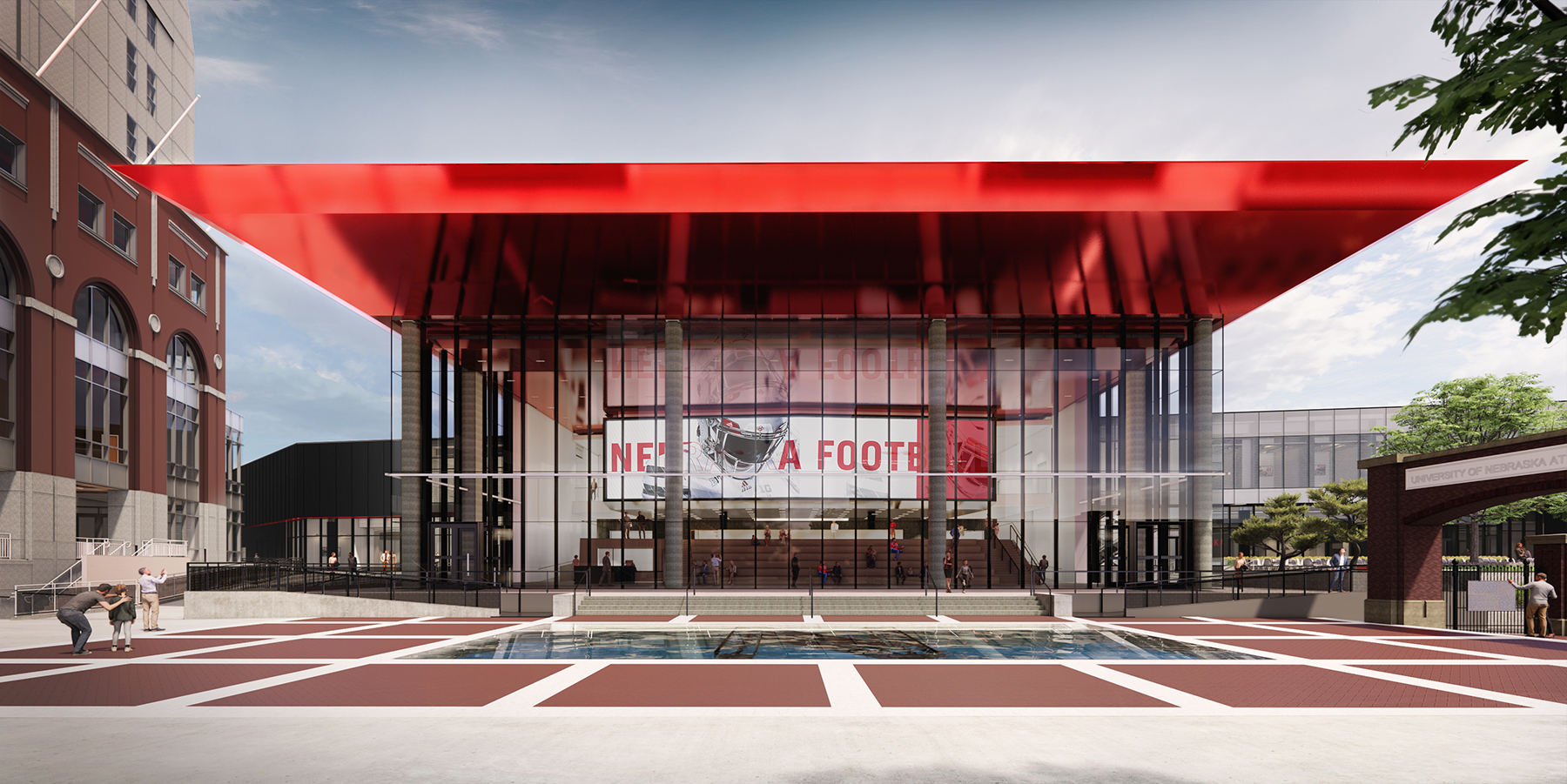
By Erleen Hatfield, P.E., F.ASCE, and Rebecca Jones, P.E., S.E., M.ASCE
After years of fundraising, in 2019 the University of Nebraska-Lincoln announced the construction of a state-of-the-art training center to attract and cultivate some of the nation’s top student-athletes. More than just another athletic facility, it is a showpiece in UNL’s stadium complex and a testament to the university’s commitment to athletic excellence.
