Built in 1903 at the corner of Third and Mission streets in what is now San Francisco’s South of Market neighborhood, the 10-story Aronson Building has certainly earned its longevity: It survived the devastating April 18, 1906, San Francisco earthquake and subsequent fires, which destroyed 500 city blocks, killed an estimated 3,000 people, and left half the city’s population of 400,000 without homes.
The Aronson survived largely because of its construction with a flat slab system that is known as the Roebling System B. This system consists of fire-resistant concrete slab floors supported by steel columns. For fireproofing, the interior steel columns are encased in concrete and the exterior columns are embedded in the exterior masonry walls, which are a combination of hollow clay tile and brick, according to architecture and preservation firm Page & Turnbull.
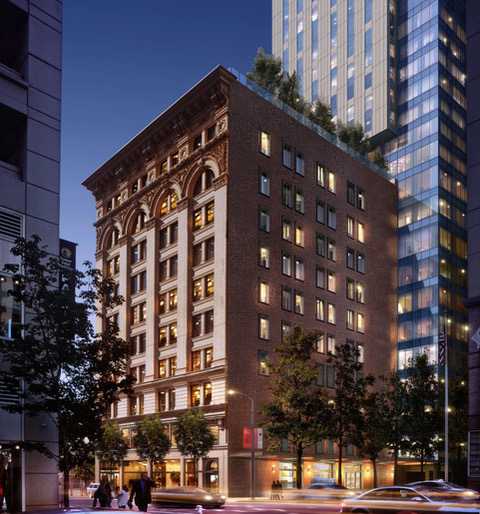
In 2016, developer Millennium Partners began construction on an ambitious, $398 million mixed-used project, the Four Seasons Private Residences at 706 Mission, to deliver 146 high-end luxury residences. These housing units are in a restored Aronson and a new, adjoining 43-story, high-end condominium tower also housing the city’s long-standing Mexican Museum in its lower levels. This tower, designed by Handel Architects, finished construction in December 2020, and residents moved in soon after, though the Mexican Museum is still building out its space and has yet to take occupancy. (Millennium ultimately sold the project to Westbrook Partners; its subsidiary, 706 Mission Street Co. LLC, is the legal owner of the site.)
Seismic upgrades
To make the whole project work, the Aronson had to be rehabilitated and upgraded to current seismic standards. Seattle-based civil and structural engineering firm Magnusson Klemencic Associates faced two options for improving the historical building’s underlying structure: Use the new tower to brace the existing building or keep the buildings structurally separate.
There were technical benefits to keeping them structurally separate even though they would be linked at each level for circulation purposes. "You're not mixing a brand-new system with a historic(al) building," says Peter W. Somers, P.E., S.E. a principal at MKA. Somers managed the structural design of the Aronson renovation and seismic upgrade.
However, there were downsides. Having to add concrete shear walls, steel bracing, or other lateral elements within the interior of the Aaronson to seismically strengthen it would have taken up valuable floor space, he says. And the joint needed between the two buildings to allow each to move independently would have needed to be 2.5 ft to 3 ft at the roof. "It's very hard to design a joint that's that wide. It would look messy from the outside as well as (in) its interior layouts and finishes, (and) it's hard to detail for waterproofing,” Somers says.
So MKA abandoned this approach in favor of structurally connecting the Aronson to the new tower.
The new tower is primarily a post-tensioned concrete structural system supported by perimeter concrete columns and an interior core. The building uses concrete-filled metal decks at the lower museum levels for flexibility. The circulation core provides resistance to seismic and wind forces in east-west and north-south directions.
