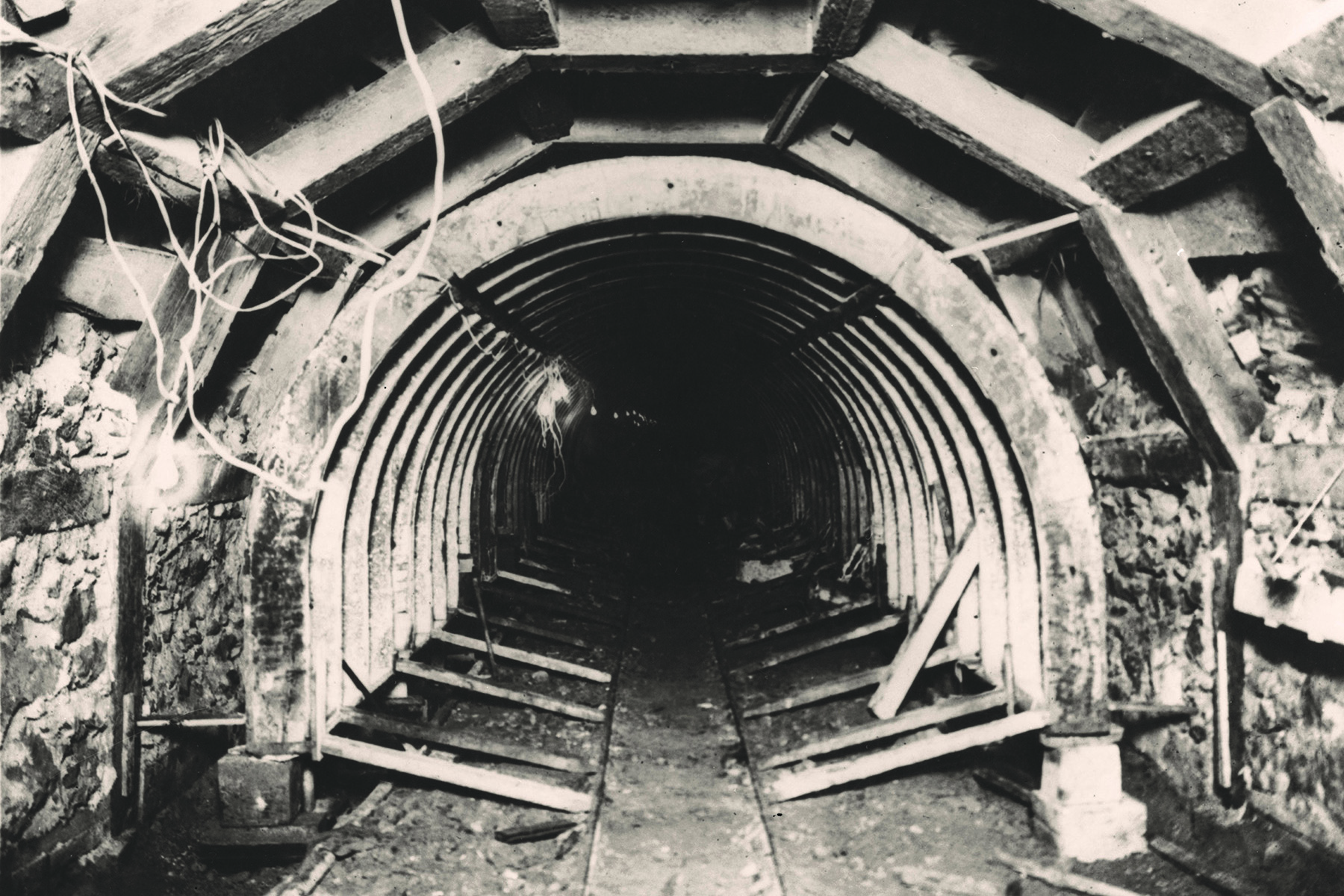
By Leslie Nemo
Workers blasted through hundreds of feet of rock using innovative technologies to construct San Francisco’s Mile Rock Tunnel — all for a project that was a tiny fraction of the city’s ongoing transformation.