When Tom Osborne retired as head coach of UNL’s football team after the 1997 season, he left a team that he had shaped into one of the most dominant forces college football had seen up to that point, having led his Cornhuskers to three national titles in four years (1994, 1995, and 1997).
Unfortunately for the university, after Osborne’s departure the Cornhuskers would not be the same. They saw success only in fits and starts and were overshadowed by their Big 12 Conference rivals.
So, when the Cornhuskers moved to the Big Ten Conference in 2011, it signaled a new start for a team struggling to reclaim its former glory. Fast-forward to 2019, when UNL, in another effort to realize its full potential, announced it would build an athletics training facility. Opened in August, the new sports center is the culmination of an ongoing, multiyear fundraising campaign dubbed GO BIG.
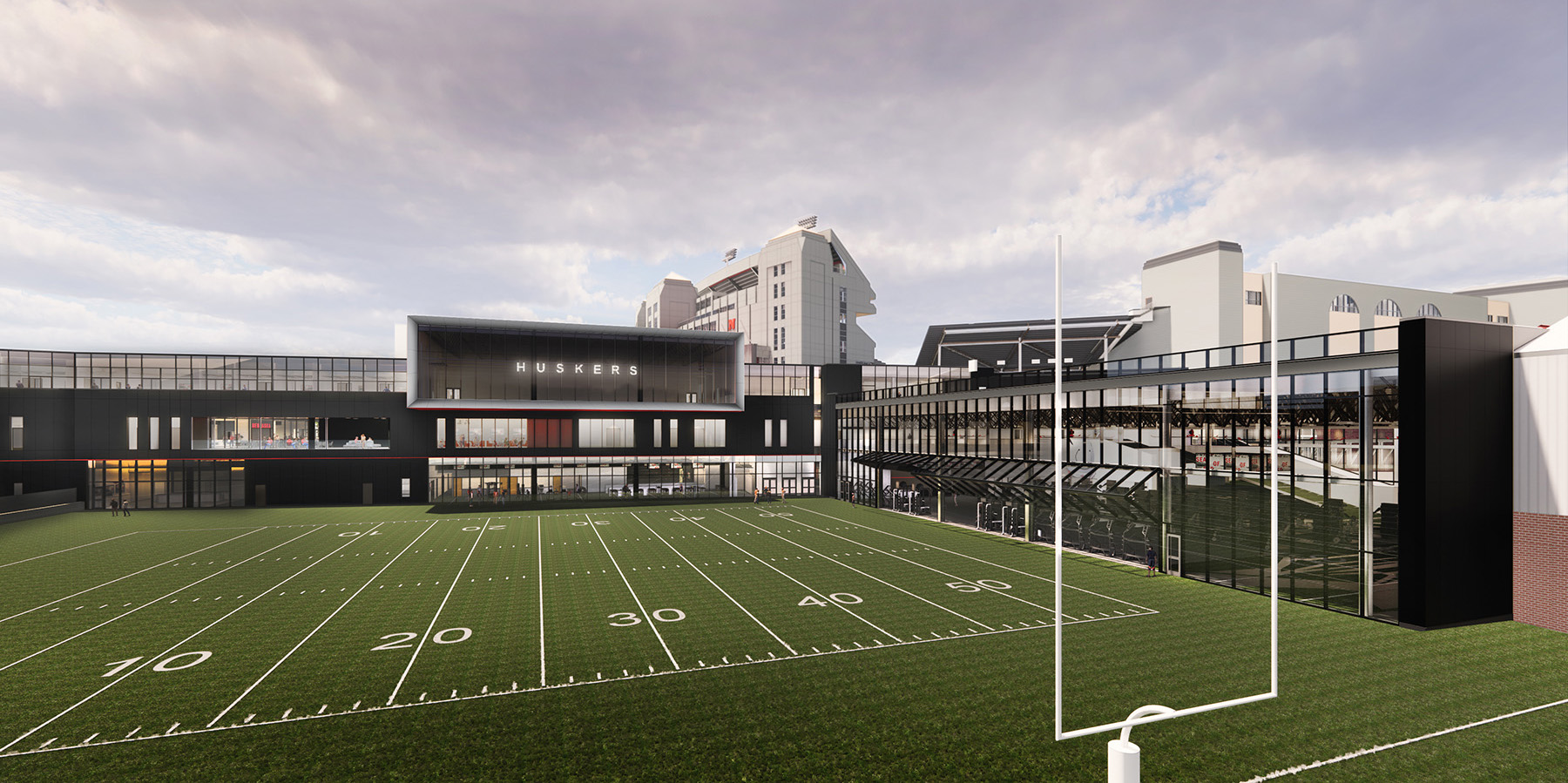
The $165 million, 315,000 sq ft facility offers world-class weight training facilities, locker and recovery rooms, a hydrotherapy pool, walkthrough rooms, specialized athletic clinics, conference halls, public auditoriums, and offices with balconies overlooking the adjacent practice fields.
