By Bruce Erickson, P.E., S.E., ENV SP, M.ASCE
“Industrial Refuge,” in the March/April print issue of Civil Engineering magazine, looks at a 3-acre aquatic habitat restoration at the Vigor Shipyards’ Harbor Island facility in Seattle that reintroduced a salmon habitat to the industrial waterfront. This piece looks at a neighboring project owned by a separate entity, King County, which involved the demolition of a dock containing creosote piles that could have potentially contaminated the waterway.
Every project has its challenges. The demolition of a wooden dock owned by King County, Washington, on Seattle’s Harbor Island was conceptually simple: remove an existing decayed dock and leave the beach below it in stable condition. However, determining the best way to remove the severely deteriorated timber piles — which had been treated with creosote, a toxic wood preservative — without them disintegrating during extraction and introducing large quantities of creosote-laden wood particles into the waterway was complicated.
The answer was found during a two-week test period.
The location
Construction of the 350-acre artificial Harbor Island was completed in 1909. The island was built up with dredge spoils from the creation of the East and West Waterways in the Duwamish River and from excess soil generated during the regrading of Seattle.
A company named Fisher Mills acquired the site on Harbor Island in about 1911 and constructed a flour mill. The facility included constructed timber docks that extended into the West Duwamish Waterway, which runs along the west side of Harbor Island. After the mill was closed in 2002, portions of those docks had stopped being used and were in disrepair. By 2018 the docks had deteriorated to the point that some deck sections had collapsed into the water. The creosote timber piles holding up these decks were severely decayed, some to the point that large holes had formed through the full thickness of the piles; others had completely broken off near the mud line.
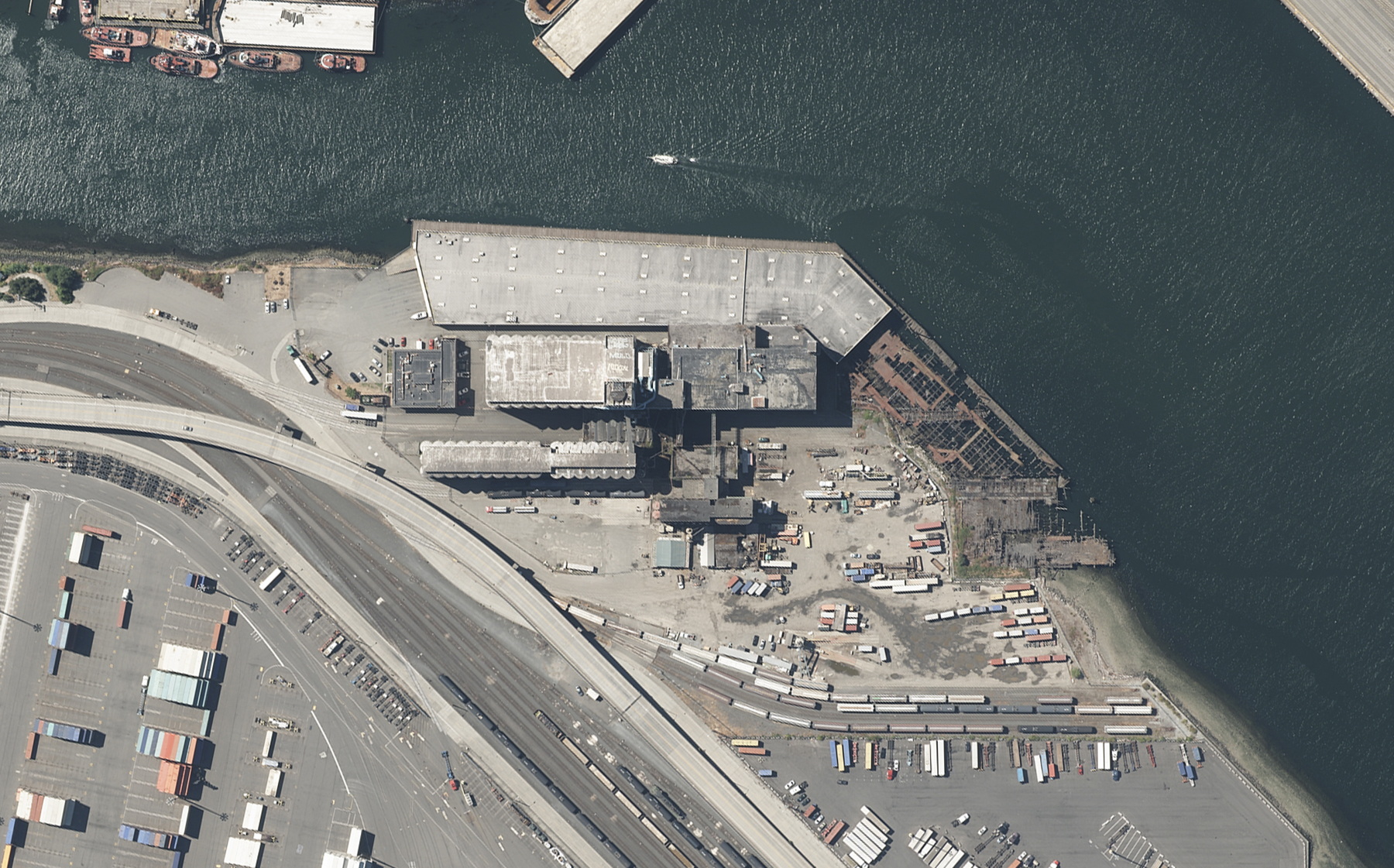
King County acquired the property on Harbor Island that included the abandoned flour mill and docks and by 2018 determined that the derelict portions of the old docks needed to be removed. The partially collapsed docks were a hazard to navigation, and there was concern that the timber piles were potentially leaching creosote into the surrounding soil and water. Demolition would require removing approximately 24,000 sq ft of timber and steel plate dock, about 450 linear ft of concrete bulkhead walls, isolated mass concrete foundations, and about 2,100 timber piles.
In 2018, King County hired a consultant team to provide engineering, permitting, and construction management for the dock demolition. This team was led by engineering firm KPFF Consulting Engineers and was supported by multiple subconsultants, including Floyd|Snider as the environmental and permitting consultant.
