By Robert L. Reid
Civil engineers who work on historic preservation projects need to understand more about the so-called archaic materials they might be dealing with and other aspects unique to preservation work.
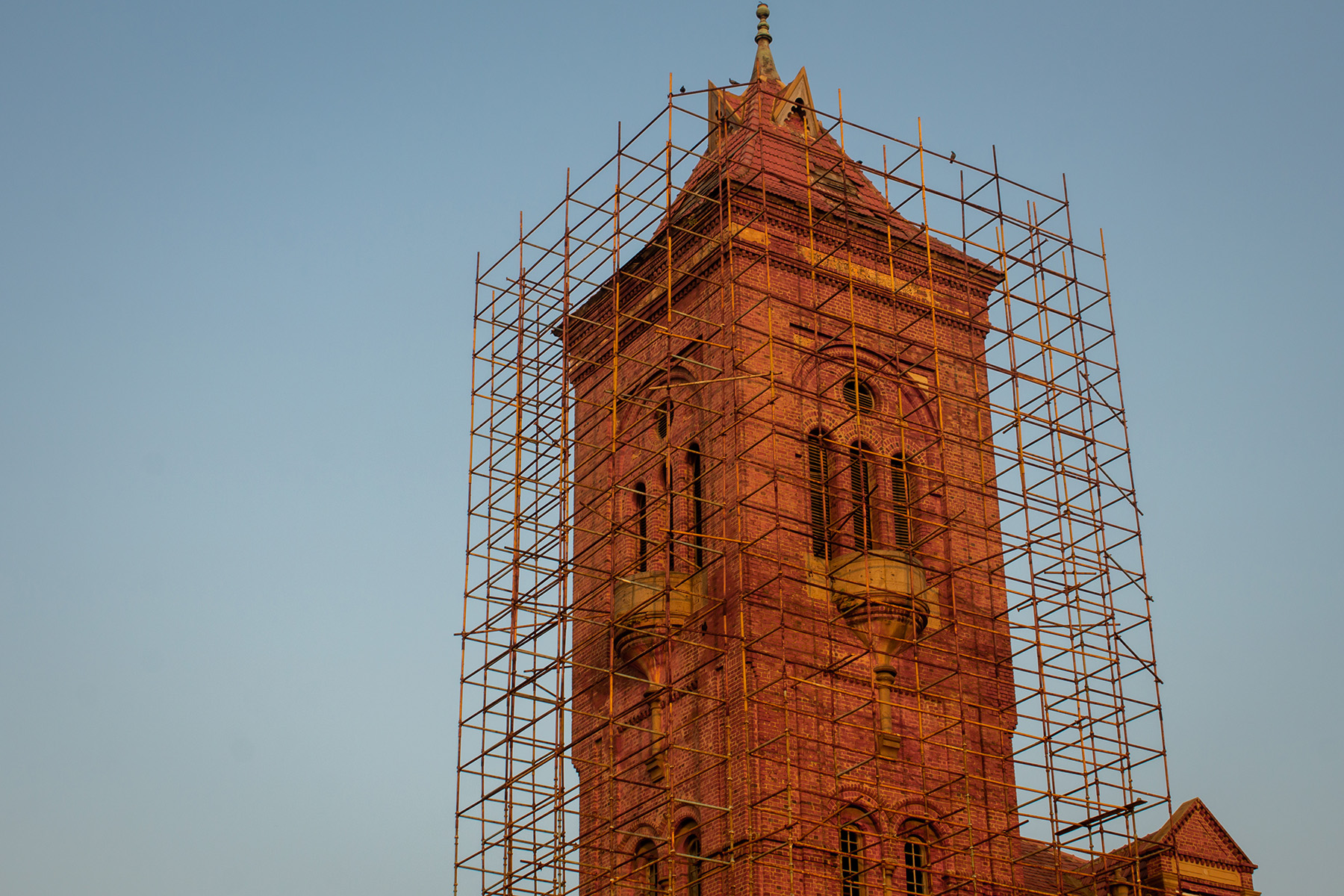
The civil engineers who help preserve historic buildings and other landmark structures live a sort of double life. For while they can work in ways that are similar to traditional structural engineering or other engineering disciplines, they must also deal with areas or aspects that can be unfamiliar to their fellow engineers.
These efforts, known as either preservation or conservation engineering, require an understanding of archaic structural systems that are no longer widely used as well as archaic materials, such as cast and wrought iron, and how they differ from each other and from modern steel. It is important to know the properties and capacities of different mortars, masonry materials, and wood products.
