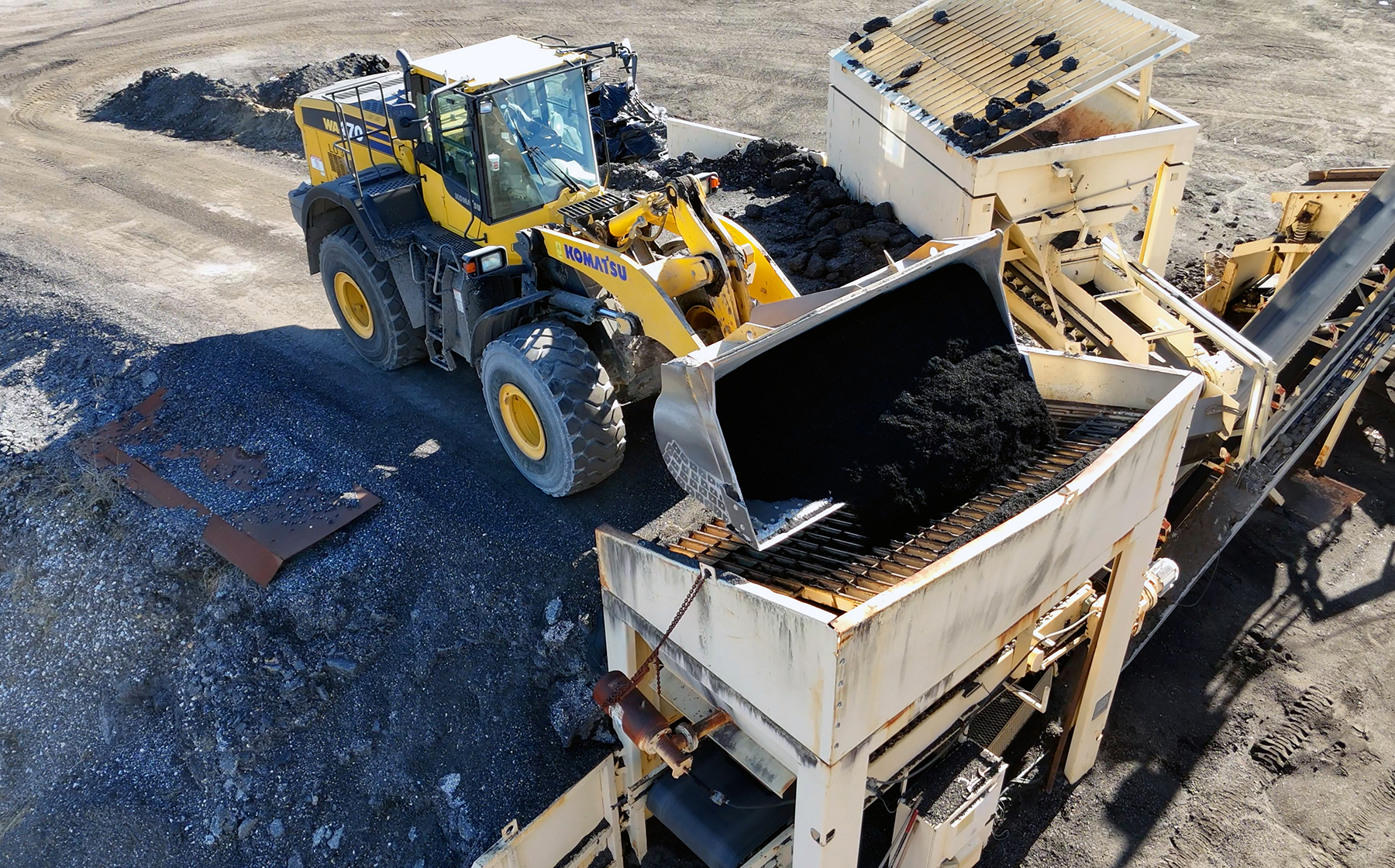
Hot, smelly, and utilitarian, asphalt is a go-to material for roadway construction.
In the U.S., about 94% of roads are paved with asphalt, stretching more than 2.6 million miles. Asphalt also packs a climate punch, releasing carbon dioxide emissions throughout the production and installation process.
Further reading:
- System estimates asphalt density in real time
- Concrete collaboration promising for speedy, cost-effective bridge repairs
- The renewable energy source right beneath our feet
A new bio-based asphalt could disrupt the traditional asphalt production and installation processes. Verde Resources Inc., a St. Louis-based construction and building materials company that focuses on net-zero products, tapped into the underused biochar industry and reimagined what asphalt could be.
