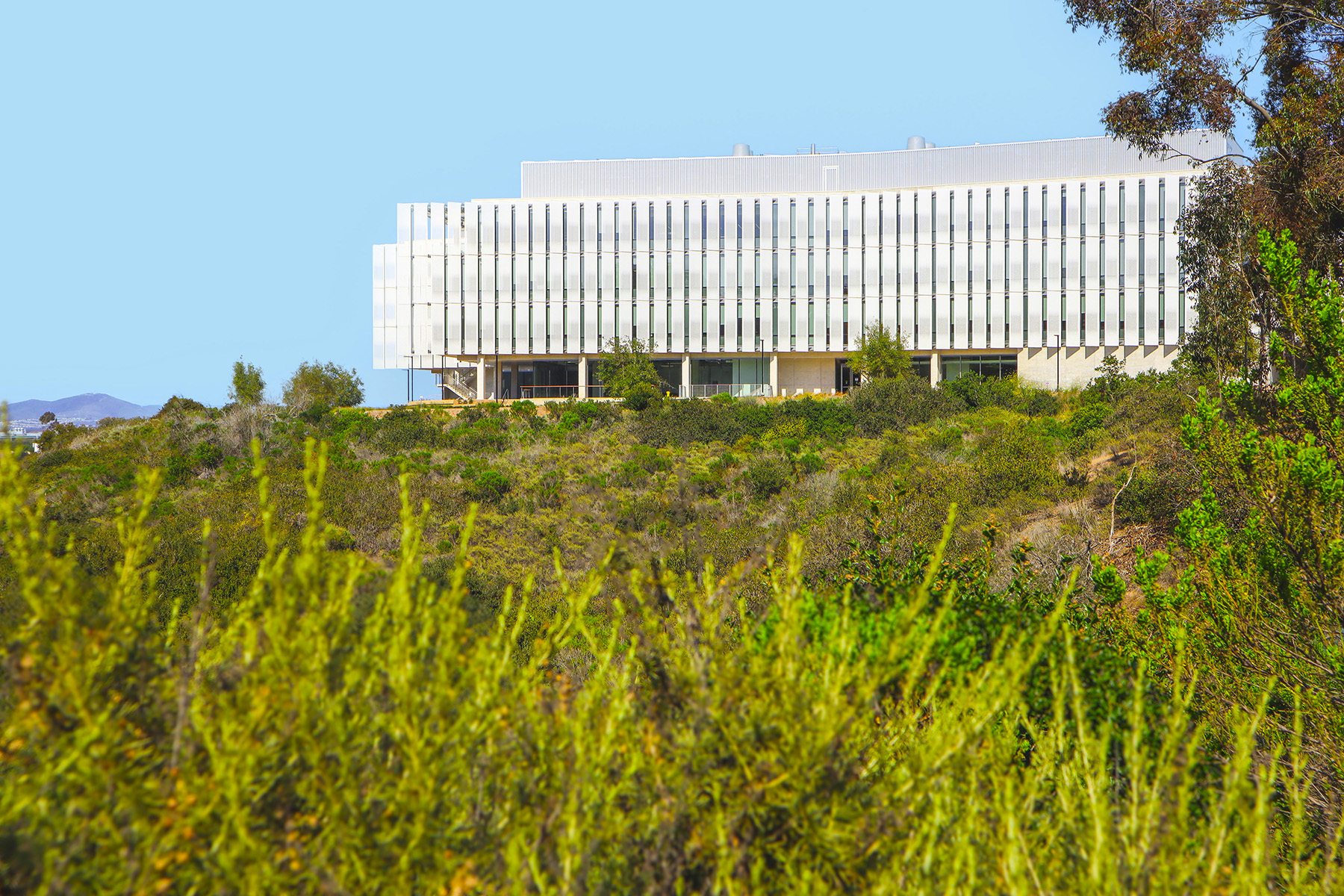
By Casey Whitsett, P.E., S.E., and Chelsea Kemmerrer, P.E.
Within the University of California San Diego’s Franklin Antonio Hall, soaring glass ceilings spill sunlight into three-story atriums, and a monumental steel spiral staircase appears to defy gravity in the main concourse. Throughout, the building seamlessly integrates into San Diego’s natural environment. Franklin Antonio Hall, the latest addition to UC San Diego’s Jacobs School of Engineering, provides a flexible and collaborative environment that will fuel the next generation of cutting-edge research and innovation.
Inspiring collaboration
Franklin Antonio Hall is a four-story, cast-in-place concrete building that sits atop a basement level. Set on a hillside, the structure is approximately 186,000 sq ft, comprising 13 research spaces dubbed “collaboratories” as well as new classrooms, an auditorium, and core facilities that support the students and faculty.