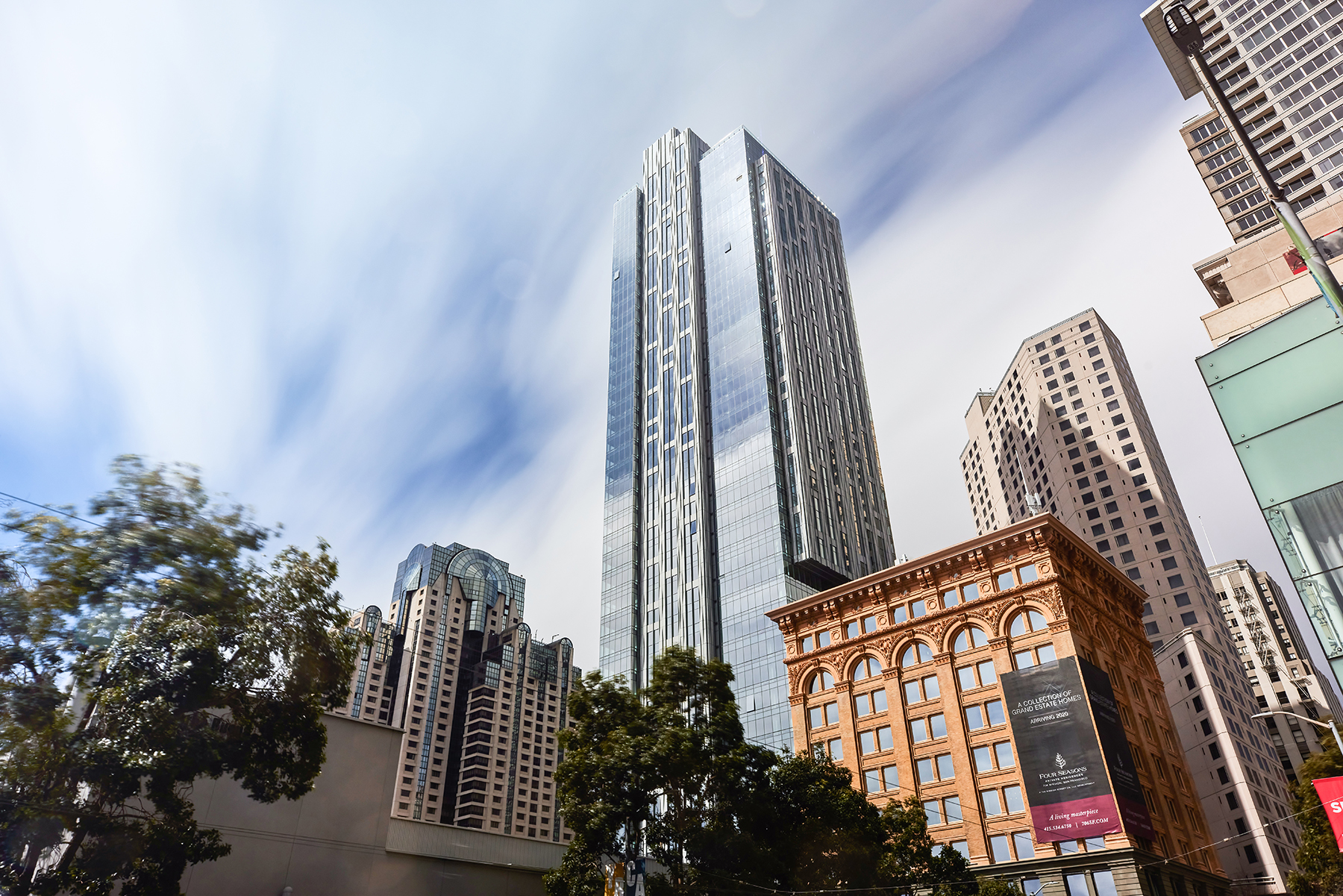
The Aronson is connected to this tower in the east-west direction at each floor level. “So where the buildings are in alignment, the Aronson forces are 100% resisted by the tower,” Somers says. “So we have structure that drags the Aronson lateral forces from the Aronson Building into the tower floor and into the core walls.”
Meanwhile, he adds, in the north-south direction, a portion of the Aronson has two north-south oriented concrete shear walls that are approximately 24 in. thick and 20 ft long, extending the full height of Aronson. These provide additional lateral resistance to keep the old building from “twisting off” the new one. (These walls take up less space than the shear walls that would have been required if the two buildings were braced separately).