The 7.9 magnitude earthquake that forced San Franciscans out of their beds the morning of April 18, 1906, kicked off an overhaul of how the city handled its water supply and wastewater collection. The changes included the Mile Rock Tunnel, a 4,233 ft long sewer and stormwater drain running under the city streets.
Originally 9 ft tall and 11 ft wide, the horseshoe-shaped conduit runs mostly north-south in a stretch of San Francisco that today skirts Sutro Heights, a park on the northwestern edge of the city. Much of what surrounds the tunnel is likely more famous, such as the scenic Lands End trail or, slightly farther away, the Golden Gate Bridge. But the Mile Rock Tunnel shows that in recovering from disaster, San Francisco was willing to try out brand-new technologies even as its citizens and civil engineers took on several ambitious projects at the same time.
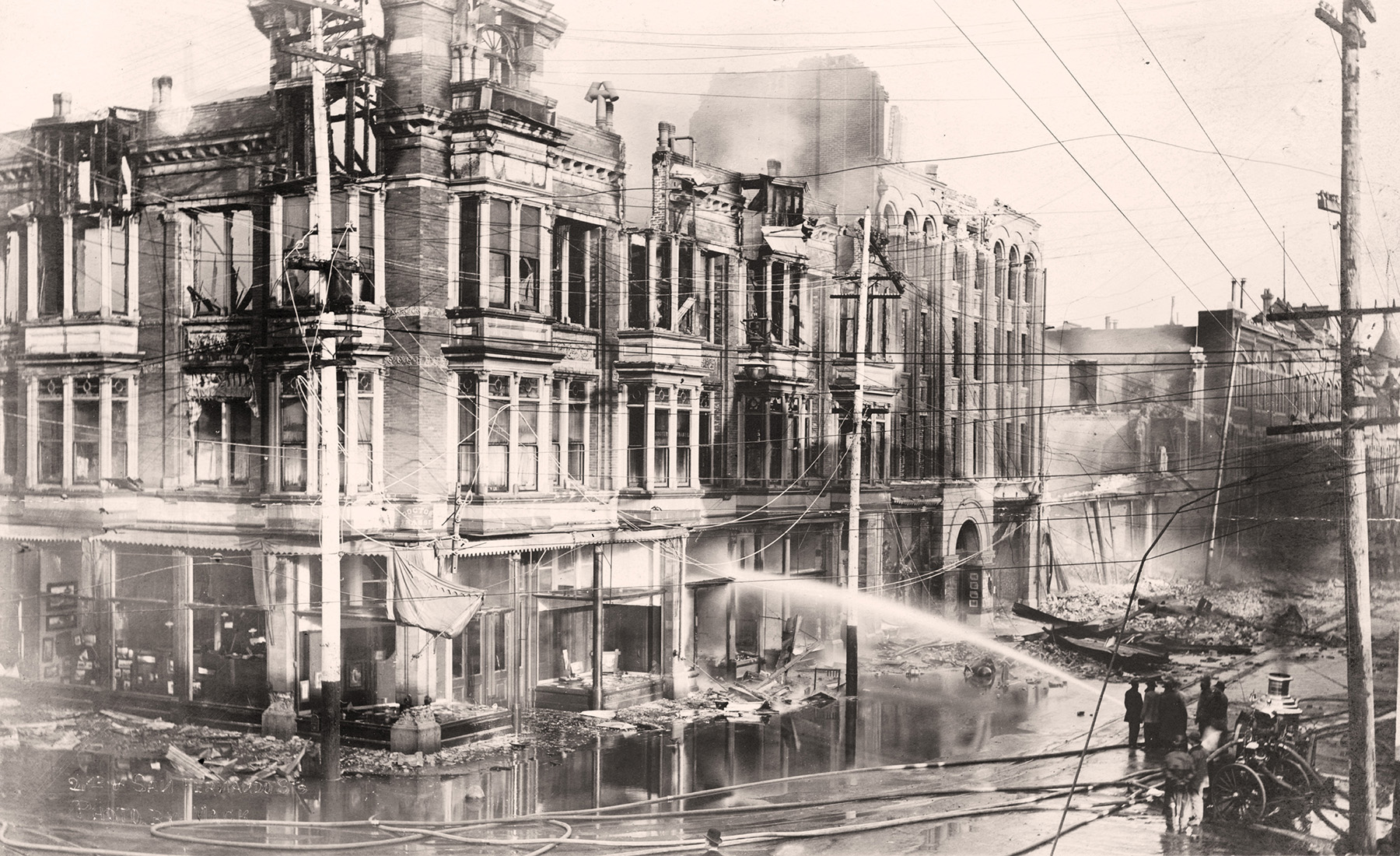
Though the devastation that San Francisco experienced in 1906 was started by an earthquake, most of the damage resulted from the four-day-long fire the tremors had triggered. When the flames were finally extinguished, roughly 4 sq mi were flattened, about 28,000 buildings were destroyed, and at least 3,000 people had died. The damage would have been more extensive had it not begun to rain. Major pipelines as well as smaller distribution lines in the San Francisco water system broke during the earthquake, draining the water supplies fire crews needed.