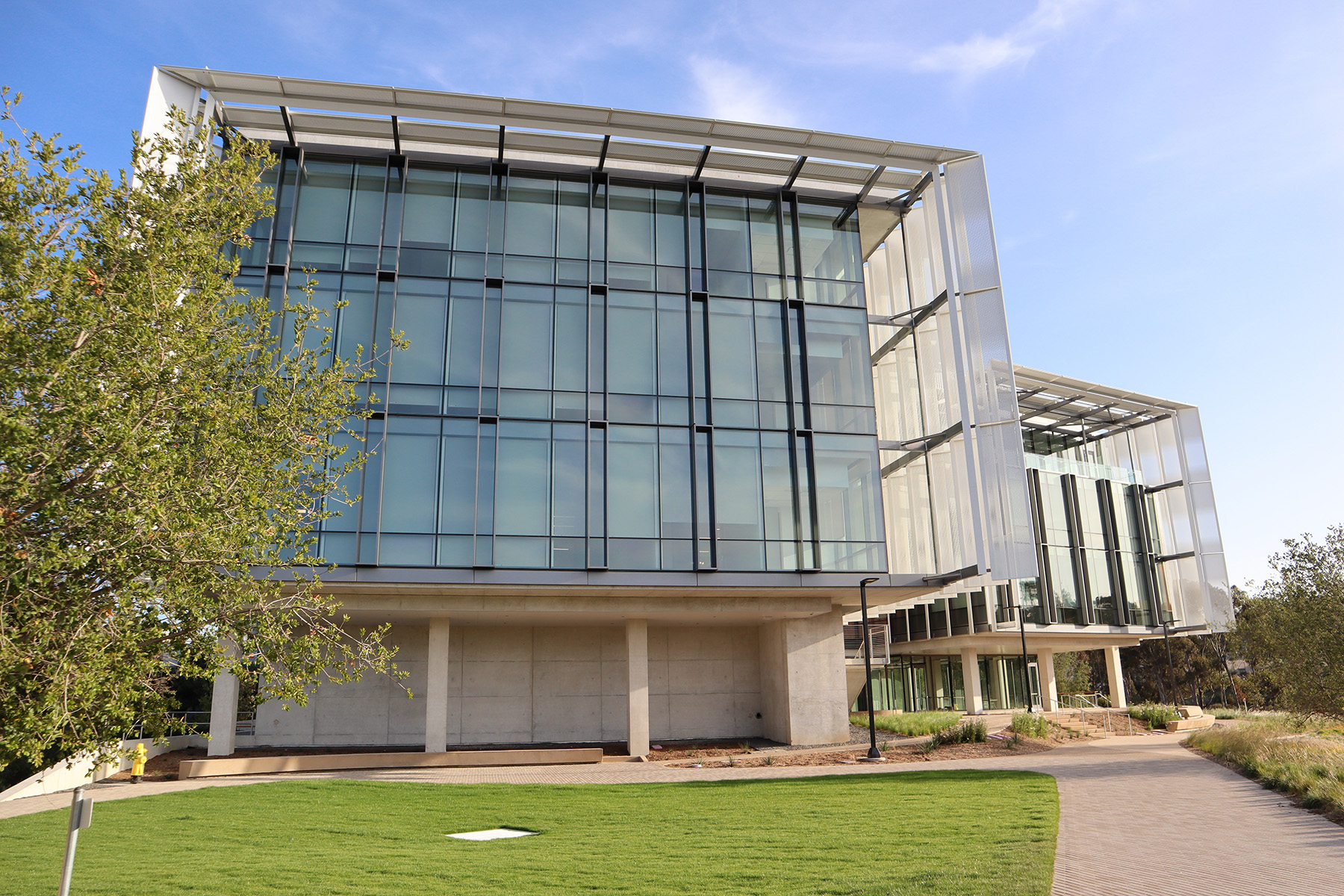
Design began in May 2018, and construction was completed in March 2022, coming in at a cost of $185 million. The design team consisted of Perkins&Will (architect), Coffman Engineers Inc. (structural engineer), and McCarthy Building Companies Inc. (general contractor).
The design team was tasked with four main goals:
1. Provide ease of movement and visibility.
2. Allow cross-disciplinary inter-lab collaboration.
3. Capitalize on the hillside location to blend interior and exterior experiences.
4. Create a landmark structure.
To meet the first two goals, the design team exposed the concrete frame as an architectural element to showcase the building geometry and symbolize the connection between the engineering disciplines and varying scientific research occurring throughout. The floor plate, which resembles the process of mitosis or cell splitting, is divided by two three-story atriums on each end of the building, creating four main wings connected by a central core.
However, this configuration created a structural engineering challenge because it limited the placement of the reinforced-concrete shear wall cores to the center of the building. This further complicated the building’s torsional behavior and required hefty diaphragm reinforcement to drag the load from the wings back to the central core.
To inspire connectivity across the atrium spaces and between the four wings of the building, the design team added slender bridge elements at the exterior glass line. Steel-framed bridges that are 6.5 ft wide span the atriums at each level, connecting the east and west wings, directly next to the full glass curtain wall. The bridges brace the full-height glass walls out of plane by connecting hollow structural section, 4 in. by 0.25 in. kickers back to the main bridge steel.
