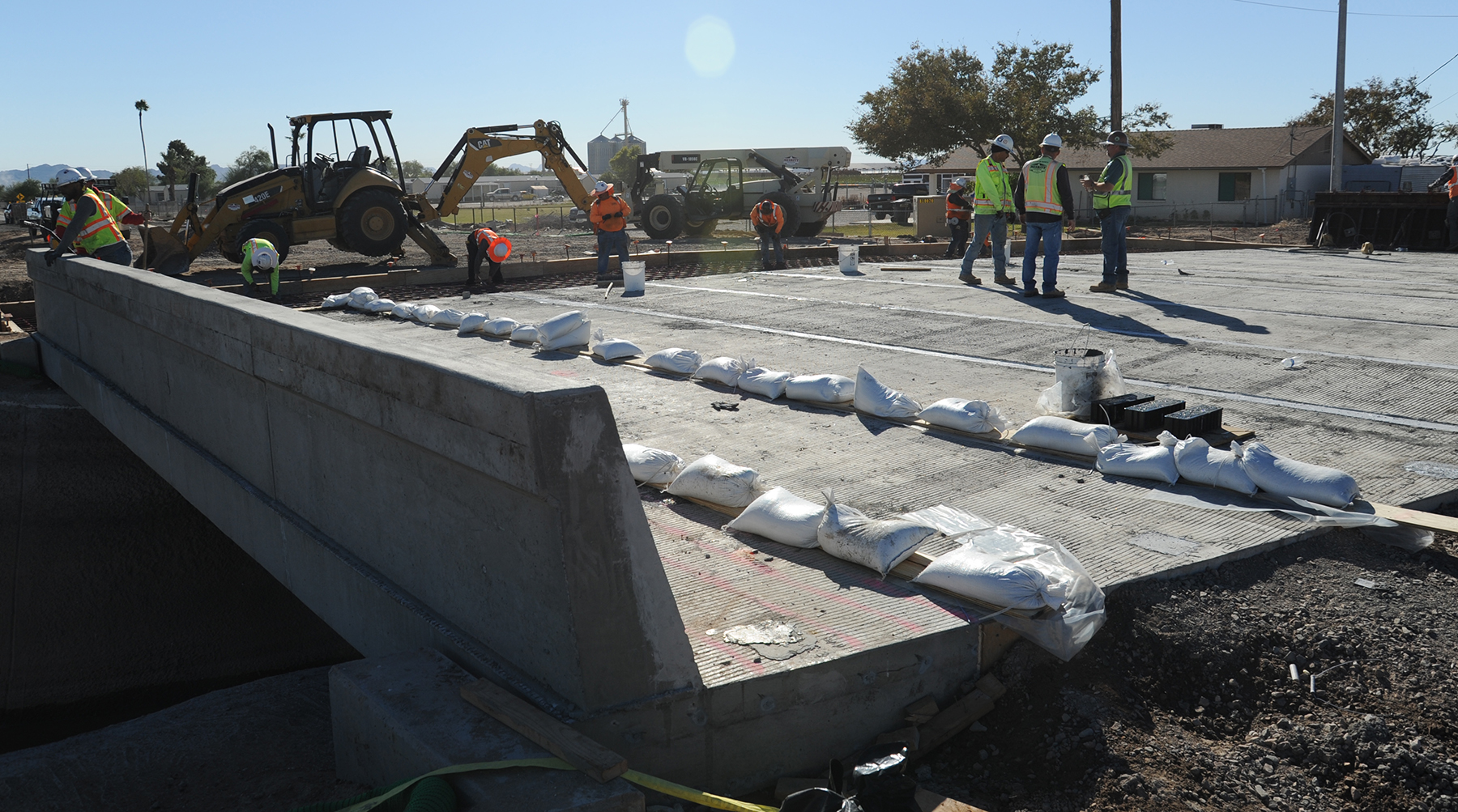
The old joke about only two seasons – winter and road construction – might become obsolete. A new collaboration between researchers at Arizona State University and the Maricopa (Arizona) County Department of Transportation has transformed bridge repair work from a weekslong endeavor to a weekend project.
The final project even came in far below the allotted budget.
Further reading:
- How well does concrete-filled steel deck flooring perform under pressure?
- Fiber-reinforced concrete cuts time, cost on light-rail project
- How well do reinforced concrete structures hold up following an earthquake?
The key ingredients to speedy, cost-effective roadway repairs? A nonproprietary, ultra-high-performance concrete; thorough training and testing; and a willingness to try something new.