A campus centerpiece
The proposal for the facility was bold. The design called for a three-story structure — with the option of adding a fourth — that would have a cantilevered roof section above a sweeping, almost column-free glazed atrium.
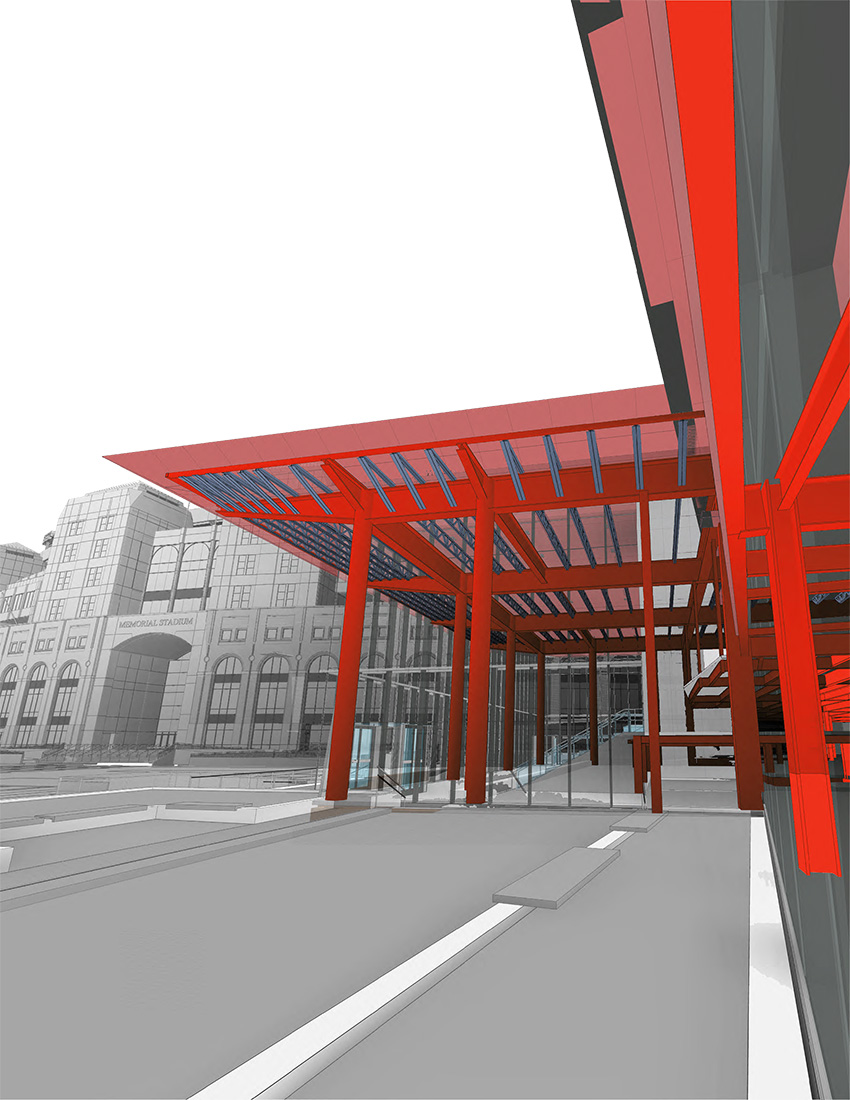
The existing athletics field (where the track and field teams practiced) and encircling track next to the 90,000-person capacity Memorial Stadium would be moved, leaving an L-shaped plot about 400 ft long and 150 ft wide for the new building.
In addition to relocating the athletics field and track, there were site challenges to overcome as well: The new building had to navigate a full-story grade difference across the site and accommodate infrastructurally demanding training equipment, not to mention integrate into the surrounding stadium complex and connecting tunnels.
