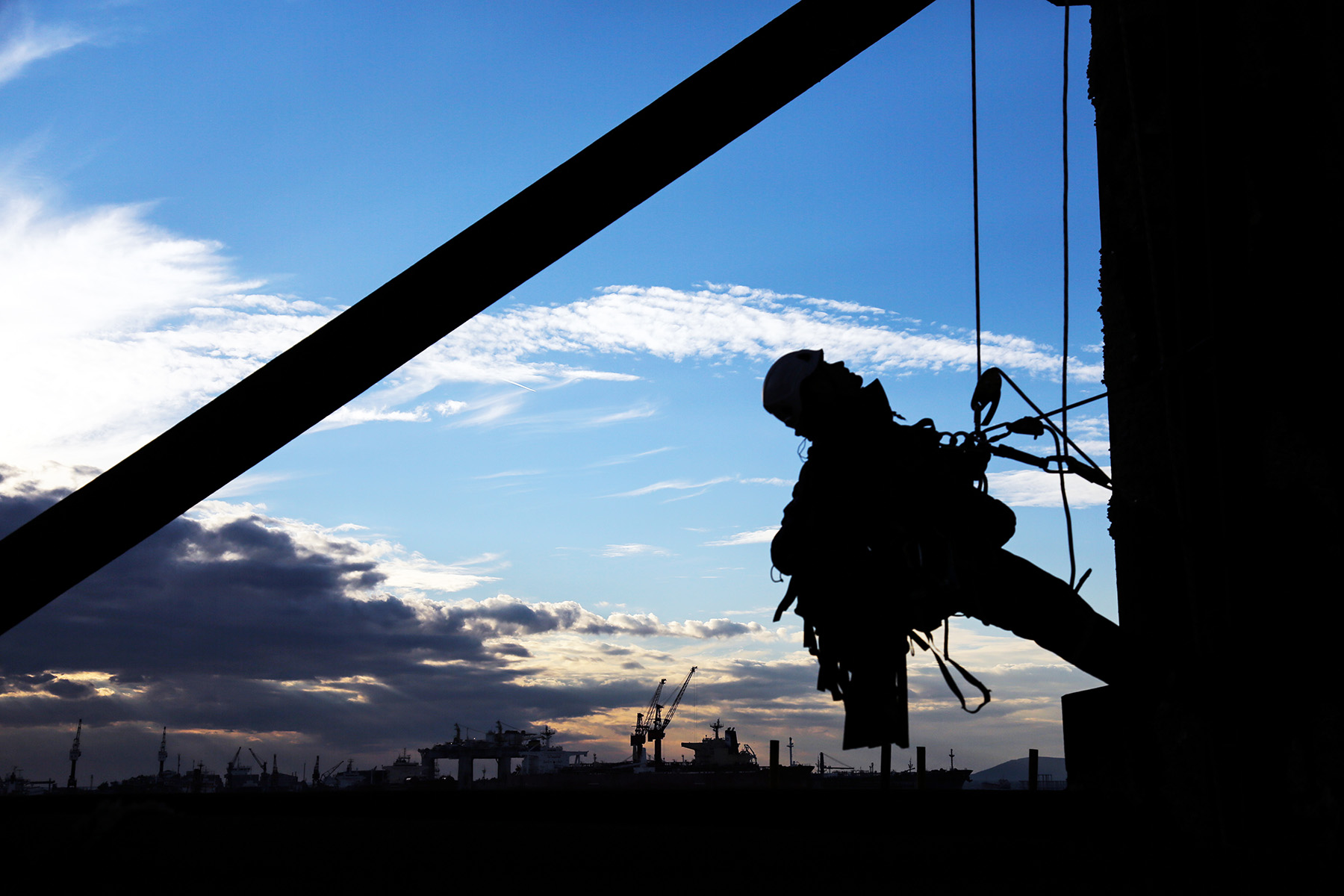
By Robert L. Reid
Civil engineers can work at a wide variety of potentially dangerous job sites and in many challenging situations. For those charged with protecting these engineers and other employees of engineering firms, the goal is always the same: Get your people home safely at the end of each day.
Last year, Civil Engineering held a roundtable discussion with various safety experts to discuss the need to add safety to the civil engineering college curriculum (read “Who needs to learn more about safety? Engineers, say roundtable panelists”). This article continues the safety discussion, focusing on what civil engineering firms are doing to protect their employees, other workers at job sites, and the public.
When civil engineers go into the field to visit construction sites, examine existing structures, investigate collapsed buildings or explore other disaster settings, or perform myriad other tasks, they face any number of workplace hazards. They might fall from a great height or be struck by moving vehicles or other heavy equipment. The ground they walk on — or in, in the case of an excavation — might be unstable.
If they are investigating a building collapse, the building might collapse further while they are inside. Or it might catch fire or explode. Or the electricity might still be on in damaged buildings or along railroad tracks, either underfoot in a third rail or overhead in a catenary system.
Even in the office — while generally less dangerous than being in the field — civil engineers and other employees of civil engineering firms face the same potential hazards that any office workers must be guarded against. These can include slips, trips, and falls; ergonomic concerns; and, as recent history demonstrated all too powerfully, exposure to a global pandemic that made keeping offices open a challenge (read “Pandemic Problems,” below).
For those charged with protecting civil engineers and other employees, the hazards vary with the situations. But the goal is always the same: to return them all safely to their homes.
Unique position
Civil engineering firms address workplace hazards through various organizational approaches. For instance, Thompson Engineering, with a staff of about 300, and Pennoni, with roughly 1,100 employees, each has a full-time director of safety and health, or someone with a similar title, who is a certified safety professional, not an engineer.