After gathering site data, the consultant team identified challenges to demolishing the dock and potential solutions. Challenges identified included how to remove the 2,100 severely deteriorated piles that were part of the flour mill’s dock while minimizing potential adverse impacts to the environment and how to stabilize the beach against erosion after the piles were removed.
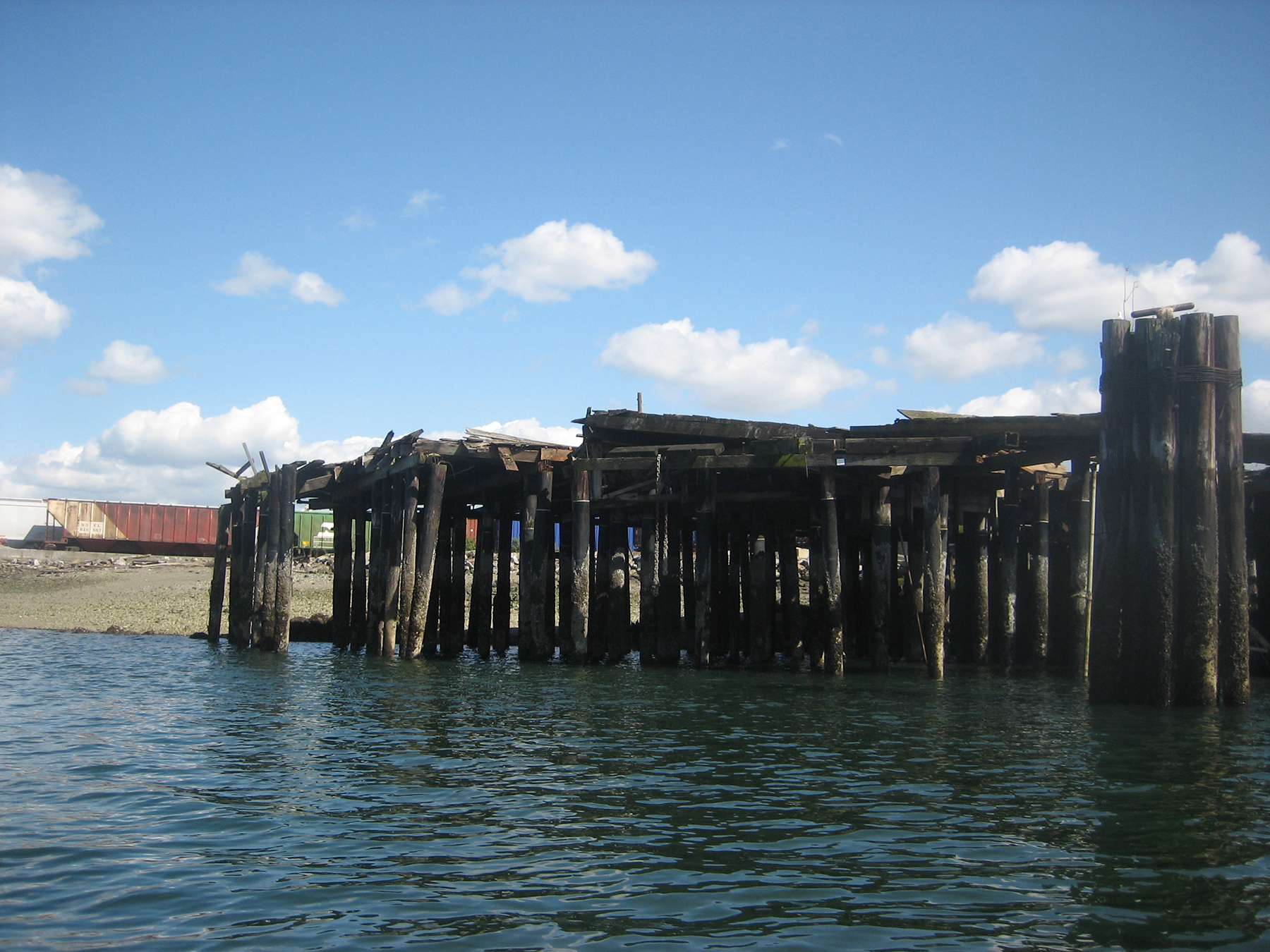
Removing the deteriorated piles
Regulatory agencies and pile removal best-management practices typically call for piles to be fully extracted to the maximum extent feasible. This removes potential sources of creosote that might leach into surrounding soil and water and eliminates potential obstructions to any future pile driving. Cutting off the pile at the mud line and removing only the above-grade portion is usually only done as a last resort.
Due to the heavily deteriorated condition of the timber piles at this site, it was feared that a substantial number of piles would not be able to be fully extracted, which could have resulted in construction risk and potential change orders. There was also concern that attempting to fully extract such deteriorated piles might cause them to disintegrate, putting significant quantities of creosoted wood fibers into the waterway.