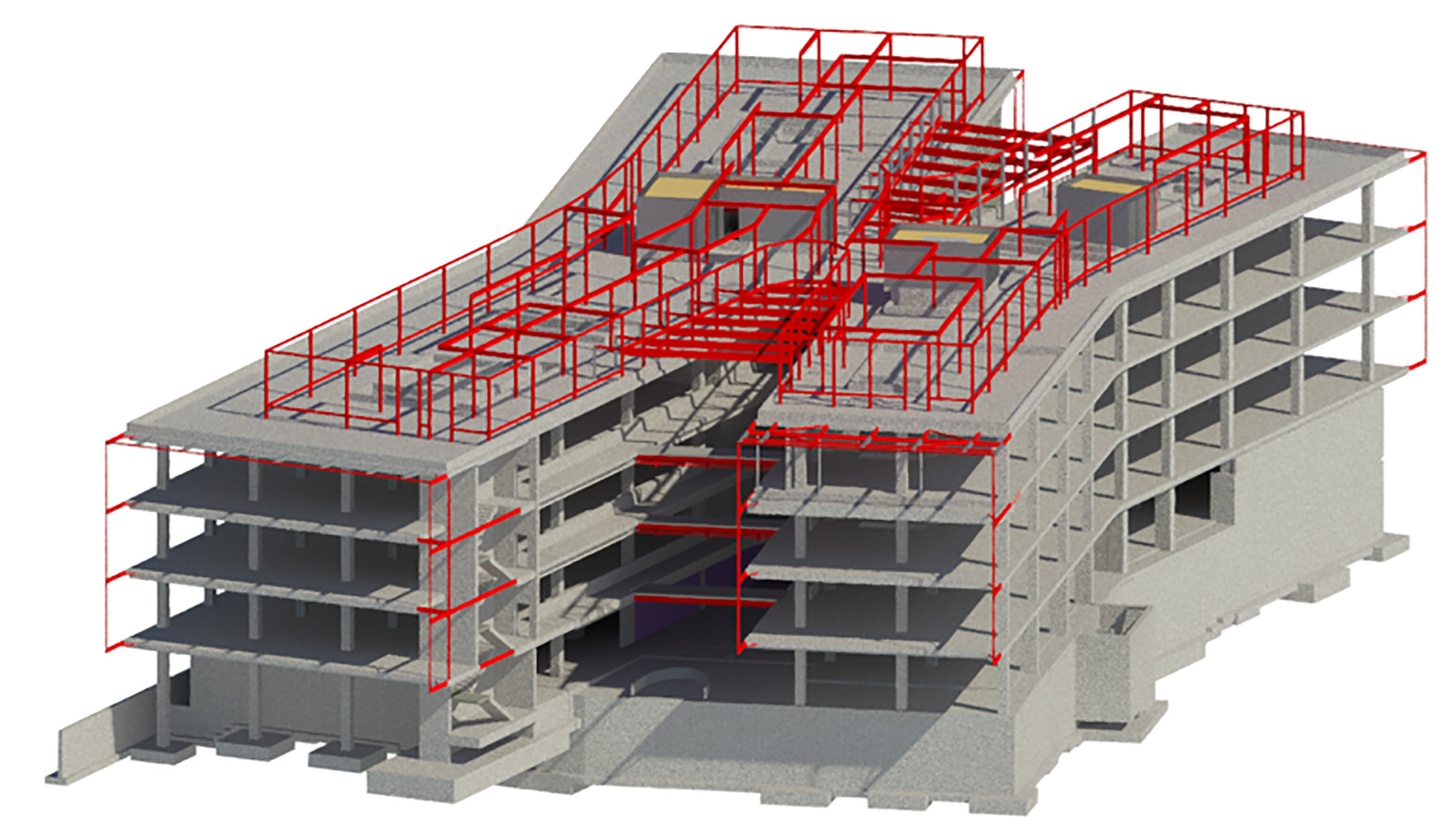
To combat the tendency of the building wings to transfer axial load through the bridges in a seismic event, the design team fit a slotted connection at the west end to allow the wings to behave independently. Interior glass walls in the laboratories on the atrium side provide visibility across lab spaces and thus the opportunity for a more collaborative environment overall.
Additionally, the atriums have steel-framed skylights consisting of HSS members that are 20 in. by 8 in. by 0.375 in. and span 35 ft at the roof level. These steel beams are connected to roof screen posts with back span kickers that are designed to prevent the atrium roof from racking in a seismic event. At the ends of the skylights, full-height glazed curtain walls hang from the outermost structural HSS beam and are braced out of plane by the steel bridges at each level, enabling outstanding canyon views and plenty of natural light.
An iconic structure
A 12 in. thick, two-way, mild-reinforced flat plate concrete gravity-framing system provides a thin profile that is optimal for exposing the concrete edges of the building as well as a floor structure that is ideal to meet the vibration criteria required for the building. To achieve a column-free lecture hall, the design team constructed two 6 ft wide by 4 ft, 6 in. deep posttensioned transfer beams to support two columns each and four stories of structure above.