To protect itself from another similar disaster — and in some cases, to placate the fire concerns of the insurance industry, which ratcheted up the cost of coverage after the fires — the city took on challenging programs with a new attitude. For one, San Francisco started to fund and build an auxiliary water supply system dedicated to fire fighting. The city constructed 72 mi of pressurized cast-iron pipes, “ranging from 10 inches to 20 inches in diameter and connected to 889 hydrants,” according to Michael Maurice O’Shaughnessy, M.ASCE,* in “Rebuilding San Francisco After the Fire” (The Military Engineer, November-December, 1922, vol. 14, pages 376-380).
These pipes were designed to be earthquake-resistant. The city still uses the network today, expanding it to 135 mi of pipe. Plans are in motion to replace the cast-iron pipes in many sections of the sewer system.
Second, residents and politicians felt further justified in their pursuit of a dedicated water supply from the Hetch Hetchy Valley in the Sierra Nevada, some 240 mi from San Francisco. Though the municipality had been campaigning to build a dam on the Yosemite National Park site for years, it won the battle after the earthquake and fire, despite pushback from environmentalists and others who wanted to preserve all parts of the national park.
In addition to the water supply, the city also needed a better sewer system. Before the 1906 earthquake, “the need for a comprehensive system of sewers in San Francisco was pointed out, with increasing frequency and emphasis, by various city officials and committees,” wrote Carl E. Grunsky, M.ASCE, Pres.1924.ASCE, a former city engineer for San Francisco, in the article, “The Sewer System of San Francisco, and a Solution of the Storm-Water Flow Problem,” which appeared in a 1909 issue of ASCE’s Transactions (Paper No. 1127).
The calls for an overhaul began to be addressed officially in September 1892, when the city appointed a board of civil engineers to develop a cohesive sewer system. At the time, sewers emptied into the San Francisco Bay wherever they reached the water, according to Grunsky.
Furthermore, sewer construction had been careless, often not showing good engineering design: Grading sloped the wrong way in parts of the city, and discharge points failed to drain. “During half the year there is no rain to dilute the sewage, and it ebbs and flows,” Grunsky wrote of a particular spot in town in the Transactions paper, “creating a filthy nuisance beggaring description.”
The changes Grunsky and his colleagues dreamed of materialized by fits and starts; public funding was limited and came together as short stretches of the sewers developed. Only in May 1908 did city residents approve a sewer bond worth $4 million to fund a larger number of changes, some of which would eventually cover the Mile Rock Tunnel.