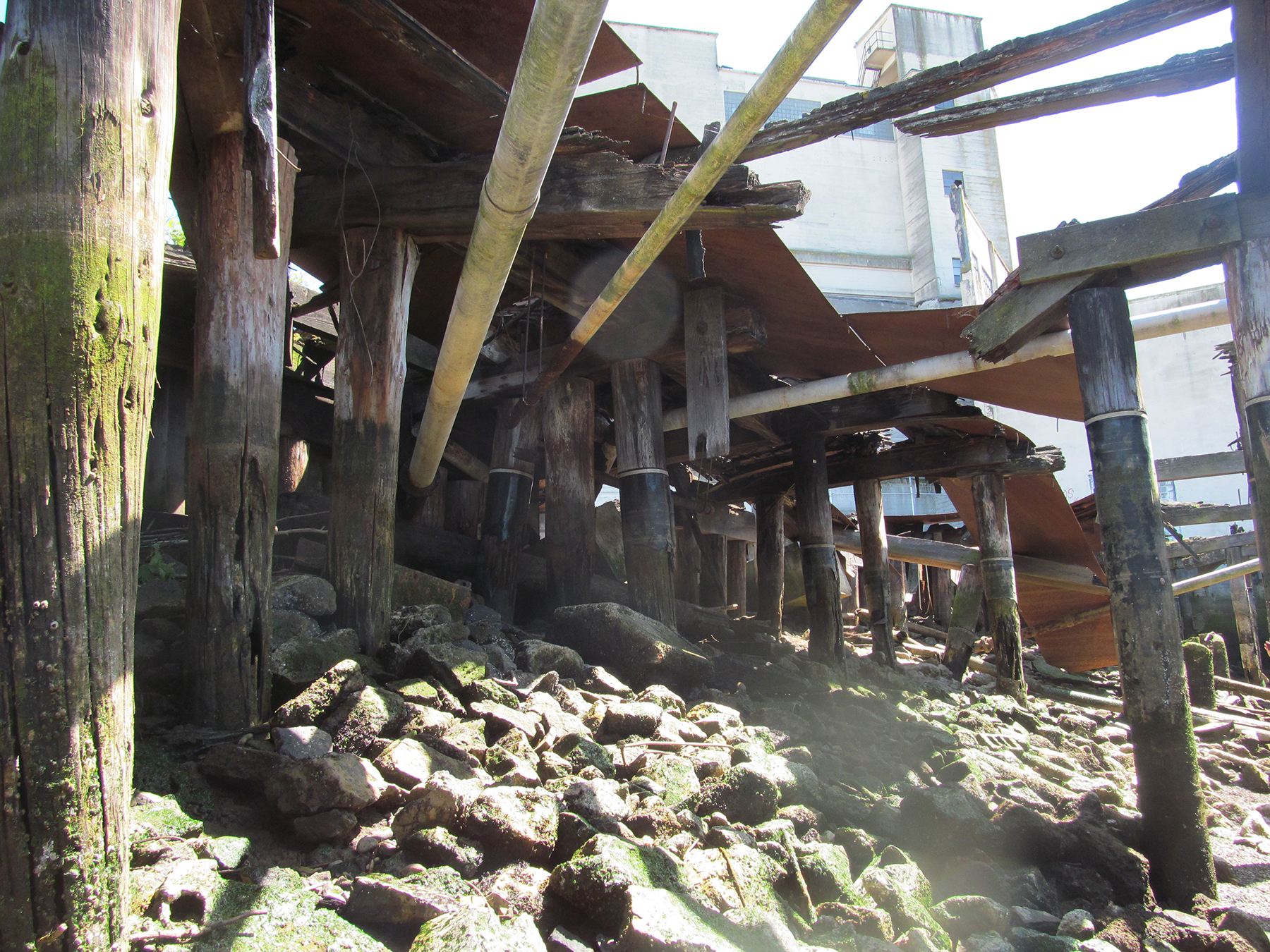
Further compounding the challenge was the fact that the site included piles with varying degrees of decay and with multiple types of past repairs, including concrete collars near the mud line. It was assumed that different pulling methods might have varying degrees of success with different degrees of pile deterioration and different pile repair methods.
There was also concern about the impact to project schedule and construction cost, as the process of trying to extract piles using multiple extraction methods for each type of pile decay before resorting to cutting off would require significant labor and equipment time, presenting significant cost uncertainty and potentially jeopardizing the contractor’s ability to complete the project within the required project schedule.
To reduce impacts to the environment and project cost and schedule, a pile removal pilot program was proposed to be implemented at the start of construction to mitigate risk to owner and contractor.