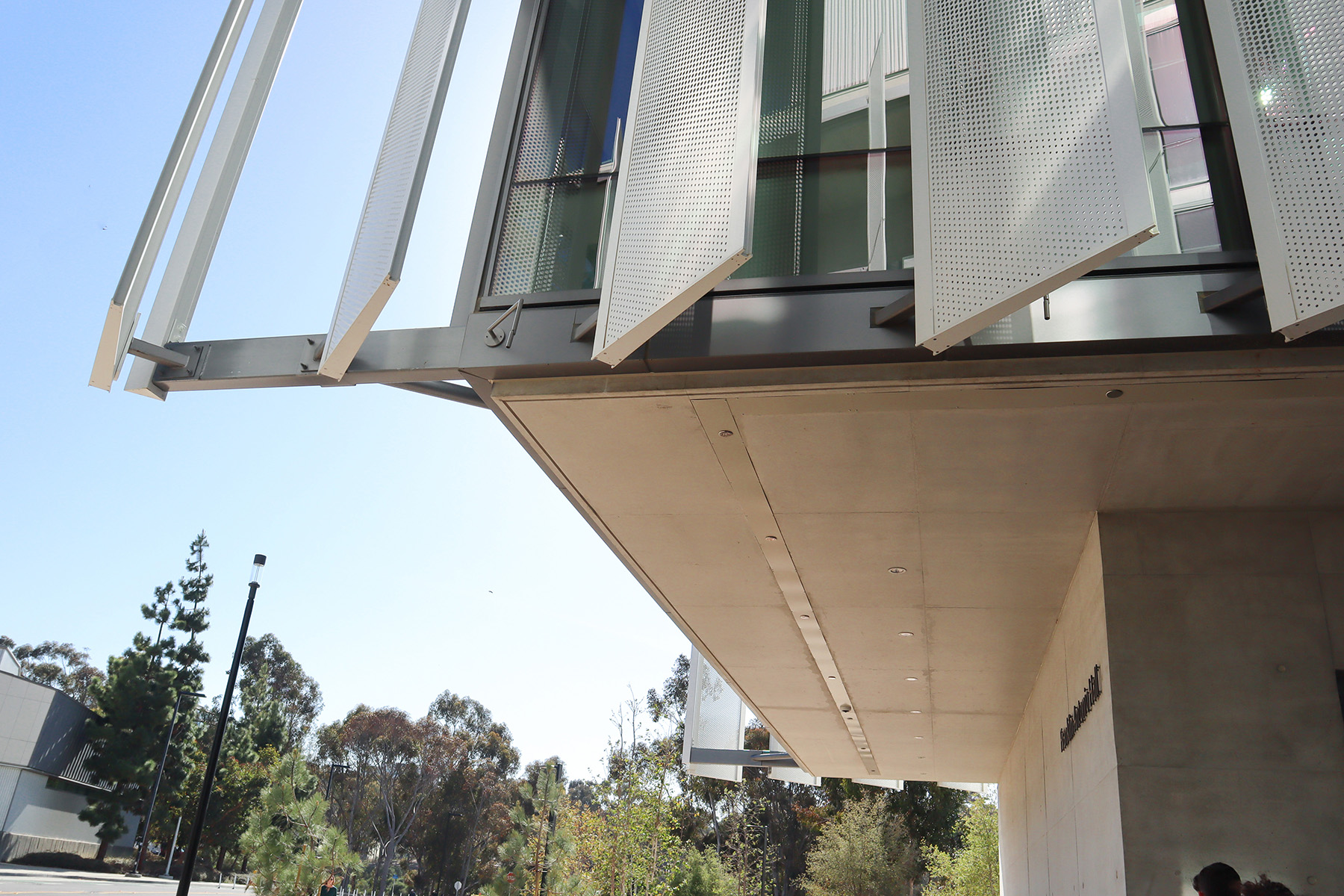
Concrete cantilevers extend more than 14 ft at the north and south ends of the building to create the illusion that the building is floating over the canyon that surrounds the university. To achieve the long cantilevers, the engineering team thickened the concrete slabs in the end bays to 18 in. and then notched them at the ends, reducing them to 12 in. to maintain a thin profile around the perimeter of the building.
These thickened slabs at the building ends also enabled easier placement of trenches in the slab soffit in order to hide the sprinkler system. At the underside of the second-story slab, piping and sprinkler trenches, measuring 8 in. by 8 in., were routed along the exterior perimeter to protect the building from wildfire due to its close proximity to the canyon.
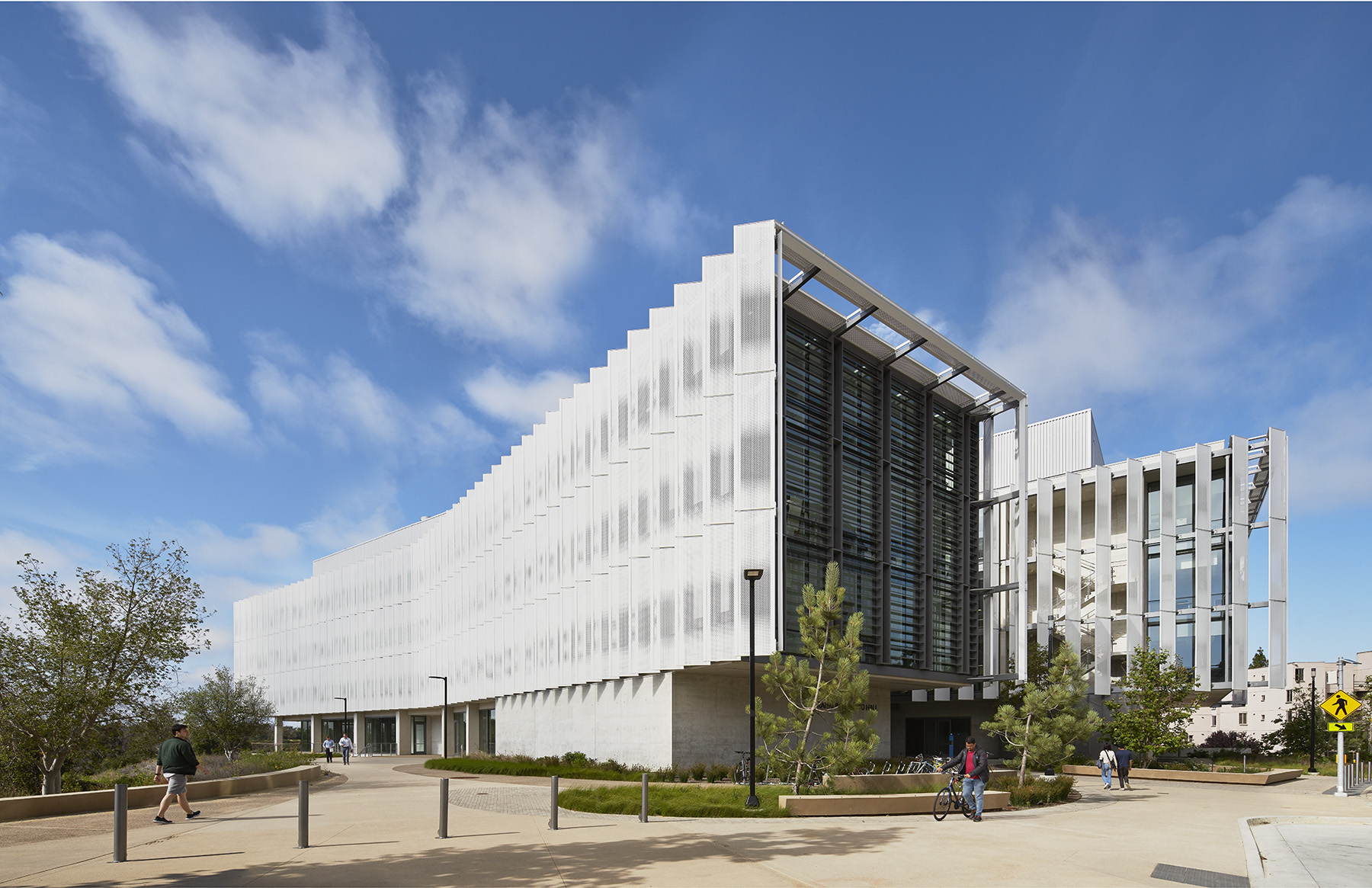
Large architectural aluminum sunshade “fins” also create the illusion of a building floating on the hillside. The fins, which span from level 2 to the roof, protect the building from direct sunlight while permitting abundant natural light. To support these substantial fin elements, the design team used HSS beams to cantilever off the already long concrete cantilevers.