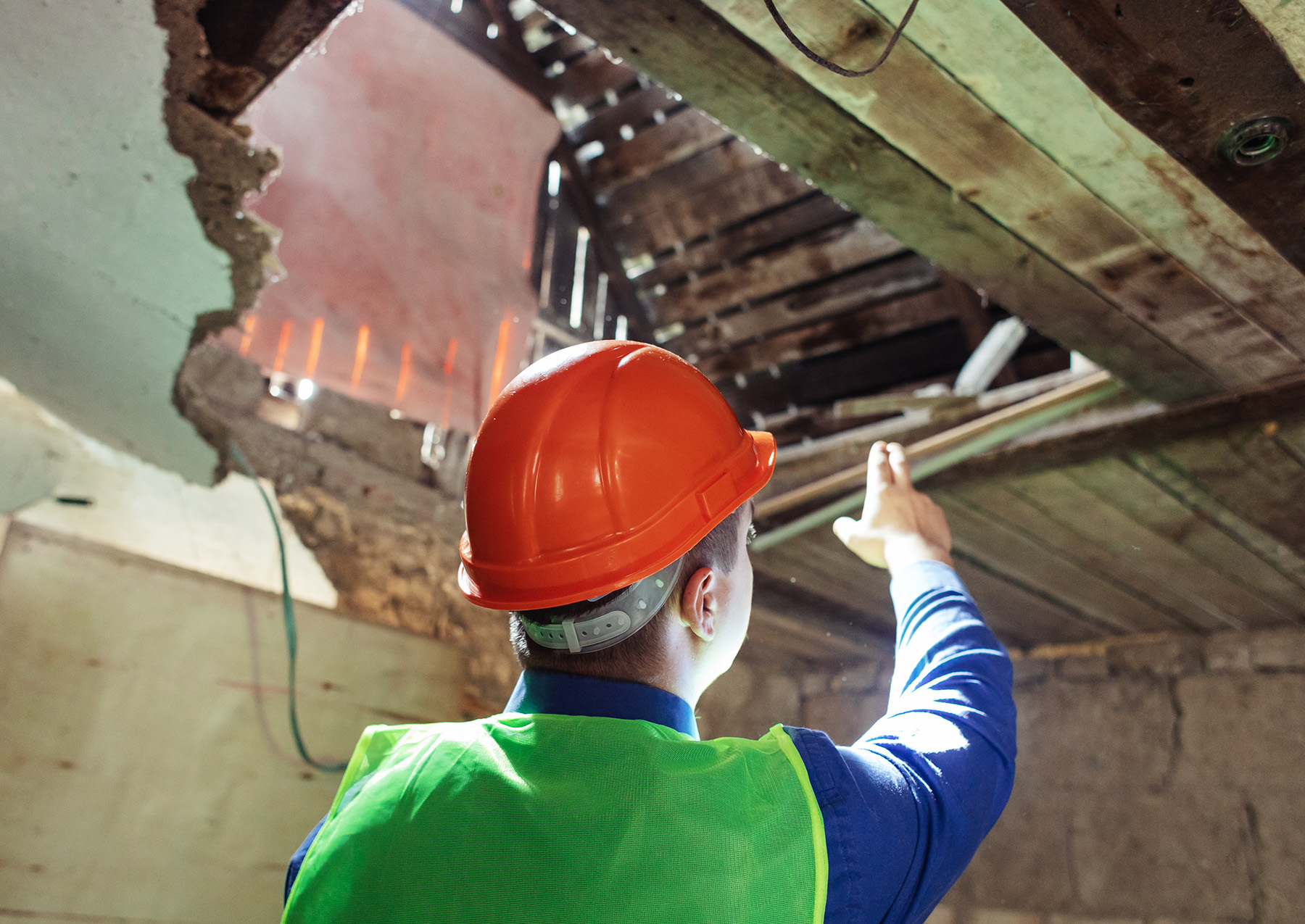
Others, ranging from Atlas Engineering, with 12 employees, to Thornton Tomasetti, which employs more than 1,500 worldwide, rely on their engineers to staff safety committees, serve as safety leaders, develop in-house safety training materials, conduct training courses, and perform other safety-related functions. Firms can also bring in outside safety consultants for specialized training.
Civil engineers are “uniquely positioned to affect the safety of others through design,” notes Kate McGee, CSP, an associate vice president at Pennoni and the firm’s director of health and safety. “However, occupational safety is rarely part of their college education.” ASCE and others are working to change that oversight, but all involved realize it will be a slow process.
A first step to keeping civil engineers safe in the field involves identifying the work-related hazards and risks, notes McGee. So prior to the start of any fieldwork, Pennoni’s engineers are required to conduct a job safety analysis that features checklists that address the specific hazards they might face. These JSA checklists include sections identifying the tasks to be performed, the hazards of each task, and the safety protocols the engineers will need to follow, including the required training and personal protective equipment — from hard hats to safety boots, gloves, or other gear, McGee explains.
The employees must sign the JSA form when completed, McGee says. “We also include emergency contact information on the form, so employees have that information readily available on a project-specific basis,” she adds.
Other engineering firms also require employees to fill out JSAs to be sure they understand workplace risks. Thompson even adds an extra letter — making the acronym JSEA — to emphasize its commitment to addressing environmental hazards, notes Mike Shumaker, CSP, the firm’s health and safety director. For example, if the firm is working with toxic materials that might result in chemical spills, “we want to make sure we protect the environment and the communities we serve,” Shumaker explains.
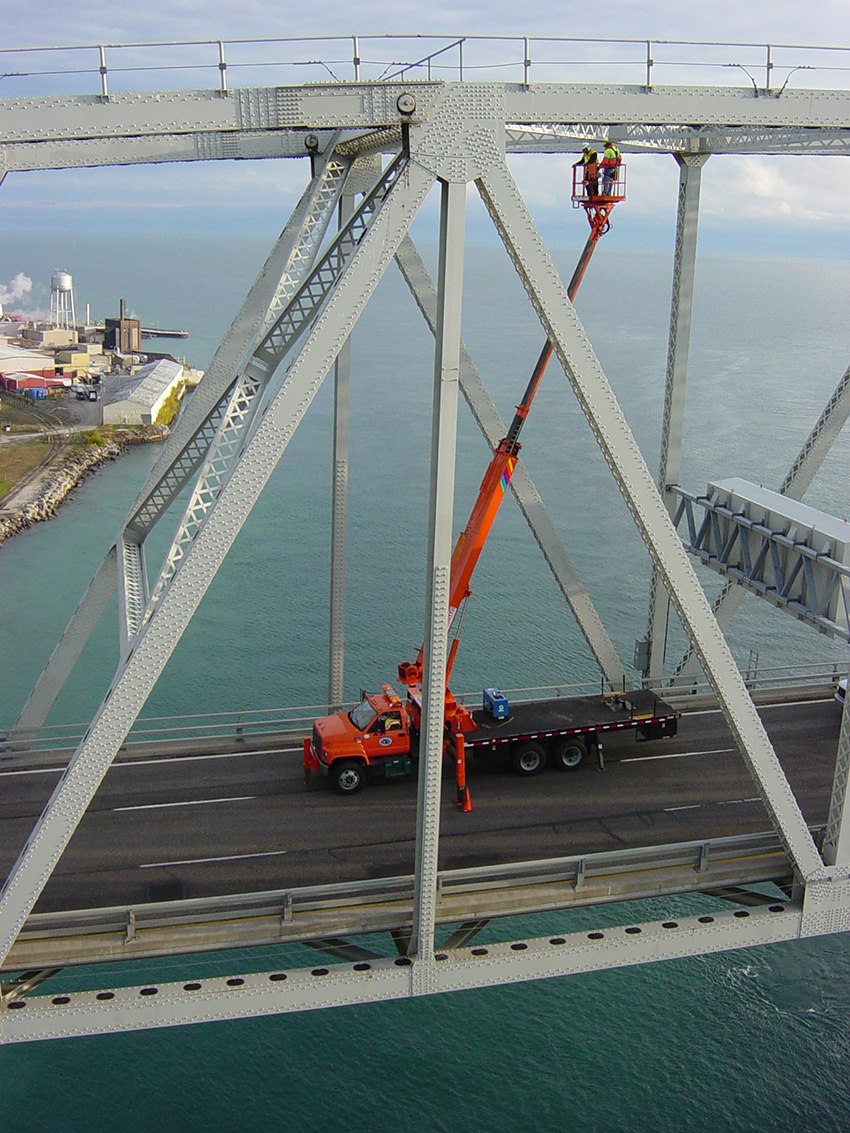
To that end, Thompson also requires employees who work in hazardous waste operations and containment to be trained and certified according to the Hazardous Waste Operations and Emergency Response guidelines known as HAZWOPER, which are produced and maintained by the Occupational Safety and Health Administration.