Engineers on preservation projects may need to work more closely with architects and contractors than they might otherwise as well as with specialty craftspeople and various government agencies or preservation-focused entities to obtain approvals, funding, or even information.
And perhaps most significantly, historic preservation can demand a different way of thinking for engineers, notes Kunal Badheka, P.E., an associate principal at Thornton Tomasetti who has worked on numerous historic preservation projects.
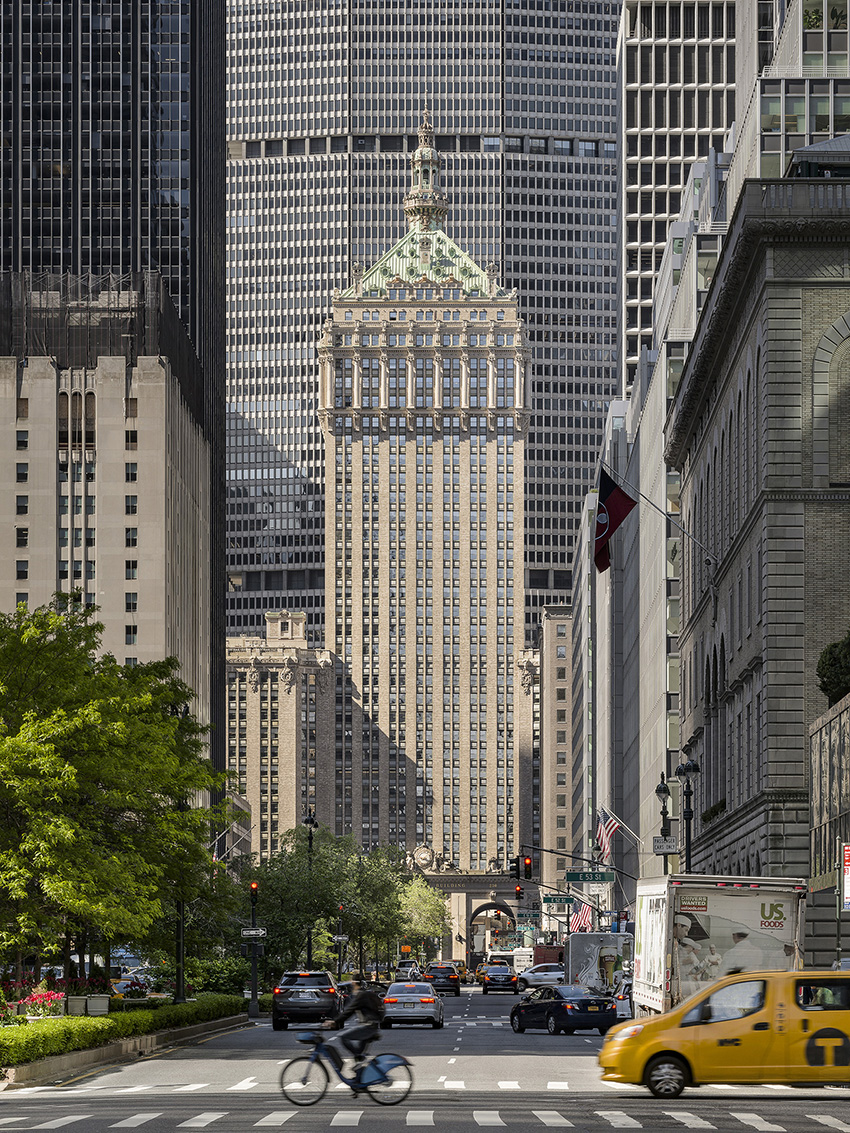
“When restoring a building with a historic fabric or historic elements, you need to have the mindset of an architect,” Badheka says, by which he means that engineers need to think in terms of colors, textures, and other aesthetics as well as the technical aspects. He compares being a preservation engineer to “an orthopedic surgeon who also needs to have plastic surgery expertise.”
Kevin Duffy, P.E., the vice president of operations for building envelope services at Rimkus, echoes those ideas. “It’s something you have to get used to when you come into the (preservation) industry — that aesthetics and looks really do matter in the end,” says Duffy, another preservation veteran. “It can be tough” for engineers to understand, he adds, “because you might want to just go out and make (the structure) functional, which should be fine, right? That’s the engineering perspective.”