The fins lower the building’s energy consumption, allowing Franklin Antonio Hall to attain a Leadership in Energy and Environmental Design Gold certification.
Stunning staircase
Winding its way from the ground level to the fourth floor, the architecturally imposing and gravity-defying steel spiral stair evokes the look of a double helix strand of DNA. The 15 ft diameter staircase seamlessly passes through floor openings at the building core, tied only to a small wedge of concrete floor framing at each level, far from the nearest column or shear wall. The main structural support is a tightly ribboned, 5 ft tall, solid webbed truss with box-shaped chords.
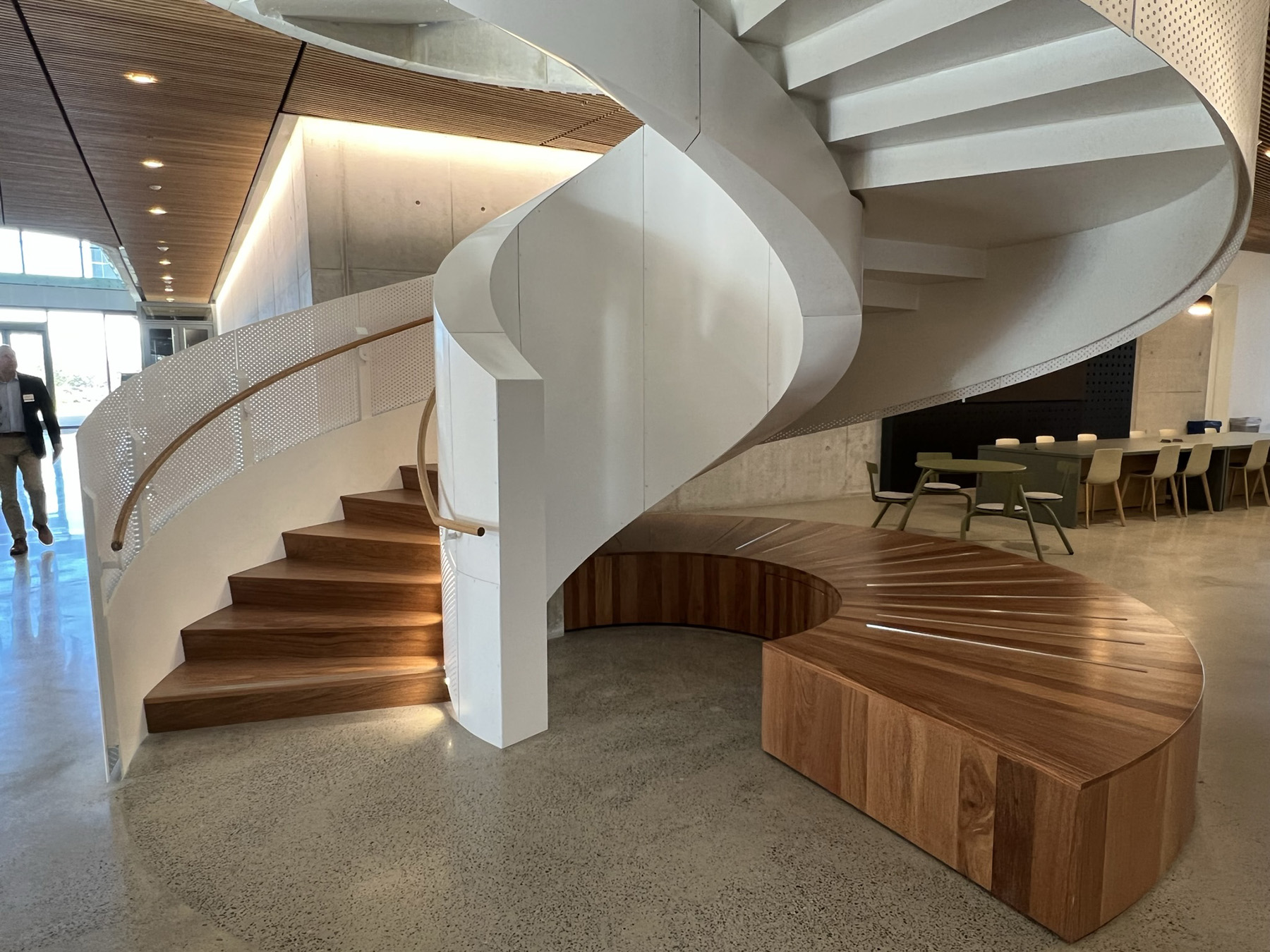
Rotating more than 360 degrees between floor levels, a series of cascading 4 ft long cantilevering treads and risers pinwheel from the main support. Each bladelike tread and riser pair is held at the perimeter by a low-profile and delicate outer banding stringer.