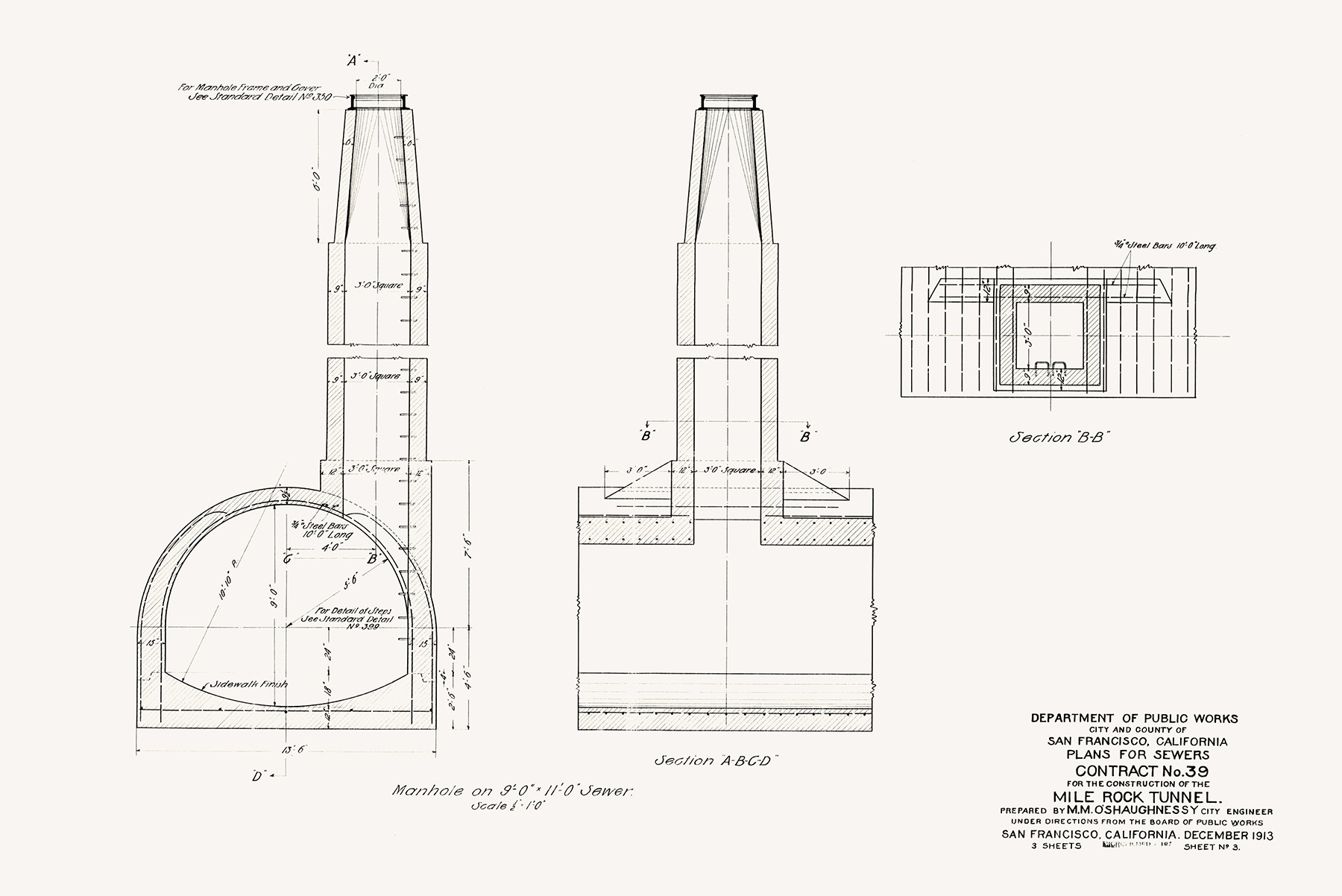
The surge of building projects meant that post-earthquake construction and design talent in San Francisco were plentiful. “The challenge of creating a new water and sewer system for the city drew a gold mine of talented engineers who came to participate in the public works projects,” wrote historian Mary L. Maniery in the February 1995 Historic American Engineering Record report aptly named “Mile Rock Tunnel.”
In 1912, Mayor “Sunny Jim” Rolph tapped O’Shaughnessy to be the city engineer. The Irish immigrant had spent most of his career in California and had recently overseen several waterworks projects. At the time that Rolph reached out with the job offer, O’Shaughnessy was running his own consulting business, earning twice as much as Rolph offered and almost four times as much as what the previous city engineer had earned.
So while the prospective income was not a draw, other factors made the job appealing, namely that the work gave his wife a chance to return to the city she grew up in and gave him an opportunity to see San Francisco through the challenge of building back after the 1906 events.