But just making a historic building functional is “not fine,” Duffy explains. “The client won’t find it fine, the government agencies (that protect historic structures and oversee preservation projects) won’t think it’s fine. So you’ve got to develop the approach that aesthetics do matter.”
Focusing on facades
An emphasis on aesthetics is necessary because the preservation of historic buildings often focuses on the building’s facade rather than the underlying structure. “When you think about historic properties or buildings, you need to consider what’s the historic fabric. What are the contributing elements of that historic structure?” asks Jeffrey Kobes, P.E., S.E., a principal in the diagnostics group in the Dallas office of Walter P Moore. “Most of the time, it will be the exterior.”
In some cases, the historic facade is the only portion of a building that is considered significant enough to preserve, notes Duffy. Before the facade is restored, it is braced or otherwise protected, and the rest of the structure, especially the interior, is sometimes altered dramatically for some new use or even demolished and replaced with an entirely new structure.
As Badheka explains: “What sets historic preservation apart is the ability to restore the historic fabric in a way that does not alter the appearance of the building’s exterior.” That goal can be challenging, he notes, especially when the historic materials are difficult to replicate. “In those instances, we also have to find a repair solution that will minimize any disturbance to the larger system or elements” of the building’s design, he adds.
In the United Kingdom, for example, the Elizabeth Tower at the Houses of Parliament — the site of London’s famous Big Ben clock — was recently restored. As part of that restoration, a new quarry had to be found to provide limestone to replace portions of the tower’s damaged cladding because the Victorian-era quarry that had supplied the original stones was no longer in operation, notes Matt Penellum, CEng, MIStructE, MICE, a senior structural engineer at AECOM.
Structural matters
The Elizabeth Tower project also demonstrates another aspect of preservation work: While the primary focus can be on appearances, especially on matching the original appearance of the building envelope being preserved, the project can involve critical structural engineering work as well. During the tower project, for instance, an old foundry was reopened to cast new iron elements to replace the original, damaged pieces that would be hidden behind the structure’s historic envelope but that were critical to maintaining the tower’s structural integrity, Penellum explains.