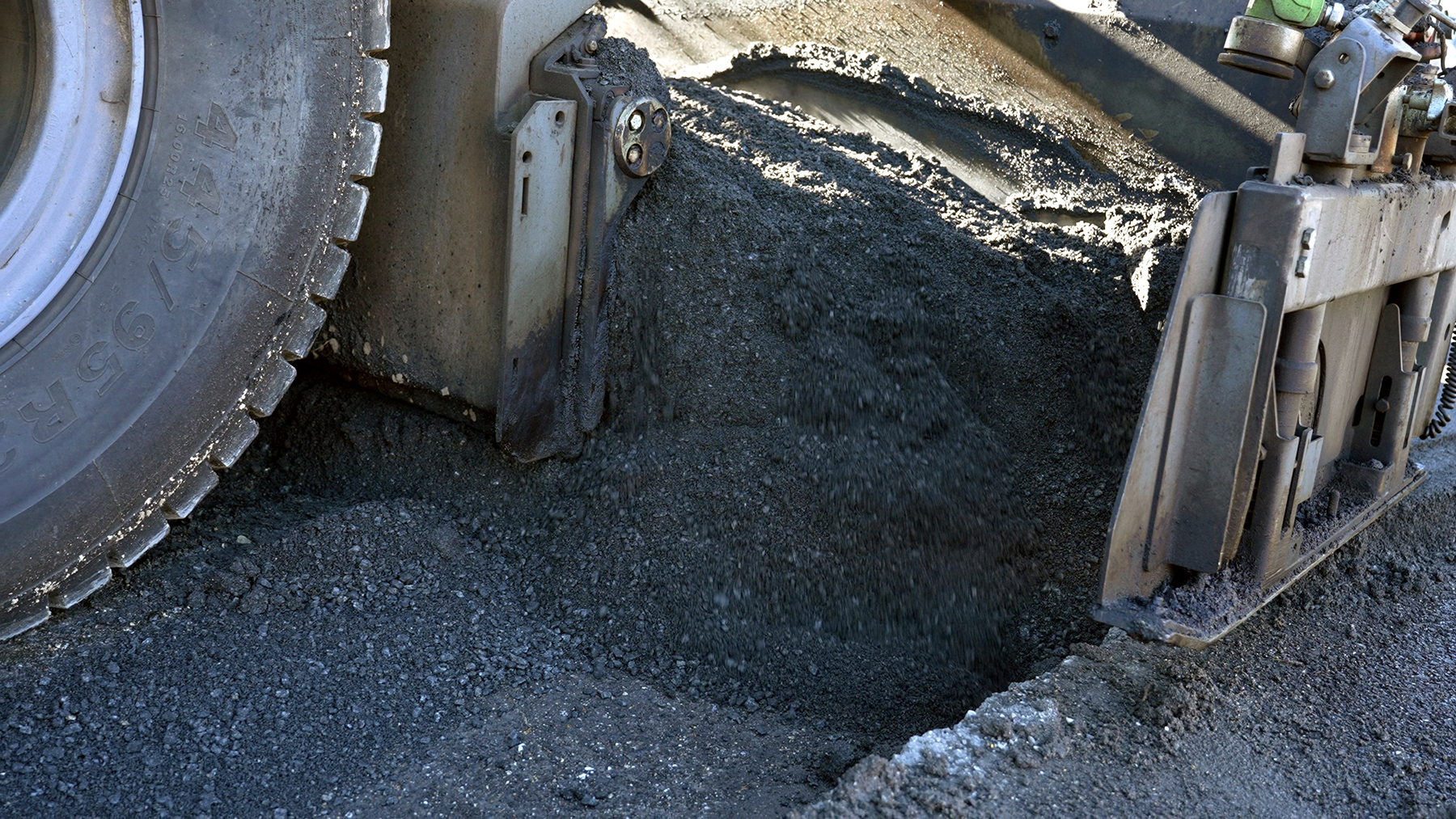
Using aggregate mixed with a proprietary chemical in its binder, the team created a cold-mix, odorless, reduced-emission asphalt that can be driven on immediately after installation. The asphalt incorporates biochar into the aggregate, which also sequesters carbon within the mix.
The bio-asphalt was installed in December at the National Center for Asphalt Technology Test Track, at Auburn University in Alabama, and is in a three-year testing period. The team noted the initial performance has been promising – in April, the 110-ton cold-mix project was issued 8 tons of carbon removal credits by the crediting platform Puro.earth.