In addition to the JSAs that engineering firms require their employees to perform, some clients also have their own safety forms that must be filled out. “Or we might have to write a full safety plan for the specific site” to meet the client’s or site’s requirements, explains McGee.
Confronting hazards
Among the most common workplace hazards that civil engineers might confront are working at height — inspecting bridge towers or cables or the undersides of bridge decks, for instance — and working around moving vehicles or heavy equipment. Moving objects are especially dangerous at construction sites or on highways and bridges while traffic continues to flow. Working on ladders and scaffolding, working in trenches and other excavations, or entering confined spaces also pose considerable safety challenges.
Modjeski and Masters specializes in bridge inspections, especially on complex, long-span structures, says Mike Januszkiewicz, P.E., SPRAT III, the assistant director of field services in the firm’s Poughkeepsie, New York, office. Januszkiewicz coordinates Modjeski and Masters’ rope access program, which involves using a combination of ropes, straps, and safety lines, as well as various ascender and descender tools, to climb up, rappel, or slide along the structural members of a bridge or other structure being investigated (read "Telescope inspectors reach for the stars in West Virginia”).
Prior to adopting rope access, the firm relied on large aerial work platforms — some machines reaching as high as 158 ft into the air — that could require lane closures on or under bridges or even complete shutdowns of crossings. Such closures hampered traffic and posed safety hazards to inspectors. Yet this equipment did not provide access to all parts of bridges, Januszkiewicz says. Modjeski and Masters’ inspectors sometimes climbed up the outside of bridge towers or bents, which posed additional hazards while still not enabling inspectors to reach every part of structures, Januszkiewicz says.
Although rope access requires considerable training, especially in terms of safety, and potential certification by the Society of Professional Rope Access Technicians, the program allows Modjeski and Masters’ inspectors to conduct a full, hands-on inspection of every part of a bridge or other structure, even along the full length of cable stays, Januszkiewicz says. “With rope access, I can get to every square inch of a structure,” Januszkiewicz explains. “So it’s made a huge difference in our ability to get to and inspect things we probably couldn’t even look at before.”
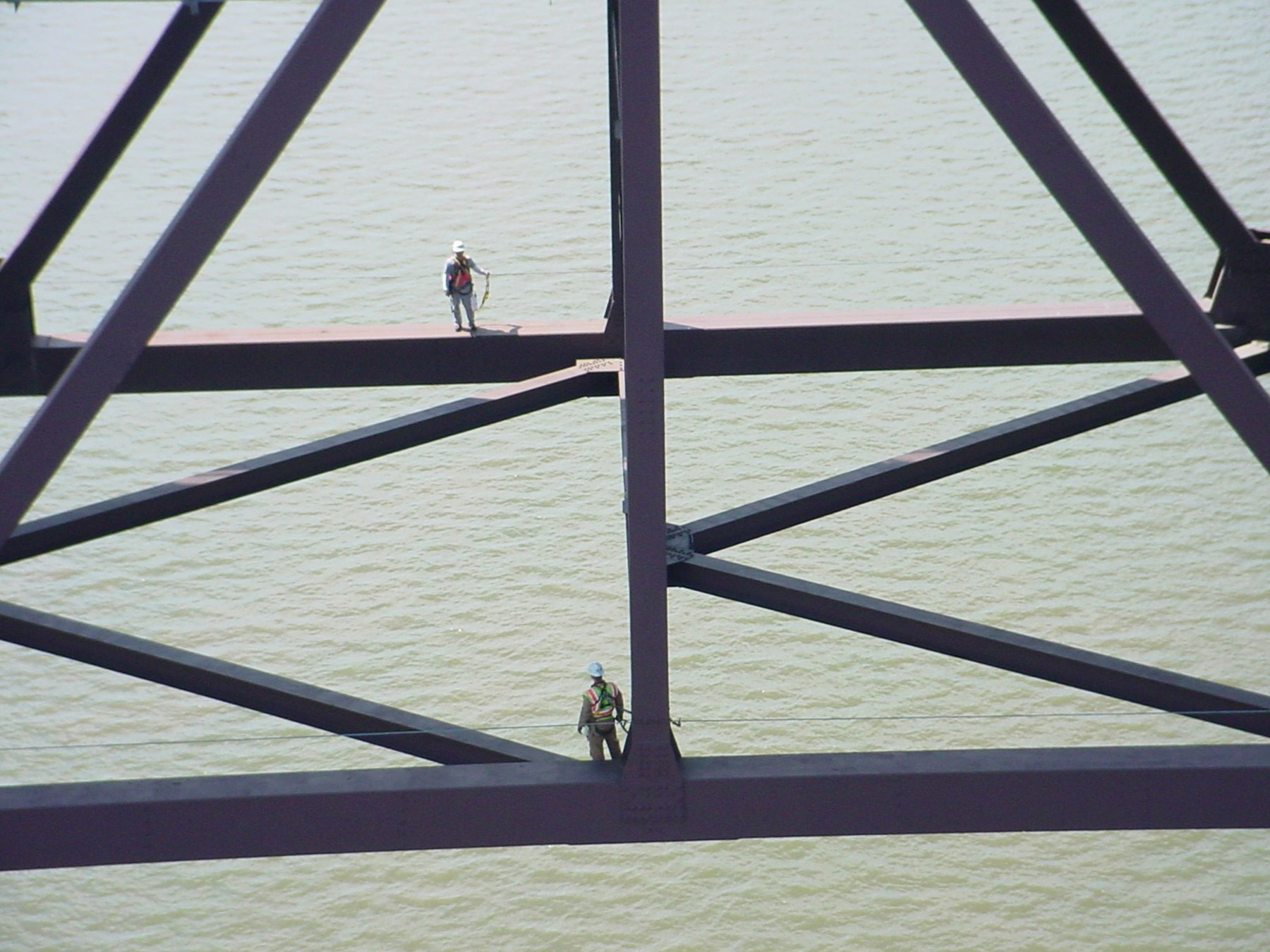
Aerial work platforms are still used in some situations, he adds, but the largest and most potentially hazardous equipment has been eliminated, and the closures can now be limited to the shoulders of bridges, leaving all lanes open to traffic. Keeping traffic in motion is actually safer for the inspectors and the public, Januszkiewicz says, because “when you close down lanes and the traffic starts getting congested, people start doing things they shouldn’t do, or sometimes they get confused — and so they might pull into a lane closure where you’ve got vehicles and people working, which is always a safety concern.”