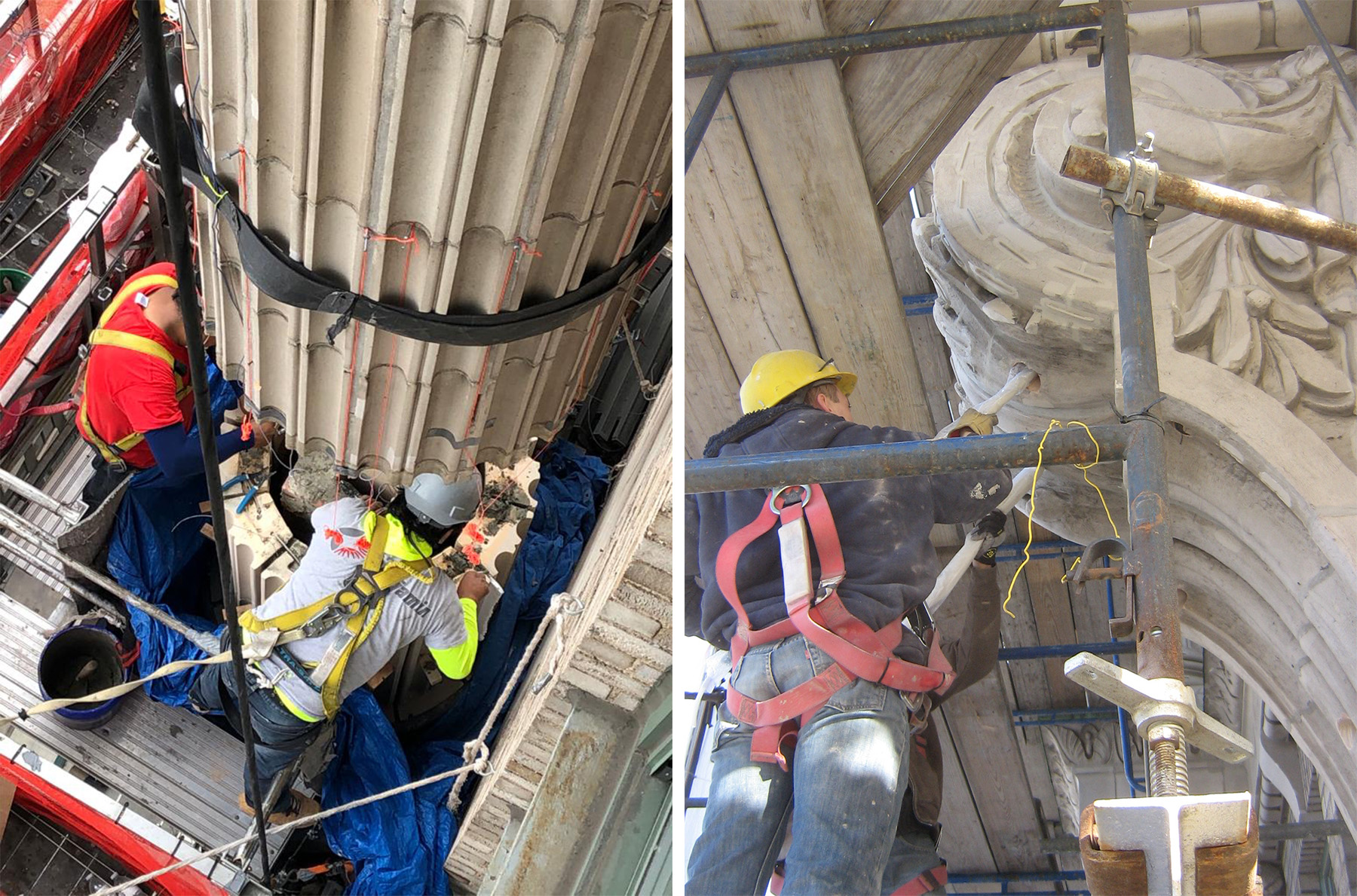
Likewise, parts of a historic facade might be poorly supported, such as a large, cantilevered cornice that needs to be resecured. Or portions of the facade might be deteriorated to the point that they no longer protect the building by keeping out moisture, says Kobes. “So the facade touches both the aesthetics of the building enclosure and the structure,” he notes.
A preservation project involving an early 20th-century building at 230 Park Ave. in New York City had aesthetic and structural issues, Badheka says. Several three-story-tall, free-standing decorative terra cotta columns were cracked, as were the one-story-tall terra cotta bottom brackets with embedded steel that supported the columns. One consultant told the owner to replace everything, notes Badheka.
“But when we looked at it, we took a different approach,” he says. In order to correlate the degree of cracking evident at the surface of the terra cotta column enclosure to the corrosion of the structural-steel lattice elements within it, Thornton Tomasetti decided to use impact echo, ultrasonic pulse velocity, infrared scanning, and invasive probing methods.
The design team developed a finite-element engineering model to analyze the behavior of cracks in the terra cotta brackets. These techniques helped the engineers develop appropriate and cost-effective repair solutions, including specially designed stabilization anchors. An impressed current cathodic protection system was also installed at certain locations to prevent and monitor steel corrosion.
“So instead of replacing it all, we ended up restoring sections of it in place and retaining most of the historic terra cotta. This was a robust repair program that was accomplished with sensitivity to preservation requirements,” Badheka says.
Learning the trade
There do not seem to be any four-year undergraduate or graduate-level programs intended specifically for civil engineers, but there are various courses on key topics available at certain colleges and universities — from community colleges to Ivy League schools such as Cornell. Although such classes are often aimed primarily at architects, not engineers, Johns Hopkins University in Baltimore does have a series of courses that were developed by and are taught by experienced civil engineers.
These courses include information on structural materials that are no longer in widespread use as well as structural materials for which analysis and design practices have changed significantly over the last half-century. Other topics cover avoiding damage to historic buildings during adjacent demolition, excavation, dewatering, and construction activities.
