By Jay Landers
In 2022, hydropower provided 6.2% of the total utility-scale electricity generation in the United States, according to the U.S. Energy Information Administration. Among renewable energy sources, hydropower accounted for 28.6% of the utility-scale electricity generation. If the U.S. hydropower sector is to maintain, or even increase, its electricity generation capacity going forward, however, it will need to address such challenges as aging infrastructure and take advantage of opportunities to expand into existing nonpowered dams or new stream reaches. Rising material costs and continued supply chain problems complicate these efforts. One cost-effective solution, however, is to fabricate hydropower parts and provide for other operations and maintenance needs using advanced manufacturing and materials, known as AMM.
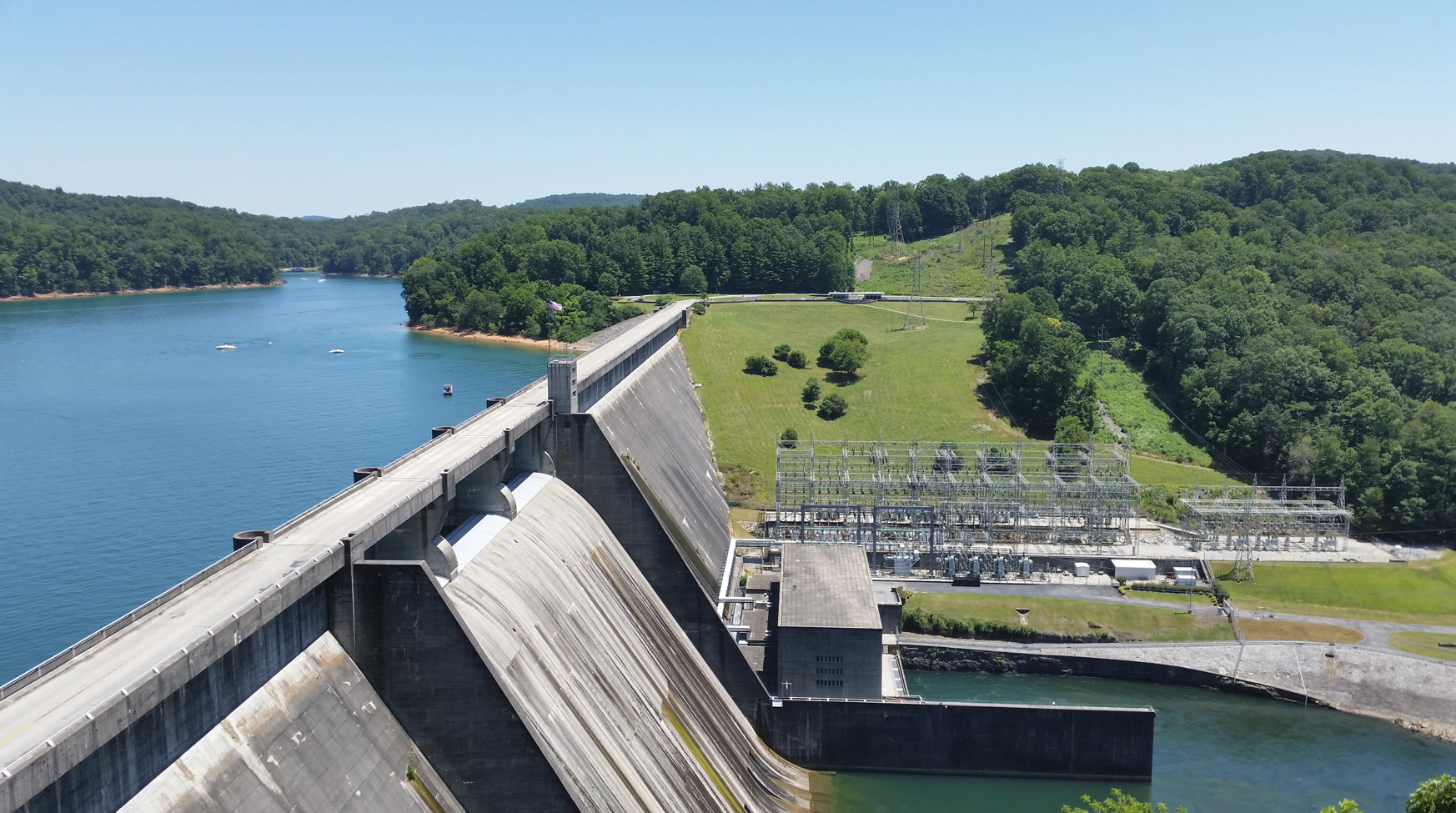
“Hydropower is critical to the transition to a zero-carbon grid,” says LeRoy Coleman, the director of communications for the National Hydropower Association. “From maintenance to capital improvements, the industry supports and embraces continuous innovation. Advanced manufacturing is one area that has the potential to increase generation efficiencies and lead to greater environmental outcomes.”