It became apparent quickly during the schematic design phase that achieving the project’s goals and design intent would require testing new ideas and questioning traditional approaches and that solving the various challenges would require close cooperation among the project team.
Hatfield Group was the structural engineer. Populous was the design architect; BVH Architecture was the local architect; ME Engineers provided mechanical, electrical, and plumbing services; and Hausmann Construction was the general contractor. Uni-Systems Engineering, a specialist in moving structures, was tapped to design a key program element and selling point to prospective student-athletes: moving weight training platforms that maximize athletes’ strength and endurance.
Hatfield Group, in concert with the architects and taking into account local practices, designed a framing system comprising A992 composite steel that is supported by steel columns with concrete shear walls and steel moment frames. Cast-in-place concrete cores with a compressive strength of 6 ksi provide lateral resistance.
Making space
The roof was designed using steel joists and deck from Vulcraft, a steel products company. These joists eliminated the need for columns at many locations and enabled open spaces and clear sightlines in the atrium. A series of 30 in. deep steel-rolled shapes cantilever at the roof level to carry hangers that support the second level and remove obstacles to circulation on the ground floor.
The atrium has a two-way tapered plate girder system with depths ranging from 48 in. to 60 in. and spanning 120 ft in two directions; deep plate girders made from built-up steel plates further help support the floor below and keep the atrium interior nearly column free.
These plate girders also support the building’s iconic red canopy, which is the dramatic centerpiece of the design. The canopy’s plate girders themselves are supported by 50 ft tall steel-rolled-shaped columns. The girders narrow as they extend away from the building, creating the sense of a razor-thin edge on the cantilever as it hovers over the courtyard that fronts the facility. The cantilever shades soaring double-height glass along the building’s front facade, creating a welcoming atmosphere and leaving an unforgettable impression on team members and prospective student-athletes.
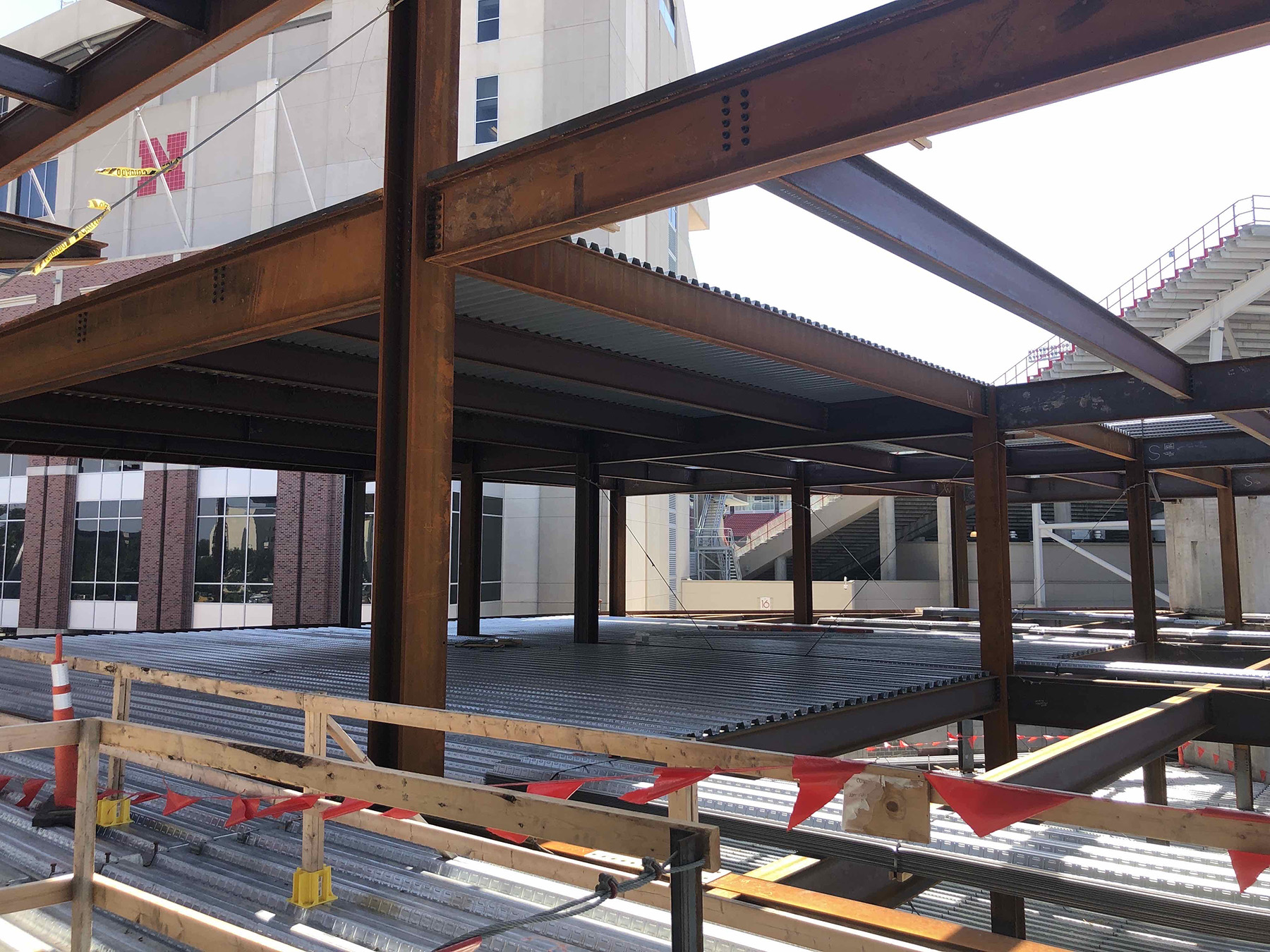