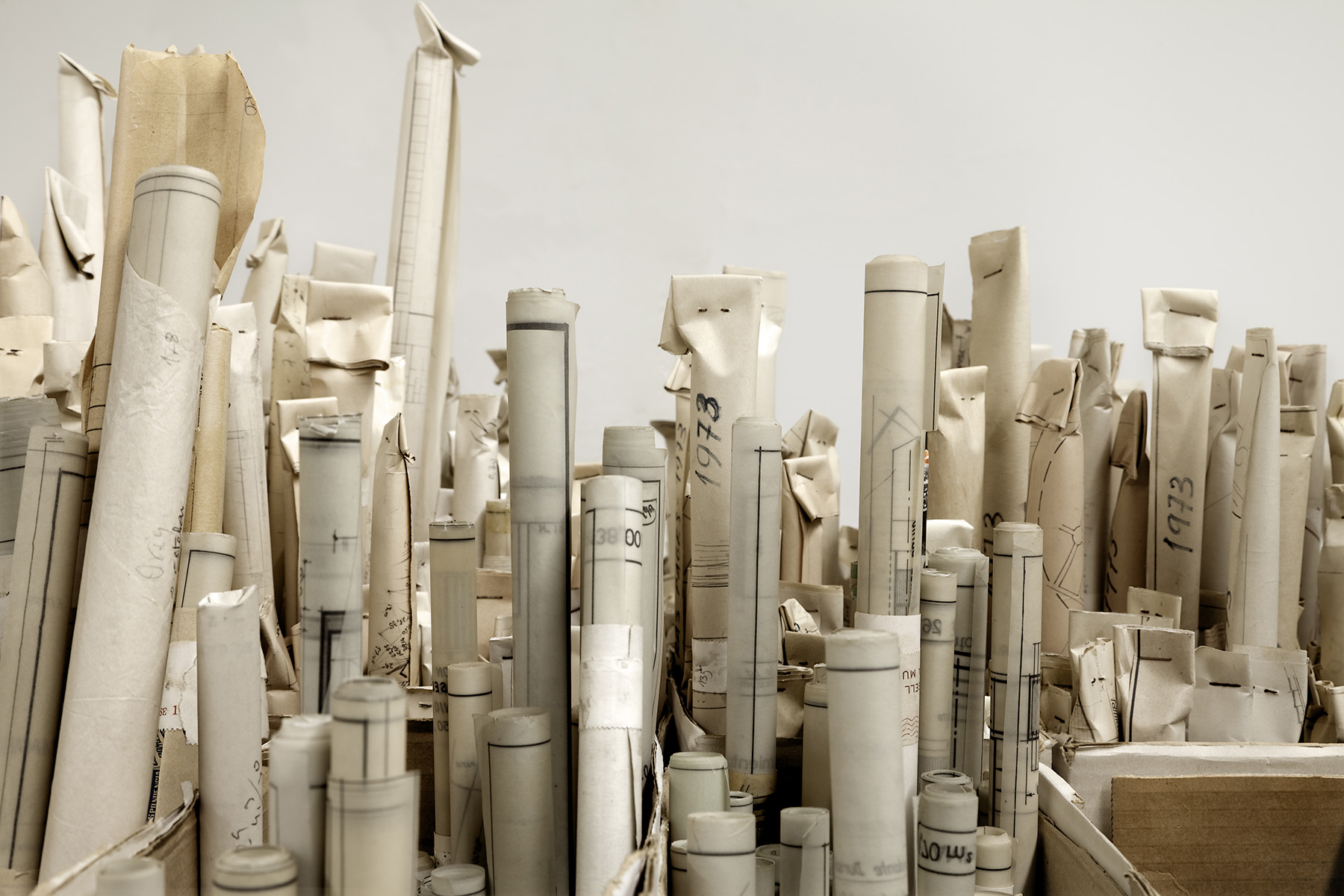
There are also a number of resources civil engineers can turn to for general information on working with historic structures, ranging from books, websites, and preservation-focused organizations to critical government documents, such as the almost-ubiquitous The Secretary of the Interior’s Standards for the Treatment of Historic Properties (read the sidebar “What preservation engineers need to know”).
General information is sometimes all that can be found, as many preservation projects must proceed with little or no original drawings or other historical documents about how the building or structure was designed and constructed.
“It’s surprisingly common to not have documents,” says Penellum. “At the time, when the original architects designed the (historic structure), there would have been a lot of drawings of exactly how it was to be built. But more often than not, over the intervening years, those documents haven’t survived.” Even maintenance or repairs conducted more recently — in the 1950s or 1960s, for instance — were often not documented well, Penellum says. “There’s a whole legacy of people doing minor things, or even quite serious interventions, without seemingly any record,” he explains.
On the job experience
While these somewhat limited educational opportunities and general resources are useful for gaining some of the knowledge and skills needed to conduct a historic preservation, nearly all the engineers contacted for this article noted that they learned about historic preservation on the job by working on such projects, often alongside more experienced engineers.
Consider the case of Edmund Meade, P.E., FAPT, a principal and the director of preservation at New York City-based Silman, a T.Y. Lin company. Meade earned a bachelor’s degree in civil engineering at Johns Hopkins, where he also took courses in architecture history. Later he earned a master’s of architectural history and a certificate in historic preservation from the University of Virginia. He also helped create and still teaches several of the historic preservation engineering courses at Johns Hopkins.