The Verde team hopes its bio-asphalt product will prove to be a cost-effective, carbon-credit road material that can be installed during all seasons.
A new life for biochar
Typically, during the summer months, construction workers are installing hot-mix asphalt along roadways. The shimmering-hot and odiferous material is about 95% aggregate (stone, sand, or gravel) and bound together by a petroleum-based asphalt cement.
HMA is a robust material for high-traffic areas, but producing, transporting, and installing the material results in a high carbon footprint. For instance, researchers found that between 2016 and 2019, the Oregon Department of Transportation’s use of asphalt concrete pavement released an average of 65,200 megatons of carbon dioxide emissions each year.
The Verde team wanted to tackle these emissions on multiple fronts. Working with Oregon Biochar Solutions, the team looked to give high-carbon biochar a new purpose. Biochar companies turn biologic material – food waste, tree bits, corn stalks – into charcoal, which locks carbon into place.
Biochar has been touted as a product for regenerative farming, but there has been a bottleneck in widespread adoption.
“Farmers are not paying for char because farmers have very little margins,” explained Verde CEO Jack Wong. Biochar companies remain viable because instead of selling the char itself, they turned to giving char away and selling carbon removal credits.
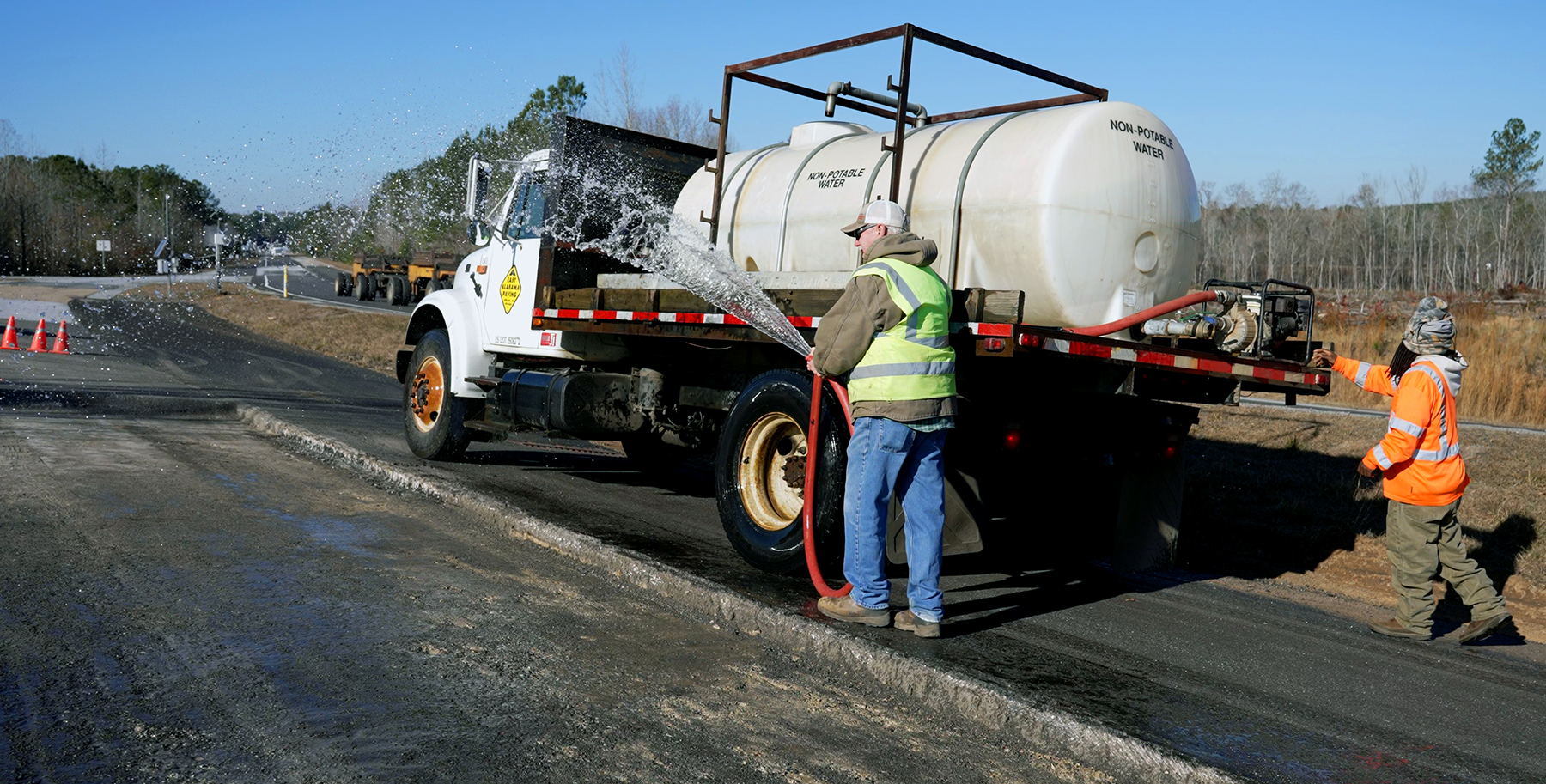
But Verde saw potential in using the biochar for a bio-asphalt. “Our MO is to make the product on par with HMA pricing-wise – or better yet, cheaper – because we want to create a no-brainer scenario for industry, clients, and DOTs to switch.”