With such complex geometry and minimal vertical support, Coffman needed to integrate not only considerations for design loading and vibration performance due to the location but also the unique detailing. With all structural members being built up out of steel plate, the intricate structure required close collaboration with the contractor for erection sequencing.
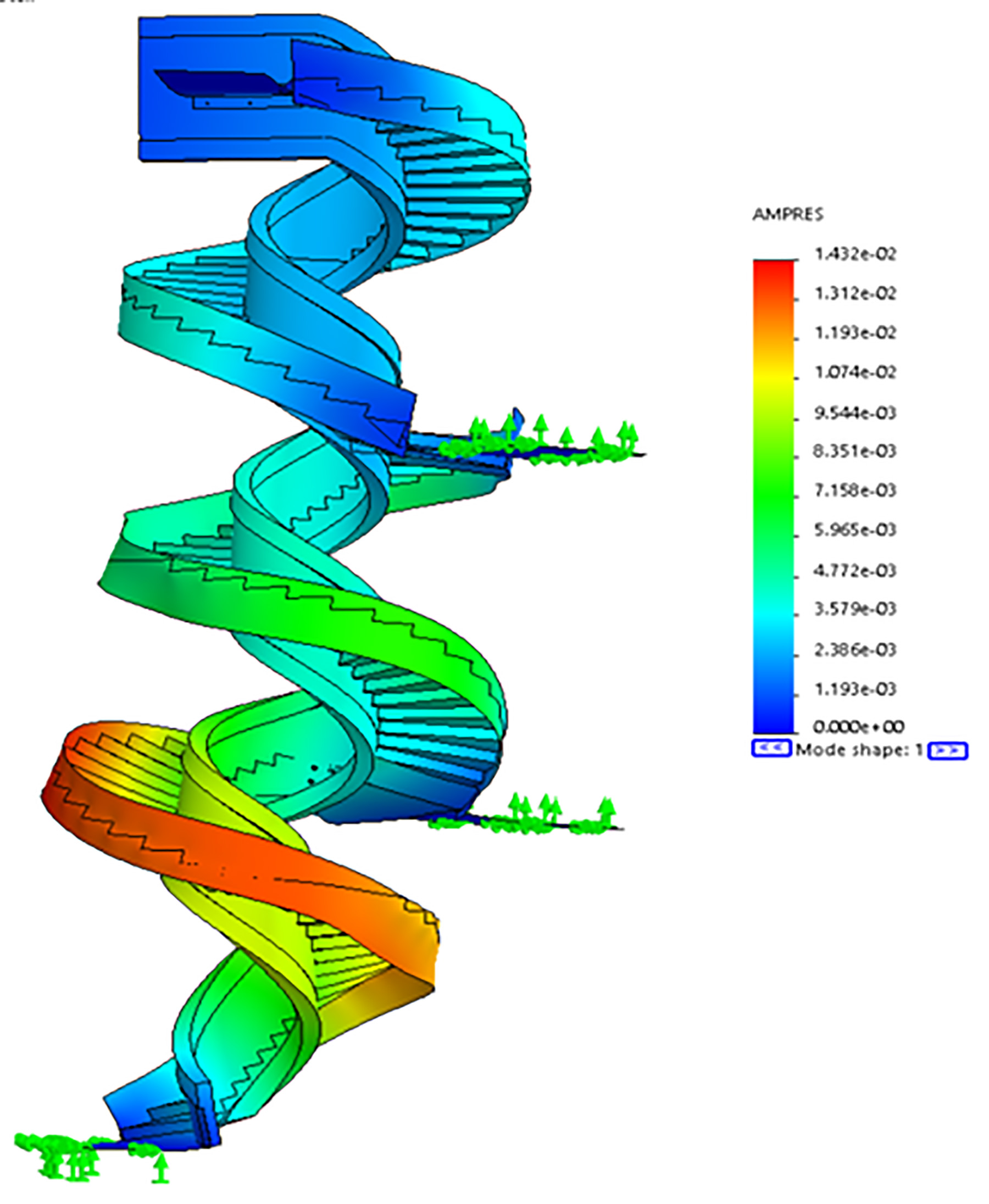
Enhanced finite element modeling identified areas of concentrated stress, captured connection-force envelopes for skip live-loading cases, and was pivotal in identifying vibrational mode behavior to ensure the four-story “spring” was calibrated to an appropriate stiffness. Because of the floor framing’s relative flexibility, the design team took into account vibration and deflection of the staircase in concert with that of the nearby concrete elements to which it would ultimately connect.