Yet, Meade says, “about 95% of my historical engineering knowledge comes from learning by doing — through analysis, investigation, design, and fieldwork before, during, and after construction” on preservation projects.
Justin M. Spivey, P.E., FAPT, APT RP, M.ASCE, a senior associate at Wiss, Janney, Elstner Associates Inc., in Philadelphia, adds: “It sometimes becomes a chicken or egg question: How do you get experience in historic preservation engineering? It’s by doing historic preservation work.”
Spivey worked at Silman earlier in his career and was later invited by Meade to help create and teach the Johns Hopkins preservation engineering courses. His career began not with engineering — even though he earned degrees in civil and structural engineering — but with history. His first job after graduate school was as a historian with the National Park Service, working for the Historic American Engineering Record, now part of the NPS’ Heritage Documentation Program. But while there, he worked with a number of engineers whom he considers his mentors.
“They showed me you could work with historic structures and practice engineering,” Spivey says, which eventually persuaded him to return to the civil engineering fold. “I really had to go away from engineering to meet these engineers who worked in historic preservation and then come back to the field,” he explains. So now, when he teaches classes to young engineers, he feels he’s sharing what his mentors taught him.
Working well with others
In addition to collaborating with and learning from their engineering colleagues, civil engineers working on preservation projects can also encounter diverse teams from other disciplines, including architects, skilled craftspeople, contractors, and specialists in various materials. Spivey refers to “a community of people doing this work who help each other.”
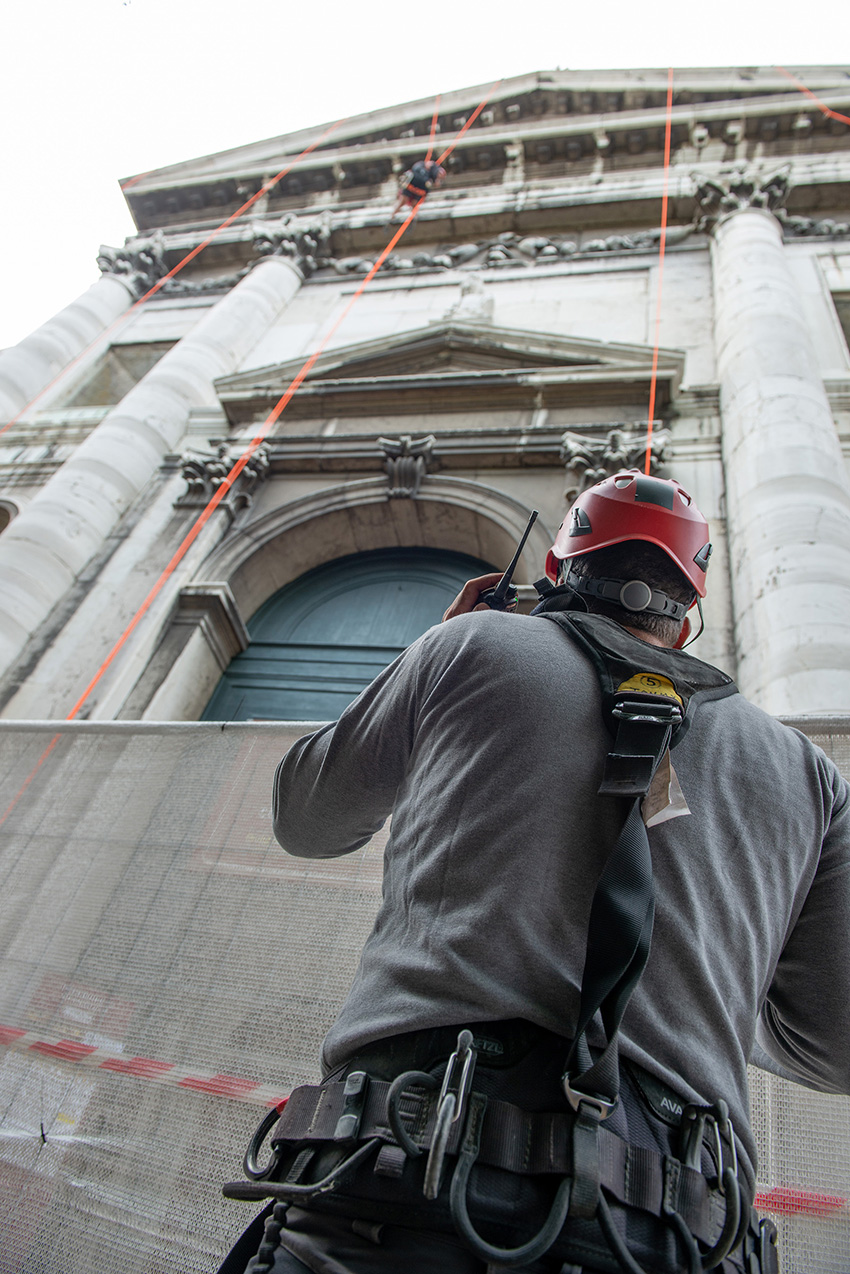
Meade notes that preservation engineers will “probably be working with a team, and that means asking everyone on the team what they think” about the project and its challenges. The likely variety of answers is critical to identifying the best solutions, the best designs, and the best order of work.