The roof design addresses another project priority: leaving the door open for a potential upward expansion. The design team needed to keep the structural framing on-grid while allowing the architectural steps to break away from it. The roofing and insulation can be removed to make way for headed studs and a concrete slab needed for an additional level.
Considering the soil composition of the site and the adjacent buildings, the design specified deep auger-cast pile foundations — mostly 18 in. in diameter — that delve an average of 80 ft below grade. Portions of Memorial Stadium’s foundations were reinforced to accommodate the new corridors and walkways between the stadium and the training facility.
Reducing size
While typical floor framing comprises W30 floor girders and W21 floor beams, the design team combined this system with composite lightweight-concrete slabs. With a self-weight of 20 psf less than standard concrete, this material not only helped reduce the dimensions of the steel floor beams, columns, and foundations, but it also offered other advantages such as reducing the necessary fireproofing and lowering the overall carbon footprint.
As perfectly as the material met the demands of the project, it did not come without its own set of complications. Composite lightweight-concrete construction is not particularly common in Nebraska. Moreover, the architectural design called for areas of polished concrete, a challenging finish to achieve with lightweight concrete, as the aggregate can chip if it is not polished with care.
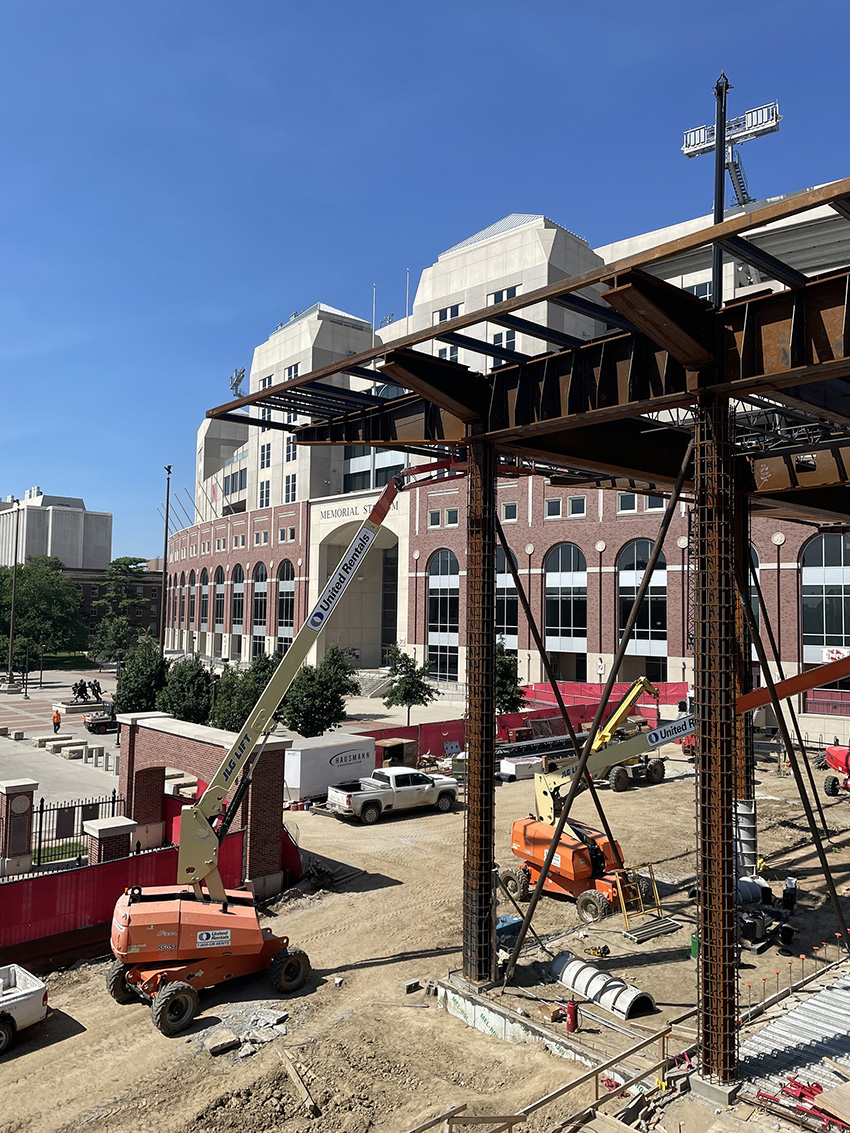
In concert with suppliers, stakeholders, contractors, and design team members, mock-ups of the polished lightweight concrete were made to test how it would hold up to polishing. The trials were successful, demonstrating that lightweight concrete could perform as well as traditional concrete and achieve a high degree of finish when polished. By using lightweight concrete, the steel tonnage could be reduced in the framing systems.
Connecting building and context
The new connections between the facility and its surroundings were complicated by the steep change in grade over the site mentioned earlier. This challenge meant the structural engineer needed to think more broadly than usual about the structural scope, looking beyond the building to the site’s new retaining walls and the layout of the new walkways and tunnels.
This holistic approach assisted in harmonizing the full-story grade difference from one side of the facility to the other. The retaining walls for the building help support the cast-in-place tunnels and site walls. Additionally, the retaining walls support outdoor pedestrian walkways that meander around the new facility and adjacent buildings, allowing access to the various buildings in the complex.