O’Shaughnessy, too, recognized that pre-earthquake San Francisco had been operating with a struggling sewer system. By the time he joined the city payroll, San Francisco was already moving through land negotiations crucial to building out the proposed Mile Rock Tunnel, which would cut through a northwestern part of town and end in an outfall into the Golden Gate strait, near a location Grunsky had suggested several years earlier.
After getting acquainted with all the public structures the city was building, O’Shaughnessy submitted his specifications for Mile Rock Tunnel to the San Francisco Board of Public Works, which were approved in January 1914. The contract went to builder Edward Malley the following month for $193,314, but the agreement quickly fell apart: Newspapers reported that Malley did not know the city would require him to take out indemnity insurance, a cost he claimed would force him to hire only unmarried men.
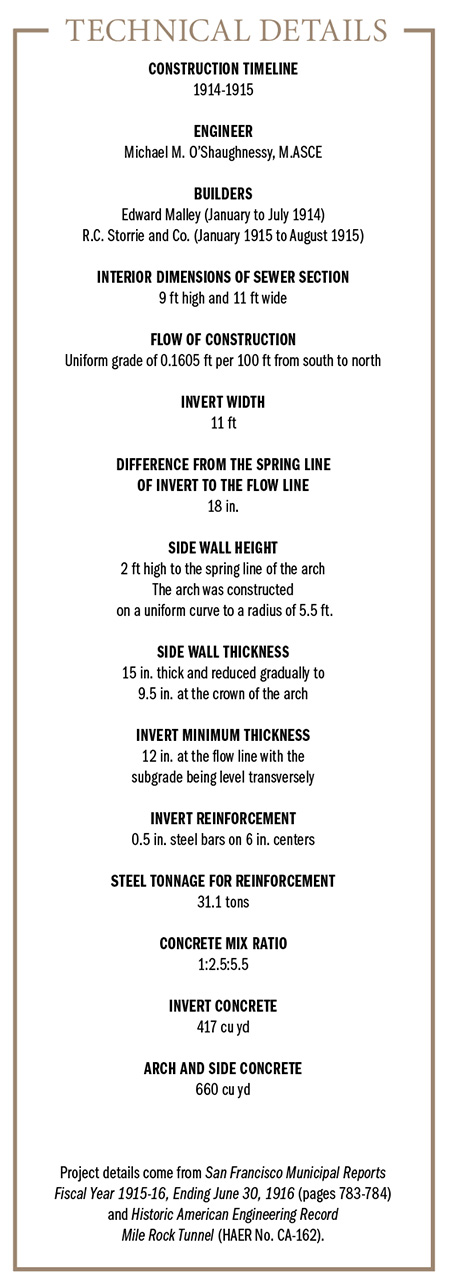
By early 1915, the contract was instead in the hands of R.C. Storrie and Co. The two Scotsmen — R.C. Storrie and Robert Muir — had completed a number of other infrastructure projects not only in San Francisco but also in various states.
The company took over after construction of the tunnel had begun with workers at both headings digging toward each other. These workers had to cut through more than 900 ft of solid rock, Maniery wrote, so the teams at both headings turned to drilling and dynamite to make progress, with slight tweaks based on the local geology they each encountered.
The team starting farther south moved through blue shale, creating eight to 11 holes using hand drills before every round of dynamite. Farther north, where workers encountered blue sandstone before reaching blue shale, 17 to 21 holes from column-mounted piston drills were needed before any explosives could blast away rock.
A side-dump car mounted on a narrow-gauge track and pulled by mules carried the muck out of the growing tunnels. In stretches without rock, approximately 2,600 ft, timber cribbing offered support.
Miners and shovelers worked in two eight-hour shifts at either end of the tunnel to make progress. The third shift of every day was for concreting, with an “average of 10 ft per day” being cleared at each end, according to “Mile Rock Tunnel for the San Francisco Sewer System” in Western Engineering (January 1915, vol. 5, pages 279-280).
The Mile Rock Tunnel was “the first successful application in San Francisco of the pneumatic mixing and placing (of) concrete using compressed air,” according to Maniery in the HAER report.