Nighttime lane closures were often the most dangerous even though the volume of traffic was reduced, Januszkiewicz adds. That’s because a driver might think the lane is simply empty and turn into it. But because the rope access program allows inspectors to work without shutting down traffic lanes in the daytime, they can more easily get the work done without night closures.
For a recent Thompson project at Oak Ridge National Laboratory, the firm’s geotechnical team had to deal with potential exposure to silica as well as updated silica exposure rules from OSHA and the Department of Energy, says Shumaker. “So we had to develop a new program and provide training,” he explains.
These efforts included ensuring that each team member was medically qualified to wear a respirator, which involved taking a pulmonary function test, fit-testing the mask, and learning what filter systems were required as well as training on the new exposure limits — all of which required considerable coordination of people and policies before the firm could take on that task, Shumaker says.
Heading into risk
Atlas often investigates collapsed or partially collapsed structures, buildings where there have been explosions, and similar situations that are inherently unsafe. Engineers at the firm also participate in urban search and rescue teams coordinated by the Federal Emergency Management Agency (read “What it takes to serve on urban search and rescue teams”). Such work does expose the firm’s engineers to “extra risks,” concedes Tom Caldwell, P.E., M.ASCE, Atlas’ senior partner and founder, who also serves on FEMA rescue teams. But those risks are justified because of the urgent need to rescue live victims, recover human remains, or assist law enforcement investigations in collecting evidence, Caldwell says.
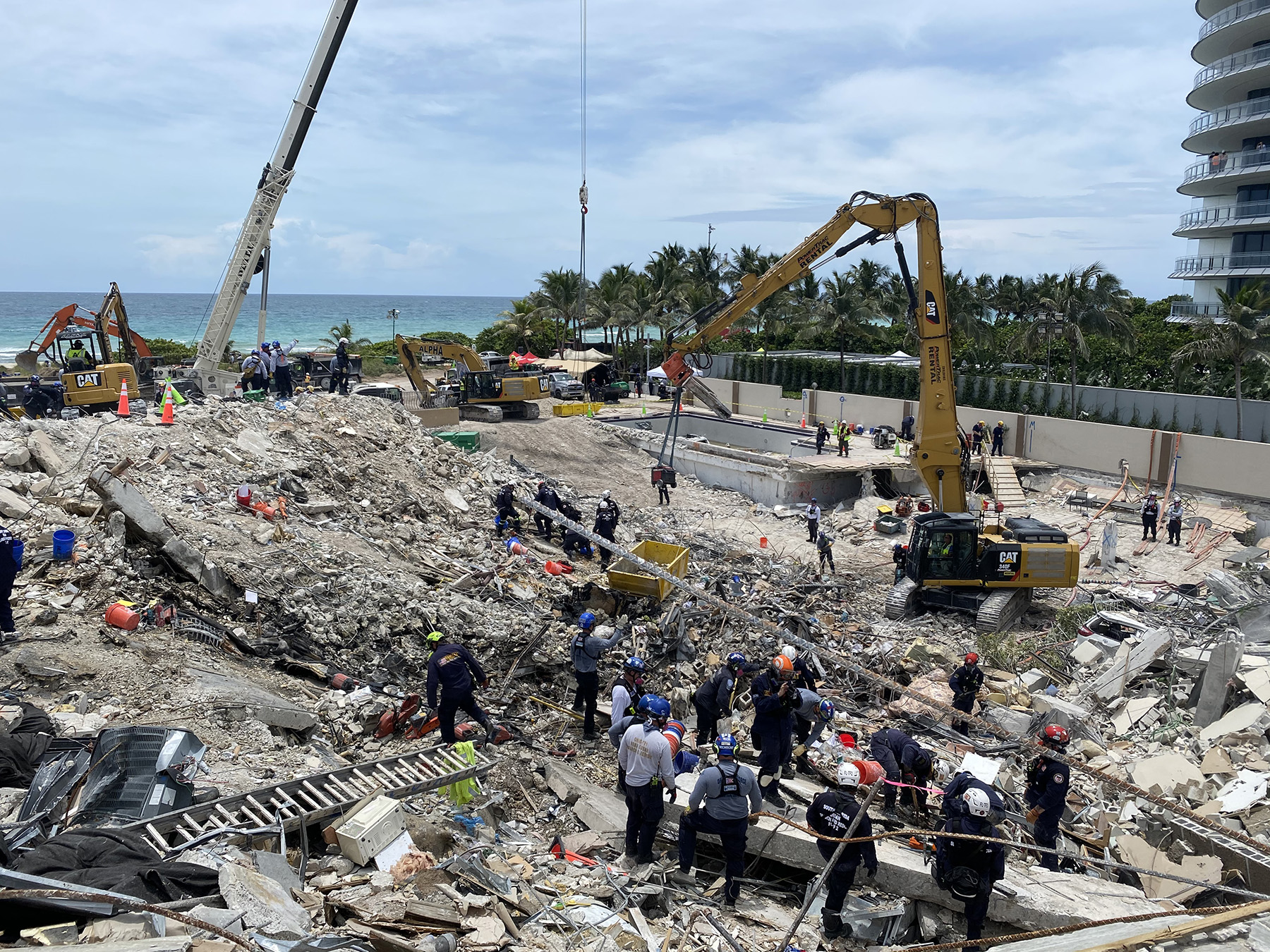
A key lesson Caldwell has learned from working in such dangerous situations is that they can always get more dangerous. A common misconception, even among other engineers, is that if a partially collapsed building has not collapsed any further after several days, it must now be safe to walk on or in, Caldwell says. “But that’s just not true,” he explains. “It’s just as dangerous after two days of not moving as it was right after the initial collapse.”