The benefits of UHPC
The well-established, long-lived nature of concrete has made it the go-to building material for millennia. Each year, more than 30 billion metric tons of the slurry is used worldwide. And it’s no wonder that concrete is so ubiquitous: The simple recipe requires some raw rocks, cement, and a good mix with water.
“There is nothing as simple as this and as novel as this,” said Barzin Mobasher, Ph.D., P.E., M.ASCE, a civil engineering professor at Arizona State University. “There is only one problem: Concrete is brittle.”
To strengthen concrete against tensional forces, rebar has been the traditional solution. Adding this steel support is important, but it also raises the cost and labor of projects. Mobasher noted that the 30 billion metric tons of concrete used every year also contains about 500 million metric tons of steel rebar.
UHPC can solve several issues with traditional concrete-rebar construction. Instead of steel supports, UHPC uses fibers to strengthen the material. “The idea of fiber reinforcement is that I can redistribute that same amount of rebar in terms of smaller fibers,” Mobasher said.
These fibers can be made from a number of materials – carbon steel or polypropylene – and are about the thickness of a human hair. He noted that this technology has been around for about 40 years, but buying UHPC usually meant buying through a company.
“The cost would go up tremendously because everything is proprietary,” Mobasher said.
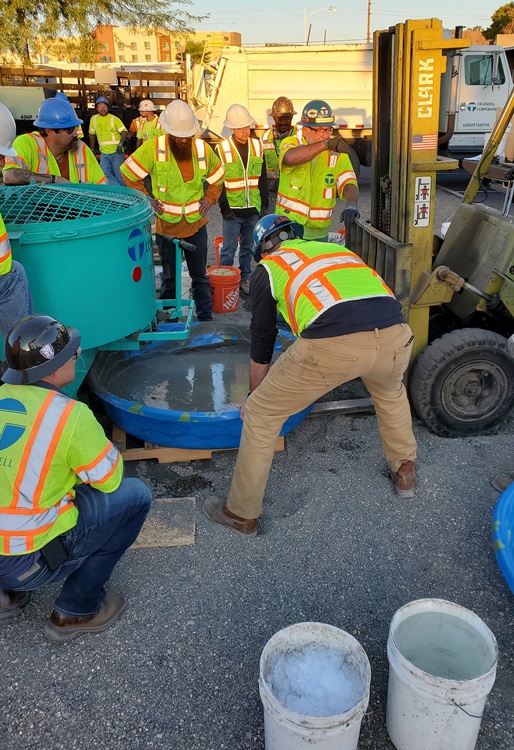
Mobasher and his colleagues at ASU developed their own fiber-reinforced concrete from locally sourced materials. “There are no proprietary rights. Nobody can claim it; anybody can use it,” he noted.
ASU worked with the Arizona Department of Transportation to develop a UHPC that could be used in state- and county-wide infrastructure projects. It was first put to use in a light rail extension project. The team used its FRC on a 1.6-mile stretch on the Northwest Extension Phase II project, cutting construction time in half and slashing the installation costs from an estimated $17 million per mile to $5.3 million. The project was nominated for Engineering News-Record’s 2024 Project of the Year.
Collaborations bloom
Seeing the success of the light rail project, Jimmy Camp, P.E., M.ASCE, a bridge engineering manager at MCDOT, thought UHPC would be a good option for the many bridge repairs in Maricopa County. He and Mobasher talked about the possibilities, and a partnership was formed.
While costs and durability are crucial factors in bridge repairs, repair times also can be extremely important. In rural areas, closing bridges can mean hassles for nearby residents; commuters may have to drive long distances while a bridge is closed for repairs. Mobasher said using UHPC instead of rebar and concrete can shorten repair times from weeks to days.
MCDOT staffers were excited about the possibilities, but they also knew that changing from tried-and-true methods to a new material might cause some workers to balk.
As part of their collaboration, ASU researchers had regular meetings and trainings with MCDOT personnel and contractors on the properties of the FRC, including its strange consistency and unique pouring behavior.
“There are people who’ve done concrete for 30, 40 years, and they would look at the mix design, shake their head, and say, ‘No way,’” Mobasher said. The mixture is stiff and dry, but after about 25 minutes, it suddenly becomes a molasses-like fluid.