The technology was significant enough that the company that supplied the cement, Pacific Portland Cement Co. Consolidated, and the placing contractor, Pacific Concrete Placing Co., took out ads in engineering magazines based on their Mile Rock Tunnel contracts. One such ad read: “The city of San Francisco selected (Pacific Portland Cement) to do this work. You may well afford to follow their example.”
A compressor at the south end of the tunnel provided the air, while cement, sand, gravel, and water were fed into a mixer at the tunnel adit.
After two workers loaded the mixer, they turned on the compressor. When the cement and aggregate were sufficiently mixed, a valve let the material flow from a 6 in. pipe into a 6 in. rubber hose, which two other laborers could maneuver around the tunnel.
“An average of 32 batches of concrete per hour were placed when the distance from the mixer to the discharge point was as great as 2,000 feet,” wrote Maniery in the HAER report.
The mixer and hose teams communicated with each other thanks to a system of bells. “As conveying the concrete is practically instantaneous, it is in place in the forms before it has even started to set,” according to the Western Engineering article.
The final section of the tunnel, roughly 30% of the total length, required cut-and-cover construction through sand. A dragline excavator and a turntable derrick rig did the job by excavating “a trench the entire width of the street” above before workers put up lagging, according to the San Francisco Municipal Reports for the Fiscal Year 1915-16, Ending June 30, 1916, published by the San Francisco Board of Supervisors. First one set of lagging was constructed and then a second was added approximately 4 ft below subgrade. A layer of gravel at the bottom of the excavation guarded against the groundwater that kept flooding the trench, per the HAER report.
Workers also directed the groundwater to two sumps via a 10 in. underdrain, which removed 1.25 million gallons of water every day. For 35 days, about a third of the daily water removals went into another brand-new sewer the city had created.
On Aug. 26, 1915, a final inspection crew, including Rolph, O’Shaughnessy, Muir, and the president of the Board of Public Works, went for a short drive in the mile-long, dish-bottomed tunnel. A ramp had been specially built to get the car into the passage, and electric lights were hung — though the drivers had to go in reverse the entire mile back to where they started, Maniery noted. The tunnel went into operation by September, and by March 2, 1916, the only work that remained on the tunnel was the filling of a shaft and some pavement restoration, according to a letter from O’Shaughnessy to the Board of Public Works. Those details were completed by early June.

When O’Shaughnessy’s tenure as city engineer was up in 1932, the Hetch Hetchy Water Supply had dominated his time with San Francisco. Construction began in 1914, the same year as the Mile Rock Tunnel, and continued past his employment and even after his death in 1934.
The arched, concrete tunnel still stood out to the long-time city engineer years after its completion: O’Shaughnessy mentioned Mile Rock specifically in his 1922 summary of city construction for The Military Engineer, despite all the other projects he had worked on and the $9 million total the city had spent up to that point on a brand-new sewer system.