The team created a mix that incorporates biochar into the aggregate mixture. A proprietary emulsion – which Wong calls a “spice” mixed with water – keeps the char’s carbon-storing integrity while maintaining the durability of the asphalt.
“If you were to mix biochar with liquid emulsion and other aggregates like limestone or granite without our proprietary spice, it will not work,” he said. “The product will become very, very brittle, very fragile.”
Putting bio-asphalt to the test
Incorporating biochar into the mix was only one method of reducing carbon emissions in asphalt.
The team also wanted to eliminate the need for heating asphalt during production and installation – a process that uses a significant amount of fossil fuel. And workers need to move fast after mixing up a batch of HMA.
“With HMA, you only have a six- to eight-hour window to install before it goes bad,” Wong said.
Verde wanted to avoid these limitations. The team focused on creating a cold-mix asphalt that can be made with traditional machinery, stored overnight, installed during winter months, and ready for immediate traffic.
After creating the proprietary mix, the team headed to the track at Auburn to test the product. The team worked with East Alabama Paving, retrofitting an existing HMA system to mix a batch of bio-asphalt.
On a cold day in December, team members made 110 tons of bio-asphalt and stockpiled it overnight to test its longevity. The next day, they installed the bio-asphalt with traditional paving equipment, using no heat and no solvents (only water). Wong said that avoiding solvents also eliminates the typical cloud of intense odors and reduces health risks for workers.
After installation, the bio-asphalt was immediately exposed to heavy-duty traffic.
“With HMA, once you put up the product, you need to close the section and allow it to dry at least 24 hours before it opens,” said Wong. “Ours is the exact opposite. We encourage immediate opening – the more tires that run on it, the better because they drive the moisture out.”
Running 80-ton trucks, which are twice the legal U.S. weight limit, on the NCAT track allows researchers to reduce a 10-year testing of new materials to three years. This testing helps identify longevity issues with materials.
Facing potential limitations
Verde knew it was important for the bio-asphalt to be competitively priced. Today, the costs are on par with HMA, but Wong said when “you can turn off the burners, there’s a lot of savings.” When factoring in energy savings during production, carbon credits, increased efficiency, and the fact that no solvents are needed, he said bio-asphalt is “definitely cheaper than HMA.”
And biochar is an abundant resource. “The good news is there are 700 million tons of biogenic waste in the U.S.,” quipped Wong. That waste, he estimated conservatively, could make about 70 million tons of biochar – enough char to make 1.4 billion tons of end product. “Scalability is there,” he said, but Verde is waiting for testing to be complete.
There are two big problems with road asphalt: deformation and cracking. When traffic moves slowly or stops, say at traffic lights and intersections, it is easy to spot deformation – the asphalt sort of oozes, creating low, puddlelike divots in the roadway.
“The big problem in the U.S. is cracking,” said Erdem Coleri, Ph.D., a civil engineering professor at Oregon State University and the director of the OSU-Asphalt Materials and Pavements Laboratory. “How is the biochar going to affect the cracking resistance? That’s a big question.”
While field testing can reveal a lot about the longevity and behavior of a material, Coleri noted some limitations. Because field tests are normally at one location, he argued that the tests are “not really representing the clients all over the United States … material properties are different, climate is very different, traffic is different.” Instead, Coleri said, running more comprehensive laboratory studies could help tease out these variables in a more efficient and cost-effective way.