The tunnels posed another hurdle that required innovative thinking. To ensure that there was sufficient time for steel fabrication, the project team accelerated the construction document and construction administration phases, which left little time to make calculations for each connection and requiring the team to rely on standard details.
3D from day 1
The various design solutions implemented would not have been possible without an integrated project team that collaborated on a single building information model using Autodesk’s Revit and BIM 360. Using this software in the early stages of a project streamlines collaboration across the design team, and it is a more intuitive way to present ideas to clients and contractors. For example, for this project using BIM was essential to tracking updates to the architectural design and then sharing the geometry of the structures with the overall team.
In addition, to fully understand the 24 column transfers and coordinate the load paths to the ground, BIM was indispensable. The BIM models were shared with the contractor and steel fabricator, and the contractor effectively used the BIM models on-site to coordinate with its teams, as the 3D visuals of the models expedited problem-solving.
The building broke ground in spring 2021. By press time, it was being used for practice and training, with the third floor nearing completion. The new facility will hopefully usher in an era of successful football teams to make Osborne and all Nebraska natives proud.
Erleen Hatfield, P.E., S.E., M.ASCE, is the founder of and Rebecca Jones, P.E., S.E., M.ASCE, is a project principal at the Hatfield Group in New York.
Authors’ note: Erleen Hatfield, P.E., F.ASCE, is a University of Nebraska-Lincoln alumna. Both authors are Nebraska natives and were thrilled to be selected to engineer such an important project for their home state.
Project credits
Owner: University of Nebraska-Lincoln
Structural engineer: Hatfield Group, New York City
Design architect: Populous, Kansas City, Missouri
Local architect: BVH Architecture, Lincoln, Nebraska
Mechanical, electrical, and plumbing: ME Engineers, Kansas City, Missouri
General contractor: Hausmann Construction, Lincoln
Steel fabricator: Paxton & Vierling Steel Co./Owen Industries, Omaha, Nebraska
Specialized platforms: Uni-Systems Engineering, Minneapolis
This article first appeared in the November/December 2023 print issue of Civil Engineering as “Go Big.”