“In addition to integrating variable wind and solar, the grid reliability services that hydropower provides, and by extension the role its equipment plays in maintaining grid resiliency and sustainability, has never been more important,” Coleman adds.
Motivating factors
The Oak Ridge National Laboratory — a federal research laboratory managed by UT-Battelle LLC for the Department of Energy — examined this potential solution in a report titled Advanced Manufacturing and Materials for Hydropower: Challenges and Opportunities that it released on March 27.
The absence of cost-effective domestic manufacturing capabilities for some large hydropower components and supply chain constraints prompted the DOE to produce the report, says Colin Sasthav, Ph.D., a general engineer for the Water Power Technologies Office and an author of the report.
For example, steel castings and forgings weighing more than 10 tons that are used to produce turbine runners are “typically outsourced from other countries,” Sasthav says. This part of the turbine uses buckets or blades to capture the force of water and transfer it to the rotating shaft that powers the generator. “We wanted to come up with domestic ways of developing” those parts, Sasthav says.
Promoting growth within the small hydropower sector — that is, the sector that encompasses projects generating less than 10 MW — was another motivation for producing the report, Sasthav says.
Smaller hydropower projects are “typically more expensive per kilowatt to build” because their size means they have less opportunity for economies of scale to bring down costs, Sasthav says, adding “we need technologies to reduce costs and increase performance. Advanced manufacturing has a few ways to do that.”
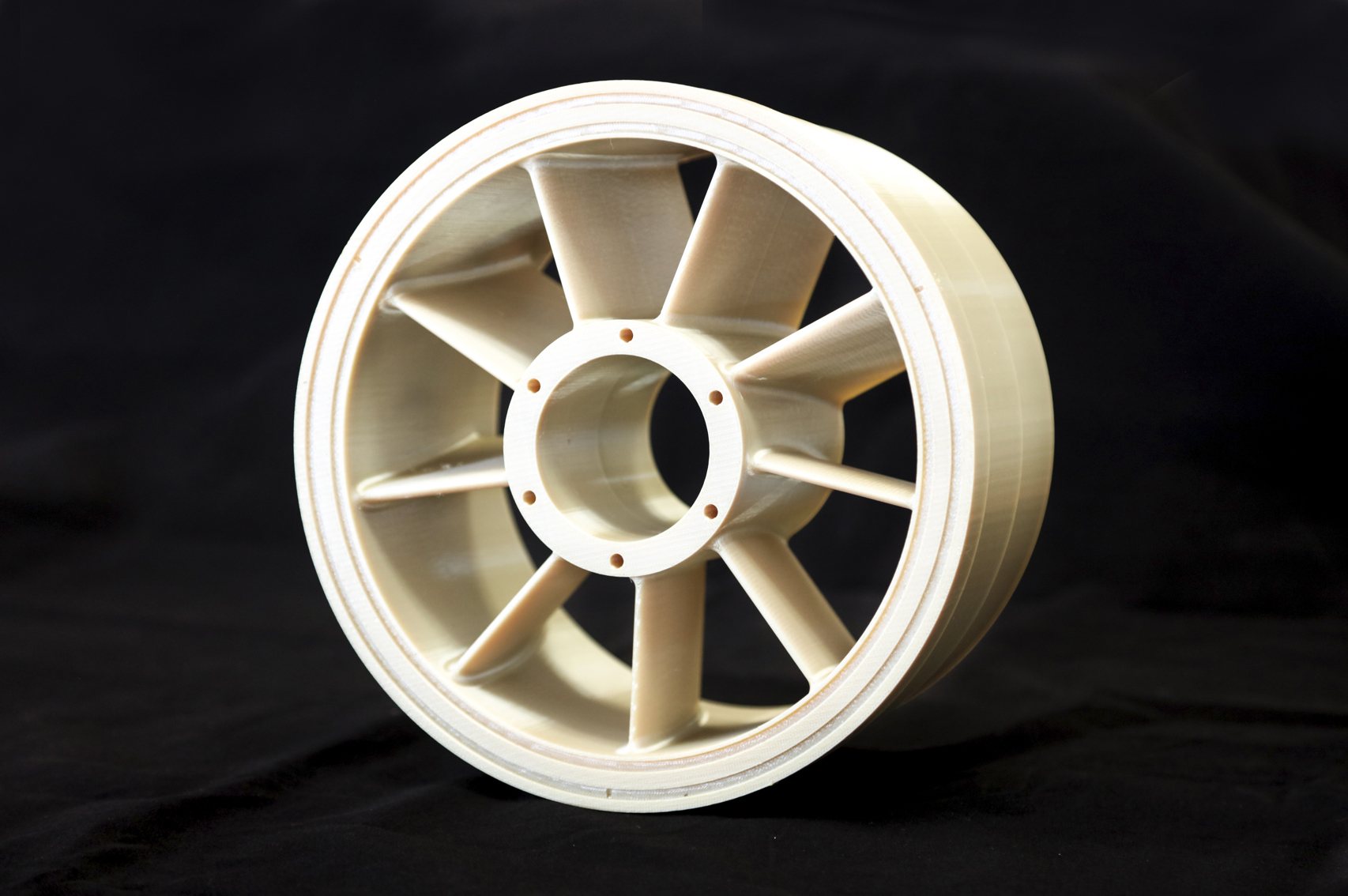
AMM could also be used to replace legacy parts for aging hydropower facilities. Dam owners “may not have the drawings needed to build some of these components or source these components if they were to break nowadays,” Sasthav says. However, scanning the part and using AMM to create a replacement could be a simpler process than having to design and procure it, he notes.