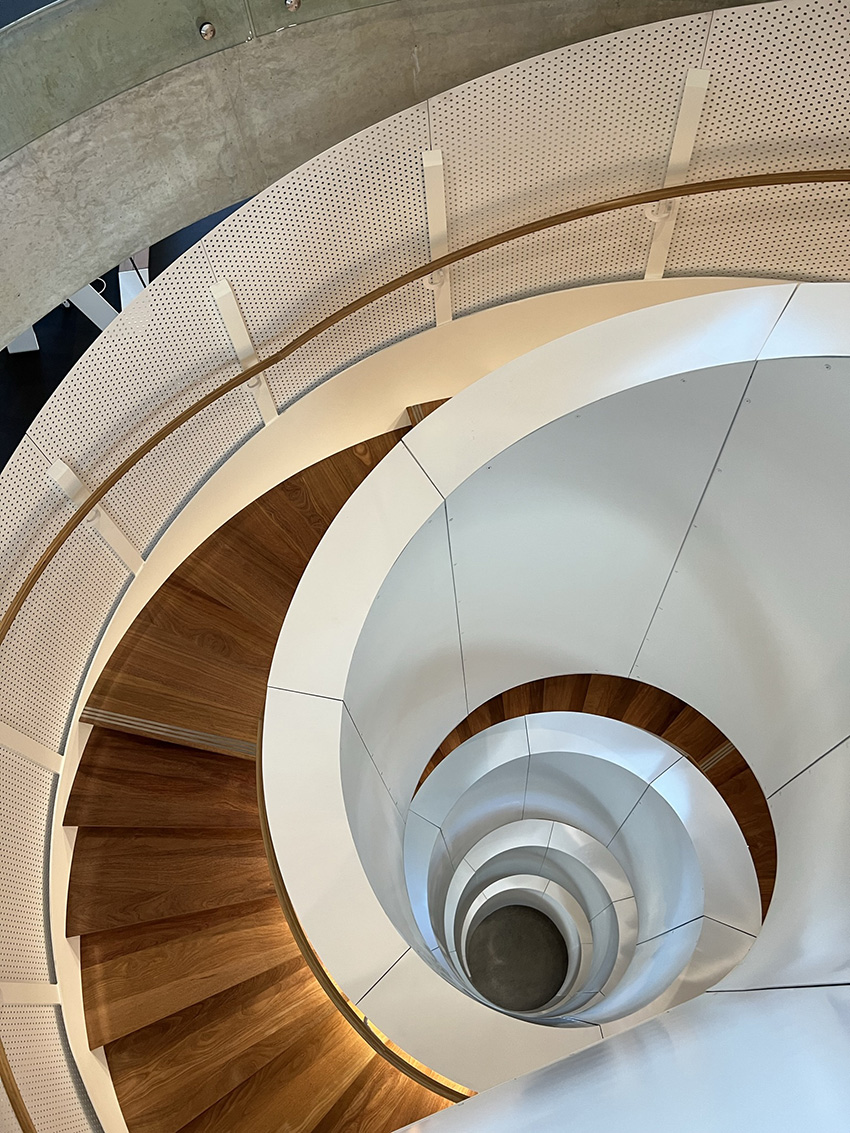
A combined fundamental vibration frequency of 10 Hz or better was targeted to avoid nuisance excitation anticipated from footfall in the 5-8 Hz frequency band. Accordingly, the predicted peak acceleration was successfully held to less than 1% g.
The construction of the stair included a series of complex, radiused A572 Gr50 steel-plate elements tied together with complete joint penetration welds.
The 1 in. thick main stringer support element comprises a single, freestanding, 5 ft tall, 3 ft, 6 in. radius plate, flanked at the top and bottom by 6 in. by 8 in. hollow built-up box sections. These box sections act like truss chords for the tall stringer plates, contributing significantly to the overall strength and stiffness of the staircase.
The treads and risers comprise 0.375 in. plates, and they cantilever from the face of the main stringer plate. They were joined at the outside edge with a 7 ft, 6 in. radius, 0.375 in. by 30 in. tall banding stringer. Irregular, tapered, and trapezoidal concrete wedges were formed as the stringer plates twisted past concrete floor framing.
To marry the steel plate and concrete floor framing, the design team added 0.625 in. thick plates to reinforced-concrete wedges projecting into the floor opening, acting as composite formwork.
Integrating the sequencing of the concrete main structure with the fine details, tolerances, and connections to the spiral staircase was a major challenge. To accommodate these factors, the design and construction teams coordinated early in the design phase to develop a well-orchestrated design of a temporary column and bracing support system.
The temporary column, a 24 in. diameter steel pipe, supported the full weight of the staircase by attaching to HSS “branches” cantilevering off its edges until the concrete slabs could be poured and the staircase welded to the steel plate composite formwork at each landing. This temporary steel support system allowed the two trades to work concurrently, avoiding delays and ultimately achieving the intended aesthetic and structural design.