The purpose of the pilot program was to determine whether it was realistic to fully extract the deteriorated piles and which method of extraction would be most successful. The pilot program was implemented during a two-week period at the beginning of construction with environmental agency representatives present on-site to review proposed methods and results.
The pilot program called for contractor Pacific Pile & Marine to implement as many extraction attempts as possible with a total of at least 80 piles (representing all the varying degrees of decay and multiple types of past repairs present on the site), with the goal of determining the best methods for pile removal to be used for each pile type. Methods tried included vibratory extraction, direct pulling by wrapping a chain around the pile top and pulling up on the chain with a crane, and grasping the top of the pile with a clam shell bucket and gently moving the top of the pile back and forth while pulling upward. Unit prices for each of these methods had been included in the project bid tab, and the contract required that quantities for each removal method would be determined based on results of the pilot program.
Vibratory extraction was found to be the most successful for most pile types and was able to fully extract even severely deteriorated piles with a high degree of success. So this was the primary method selected to use for the remainder of construction.
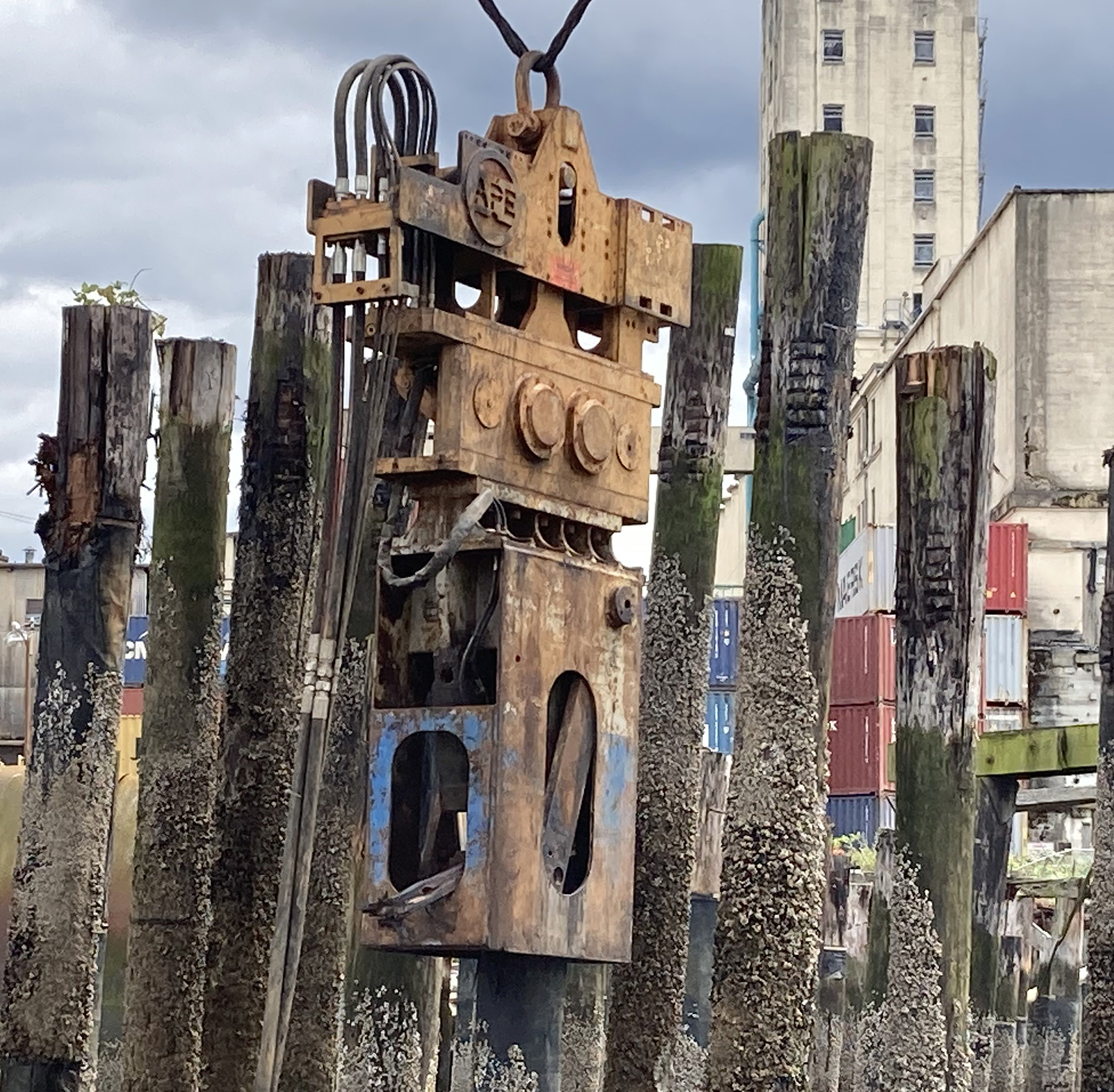
Stabilizing the beach