AMM applications
As for the types of AMM that potentially could benefit hydropower, the report specifically looks at additive manufacturing, novel machining and casting processes, innovative materials, and novel coating processes.
Commonly known as 3D printing, additive manufacturing involves fabricating parts layer by layer, which would make possible the “unconventional geometries and material configurations (necessary) for hydropower components,” according to the report. “Additive technologies provide many benefits, including design optimization and the ability to potentially manufacture parts on site, thus increasing accessibility to necessary parts. Embedded sensors, aeration, and cooling channels are some potential hydropower applications.”
For novel machining and casting processes, the report notes that combining “additive and subtractive techniques into a hybrid process can enable faster production and higher-quality parts by avoiding supply chain bottlenecks and reducing manual interaction.”
Using innovative materials could help produce hydropower components that cost less, achieve higher performance, or do both, according to the report. “For example, functionally graded materials could help optimize the surface and bulk properties of runners,” the report states. At the same time, “fiber-reinforced polymer composites could help reduce conveyance costs for new facilities,” according to the report.
Finally, novel coating processes “can reduce toxicity and improve durability of conventional alternatives,” the report notes.
Potential benefits
AMM approaches also offer multiple potential benefits for existing and new hydropower facilities when it comes to operations and maintenance, capital costs, system performance, and environmental compliance, according to the report.
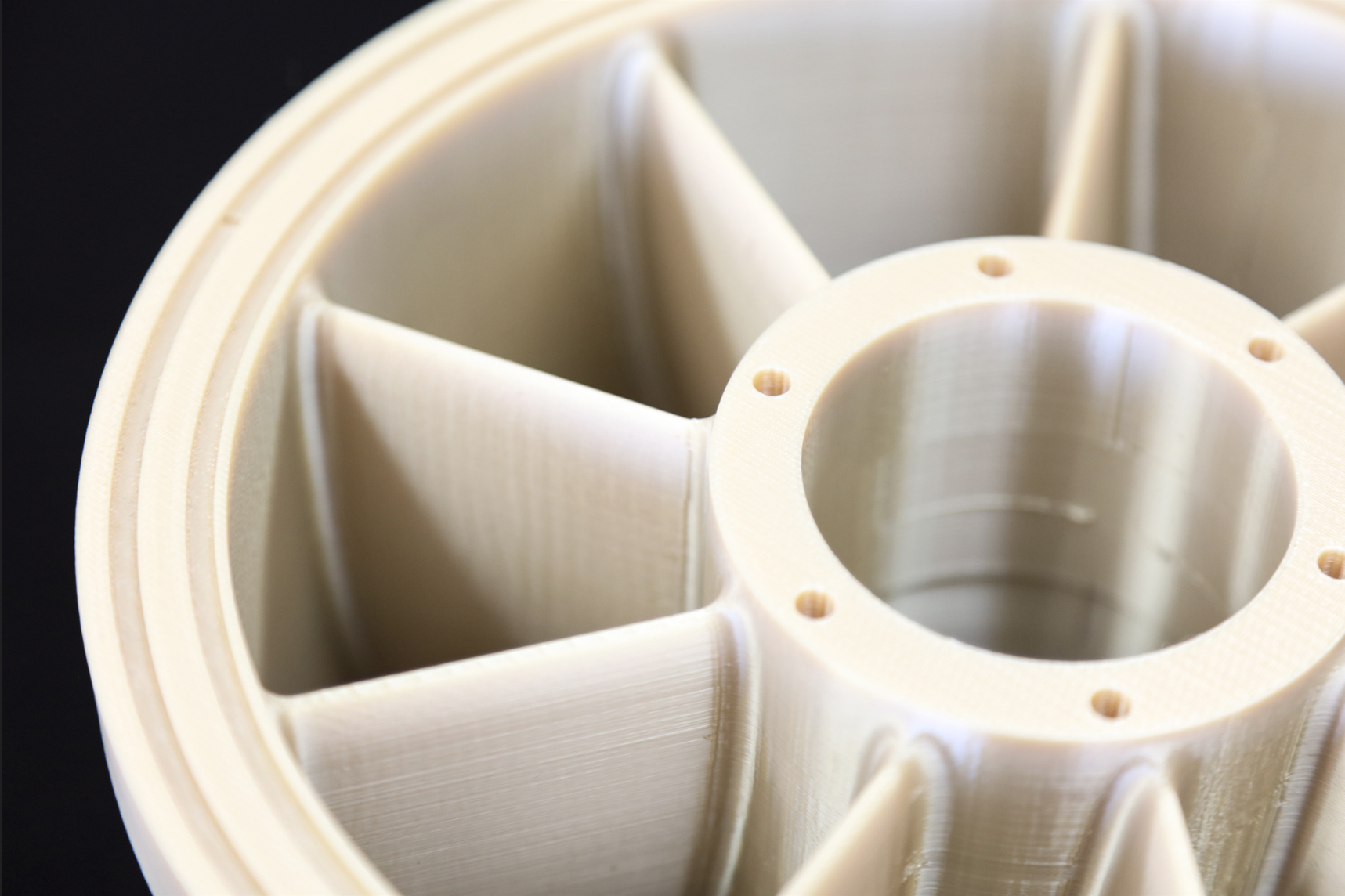
Self-healing coatings, for example, “can reduce O&M costs by expediting repair processes and eliminating certain routine maintenance practices,” the report states. “AMM technologies that increase durability and decrease component complexity can also decrease the frequency of required maintenance.”