Moreover, human error can make a bad situation worse. Caldwell recalls escorting investigators into an agricultural mill complex following a devastating dust explosion. While Caldwell and his team were deep within a partially collapsed building, repair crews mistakenly reenergized a major power feed to a transformer near the investigation team. The transformer exploded, shaking the structure and filling it with smoke. The team escaped, but the episode highlighted two fundamental safety lessons for working in damaged buildings: deenergize all power sources and maintain clear communication with all parties at the site.
A sitewide stand-down occurred “to figure out what happened and why and discuss how to prevent it in the future,” Caldwell says.
Tragically — but not surprisingly — many workplace safety problems do not end so well. The Boeing Co. employs more than 1,700 people with civil engineering degrees and backgrounds because the breadth of these degrees helps such employees “see the big picture of a project from start to finish,” notes Steve Murphy, A.M.ASCE, a semiretired engineering leader at Boeing and the chair of ASCE’s Industry Leaders Council safety committee.
Murphy recounts a fatal accident from almost a decade ago that occurred at the company’s Charleston, South Carolina, plant. An employee was killed after falling through an open hatch in a 40 ft tall scaffolding tower that was supposed to be closed. That employee was not an engineer, but many engineers were working at that facility, Murphy says. In response to the accident, the plant’s leadership made changes to the design of the scaffold hatch to make sure it could not be left open.
And because falls from heights overall were a major safety problem, they also eliminated all but 10 of the more than 230 ladders that had been in use throughout the facility, Murphy says. Work was redesigned so that ladders were no longer necessary, or safer alternate ways were adopted to get employees to the work zones that had previously involved ladders.
Lacking control
In addition to the potential hazards of working in the field, civil engineers must also contend with the fact that those work sites are generally not under their control. “We don’t have control over means and methods, including personnel, equipment, how the site is run and managed, and safety protocols,” explains James Feuerborn Jr., P.E., M.ASCE, a managing principal at Thornton Tomasetti and the firm’s New York region co-leader. And that lack of control, Feuerborn admits, makes him nervous. “You’ve got to keep your eyes and ears open.”
To help make things safer, civil engineering firms can try to work with clients, general contractors, and other firms at the sites, coordinating safety plans and information about hazards. But at times, that simply is not enough.
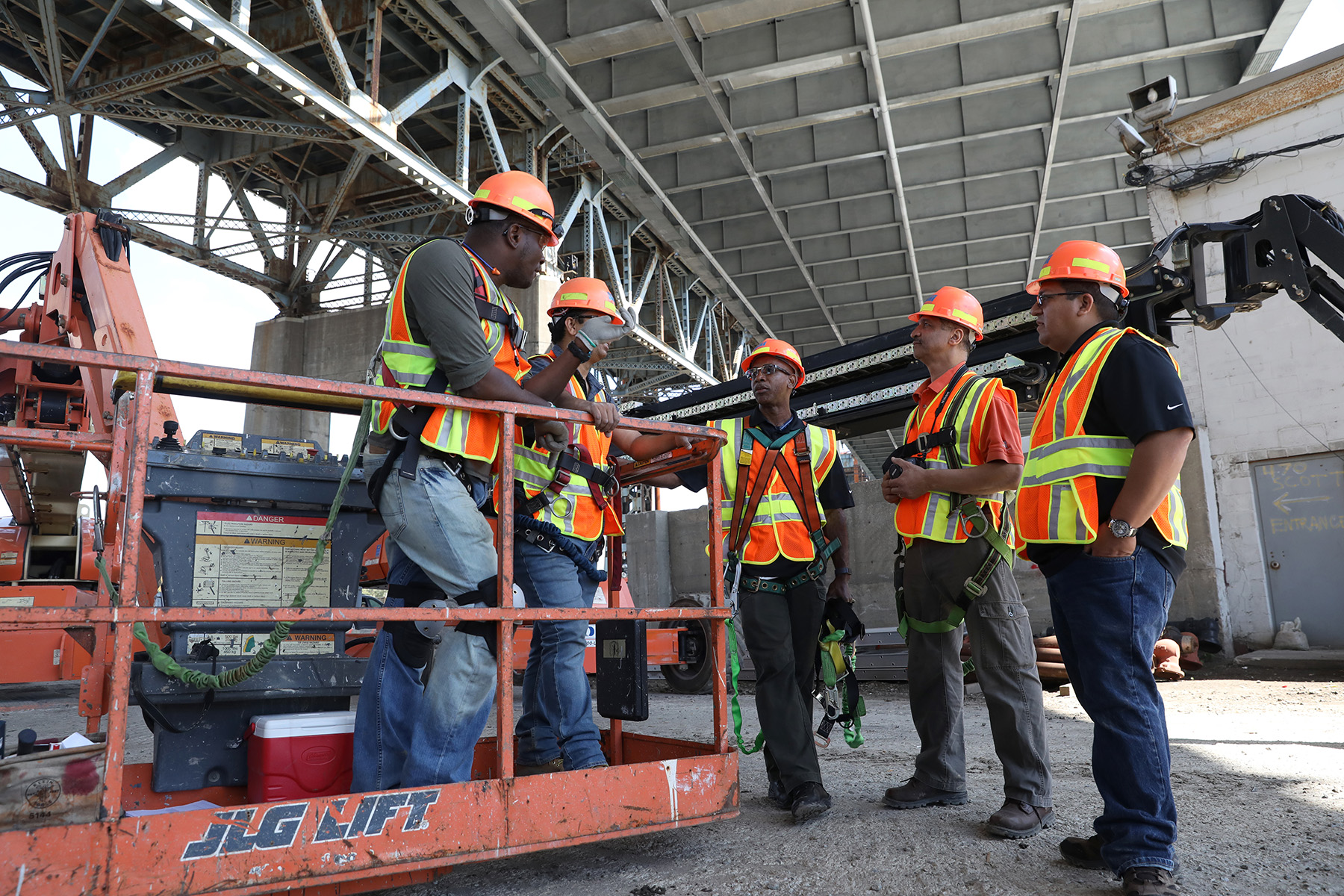
McGee recalls an incident during an inspection of a three-story dormitory that was under renovation. Walking around on the third floor, she noticed that a subcontractor’s welder had removed the guardrails for a stairwell, leaving a wide-open fall hazard, with no fall protection for the many workers in the area.