Efficiency and cost savings
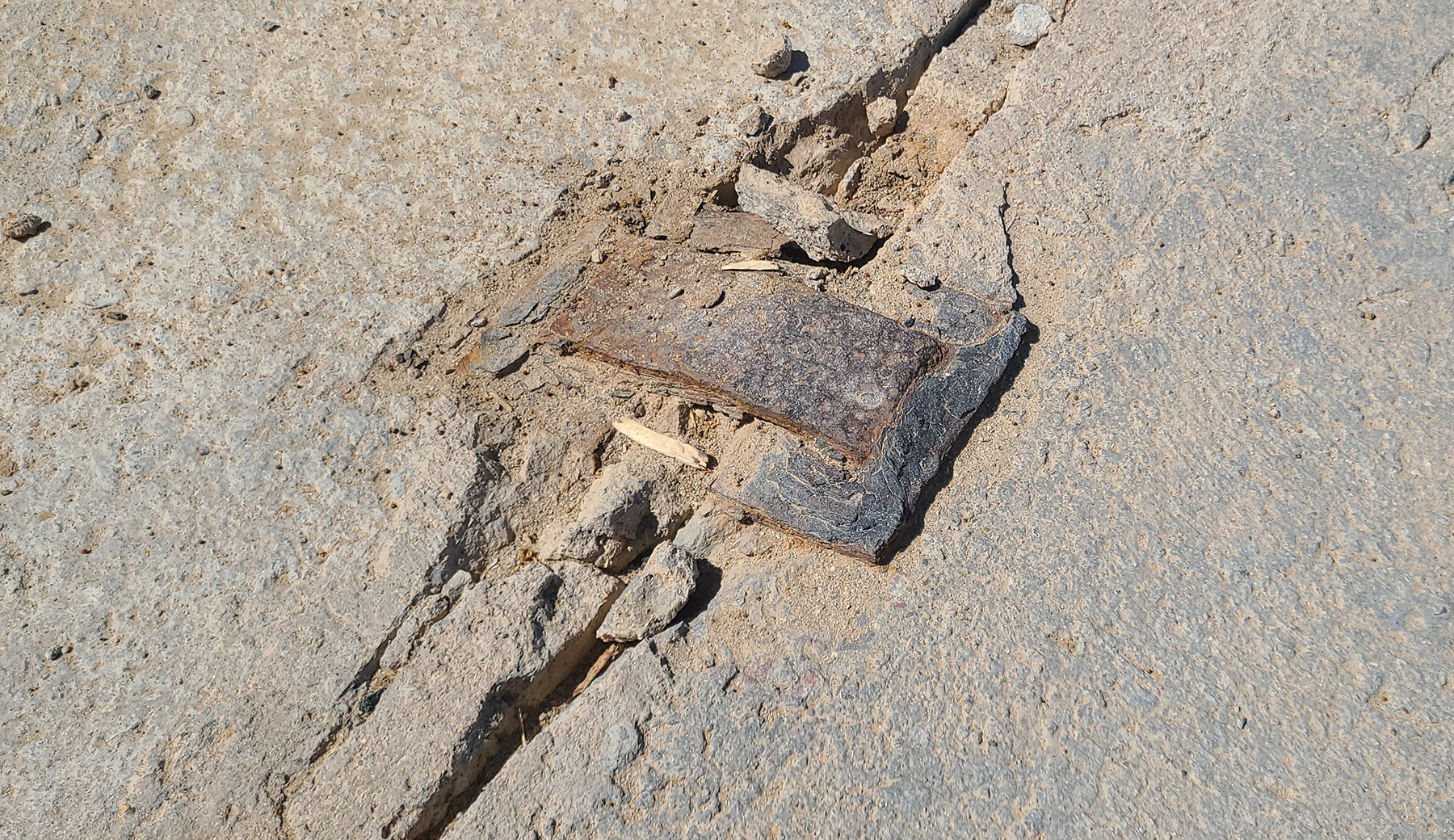
The bridges in Maricopa County are often premade slabs essentially glued together with cement grout, rebar, and key joints. Camp noted that the grout and key joints have a lifespan of about 15-20 years before they start deteriorating. And these grout connections do some heavy lifting for bridges.
“The grout key is supposed to help transfer load from one slab to the adjacent slab to help carry the load,” he explained. “When the grout goes bad, the slab has to carry all the load by itself. By putting these UHPC keys back in there, we can get the structure back to where it acts as a unit instead of a bunch of individual slabs.”
Deteriorating grout and key joints can also create pathways for water to seep in, said Camp. The water can percolate under the premade slabs and corrode strands or come in contact with the rebar in traditional concrete. With UHPC, the grout connections are watertight and longer-lasting.
Mobasher agrees, noting that the fibers are distributed throughout the concrete, strengthening it and making it difficult for small cracks to grow. He said that concrete will always have cracks, but with UHPC, “those fibers are now bridging it like staples. They're holding the cracks together and still carrying the load.”