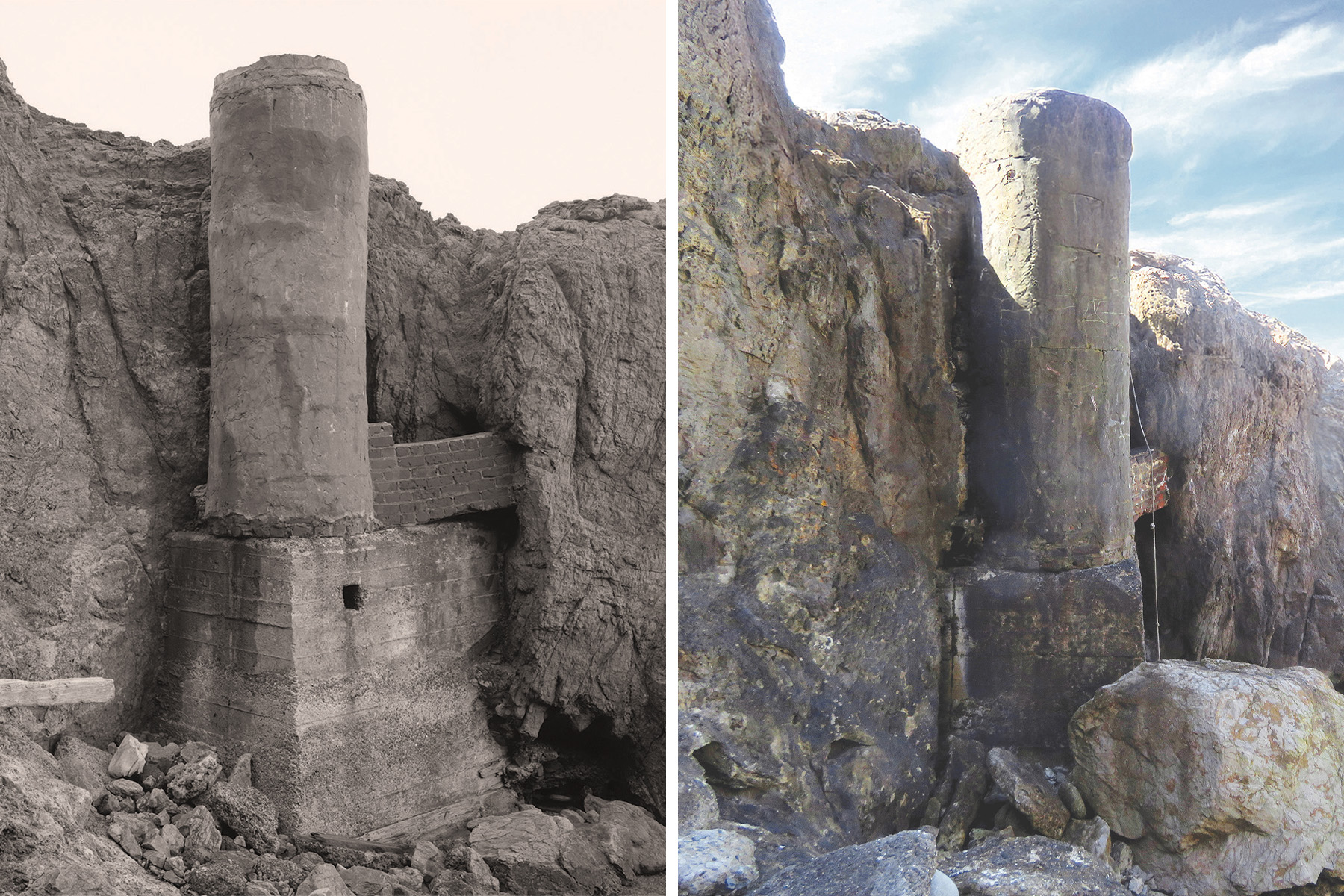
Time has changed the tunnel and its use. A weir wall was constructed in the mid-1990s that makes the tunnel only operational as an emergency overflow system. The tunnel cross-section has been reduced as the tides have brought sand into its outfall over the years. By the time the weir was added, the tunnel was only about 3 ft tall within about 110 ft from the exit.
Despite its fading utility, the sewer remains a testament to resilience and to how San Francisco civil engineers were willing to try new ideas as they overhauled its wastewater collection after the 1906 earthquake. The tunnel was innovative in its use of pneumatics for concrete placement, and it was the first in the city made with both rock boring and open-cut timber cribbing. That legacy of innovation remains, even if the tunnel no longer has an active role in making Sutro Heights a pleasant site to take in some of the city’s most famous views.
Leslie Nemo is a journalist based in Brooklyn, New York, who writes about science, culture, and the environment.
This article first appeared in the July/August 2025 issue of Civil Engineering as “A San Francisco Feat.”
*Michael M. O’Shaughnessy, M.ASCE, has been given the designation of Notable Civil Engineer by the ASCE History and Heritage Committee. “These historic civil engineers used their creativity and ingenuity to lead the way to innovative civil engineering design, serving as an inspiration for today’s practitioners,” per the ASCE website. To find out more about O’Shaughnessy and the other NCEs, visit www.asce.org/about-civil-engineering/history-and-heritage/notable-civil-engineers.