McGee did not have stop-work authority at that site, but she did have a good relationship with the general contractor. “So I went to the GC and showed him what was happening and said, ‘This could get someone killed,’” she explains. The general contractor then used his authority to stop the work. “It was a contentious discussion” between the general contractor and the subcontractor, McGee recalls. “But after 20-30 minutes, we were able to get on the same page and get proper fall protection in place.”
Januszkiewicz has encountered work sites at which catwalks were so dilapidated and deteriorated that he would not let his people walk on them. “Then I notify the owner as to why I won’t send my people out on that structure,” he says.
Likewise, Shumaker remembers a recent job for Thompson that involved the inspection of a tall super-structure at a petrochemical industry plant, requiring specialized training and fall protection equipment. But when Thompson’s team got to the site, it discovered that part of the structure — which was as much as 235 ft in height — was so deteriorated that there were no safe tie-off points. “So they stopped work and notified the client,” Shumaker says. “And we came up with an alternative plan.”
Although civil engineers often do not have the authority to stop all work on a project, they do have other safety duties, says Caldwell. “We stress that you have an obligation, over and above your job and your client, that if you see imminent danger on the job site, it is your obligation as a professional engineer to bring attention to it and do everything you can to mitigate that hazard,” Caldwell explains.
In the end, the engineering firm always has the option to pull its employees out of any situation that seems unsafe.
Thornton Tomasetti uses what it calls a red ticket safety protocol, notes John Deerkoski, P.E., M.ASCE, a senior principal and transportation practice co-leader: “If anyone feels at risk, for any reason, you can stop work and go to a safe location,” explains Deerkoski, whose teams conduct bridge and highway inspections, among other potentially hazardous operations.
Once the employee is someplace safe, “we’ll have a conversation to determine what the issue is,” Deerkoski says. “It’s better to err on the side of caution because we want everyone going home at the end of the day — that’s the No. 1 thing! We do our best to ensure that all protocols and procedures are in place, but we also want our people to feel comfortable speaking up if something doesn’t seem right.”
Tackling training
Safety training is a key component of any job safety program. Engineering firms mandate such training — sometimes purchased from vendors, sometimes created in-house — for their own employees and in some cases must also accommodate requirements for other specific training set by clients and/or localities.
For example, Thornton Tomasetti has an in-house training program that is required for all new engineers that gives them a basic understanding of site safety, says Marco Coco, P.E., S.E., a vice president in the firm’s structural engineering practice. But major construction firms can also have their own safety training requirements that anyone who wants to come onto their construction site must take, notes Feuerborn.
Once the engineers complete a contractor’s site-specific training, which might involve several hours of instruction, they receive a sticker for their hard hat or a card that serves as permission to allow them onto the site.
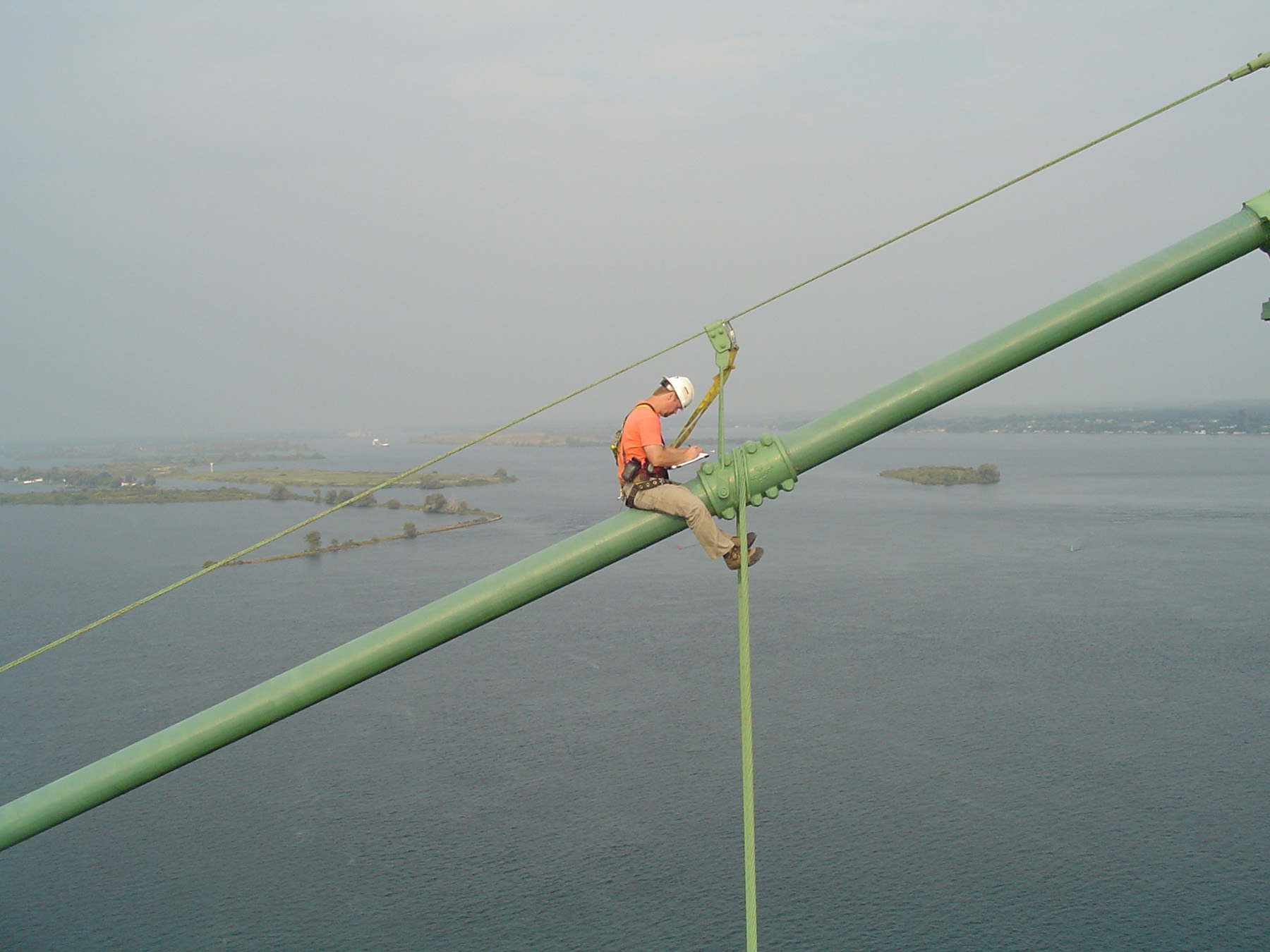
There can also be additional contractor-required training for particular tasks being performed on particular days — such as working at height while large trusses are being moved about. Before such activities begin, the contractor will require anyone who is going to be in the vicinity of that work to attend a highly specific safety meeting, known as a toolbox talk, “so everyone walking around that area — workers, inspectors, people observing the work — is cognizant of what’s going on around them (and understands) the hazards and what needs to be done to stay safe,” explains Feuerborn.