In addition to removing piles and debris within the former dock footprint, approximately 450 linear ft of multiple discontinuous and failing existing vertical bulkheads were demolished. The bulkhead sections had originally been constructed on varying alignments, resulting in an irregular pattern in plan view. The newly exposed shoreline was smoothed out and regraded to a continuous slope, eliminating existing shoreline protrusions which were vulnerable to scour. After regrading, the shoreline was armored with riprap, while the intertidal areas were stabilized with more fish-friendly gravel and sand mixtures. To the greatest extent possible, work in the intertidal zone was conducted in the dry during low tide to minimize sediment disturbance.
Sustainability benefits
King County is strongly committed to sustainability, which includes environmental stewardship as well as building equity and opportunity for its citizens. All King County capital projects need to follow the Green Scorecard, a tool developed by the county to help teams comprehensively consider environmental, equity, and social justice impacts. It also grades the projects on their ability to successfully address those impacts.
The scorecard considers such project aspects as preservation of natural site amenities, energy use reduction, low-impact stormwater management, use of sustainable materials, engagement with community stakeholders, siting and designing to counter disparities, diversity in project teams, and contractor utilization of apprentices.
Use of the scorecard helped the design team better understand the inherent environmental, equity, and social justice benefits of removing the creosoted wood piles from the Duwamish.