Preservation engineers should also be prepared for the involvement of government agencies at the local, state, and federal levels as well as nonprofit organizations that advocate for the preservation of historic structures.
In a typical historic restoration project, explains Badheka, engineers often team with the local building department — for which the project applications and documents will be submitted for approval — as well as additional agencies that may have placed the building on a registry of protected historic structures.
Or the structure might be part of an entire historic district, such as those established in New York City by its Landmarks Preservation Commission. Other historic buildings might be registered by a state historic preservation office or the NPS, which administers the National Register of Historic Places.
“When repairs, restoration, or any type of alterations are required on a historic structure, these agencies get involved to make sure that the project is approached within the principles of preservation,” Badheka explains. “As such, these agencies tend to review the scope of work being proposed as well as conduct or perform in-depth reviews of project details and specifications, particularly those that pertain to the direct modification of the historic fabric.”
The extent of involvement by government agencies or local organizations differs by jurisdiction and depends on various factors, including how the project is being funded. For projects that receive federal money, often in the form of tax incentives, a structure that is listed or eligible for listing in the National Register of Historic Places will trigger a government review as well as the requirement for mitigation of any adverse effects to the property, notes Spivey.
“For privately funded projects, a property’s listing in the National Register offers an opportunity for the project to qualify for federal tax incentives,” Spivey adds. “Similar programs exist for properties listed on state registers in some but not all states. These provide incentives toward preservation, more so than protection against alteration or demolition.”
For a property listed on a municipal register of historic places, the requirements vary widely, Spivey notes. “But many large jurisdictions, such as New York City and Philadelphia, and some smaller ones have historic preservation ordinances that require proposed alteration or demolition of a listed property to be approved by a municipal historical commission as part of the zoning or building permit review process.”
Although some preservation engineers report difficult or challenging relationships with these various entities, including projects that seem to be delayed interminably over certain issues, others note that such groups can also be valuable resources about historic properties. Spivey says his firm often approaches the Philadelphia Historical Commission “at the start of projects, and hopefully it can be a collaborative relationship where we can say, ‘Here are the problems we’re trying to solve and here are some solutions we have in mind, so can we get a preliminary reaction to them?’”
In some cases, Spivey adds, the commission has provided information about publications in which the building was documented or archival photographs of the structure that the engineers did not know about. “So they’ve provided information we didn’t already have that helped us develop the preservation treatment,” he explains.
For preservation engineers, the best way to work with such government entities and other stakeholders “is to understand and address the preservation aspects from the inception of the project and develop an appropriate scope of work,” concludes Badheka.
“Ultimately these agencies are trying to ensure that the project is being approached in a manner that follows historic preservation principles, and they are there to help in case some approach is not having the desired results. If they reject a particular part of the work or details, it is likely for specific reasons, and in those cases, it’s best to collaborate with them to solve the challenge.”
About archaics
Preservation engineers need to understand archaic materials and structural systems — meaning materials or systems that were used in the past but are not widely used today, says Kobes. For example, certain types of old floor systems featured flat tile arches or hollow clay tiles that might have been used for strength or might have been part of the fireproofing of steel.
Likewise, there have been many evolutions in the reinforcement of concrete, with early rebar once commonly made from smooth square bars, as compared with modern round rebar that is ridged or dimpled. Engineers on preservation projects must understand the differences because they affect how deeply the rebar needs to go into the concrete to actually engage the material, Kobes says.