Specific locations can also add layers of required training. New York City, for instance, mandates 40 hours of safety training to access construction sites — training that can be accomplished by taking an OSHA 10 and OSHA 30 class, according to the New York City Department of Buildings. The OSHA 10-hour training program is primarily intended for entry-level workers, OSHA explains.
The 30-hour training program is intended to provide supervisors and workers who have some safety responsibility more detailed training. Designed to cover an overview of the hazards a worker may encounter on a job site, the construction training covers safety issues regarding cranes, excavations, scaffolding, staircases and ladders, health hazards, personal protective equipment, tools, and other topics.
Just getting your engineers trained is not good enough in some situations. It is also critical to track the training that people have had and make sure that the information is up to date, Feuerborn says. In some cities, taking the OSHA 10 and OSHA 30 training once is all that is required. But in New York City, that training must be renewed every five years, Feuerborn notes.
Likewise, a four-hour scaffolding safety training program and a 16-hour swing stage training course must be renewed every four years in New York City.
Feuerborn, who is a co-leader of Thornton Tomasetti’s forensics practice, explains that the very nature of forensics investigations — involving disasters, structural failures, or other unexpected events — means “you never know what’s going to happen, so you have to make sure you have enough people trained” to do whatever tasks might be required, from rope access to swing staging or scaffolding work. “You want to have a breadth of people to choose from,” he says.
You don’t want to have an incident occur and discover that only two members of your team are current with their training — and neither is available because they are both on vacation, according to Feuerborn.
Safety mindset
Safety equipment — from what engineers wear to what devices they might carry or monitor — is important for engineering firms to require and provide. But attitude is also critical, notes Coco.
“Safety is a mindset — a way of doing your work, and it has to start from the top,” Coco explains. “As leaders in the firm, we have to push that. We do send people out to dangerous places, so it’s our obligation to make sure that we do everything possible to ensure that it’s safe for everyone — our staff, other consultants, the public, everyone.”
The safety message needs to be supported and repeated, so those in the field or in the office know that everyone on the team is “looking out for each other,” Coco says.
In many workplace settings, a safety professional can just explain that something is an OSHA rule and so it must be followed, notes McGee. But engineers tend to be very analytical. “Doing this work with engineers has definitely made me much better at my job!” she muses. “Because I have to have a very clear explanation of the ‘why’ and the ‘how’ of what we’re doing, which is important to everyone — but especially important to engineers.”
SIDEBAR
Pandemic problems
The global COVID-19 pandemic put the people charged with workplace safety at civil engineering firms in an odd position. They were familiar with the normal hazards that engineers confront every day on the job. But the pandemic added new and unexpected safety issues — such as potential problems stemming from in-person meetings, commuting to work via public transit, and just showing up at the workplace, among others.
Kate McGee, CSP, an associate vice president at Pennoni and the firm’s director of health and safety, says the last few years have been a bit of a blur, with the rules continuously changing. “It was a huge challenge for our operations because we’re in at least 10 states, all of which had their own rules,” McGee says, explaining that the firm tended to follow the directives of local authorities when planning its COVID-19 responses.
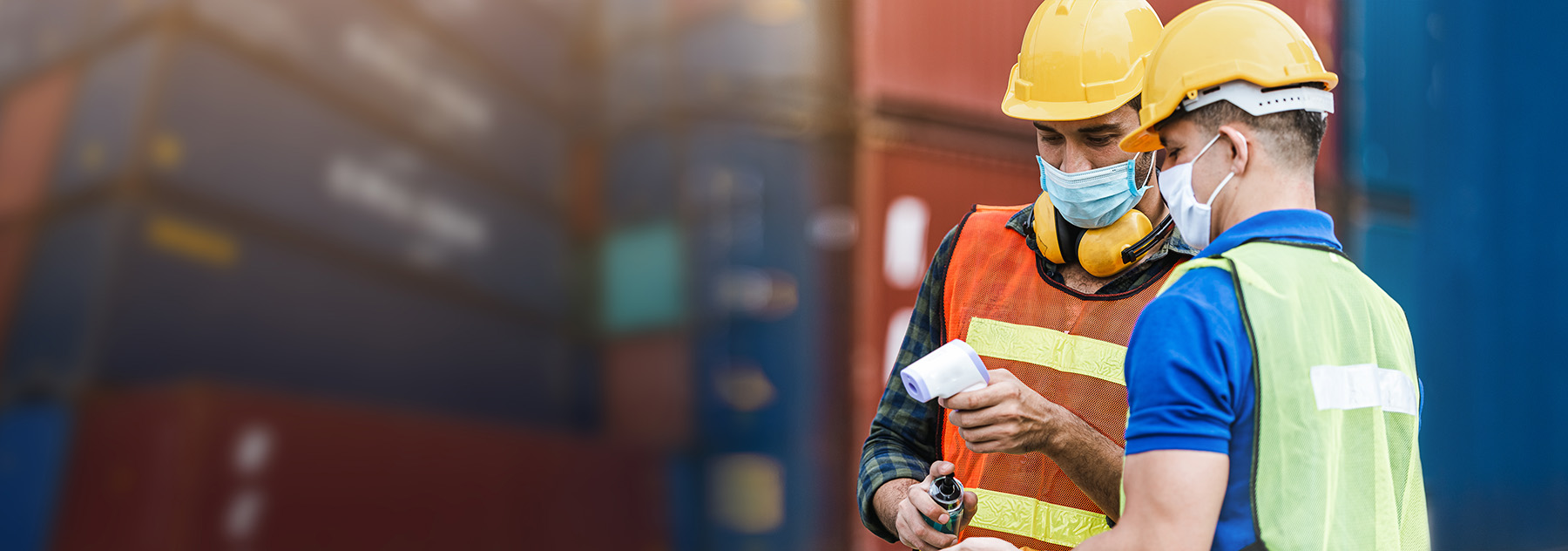
McGee especially credits Pennoni’s information technology team for quickly helping staff adapt to working from home. And in the field, issues of masking, social distancing, and other pandemic-related responses were handled on a case-by-case basis. “I had a spreadsheet (on which) we tracked all our cases (of possible exposures) and close contacts — a long spreadsheet,” she emphasizes.
