusses and composite beams over the side (gallery) aisles. The center-aisle trusses span about 50 feet, the side-aisle trusses and beams about 25 feet. Both trusses are about 8 feet deep, maximum. Both center and side-aisle trusses share the same colinear top chord. All truss members and purlins are wrought iron except for the cast-iron cruciform compression struts.”
For the walls, cast-iron panels were “connected by flathead, counter-sunk machine screws through flanged and lipped surfaces, only the counter-sunk heads appearing on the exterior. The paired cast-iron pilasters, 1/2-inch thick, are part of load-bearing channels that provide stiffening for the walls and support one end of the gallery roof trusses on the side vails. Corner pilasters are built up box columns. The fenestrated panels and the rusticated detail between the pilasters, both generally 5/16-inch thick, are non-load-bearing.”
Badger pioneered the use of prefab construction, according to historians. Bouse et al., wrote, “His exploitation of iron technology anticipated, in a crude fashion, the steel frame of the twentieth century skyscraper.” In a developing era of mass production, AIW also used a standard structural system that was easy to adapt to different uses. Badger’s firm made prefabricated pieces in New York City and then shipped them up the Hudson River to be installed on-site; work on the project took only six months.
The building’s completion was just in time; the arsenal had begun steady preparations as hostilities between the North and South foreshadowed the coming Civil War. Hightower quoted a 1920s history of the arsenal written by Francis K. Kyle that noted that at the onset of the Civil War, the arsenal was employing 2,000 people, manufacturing thousands of barrels of gun powder, and building small arms cartridges by the millions.
As it turned out, the Civil War led to Mordecai’s departure. He was a Southerner by birth, which angered many within the Army. In May 1861, he resigned from the Army and eventually relocated to Mexico. After the war, according to Bouse et al., he directed construction of a railroad running from the Gulf of Mexico to the Pacific Ocean. In 1867 he returned to the United States and spent his final 20 years working for “coal and canal companies controlled by the Pennsylvania Railroad.” He died in 1887.
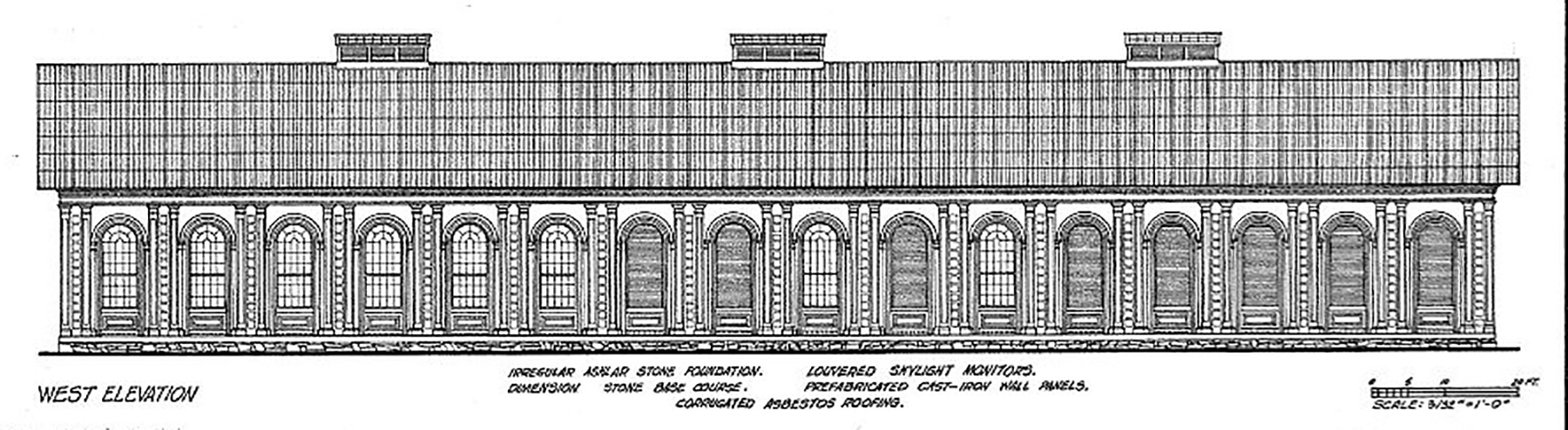
A few decades after the war, Watervliet was selected by President Chester A. Arthur to develop a new generation of breech-loading cannons. In the 1910s, the arsenal developed a balloon gun to defend attacks from airplanes and dirigibles. Not surprisingly, the arsenal expanded during World War I and reached its peak in the manufacturing of guns during World War II.
But by the time of the Korean War, Hightower wrote, most of America’s military munitions manufacturing had been transferred to private companies, a development that was later reversed during the Vietnam War era. In the 1970s, work picked up, particularly on heavy weapons like the 175 mm M113 cannon. “In late 1970 the arsenal cancelled orders to private manufacturers and again became the only active cannon producer in the country,” according to Hightower.
In the late ’70s, the arsenal was at the center of a large program called Renovation of Armament Manufacturing that led to the development of weapons systems for the M1A1 Abrams tank and, later, laser-guided bombs used during Desert Storm, according to an article written by Brig. Gen. Raymond E. Bell Jr. (“Watervliet Arsenal: Watervliet, New York,” On Point, Summer 2016, Vol. 22, No. 1, pages 45-49). According to the Army, the arsenal is currently home to Combat Capabilities Development Command Armaments Center’s Benét Laboratories, a research and design facility for large-caliber weapons. And the arsenal produces advanced weaponry for cannons, howitzers, and mortar systems. Watervliet still covers a 143-acre site with 72 buildings comprising 2.1 million sq ft of manufacturing and administrative space.
Through it all, Mordecai and Badger’s cast-iron storehouse remained resilient. Bouse and his colleagues wrote that in March 1913, the Hudson River, “exceeding all previous flood records,” left a watermark of 10 in. on the first-floor level of the structure. No major damage was incurred, “and the building still functions as it was intended.”
Eventually, the needs of a modern arsenal outstripped the capacity of the storehouse; it was converted into an ordnance museum in 1987 and closed in 2013.
Bouse, Parrott, and Pollak argue that in the first half of the 19th century, American engineers were largely supplied by Europe or West Point or were self-taught. As an expression of the structural and ornamental possibilities of cast iron, they wrote, “The iron storehouse at Watervliet Arsenal reflects in many ways the representative skills of America’s nineteenth century engineers.”
T.R. Witcher is a contributing editor to Civil Engineering.
This article first appeared in the May/June 2022 issue of Civil Engineering as “Cast-Iron Colossus: The Watervliet Arsenal.”