Reductions in lead times and capital costs for components are another potential benefit. “For example, some additive and hybrid applications can reduce the number of parts required, thus eliminating assembly and shipping times,” the report notes. “Modular technologies also provide economies of scale, helping reduce the development time and cost challenges attributed to custom designs.”
AMM could also improve component or system performance. “For example, functionally graded materials allow components to have the surface properties of one material and the bulk properties of another,” according to the report. “Composite materials could improve strength/stiffness-weight ratios, allowing for lightweight parts and a lighter, more mass-efficient machine.”
Compliance with certain environmental requirements also might become simpler and less costly as a result of AMM. “Additive and hybrid manufacturing methods could reduce the cost to create complex and customizable designs for fish passageways, screens, aeration devices, and other environmental mitigation measures commonly found in hydropower plants,” the report says. “Other technologies, such as innovative biofouling-resistant coatings that prevent the growth of zebra mussels, can reduce O&M costs without the toxicity, low biodegradability, and durability challenges of traditional coatings.”
Research remains
Of course, much more work must be done before the hydropower sector can begin to reap the benefits of AMM on a broad scale. The various approaches that fall under the heading of AMM “will have to be tested before industry can do the switch,” says Mirko Musa, Ph.D., a water resources engineer and research scientist at the ORNL and the lead author of the report.
“That was one of the main motivations behind this report,” Musa says. “Identify the challenges, identify the opportunities, and potentially inspire some demonstration projects for the future, so that the industry will feel more comfortable in adopting these components made with unconventional processes.
This article is published by Civil Engineering Online.