At Thornton Tomasetti, different pandemic issues arose based on location. In places such as Kansas City, Missouri, where the workforce tended to drive their own cars to the office or to construction job sites, transportation continued as normal. But in cities such as New York and Chicago, where employees might have used public transit prior to the pandemic, some employees were no longer comfortable getting on buses or trains with other people.
So they started using taxis or Ubers and Lyfts, notes James Feuerborn Jr., P.E., M.ASCE, a managing principal at Thornton Tomasetti and the firm’s New York region co-leader. It added to the cost of the job, Feuerborn notes, but fortunately the clients understood.
On one particular job, Thornton Tomasetti was hired to conduct an assessment of a condominium building, says Feuerborn. “We talked to our staff about what they would need to feel safe,” he notes. “We compiled a list of requirements, so if a client needed us to enter a particular apartment, we’d ask for that apartment to be vacated or for the residents to wear masks.”
The firm explained that its people would also be wearing masks and gloves and maintaining 6 ft of distance, among other safety protocols. They also warned the client that if anybody in the apartment took off their mask during the assessment, “then we’re done. We’re out!” Feuerborn says.
SIDEBAR
Falcons and gators and bears — Oh my!
Exposure to wildlife is one of the more exotic safety challenges civil engineers can face. These incidents include engineers finding black widows and snakes that make their homes in or around bridges or other tall structures, alligators that swim in waters where engineer divers are working, and bears that show too much interest in human structures or that live in places where civil engineers need to go.
Falcons, for example, like to nest on big bridges and tend to be quite territorial, notes Mike Januszkiewicz, P.E., SPRAT III, the assistant director of field services at Modjeski and Masters’ Poughkeepsie, New York, office. So while conducting rope access inspections of bridges, engineers can be faced with — and struck by — these fast-flying, dive-bombing birds of prey.
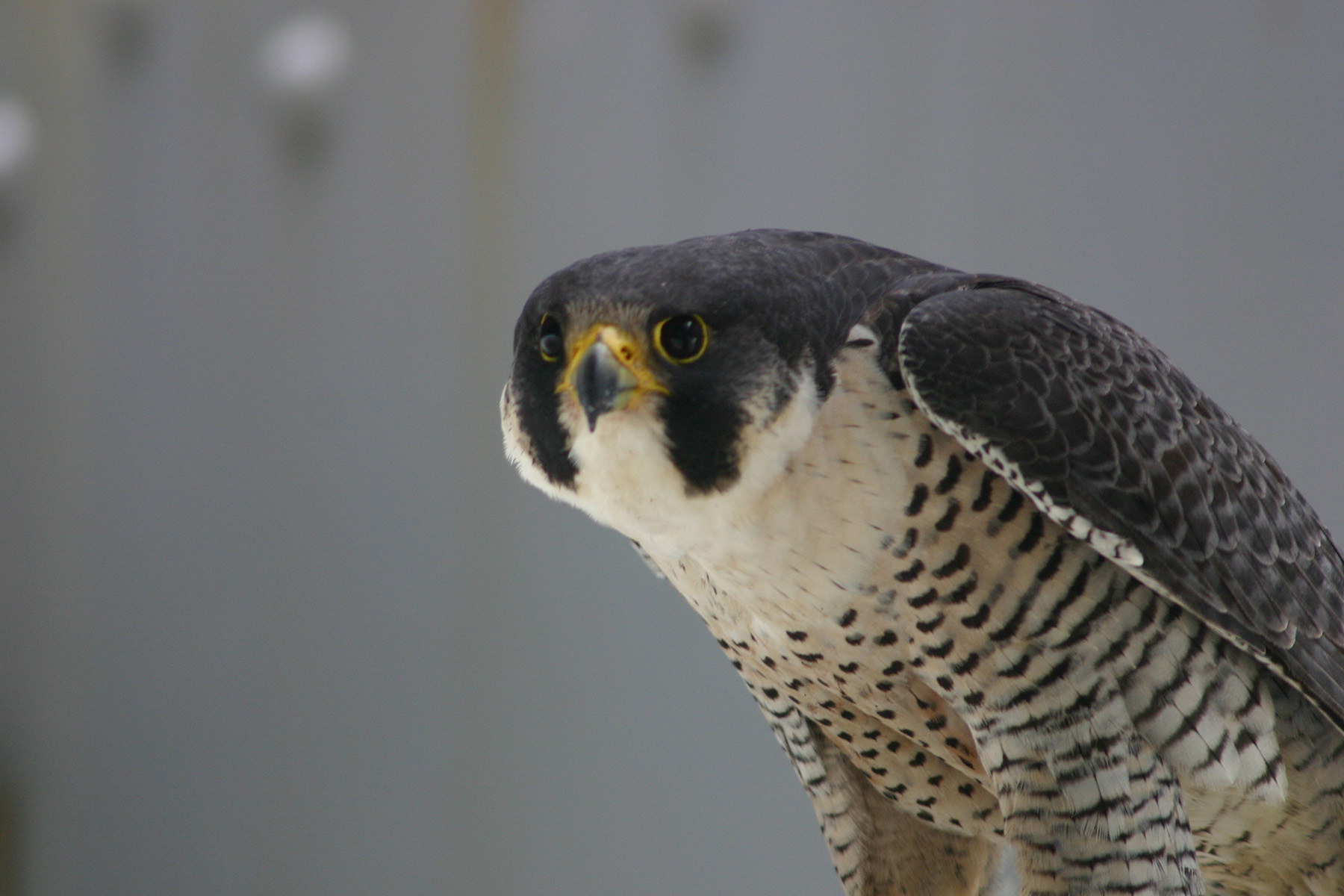
The falcons “always hit the highest thing on you, so as long as your helmet is strapped on properly, it’s OK,” says Januszkiewicz, who estimates he has been struck by falcons at least a dozen times at job sites. “But if you’re not aware of what they’re going to do, it can be scary.”
In Alaska, some engineers carry shotguns for protection against bears when going out into the wild to perform summertime maintenance on equipment used to predict spring runoffs (read “Snow Bound”).
And at one coastal Texas dive site, underwater engineering work was canceled for the day when an unwanted visitor showed up. As a dive supervisor reportedly said: “Our safety plan doesn’t keep us safe with gators in the water, so we’re going to call off the dive” (read “Diving into Engineering”).
This article first appeared in the November/December 2022 issue of Civil Engineering as “Safe at Work, Safely Home.”