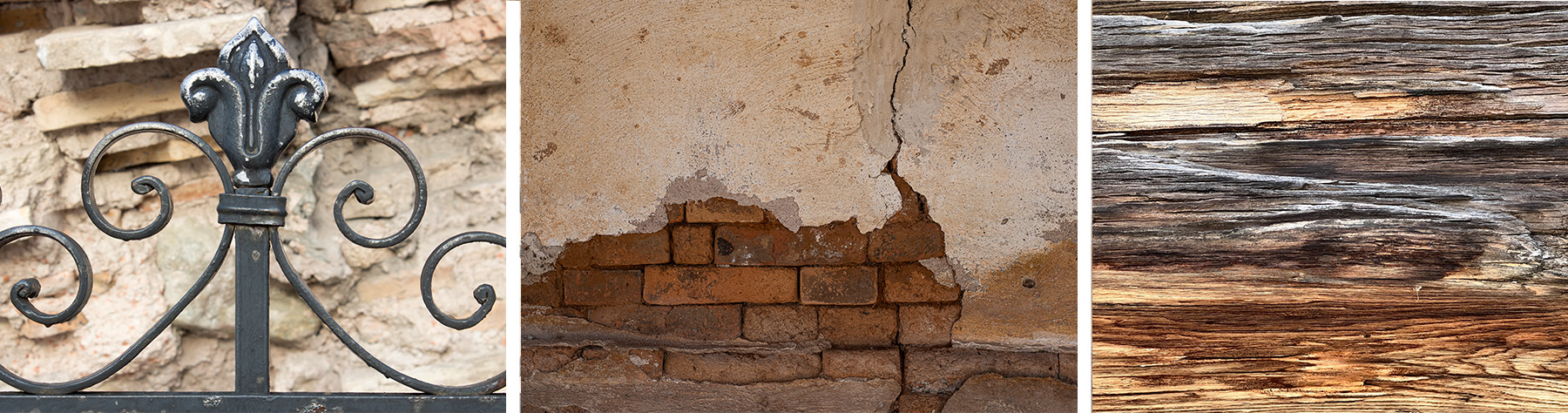
It’s also useful to know the differences between wrought and cast iron: Wrought iron is ductile while cast iron is brittle. With wooden elements, it’s important to understand what type of wood was used — for example, oak, maple, or yellow pine — because if a part must be replaced, the engineer needs to use a wood that is comparable in strength.
Understanding the compressive strength and other characteristics of the bricks and mortar used in historic structures is also useful. “Depending on the age of the building, it can be difficult to determine what type of brick or mortar to utilize” for repairs, notes Duffy. “We’ve done a number of projects (for which) you need (to perform) a mortar analysis. You take a piece of mortar and send it out to the lab, where they tell you what the chemical composition is and what the strength of it is.”
That analysis can be critical because “if the mortar has a higher compressive strength than the brick itself, the brick starts to fail — you see that in lots of older buildings,” notes James Monahan, P.E., CEng, M.ASCE, a principal building envelope consultant at Rimkus.
And the aesthetics of the mortar must also be considered. Sometimes the color of the mortar has changed because of pollution or other factors, says Monahan. “So you’ve got to find a mortar that will match” how the mortar looks currently.
Another solution, albeit an expensive one, is to hire an artist to paint the new mortar or brick so that it matches the way the original material looks now, adds William Davis, a registered architect and operations manager at Rimkus.
To resolve questions of aesthetics and other issues during a preservation project, it can be useful to prepare mock-ups to show the owner — as well as government agencies, state or local historical organizations, or other groups — what the final result will look like. On one project that involved a mortar with a high aggregate content, “we had a difficult time matching the new mortar to the way the historic mortar looked,” Davis recalls. “So we tried different aggregate sizes and concentrations, but it took weeks and maybe 20 samples or so and 20 different mock-ups to get it right!”
A trial repair on a small scale or pilot basis can also help save time and money later, notes Spivey. He recalls one preservation project involving a building with an exposed-concrete frame and brick infill. Because the contractor’s bid was based on a misunderstanding of the depth of the existing concrete that had to be removed to treat the corroding rebar inside, the project team struggled to revise and prioritize repairs while staying within budget.
“The lesson learned there was that during the design phase, we should try complex repairs,” Spivey notes, “and document the level of effort required, and then communicate that information to the bidders so they really understand what they’re getting into.”
Of course, on any historic preservation project — whether you’re a contractor, architect, or civil engineer — it’s always good to know as much as possible about what you’re getting into.
Robert L. Reid is the senior editor and features manager of Civil Engineering.
This article first appeared in the July/August 2023 print issue of Civil Engineering as “Preparing to Preserve.”