MKA also had to brace and seismically stabilize the Aronson’s exterior walls, composed of non-load-bearing brick — these were at significant risk of falling during an earthquake. MKA used heavy gauge steel studs called strong backs, which are anchored into the walls, to stabilize the exterior.
Because the roof transfers most of the force from the Aronson to the new tower, MKA also rebuilt the entire roof level.
The Aronson has a one-story basement, but the new tower has a three-story basement — this deeper foundation potentially could have undermined the Aronson. To underpin and stabilize the existing Aronson foundation so that the deeper excavation could take place for the new tower, MKA and the building’s contractor, Webcor Builders, used shoring soldier piles and lagging. This involved boring holes and installing long steel beams spaced every 8 ft interspersed with timber lagging beams placed between these steel beams. Those vertical load-carrying piles supported the Aronson footings while the tower excavation was underway and then were integrated into the tower basement walls and foundation for vertical support in its permanent condition.
A lot of planning went into the sequence of connecting the two buildings to make sure the finished condition of the tower structure and floors would align with the existing building floor levels. To maintain compatibility between the tower and the Aronson, most of the new tower was built and allowed to experience its minor initial settlement and deflection before it was connected to the Aronson.
Connecting to the neighborhood
Aesthetically, the tower design takes its cues from the historical buildings of the neighborhood, including the art deco PacBell Building at 140 New Montgomery Street, once the tallest skyscraper in the city. "All the buildings in the Transbay Terminal area, which is about six or seven blocks away, are basically all-glass buildings,” says Glenn Rescalvo, FAIA, the partner in charge of the San Francisco office of Handel. “We really didn't feel like this area was where (we) wanted to put a full-glass building." Plus, the developer, Millennium, wanted stone — a material that hadn't been used in San Francisco to clad a building of this size in years.
The facade of the tower is composed of alternating layers of glass and stone — the latter visually ties back to the masonry of the Aronson.
Replicating original elements
Page & Turnbull was hired by Millennium in 2010 to help guide the mixed-use project through the city's rigorous entitlements process. This involved completing a historic structure report, an analysis designed to assess the physical condition of older buildings as well as their historical value to their cities.
“A historic structure report is a pretty thorough ‘photograph’ in that it takes a look at everything,” says Elisa Hernández Skaggs, AIA, an associate principal with Page & Turnbull, speaking of the Aronson. “It documents what's there, what's in good condition, what's in poor condition.”
The interior of the building, for instance, had been altered over the years as tenants adapted the spaces to their needs, and much of the historical fabric was already gone. But there were places where the Aronson could be restored, chiefly by replacing the large, non-original aluminum windows inserted into the original wood frames (which range in size but are mostly 9 ft, 6 in. high and 7 ft, 6 in. wide) with operable wood windows that are similar in appearance to the originals.
"Those were a big challenge,” says Hernández Skaggs. They're very large windows, and so their weight and scale make them really difficult to produce in a way that's easy for tenants to operate. As it turned out, the first windows Millennium had installed were, in fact, too heavy to operate, so they all had to be replaced again.”
The building’s exterior cladding, except for the ground floor, was relatively intact. The firm was fortunate to work with the original 1903 terra cotta ornament manufacturer, Lincoln, California-based Gladding McBean, which is still in business. The company was able to make molds from existing ornamental terra cotta units to create new units to replace those that were deteriorated and damaged.