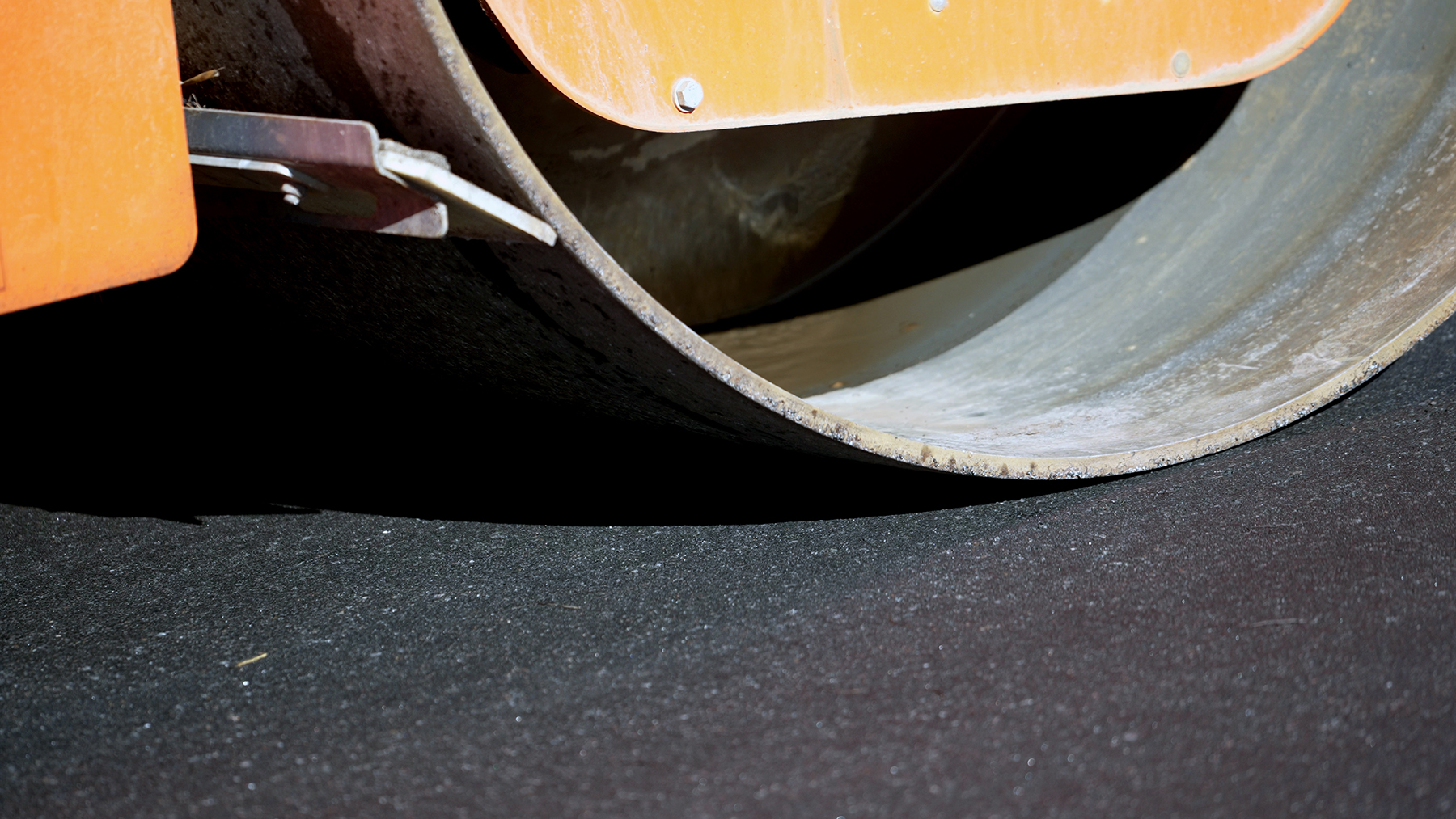
He and other scientists are considering asphalt that incorporates waste plastics, recycled tires, and recycled asphalt. Coleri argued that laboratory studies can effectively weed out the bad additives from the good. “Some people consider asphalt as like a garbage can – you can throw anything in it and it will work. But it’s an engineered material,” he explained.
Coleri noted that no single thing is enough to stop climate change, but that efforts like bio-asphalt are contributing to the solution. And although the bio-asphalt testing is only a few months in, Wong and his colleagues are confident they are moving in the right direction.
“I believe we have created a model, a blueprint that can tap into existing infrastructures, tap into existing industries to allow them to seamlessly transition to net zero,” said Wong.
Watch a video of the installation process here.