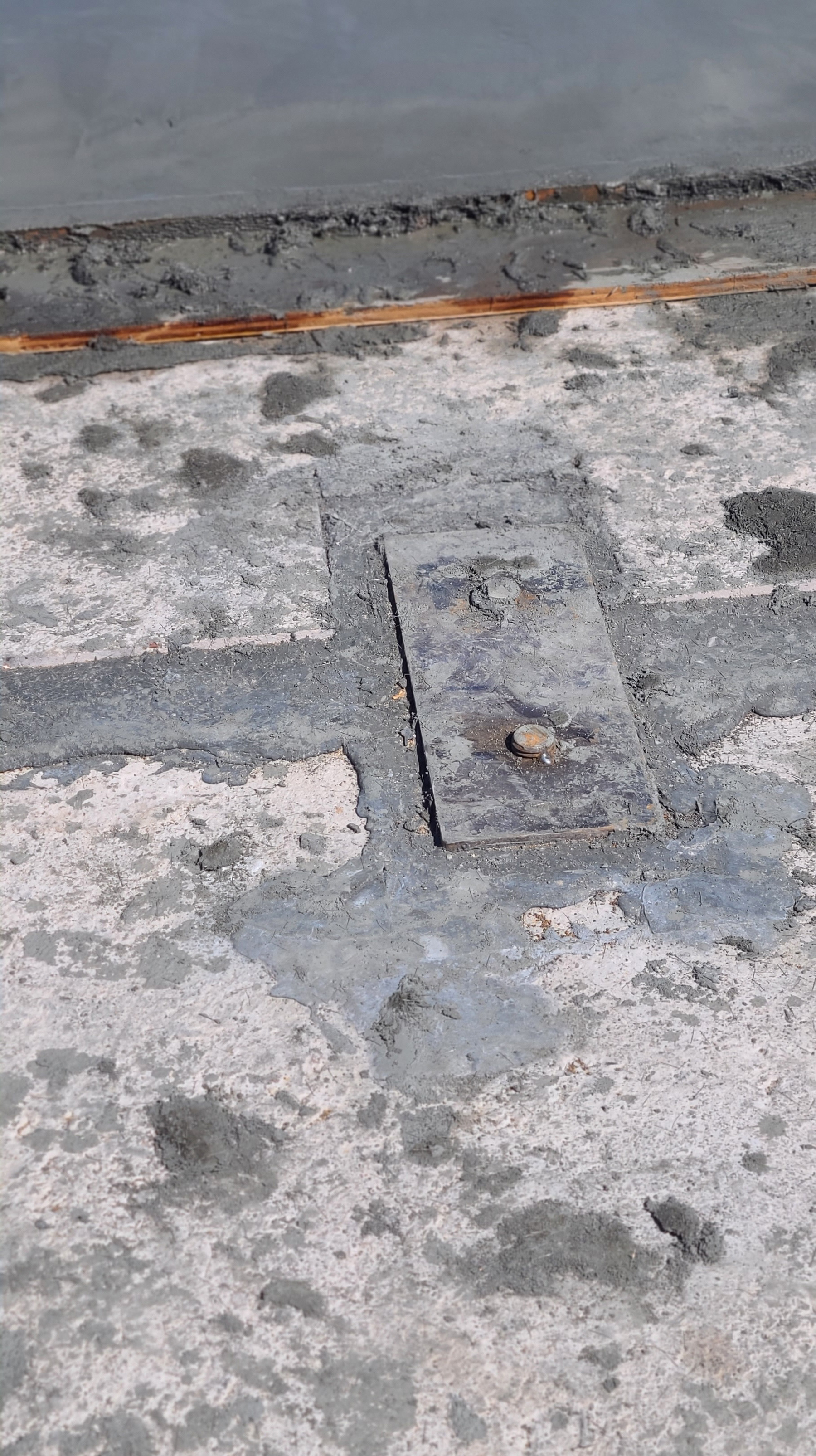
Like the light rail project, the bridge repairs were very cost-effective and fast. Originally, repairs using proprietary material was budgeted for $120,000. But Mobasher said that using ASU’s UHPC can stretch that same budget to repair around 10 bridges. The repairs were also done in a blink, with the bridge operational five days after placing the concrete.
The success of these projects is clear to everyone involved.
“I think it’s important when agencies and universities work together that they get some of the key players involved, meet often, and try to help each other,” Camp said. “It is a very collaborative effort that needs to take place; otherwise, it's just not going to happen with some of these newer technologies.”