Robust fire protection
As mentioned previously, due to the building’s proximity to the canyon hillside, wildfire danger was a major design consideration for the structure. Along with providing structural engineering services, Coffman was responsible for fire protection services, which involved running several fire analysis scenarios up the hillside to determine various impacts on the structure. As a result, the team erected a concrete fire protection wall along the eastern edge and created a gap between the building footprint and the canyon edge on all other sides.
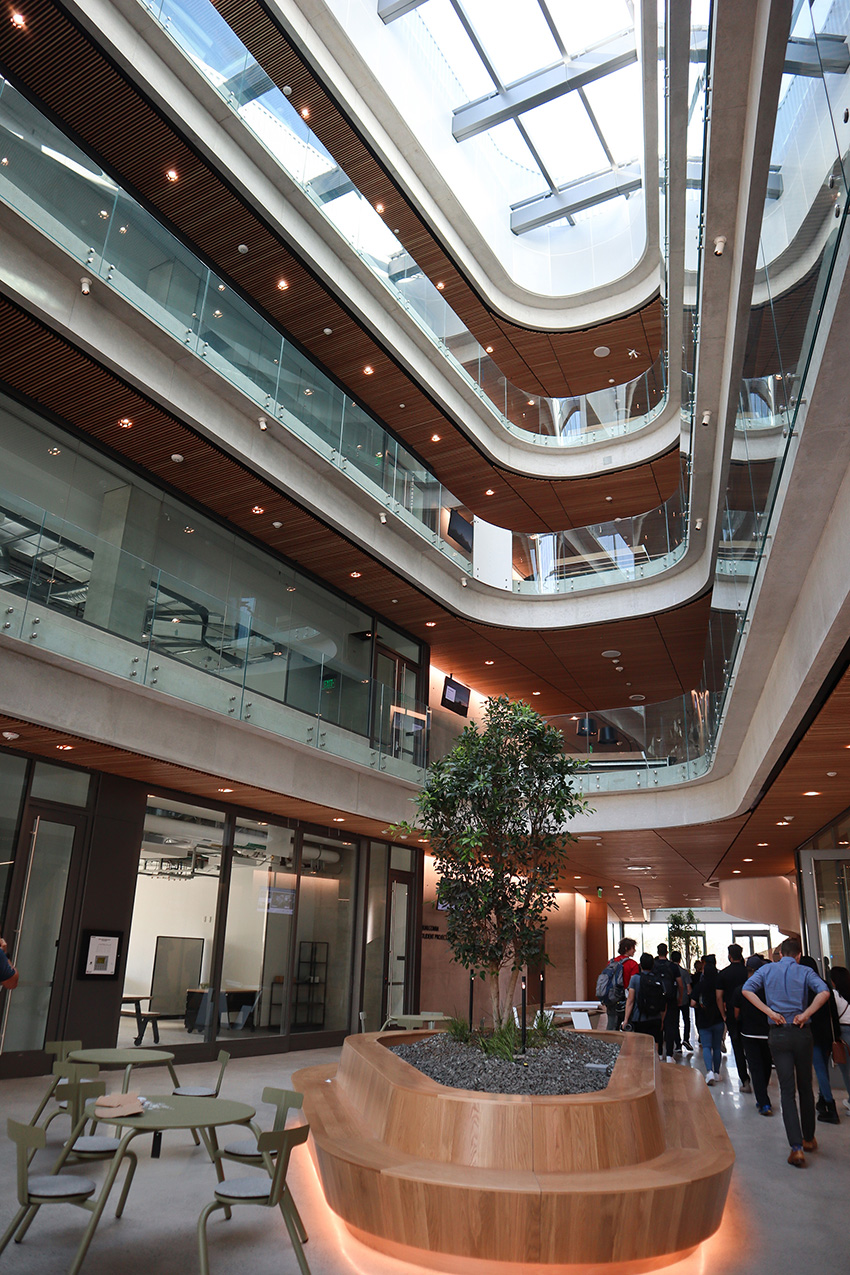
The atrium skylights are also equipped with a smoke extraction system that, in the event of fire, eliminates the ability for smoke to build up in the tall atrium space, giving building occupants extra time to exit. In some locations, the kicker system also acts as duct support for the heavy smoke extraction system.
Coffman also advised significant sprinkler piping alongside the smoke extraction system, which also necessitated some unique structural details and coordination.
Award wins
In 2022, the project received a Certificate of Merit award and the People’s Choice award from the Structural Engineers Association of San Diego, and in 2023, it received the Award of Merit from the American Institute of Architects along with the Divine Detail Award for its expertly designed spiral staircase.
Conclusion
Franklin Antonio Hall is a unique state-of-the-art building that melds ambitious architectural vision with complex aesthetic structural solutions. Every part of the architecture, from the unique floor shape, the connecting bridges, the floating fins, the gravity-defying spiral staircase, and even the huge glass skylights, is a testament to the structural engineering ingenuity required to showcase the building’s architectural brilliance.
Casey Whitsett, P.E., S.E., is a principal and Chelsea Kemmerrer, P.E., is an engineer at Coffman Engineers Inc.
Project credits
Owner
University of California San Diego
Engineer of record, structural engineer, and fire protection services
Coffman Engineers Inc., San Diego
Architect
Perkins&Will, San Diego
General contractor
McCarthy Building Companies Inc., San Diego
Mechanical and plumbing engineer
Dufoe Consulting Engineers, San Diego
Electrical engineer
Randall Lamb Associates, San Diego
This article first appeared in the January/February 2024 print issue of Civil Engineering as “Engineering Ingenuity.”