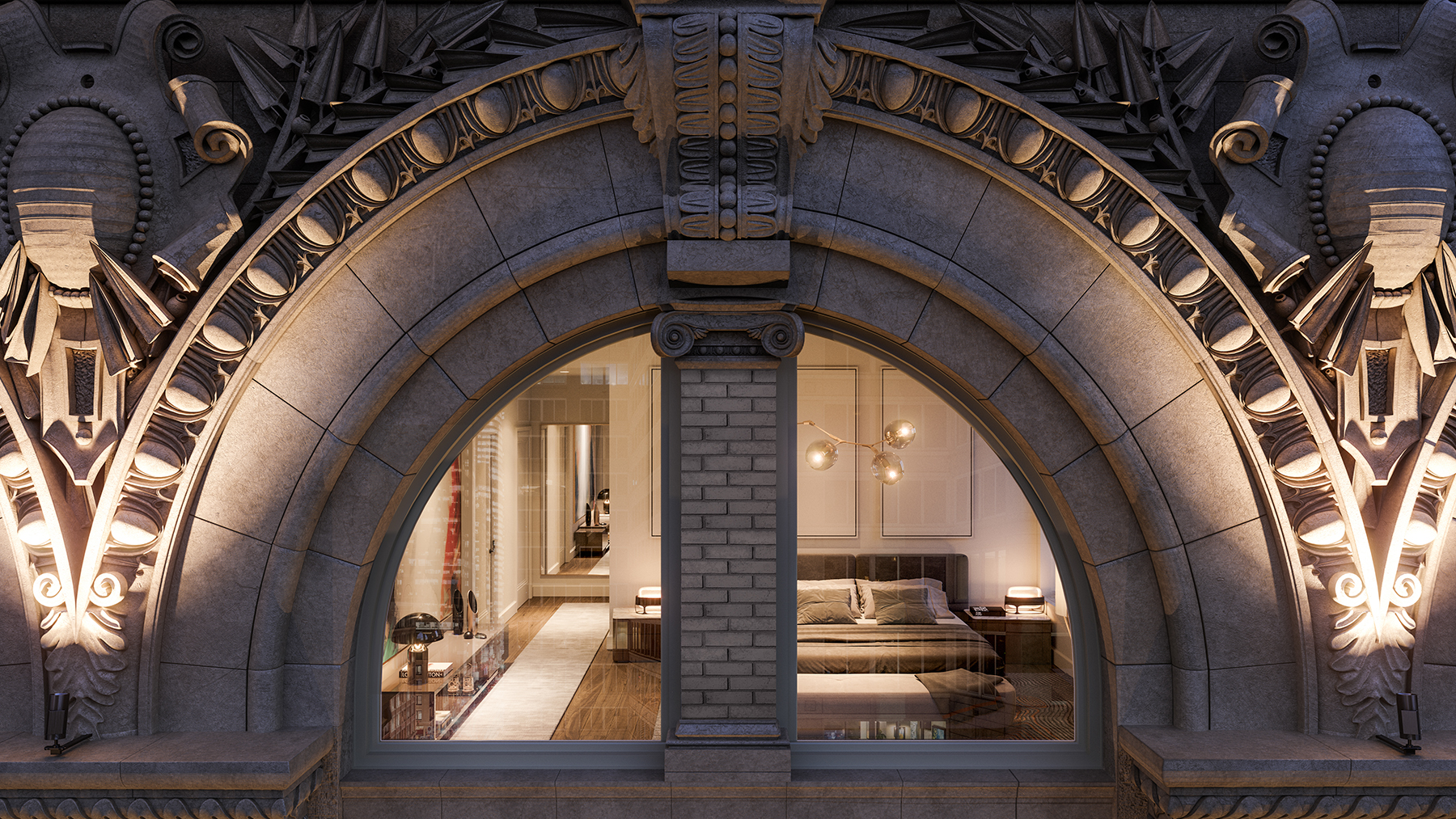
The ground floor, on the other hand, had been modernized in the 1960s and again in 1978. In the process, its retail display windows and two primary sandstone entrances were covered with brick. For the current project, the brick was removed, and Hernández Skaggs and her colleagues used a mix of sandstone patching material and cast stone replacement units to restore and reconstruct historical details around the arched entrances, guided by historical photos of the building.
“We've been able to walk away from this building knowing that we’ve added value to its historic character,” says Hernández Skaggs.