Previous research on the health of salmon in the Duwamish Waterway had demonstrated the negative impacts of contaminants to salmon populations resulting from contaminants in the waterway, including the chemical class of polycyclic aromatic hydrocarbons that derive from creosote. Removing a source of PAHs from the Duwamish was helpful to the health of the salmon and the livelihoods of tribal fishers who rely on fishing in the Duwamish for their incomes.
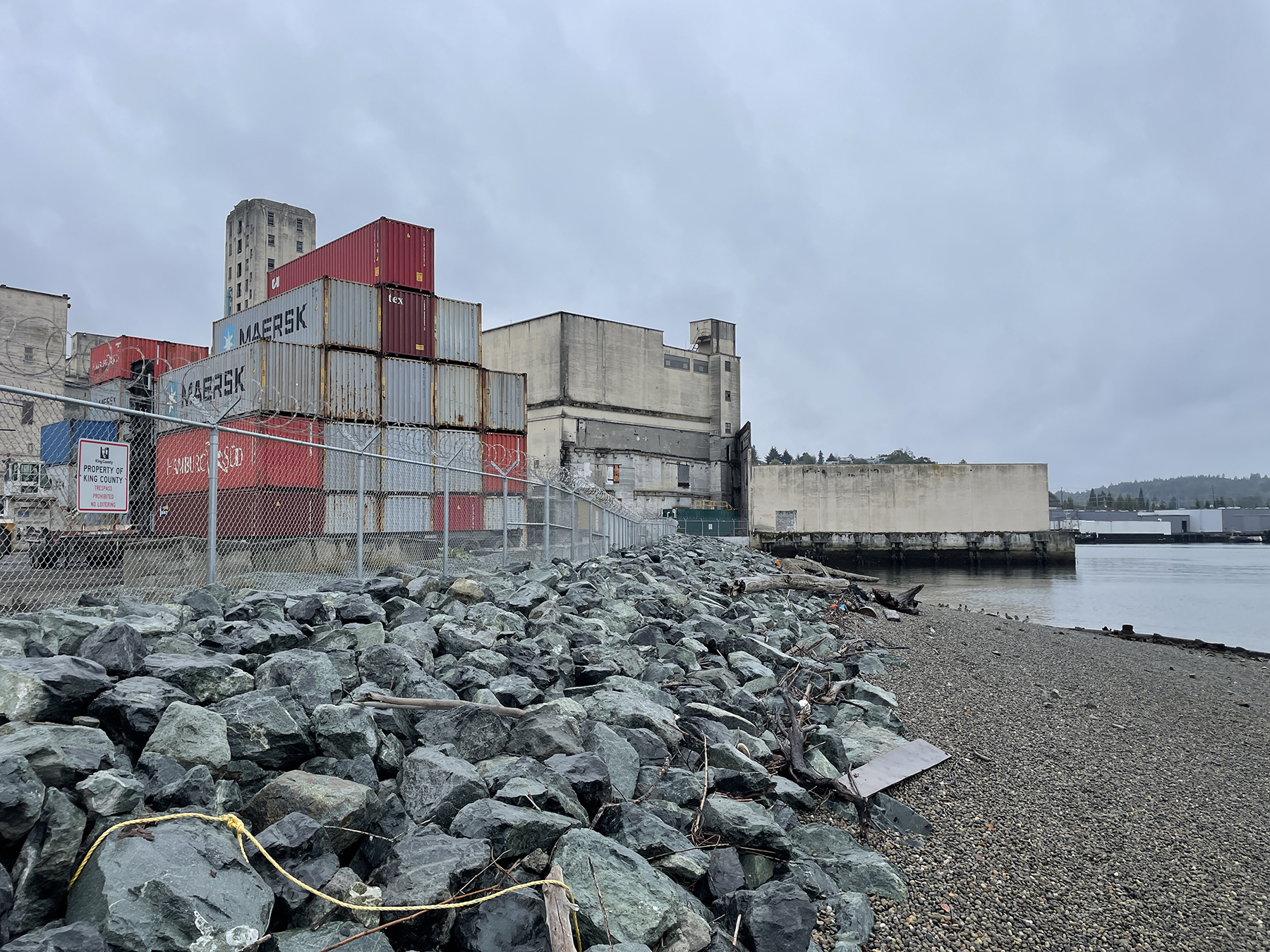
Many other factors went into the project sustainability planning, but several other elements that helped achieve the county’s sustainability goals included recycling of demolished concrete, returning the beach to a more natural condition, and placing a fish-friendly grade of sand and gravel in the intertidal zone.
Following demolition
Demolition and beach stabilization were completed in fall 2022. Pacific Pile & Marine was successful in removing almost all the deteriorated piles, and the regraded beach is now safe for wildlife and boaters who use the West Duwamish Waterway.
Bruce Erickson, P.E., S.E., ENV SP, M.ASCE, is an associate in the Seattle office of KPFF Consulting Engineers.
Project Credits
Owner: King County (Washington) Solid Waste Division Project Management Office
Prime consultant for engineering and construction management: KPFF Consulting Engineers
Environmental and permitting: Floyd|Snider
Biological assessment: Confluence Environmental
Coastal engineering: Blue Coast Engineering
Geotechnical: PanGEO Inc.
Survey: Furtado & Associates
Cost estimating: ProDims
Hazardous materials: EHSI
Sustainability consultant: Cascadia
Construction management: Pacific CM and KPFF
Contractor: Pacific Pile & Marine
This article is published by Civil Engineering Online.